Das Sintern ist ein vielseitiges Fertigungsverfahren zur Herstellung von Bauteilen aus einer Vielzahl von Werkstoffen, darunter Metalle, Keramiken, Polymere und Verbundwerkstoffe.Bei diesem Verfahren werden pulverförmige Materialien verdichtet und unter ihren Schmelzpunkt erhitzt, um feste Strukturen mit verbesserten Eigenschaften zu bilden.Zu den üblicherweise verwendeten Werkstoffen gehören Eisen- und Kohlenstoffstähle, Edelstahl, Aluminium, Nickel, Kupfer, Titanlegierungen, Molybdän, Wolfram und Keramiken.Die Auswahl dieser Werkstoffe richtet sich nach ihren spezifischen Eigenschaften und der gewünschten Anwendung, z. B. Hochtemperaturbeständigkeit, Festigkeit oder Haltbarkeit.Das Sintern ist besonders vorteilhaft für Werkstoffe mit hohem Schmelzpunkt und wird häufig in der Pulvermetallurgie, der additiven Fertigung und der Herstellung von Komponenten wie Zahnrädern, Lagern und Filtern eingesetzt.
Die wichtigsten Punkte erklärt:
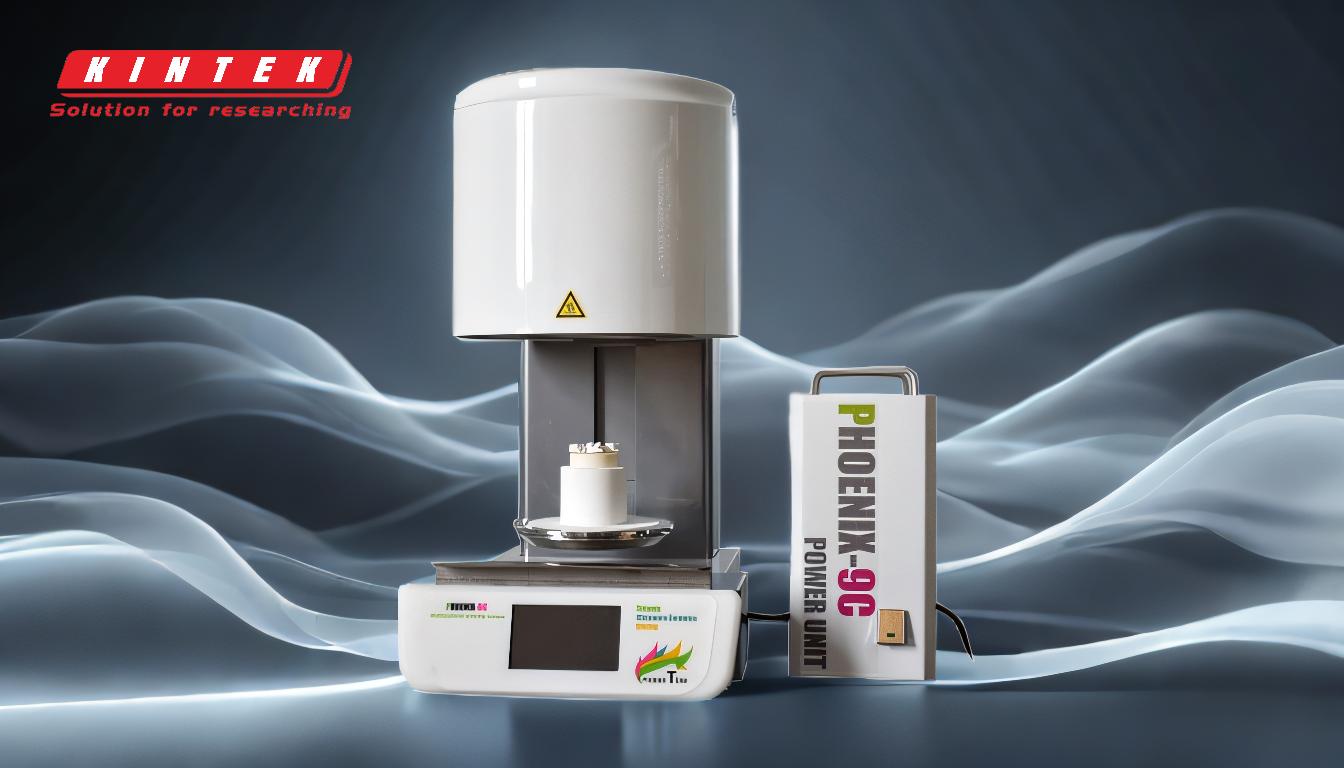
-
Übliche Materialien beim Sintern:
- Eisen und Kohlenstoffstähle:Aufgrund ihrer Festigkeit und ihres günstigen Preises werden sie häufig zum Sintern verwendet.Sie werden häufig verarbeitet, um mechanische Eigenschaften wie Härte und Verschleißfestigkeit zu verbessern.
- Rostfreier Stahl:Edelstahl ist für seine Korrosionsbeständigkeit und Langlebigkeit bekannt und wird daher gerne für Sinterteile in Branchen wie der Automobil- und Luftfahrtindustrie verwendet.
- Aluminium:Aluminium ist leicht und korrosionsbeständig und wird beim Sintern für Anwendungen verwendet, die ein geringes Gewicht und eine hohe Wärmeleitfähigkeit erfordern.
