Die thermische Verdampfung ist eine weit verbreitete Technik der physikalischen Gasphasenabscheidung (PVD) zur Herstellung dünner Schichten. Dabei wird ein festes Material in einer Hochvakuumkammer erhitzt, bis es verdampft. Dabei entsteht ein Dampfstrom, der durch das Vakuum wandert und sich auf einem Substrat ablagert und eine dünne Schicht bildet. Diese Methode ist besonders nützlich für Anwendungen wie OLEDs und Dünnschichttransistoren, da sie einfach ist und gleichmäßige Schichten erzeugt. Das Verfahren beruht auf zwei Grundprinzipien: der Verdampfung des Ausgangsmaterials und dem Einsatz einer Wärmequelle, z. B. eines Heizelements aus Wolfram oder eines Elektronenstrahls, um die erforderliche Wärmeenergie zu erzeugen. Die Vakuumumgebung gewährleistet eine minimale Verunreinigung und eine gleichmäßige Abscheidung.
Die wichtigsten Punkte werden erklärt:
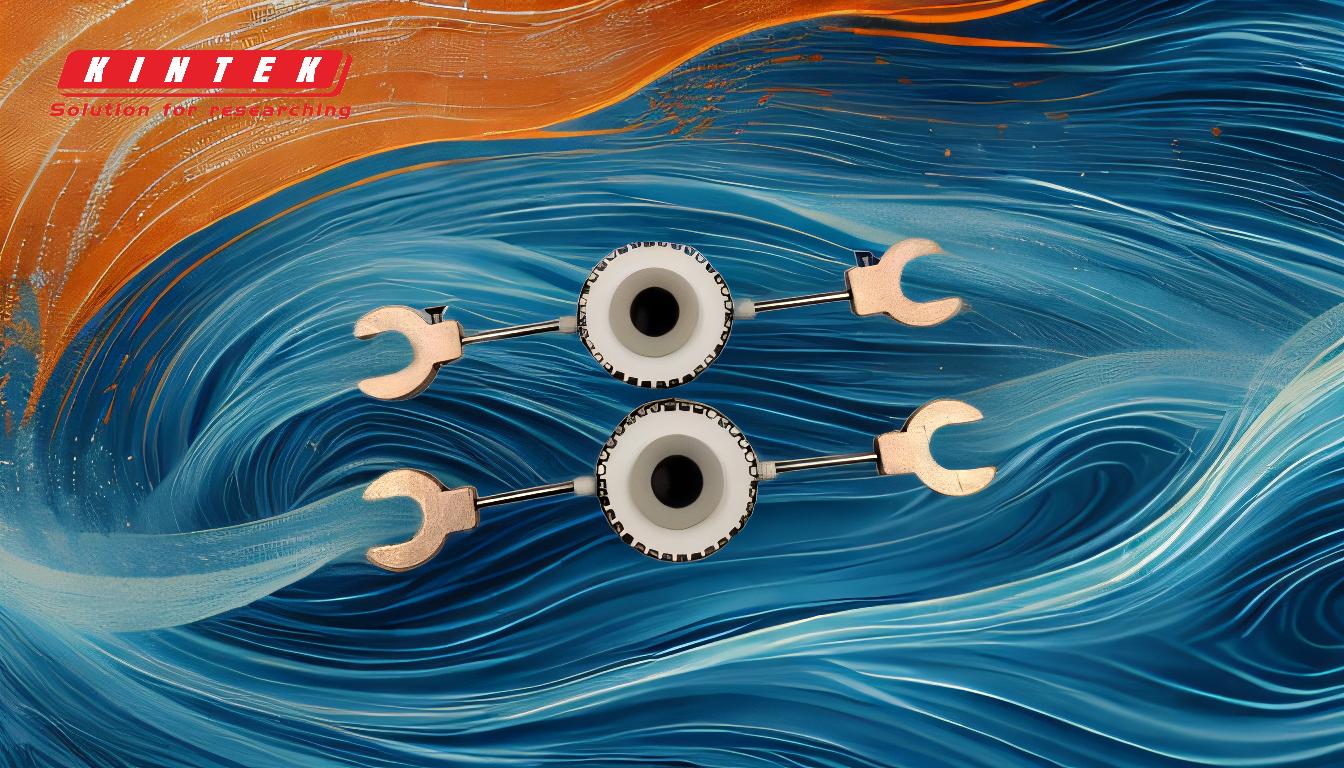
-
Definition und Zweck der thermischen Verdampfung:
- Die thermische Verdampfung ist ein Verfahren zur physikalischen Abscheidung aus der Gasphase (PVD), mit dem dünne Schichten auf Substraten erzeugt werden.
