Sinter spielt eine entscheidende Rolle im Hochofenprozess und dient in erster Linie als aufbereitetes eisenhaltiges Material, das die Effizienz und Produktivität der Eisenerzeugung steigert.Er wird durch die Agglomeration von feinen Eisenerzpartikeln, Flussmitteln und anderen Zusatzstoffen zu einem porösen, stückigen Material durch einen Sinterprozess hergestellt.Sinter verbessert die Durchlässigkeit des Hochofenguts, verringert den Koksverbrauch und gewährleistet eine stabile und gleichbleibende chemische Zusammensetzung, die für eine effiziente Eisenerzeugung unerlässlich ist.Indem Sinter das Roheisenerzfeinkorn ersetzt, trägt er zur Optimierung des Hochofenbetriebs bei, was zu einem besseren Gasstrom, einem geringeren Energieverbrauch und einer höheren Gesamtleistung führt.
Die wichtigsten Punkte werden erklärt:
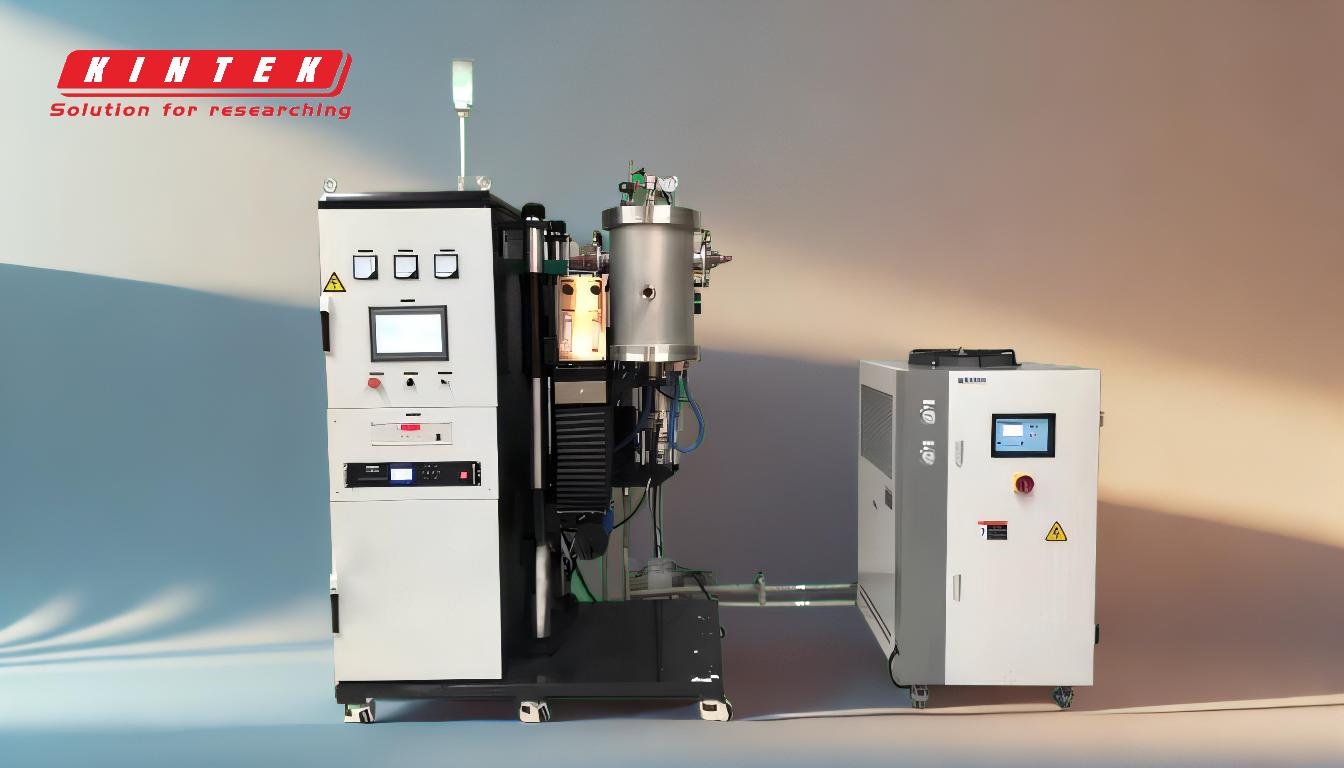
-
Erhöht die Durchlässigkeit des Hochofengutes:
- Sinter ist ein poröses Material mit gleichmäßiger Struktur, das die Durchlässigkeit des Hochofengutes verbessert.Dies ermöglicht eine bessere Gasströmung durch den Ofen und gewährleistet eine effiziente Wärmeübertragung und chemische Reaktionen.
