Induktionserwärmung ist ein Prozess, der elektromagnetische Induktion nutzt, um Wärme in einem leitfähigen Material zu erzeugen. Die bei der Induktionserwärmung erreichte Temperatur kann abhängig von mehreren Faktoren, einschließlich der Materialeigenschaften, der Frequenz des Wechselstroms und den spezifischen Anwendungsanforderungen, stark variieren. Im Allgemeinen kann die Induktionserwärmung Temperaturen im Bereich von einigen hundert Grad Celsius bis über 2000 °C erreichen, wodurch sie für eine Vielzahl industrieller Anwendungen wie Metallhärten, Hartlöten und Schmelzen geeignet ist.
Wichtige Punkte erklärt:
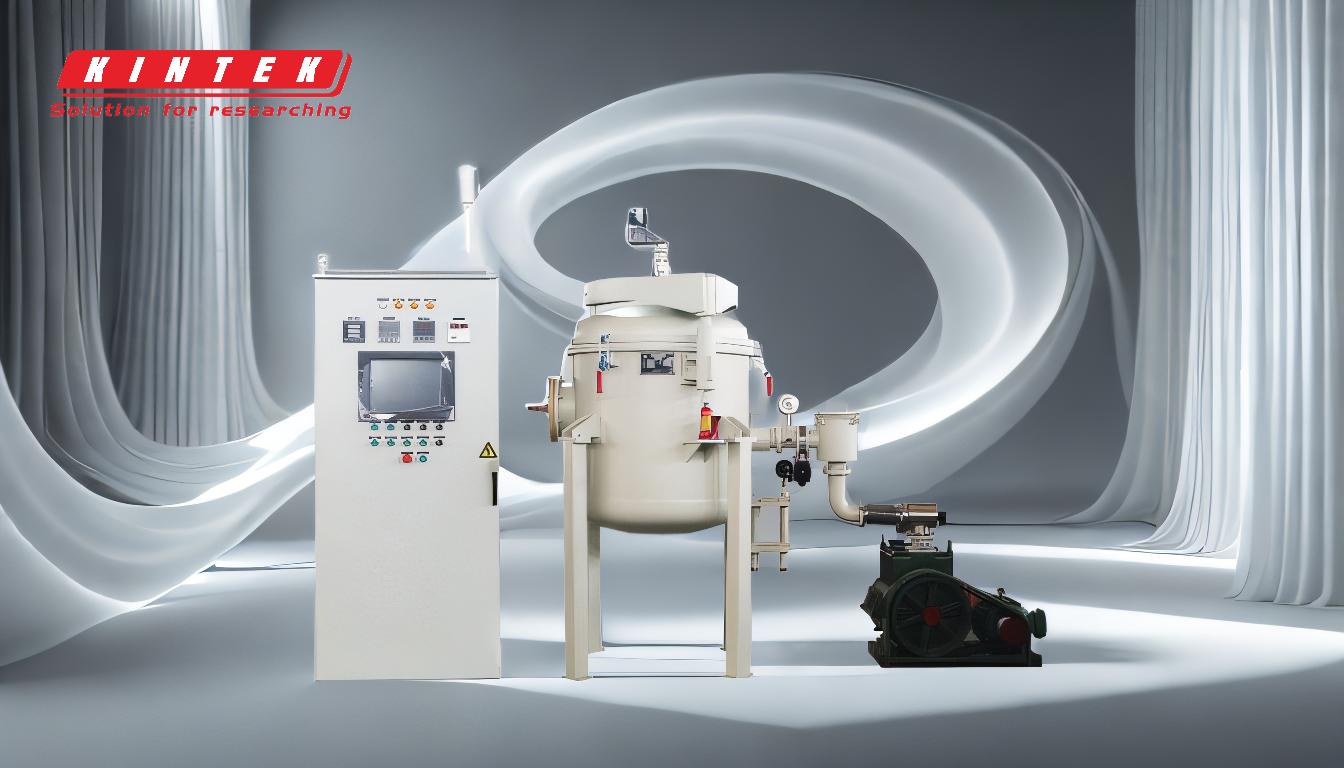
-
Materialeigenschaften beeinflussen die Heiztemperatur:
- Leitfähigkeit und Widerstand: Materialien mit höherer elektrischer Leitfähigkeit, wie etwa Kupfer und Aluminium, erwärmen sich effizienter, da sie dem Wirbelstrom einen geringeren Widerstand entgegensetzen. Umgekehrt erhitzen sich Materialien mit höherem Widerstand, wie bestimmte Stähle, möglicherweise schneller, benötigen aber mehr Energie, um die gleiche Temperatur zu erreichen.
- Magnetische Eigenschaften: Magnetische Materialien wie Eisen und einige Stähle erzeugen Wärme sowohl durch Wirbelströme als auch durch Hystereseeffekte. Durch diesen Doppelmechanismus erwärmen sich diese Materialien im Vergleich zu nichtmagnetischen Materialien schneller.
