Die Sintertemperatur für keramische Teile ist je nach Art des keramischen Materials und der vorgesehenen Anwendung sehr unterschiedlich.Im Allgemeinen erfolgt die Sinterung bei 50 bis 75 % der Schmelztemperatur der Keramik, in der Regel bei über 1000 °C.Zahnzirkoniumdioxid beispielsweise erfordert hohe Temperaturen zwischen 1400°C und 1600°C, um eine optimale Härte und Festigkeit zu erreichen, wobei eine genaue Kontrolle erforderlich ist, um Kornwachstum und Festigkeitsverlust zu vermeiden.Technische Hochleistungskeramik kann sogar noch besser kontrollierte Umgebungen erfordern, während einfachere Keramiken wie Porzellan bei niedrigeren Temperaturen in einfachen Öfen gesintert werden können.Der Sinterprozess ist entscheidend, um die gewünschte Dichte, Härte und strukturelle Integrität der Keramikteile zu erreichen.
Die wichtigsten Punkte werden erklärt:
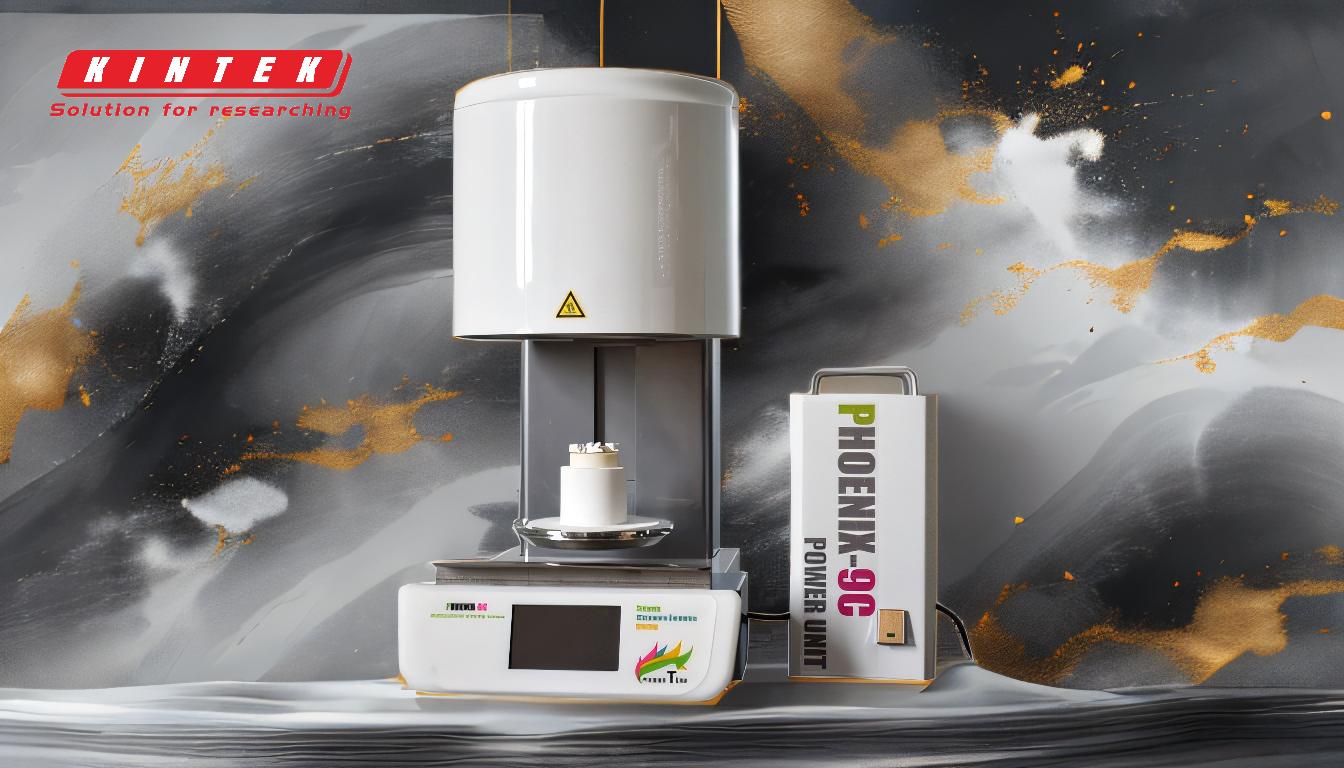
-
Allgemeiner Sintertemperaturbereich:
- Keramische Werkstoffe werden in der Regel bei 50 bis 75 % ihrer Schmelztemperatur gesintert, die in der Regel über 1000 °C liegt.Dieser Bereich stellt sicher, dass das Material mehr als 95 % seiner theoretischen Dichte erreicht, was für das Erreichen der gewünschten mechanischen Eigenschaften unerlässlich ist.