- Die einheitliche Größe und Form der Sinterpartikel verhindert die Bildung dichter Schichten, die den Gasstrom behindern und die Effizienz des Ofens verringern können.
-
Reduziert den Koksverbrauch:
- Sinter enthält bereits zugesetzte Flussmittel, wie Kalkstein oder Dolomit, die den Bedarf an zusätzlichen Flussmitteln während des Hochofenbetriebs verringern.Dadurch sinkt der Koksbedarf, da Koks in erster Linie als Reduktionsmittel und Wärmequelle verwendet wird.
- Die Verringerung des Koksverbrauchs senkt nicht nur die Betriebskosten, sondern minimiert auch die Umweltbelastung durch geringere Kohlenstoffemissionen.
-
Gewährleistet eine gleichbleibende chemische Zusammensetzung:
- Sinter wird mit einer kontrollierten chemischen Zusammensetzung hergestellt, die einen stabilen und vorhersehbaren Input für den Hochofen gewährleistet.Diese Konsistenz ist entscheidend für die Aufrechterhaltung der gewünschten Qualität von geschmolzenem Eisen und Schlacke.
- Die einheitliche Zusammensetzung des Sinters verringert das Risiko von Schwankungen in den thermischen und chemischen Bedingungen des Ofens, was zu einem reibungsloseren Betrieb und höherer Produktivität führt.
-
Ersetzt Roheisenerz-Feinkorn:
- Rohes Eisenerz-Feinkorn lässt sich aufgrund seiner feinen Partikelgröße nur schwer direkt in einem Hochofen verwenden, was zu einem schlechten Gasfluss und einer ineffizienten Verbrennung führen kann.Sinter bietet eine stückige Alternative, die einfacher zu handhaben und im Ofen effektiver ist.
- Durch den Einsatz von Sinter können Hochofenbetreiber die Möllermischung optimieren und so die Gesamteffizienz des Eisenherstellungsprozesses verbessern.
-
Verbessert die Energie-Effizienz:
- Durch den Einsatz von Sinter wird der Energiebedarf für den Hochofenbetrieb reduziert.Durch das Vorheizen und die teilweise Reduktion von Eisenoxiden während des Sinterprozesses wird die Wärmebelastung des Ofens gesenkt.
- Diese Energieeffizienz führt zu Kosteneinsparungen und einer geringeren CO2-Bilanz, was den modernen Nachhaltigkeitszielen entspricht.
-
Erleichtert eine bessere Schlackenbildung:
- Sinter enthält Flussmittel, die die Bildung von Schlacke mit den gewünschten Eigenschaften, wie Viskosität und Schmelzpunkt, fördern.Eine ordnungsgemäße Schlackenbildung ist für die Entfernung von Verunreinigungen und den reibungslosen Betrieb des Hochofens unerlässlich.
- Durch die kontrollierte Zugabe von Flussmitteln in den Sinter wird sichergestellt, dass die Schlackenzusammensetzung konstant bleibt, was die Gesamteffizienz des Eisenherstellungsprozesses erhöht.
Zusammenfassend lässt sich sagen, dass Sinter ein wichtiger Bestandteil des Hochofenprozesses ist, der zahlreiche Vorteile bietet, wie z. B. eine verbesserte Permeabilität, einen geringeren Koksverbrauch, eine gleichbleibende chemische Zusammensetzung und eine verbesserte Energieeffizienz.Seine Rolle bei der Optimierung der Möllermischung und der Gewährleistung eines stabilen Ofenbetriebs macht ihn in der modernen Eisenerzeugung unverzichtbar.
Zusammenfassende Tabelle:
Die wichtigsten Vorteile von Sinter | Auswirkungen auf den Hochofen |
---|---|
Verbessert die Permeabilität | Verbessert Gasfluss, Wärmeübertragung und chemische Reaktionen. |
Reduziert den Koksverbrauch | Senkt die Betriebskosten und den Kohlenstoffausstoß. |
Sorgt für eine gleichbleibende Zusammensetzung | Stabilisiert die Bedingungen im Ofen und verbessert die Qualität des geschmolzenen Eisens. |
Ersetzt Roheisenerz-Feinkorn | Optimiert die Möllermischung für bessere Effizienz. |
Verbessert die Energie-Effizienz | Reduziert die Wärmebelastung und spart Energie und Kosten. |
Erleichtert eine bessere Schlackenbildung | Sorgt für eine ordnungsgemäße Entfernung von Verunreinigungen und einen reibungslosen Betrieb des Ofens. |
Erfahren Sie, wie Sinter Ihren Eisenherstellungsprozess revolutionieren kann. Kontaktieren Sie unsere Experten noch heute !