Die thermische Verdampfung ist eine weit verbreitete Technik der physikalischen Gasphasenabscheidung (PVD) zur Herstellung dünner Schichten oder Beschichtungen auf Substraten. Dabei wird ein festes Material in einer Hochvakuumkammer erhitzt, bis es verdampft. Dabei entsteht ein Dampfstrom, der durch das Vakuum wandert und sich auf einem Substrat ablagert und eine dünne Schicht bildet. Diese Methode ist einfach und effizient und eignet sich für Anwendungen wie OLEDs, Dünnschichttransistoren und andere Beschichtungen. Das Verfahren kann mit Hilfe von Widerstandsheizung oder Elektronenstrahlheizung durchgeführt werden, um die erforderliche Verdampfung zu erreichen. Die Vakuumumgebung sorgt für minimale Störungen durch andere Atome, so dass sich der Dampf gleichmäßig auf dem Substrat absetzen kann.
Die wichtigsten Punkte werden erklärt:
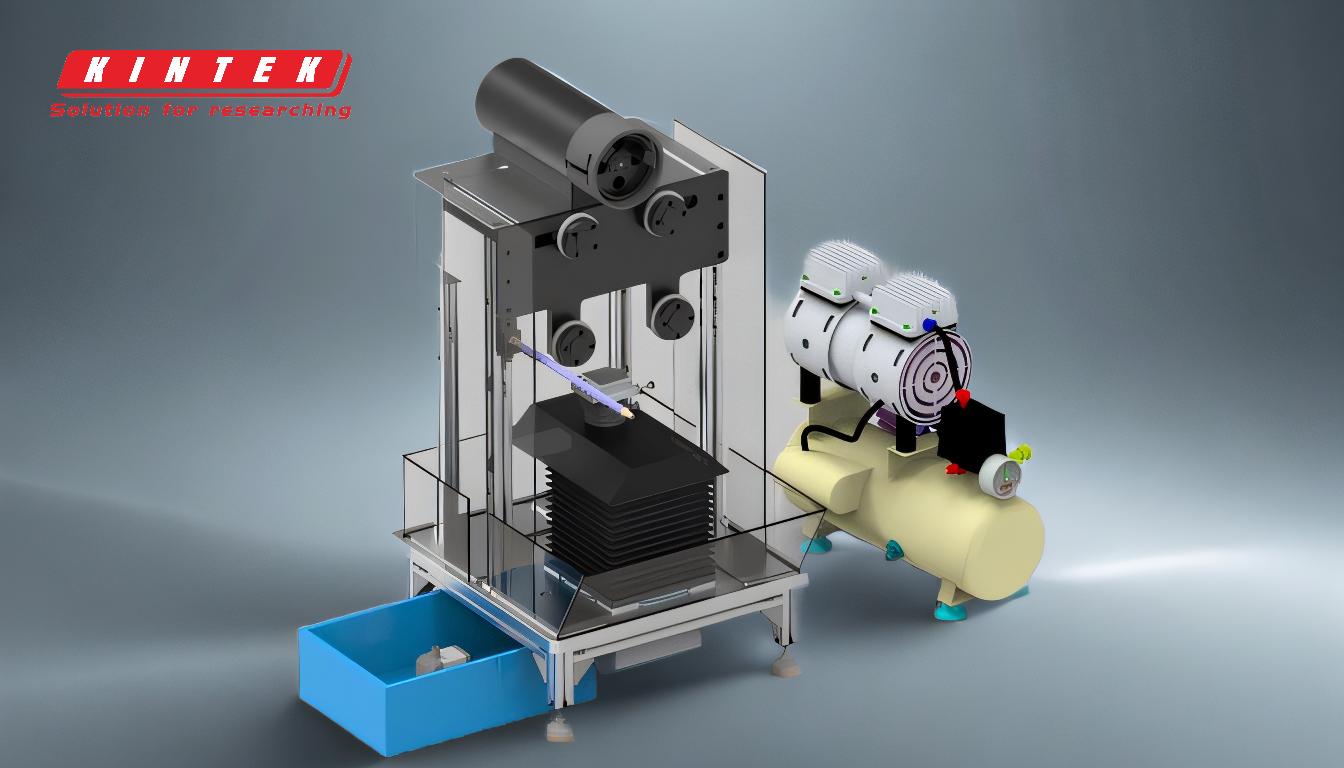
-
Grundprinzip der thermischen Verdampfung:
- Bei der thermischen Verdampfung wird ein festes Material erhitzt, bis es verdampft und ein Dampfstrom entsteht.
- Dieser Dampfstrom durchläuft eine Hochvakuumkammer und lagert sich auf einem Substrat ab, wodurch ein dünner Film oder eine Beschichtung entsteht.
- Die Vakuumumgebung ist von entscheidender Bedeutung, da sie verhindert, dass der Dampf mit anderen Atomen reagiert oder streut, und somit eine saubere und gleichmäßige Abscheidung gewährleistet.
-
Heizungsmechanismen:
- Widerstandsheizung: Ein gängiges Verfahren, bei dem ein elektrischer Strom durch ein Widerstandsheizelement (z. B. ein Wolframschiffchen oder einen Korb) fließt, um das Material zu schmelzen und zu verdampfen.