- Aufgrund seiner Fähigkeit, gleichmäßige und hochwertige Beschichtungen zu erzeugen, eignet es sich besonders gut für Anwendungen in der Elektronik, z. B. OLEDs und Dünnschichttransistoren.
-
Prozess-Übersicht:
- Das Verfahren beginnt mit dem Einbringen des Zielmaterials (Feststoff) in eine Hochvakuumkammer.
- Das Material wird mit einer thermischen Energiequelle, z. B. einem Heizelement aus Wolfram oder einem Elektronenstrahl, erhitzt, bis es seinen Verdampfungspunkt erreicht.
- Sobald das Material verdampft ist, bildet es eine Dampfwolke in der Vakuumkammer.
-
Die Rolle der Vakuumumgebung:
- Die Vakuumumgebung ist für den Prozess von entscheidender Bedeutung, da sie eine Kontamination durch Gase oder Verunreinigungen verhindert.
- Sie sorgt auch dafür, dass das verdampfte Material ungehindert durch die Kammer wandert, ohne zu streuen oder mit anderen Atomen zu reagieren, was zu einer gleichmäßigen Abscheidung auf dem Substrat führt.
-
Abscheidung des Dünnfilms:
- Das verdampfte Material wandert durch das Vakuum, kondensiert auf dem Substrat und bildet einen festen, dünnen Film.
- Das Substrat kann je nach Anwendung aus verschiedenen Materialien bestehen, z. B. aus Glas, Silizium oder Polymeren.
-
Wärmequellen bei der thermischen Verdampfung:
- Widerstandsheizung: Ein Heizelement aus Wolfram wird üblicherweise verwendet, um die für die Verdampfung des Zielmaterials erforderliche Wärmeenergie bereitzustellen.
- Elektronenstrahlverdampfung: Ein Elektronenstrahl kann zum Schmelzen und Verdampfen von Materialien verwendet werden, die höhere Temperaturen erfordern oder mit Widerstandserhitzung nur schwer zu verdampfen sind.
-
Vorteile der thermischen Verdampfung:
- Vereinfachung: Das Verfahren ist einfach und erfordert keine komplexe Ausrüstung.
- Einheitliche Beschichtungen: Die Vakuumumgebung sorgt dafür, dass die abgeschiedene Schicht gleichmäßig und frei von Fehlern ist.
- Vielseitigkeit: Es kann für eine Vielzahl von Materialien verwendet werden, einschließlich Metallen, Halbleitern und Dielektrika.
-
Anwendungen der thermischen Verdampfung:
- OLEDs (Organische lichtemittierende Dioden): Die thermische Verdampfung wird zur Abscheidung organischer Schichten in OLED-Displays verwendet.
- Dünnschichttransistoren: Es wird bei der Herstellung von Dünnschichttransistoren für elektronische Geräte verwendet.
- Optische Beschichtungen: Diese Technik wird auch zur Herstellung von reflektierenden oder antireflektierenden Beschichtungen für optische Komponenten verwendet.
-
Herausforderungen und Überlegungen:
- Materielle Beschränkungen: Einige Materialien sind aufgrund ihres hohen Schmelzpunktes oder ihrer Reaktivität nicht für die thermische Verdampfung geeignet.
- Vakuum-Wartung: Die Aufrechterhaltung eines hohen Vakuums ist von entscheidender Bedeutung, und jede undichte Stelle kann die Qualität der Dünnschicht beeinträchtigen.
- Kompatibilität der Substrate: Das Substrat muss dem Abscheidungsprozess standhalten können, ohne sich zu zersetzen.
Zusammenfassend lässt sich sagen, dass die thermische Verdampfung eine vielseitige und effektive Methode zur Herstellung dünner Schichten ist, insbesondere in der Elektronik- und Optikindustrie. Die Abhängigkeit von einer Vakuumumgebung und kontrollierten Wärmequellen sorgt für hochwertige, gleichmäßige Beschichtungen und macht es zu einer bevorzugten Wahl für viele Anwendungen.
Zusammenfassende Tabelle:
Aspekt | Einzelheiten |
---|---|
Definition | Verfahren der physikalischen Gasphasenabscheidung (PVD) zur Herstellung dünner Schichten. |
Wichtigstes Prinzip | Verdampfung des Ausgangsmaterials in einer Hochvakuumumgebung. |
Wärmequellen | Heizelemente aus Wolfram oder Elektronenstrahlen. |
Vorteile | Einfaches Verfahren, gleichmäßige Beschichtungen, vielseitige Materialverträglichkeit. |
Anwendungen | OLEDs, Dünnschichttransistoren, optische Beschichtungen. |
Herausforderungen | Materialbeschränkungen, Wartung des Vakuums, Kompatibilität der Substrate. |
Entdecken Sie, wie die thermische Verdampfung Ihre Dünnschichtprozesse verbessern kann kontaktieren Sie uns noch heute !