- Größe und Dicke: Kleinere und dünnere Materialien erwärmen sich schneller, da die induzierten Ströme weniger Material durchdringen müssen. Dies ist besonders wichtig bei Anwendungen, bei denen eine schnelle Erwärmung erforderlich ist, beispielsweise bei der Oberflächenhärtung.
-
Frequenz des Wechselstroms:
- Höhere Frequenz: Höherfrequente Wechselströme führen zu einer geringeren Eindringtiefe der Erwärmung, was ideal für Oberflächenerwärmungsanwendungen wie Einsatzhärten ist. Durch den Skin-Effekt konzentriert sich der Strom in der Nähe der Oberfläche, was zu einer schnellen Oberflächenerwärmung führt.
- Untere Frequenz: Niedrigere Frequenzen werden für eine tiefere Eindringung verwendet, die für Durchwärmungsanwendungen wie Schmieden oder Schmelzen erforderlich ist. Die Wahl der Frequenz ist entscheidend für die Bestimmung des Heizprofils und der endgültigen Temperaturverteilung innerhalb des Materials.
-
Anwendungsspezifische Temperaturanforderungen:
- Metallhärtung: Bei Prozessen wie dem Induktionshärten wird die Temperatur typischerweise auf den Austenitisierungsbereich (ca. 750–900 °C für Stahl) erhöht, um die Umwandlung der Mikrostruktur zu ermöglichen, gefolgt von einem schnellen Abschrecken, um die gewünschte Härte zu erreichen.
- Hartlöten und Weichlöten: Diese Prozesse erfordern niedrigere Temperaturen, typischerweise zwischen 450 °C und 800 °C, abhängig vom verwendeten Füllmaterial. Die genaue Temperatur ist entscheidend, um einen ordnungsgemäßen Fluss und eine ordnungsgemäße Verbindung des Füllmaterials sicherzustellen, ohne das Grundmaterial zu beschädigen.
- Schmelzen: Beim Induktionsschmelzen können die Temperaturen 2000 °C überschreiten, insbesondere beim Schmelzen von hochschmelzenden Metallen wie Wolfram oder Molybdän. Die hohen Temperaturen sind notwendig, um den hohen Schmelzpunkt des Materials zu überwinden und einen geschmolzenen Zustand zu erreichen.
-
Überlegungen zur Vakuumwärmebehandlung:
- Technische und Leistungsanforderungen: Bei der Vakuumwärmebehandlung wird die Heiztemperatur sorgfältig auf der Grundlage der technischen Anforderungen, Betriebsbedingungen und Leistungsanforderungen des Werkstücks ausgewählt. Ziel ist es, Verformungen zu minimieren und gleichzeitig die gewünschten Materialeigenschaften zu erreichen.
- Verformung minimieren: Durch die Senkung der Erwärmungstemperatur kann die Gefahr einer Verformung, insbesondere bei komplexen oder dünnwandigen Bauteilen, verringert werden. Allerdings muss die Temperatur dennoch hoch genug sein, um die notwendigen metallurgischen Umwandlungen zu erreichen.
-
Merkmale des Induktionsofens:
- Nullspannungsstart: Moderne Induktionsöfen verfügen häufig über einen Nullspannungsanlauf, der den Aufheizvorgang schonend und mit hoher Anfangsleistung startet. Dies minimiert die Auswirkungen auf das Stromnetz und ermöglicht eine präzise Steuerung des Heizprozesses.
- Energieeffizienz: Die Möglichkeit, die Frequenz und Leistung des Induktionserwärmungsprozesses zu steuern, trägt zur Energieeffizienz bei, da die Wärme direkt im Material erzeugt wird und nicht von einer externen Quelle übertragen wird.
Zusammenfassend lässt sich sagen, dass die Temperatur des Induktionserwärmungsprozesses stark schwankt und vom zu erwärmenden Material, der Frequenz des Wechselstroms und den spezifischen Anwendungsanforderungen abhängt. Das Verständnis dieser Faktoren ist entscheidend für die Optimierung des Induktionserwärmungsprozesses, um die gewünschten Ergebnisse effizient und effektiv zu erzielen.
Übersichtstabelle:
Faktor | Einfluss auf die Temperatur |
---|---|
Materialeigenschaften | - Leitfähigkeit: Höhere Leitfähigkeit = effiziente Erwärmung. |
- Magnetische Eigenschaften: Magnetische Materialien erwärmen sich aufgrund von Wirbelströmen und Hysterese schneller. | |
- Größe und Dicke: Kleinere/dünnere Materialien erwärmen sich schneller. | |
Frequenz des Wechselstroms | - Höhere Frequenz: Besser für die Oberflächenerwärmung (z. B. Einsatzhärten). |
- Niedrigere Frequenz: Besser für tiefes Erhitzen (z. B. Schmelzen). | |
Bewerbungsvoraussetzungen | - Metallhärtung: 750-900°C. |
- Löten/Löten: 450–800 °C. | |
- Schmelzen: Bis zu 2000 °C+ für hochschmelzende Metalle. |
Optimieren Sie noch heute Ihren Induktionserwärmungsprozess – Kontaktieren Sie unsere Experten für maßgeschneiderte Lösungen!