- Elektronenstrahlheizung: Eine alternative Methode, bei der ein Elektronenstrahl auf das Material gerichtet wird, um es lokal zu erhitzen und zu verdampfen. Dies ist besonders nützlich für Materialien mit hohem Schmelzpunkt.
-
Prozess-Schritte:
- Material Heizung: Das feste Material wird entweder durch Widerstands- oder Elektronenstrahlheizung auf seinen Schmelzpunkt erhitzt.
- Verdampfung: Das Material verdampft und erzeugt eine Dampfwolke in der Vakuumkammer.
- Dampftransport: Der Dampf durchquert die Vakuumkammer ohne Störung durch andere Atome.
- Ablage: Der Dampf kondensiert auf dem Substrat und bildet einen dünnen Film oder eine Beschichtung.
-
Vorteile der thermischen Verdampfung:
- Vereinfachung: Das Verfahren ist einfach und leicht zu implementieren.
- Hohe Reinheit: Die Vakuumumgebung sorgt für minimale Verunreinigungen und damit für hochreine Filme.
- Vielseitigkeit: Geeignet für eine breite Palette von Materialien, einschließlich Metallen, Halbleitern und organischen Verbindungen.
- Einheitlichkeit: Der Dampfstrom lagert sich gleichmäßig auf dem Substrat ab, was zu einer gleichmäßigen Schichtdicke führt.
-
Anwendungen:
- OLEDs (Organische lichtemittierende Dioden): Die thermische Verdampfung wird üblicherweise zur Abscheidung organischer Schichten in OLED-Displays verwendet.
- Dünnschichttransistoren: Diese Technik wird zur Herstellung von Dünnschichttransistoren für elektronische Geräte eingesetzt.
- Optische Beschichtungen: Wird zum Aufbringen von Antireflexions- oder Reflexionsschichten auf Linsen und Spiegeln verwendet.
- Metallisierung: Wird bei der Metallisierung von Halbleitern und anderen elektronischen Bauteilen verwendet.
-
Überlegungen zu Ausrüstung und Verbrauchsmaterial:
- Vakuumkammer: Er muss in der Lage sein, ein Hochvakuum aufrechtzuerhalten, um einen ordnungsgemäßen Dampftransport und die Abscheidung zu gewährleisten.
- Heizelemente: Für die Widerstandsheizung werden üblicherweise Wolframschiffchen oder -körbe verwendet, während für Elektronenstrahlverdampfer spezielle Geräte erforderlich sind.
- Substrat-Halterungen: Richtig konstruierte Halter sorgen für eine gleichmäßige Ablagerung und verhindern Verunreinigungen.
- Materielle Reinheit: Hochreine Ausgangsmaterialien sind für die Herstellung hochwertiger Filme unerlässlich.
-
Herausforderungen und Beschränkungen:
- Kompatibilität der Materialien: Nicht alle Materialien sind für die thermische Verdampfung geeignet, insbesondere solche mit sehr hohem Schmelzpunkt.
- Kontrolle der Filmdicke: Eine präzise Kontrolle der Schichtdicke kann eine Herausforderung sein, insbesondere bei sehr dünnen Schichten.
- Skalierbarkeit: Während das Verfahren für kleine Anwendungen effektiv ist, kann es für großflächige Beschichtungen komplex und kostspielig sein, es zu erweitern.
-
Zukünftige Trends:
- Fortgeschrittene Heiztechniken: Entwicklung effizienterer und präziserer Erhitzungsmethoden, wie z. B. die lasergestützte Verdampfung.
- Integration mit anderen Ablagerungsmethoden: Kombination der thermischen Verdampfung mit anderen PVD-Verfahren zur Verbesserung der Schichteigenschaften.
- Automatisierung und Steuerung: Zunehmender Einsatz von automatisierten Systemen und fortschrittlichen Kontrollalgorithmen zur Verbesserung der Reproduzierbarkeit des Prozesses und der Folienqualität.
Zusammenfassend lässt sich sagen, dass die thermische Verdampfung ein vielseitiges und effektives Verfahren für die Abscheidung dünner Schichten ist, dessen Anwendungsbereiche von der Elektronik bis zur Optik reichen. Um das Verfahren für bestimmte Anwendungen zu optimieren, ist es wichtig, den Prozess, die Ausrüstung und die Materialien zu verstehen.
Zusammenfassende Tabelle:
Aspekt | Einzelheiten |
---|---|
Grundprinzip | Erhitzen von festem Material zur Verdampfung und Abscheidung dünner Schichten im Vakuum. |
Heizungsmechanismen | Widerstandsheizung oder Elektronenstrahlheizung zur Verdampfung. |
Vorteile | Einfachheit, hohe Reinheit, Vielseitigkeit und gleichmäßige Ablagerung. |
Anwendungen | OLEDs, Dünnschichttransistoren, optische Beschichtungen und Metallisierung. |
Herausforderungen | Materialkompatibilität, Kontrolle der Schichtdicke und Skalierbarkeit. |
Zukünftige Trends | Moderne Heiztechniken, Integration mit anderen PVD-Verfahren, Automatisierung. |
Entdecken Sie, wie die thermische Verdampfung Ihre Dünnschichtprozesse verbessern kann kontaktieren Sie unsere Experten noch heute !