-
Sintern von Dentalzirkonoxid:
- Dentalzirkoniumdioxid muss bei hohen Temperaturen zwischen 1400°C und 1600°C gesintert werden.Dieser Bereich ist entscheidend, um die erforderliche Härte und Festigkeit für Dentalanwendungen zu erreichen.
- Jüngste Studien deuten darauf hin, dass das Brennen von Zirkoniumdioxid bei etwa 1500°C bis 1550°C die maximale Festigkeit ergibt.Abweichungen von diesem Bereich, selbst um nur 150°C, können zu einem erheblichen Festigkeitsverlust aufgrund von Kornwachstum führen.
-
Sintern von keramischen Verbundwerkstoffen:
- Keramische Verbundwerkstoffe werden in der Regel bei Temperaturen zwischen 900°C und 1250°C gesintert.Dieser Bereich ist geeignet, um die gewünschten Eigenschaften von Verbundwerkstoffen zu erzielen, die eine Kombination verschiedener keramischer Phasen enthalten können.
-
Die Bedeutung der Temperaturkontrolle:
- Der Sinterprozess ist sehr empfindlich gegenüber der Temperaturkontrolle, insbesondere während der Hochlauf-, Halte- und Abkühlphasen.So sind z. B. die Anstiegsgeschwindigkeit von 900 °C auf die Höchsttemperatur, die Temperaturkonstanz während der Haltezeit und die Abkühlungsgeschwindigkeit zurück auf etwa 900 °C allesamt kritische Faktoren, die die endgültigen Eigenschaften der Keramik beeinflussen.
-
Variabilität je nach Keramiktyp:
- Verschiedene Keramiktypen erfordern unterschiedliche Sinterbedingungen.So kann beispielsweise Porzellan in einem einfachen, kostengünstigen Ofen gesintert werden, während fortschrittliche technische Nichtoxidkeramik ein genau kontrolliertes Hochtemperatursintern in einer stabilisierenden Atmosphäre erfordert.Diese Variabilität ist auf Unterschiede in der Materialzusammensetzung und den gewünschten Endeigenschaften zurückzuführen.
-
Einfluss der Temperatur auf die Materialeigenschaften:
- Die Sintertemperatur wirkt sich direkt auf die Dichte, die Härte und die Festigkeit des Materials aus.So führt das Brennen von Zirkoniumdioxid bei 1500°C zu einer Festigkeit von etwa 1280 MPa, während das Brennen bei 1600°C die Festigkeit auf etwa 980 MPa reduziert und sie bei 1700°C auf etwa 600 MPa sinkt.Dies unterstreicht die Bedeutung einer präzisen Temperaturkontrolle, um eine optimale Materialleistung zu erreichen.
-
Praktische Überlegungen zur Ausrüstung:
- Bei der Auswahl von Sinteranlagen ist es entscheidend, die spezifischen Temperaturanforderungen des zu verarbeitenden keramischen Materials zu berücksichtigen.Hochtemperaturöfen mit präziser Temperaturregelung sind für Hochleistungskeramik erforderlich, während einfachere Öfen für Basiskeramik wie Porzellan ausreichen können.
Zusammenfassend lässt sich sagen, dass die Sintertemperatur für Keramikteile ein kritischer Parameter ist, der je nach Material und Anwendung variiert.Um die gewünschten mechanischen Eigenschaften zu erreichen, ist eine präzise Temperaturregelung unerlässlich, und die Wahl der Sinteranlage muss auf die spezifischen Anforderungen der zu verarbeitenden Keramik abgestimmt sein.
Zusammenfassende Tabelle:
Keramiktyp | Sintertemperaturbereich | Wichtige Überlegungen |
---|---|---|
Allgemeine Keramik | 50%-75% der Schmelztemperatur (>1000°C) | Gewährleistet eine theoretische Dichte von >95%, die für die mechanischen Eigenschaften entscheidend ist. |
Dentales Zirkoniumdioxid | 1400°C - 1600°C | Optimale Härte und Festigkeit; Abweichungen führen zu Kornwachstum und Festigkeitsverlust. |
Keramische Verbundwerkstoffe | 900°C - 1250°C | Geeignet zur Erzielung der gewünschten Eigenschaften in mehrphasigen Materialien. |
Porzellan | Niedrigere Temperaturen in einfachen Öfen | Einfacherer Sinterprozess; keine fortschrittliche Ausrüstung erforderlich. |
Technische Hochleistungskeramik | Hohe Temperaturen mit präziser Kontrolle | Erfordert stabilisierende Atmosphären und präzises Temperaturmanagement. |
Benötigen Sie Hilfe bei der Auswahl der richtigen Sinteranlage für Ihre Keramik? Kontaktieren Sie noch heute unsere Experten !