- Nickel- und Kupfer-Legierungen:Diese Werkstoffe werden wegen ihrer elektrischen Leitfähigkeit, Wärmebeständigkeit und Festigkeit geschätzt und eignen sich daher für elektrische und Hochtemperaturanwendungen.
- Titan-Legierungen:Werden wegen ihres guten Verhältnisses von Festigkeit zu Gewicht und ihrer Biokompatibilität beim Sintern verwendet, häufig in der Medizin und der Luft- und Raumfahrt.
- Molybdän und Wolfram:Diese hochschmelzenden Metalle werden für Anwendungen gesintert, die eine extreme Temperaturbeständigkeit erfordern, wie z. B. bei Ofenkomponenten und Teilen für die Luft- und Raumfahrt.
- Keramiken:Sinterkeramik wird aufgrund ihrer Hochtemperaturstabilität, ihrer Verschleißfestigkeit und ihrer elektrischen Isolationseigenschaften verwendet und ist daher ideal für Bauteile wie Lager und Isolatoren.
- Polymere:Gesinterte Polymere werden aufgrund ihrer Vielseitigkeit und einfachen Verarbeitung für das Rapid Prototyping und die Filterherstellung verwendet.
-
Anwendungen von gesinterten Materialien:
- Pulvermetallurgie:Das Sintern ist ein Schlüsselprozess in der Pulvermetallurgie, bei dem Metallpulver verdichtet und gesintert wird, um kleine Bauteile wie Zahnräder, Riemenscheiben und Lager herzustellen.
- Additive Fertigung:Moderne Sintertechnologien wie das selektive Lasersintern (SLS) werden im 3D-Druck eingesetzt, um komplexe Bauteile aus Metall- und Polymerpulvern herzustellen.
- Hochtemperatur-Komponenten:Materialien wie Molybdän, Wolfram und Keramik werden für den Einsatz in Hochtemperaturumgebungen gesintert, z. B. für Ofenteile und Komponenten für die Luft- und Raumfahrt.
- Filter und Prototypen:Gesinterte Polymere und Metalle werden zur Herstellung von Filtern und Prototypen verwendet, wobei die Fähigkeit des Verfahrens zur Herstellung poröser und komplizierter Strukturen genutzt wird.
-
Vorteile des Sinterns:
- Verbesserte Materialeigenschaften:Das Sintern verbessert die mechanischen, thermischen und elektrischen Eigenschaften von Werkstoffen und macht sie für anspruchsvolle Anwendungen geeignet.
- Kosteneffizienz:Das Verfahren ermöglicht die Herstellung komplexer Formen mit minimalem Materialabfall, was die Kosten senkt.
- Vielseitigkeit:Das Sintern kann bei einer Vielzahl von Werkstoffen eingesetzt werden, darunter Metalle, Keramiken und Polymere, und ermöglicht die Herstellung verschiedenster Komponenten.
- Nachhaltigkeit:Beim Sintern werden häufig recycelte Materialien verwendet und es entsteht weniger Abfall als bei herkömmlichen Herstellungsverfahren.
-
Technologische Fortschritte beim Sintern:
- Verbesserte Sintertechniken:Fortschritte bei den Sintertechnologien, wie das Spark-Plasma-Sintern (SPS) und das Mikrowellensintern, haben die Effizienz und Präzision des Prozesses verbessert.
- Integration der additiven Fertigung:Das Sintern wird zunehmend in die additiven Fertigungsverfahren integriert und ermöglicht die Herstellung komplexer, leistungsstarker Bauteile.
- Materialveredelung:Laufende Forschung und Entwicklung haben zur Verfeinerung von Sinterwerkstoffen geführt, wodurch sich ihre Eigenschaften verbessert und ihre Anwendungsmöglichkeiten erweitert haben.
Durch das Verständnis der Werkstoffe und Verfahren, die beim Sintern zum Einsatz kommen, können die Hersteller die geeigneten Werkstoffe und Techniken auswählen, um spezifische Anwendungsanforderungen zu erfüllen und eine optimale Leistung und Kosteneffizienz zu gewährleisten.
Zusammenfassende Tabelle:
Werkstoff | Wichtige Eigenschaften | Allgemeine Anwendungen |
---|---|---|
Eisen und Kohlenstoffstähle | Festigkeit, Erschwinglichkeit, Verschleißfestigkeit | Zahnräder, Lager, Automobilteile |
Rostfreier Stahl | Korrosionsbeständigkeit, Langlebigkeit | Luft- und Raumfahrt, medizinische Geräte |
Aluminium | Leichtgewicht, Wärmeleitfähigkeit | Wärmetauscher, leichte Komponenten |
Nickel- und Kupfer-Legierungen | Elektrische Leitfähigkeit, Wärmebeständigkeit | Elektrische Komponenten, Hochtemperaturteile |
Titan-Legierungen | Hohes Verhältnis von Festigkeit zu Gewicht, Biokompatibilität | Medizinische Implantate, Komponenten für die Luft- und Raumfahrt |
Molybdän & Wolfram | Extreme Temperaturbeständigkeit | Ofenteile, Komponenten für die Luft- und Raumfahrt |
Keramiken | Hochtemperaturstabilität, Verschleißfestigkeit | Lager, Isolatoren |
Polymere | Vielseitigkeit, einfache Verarbeitung | Filter, schnelles Prototyping |
Benötigen Sie Hilfe bei der Auswahl der richtigen Materialien für Ihr Sinterverfahren? Kontaktieren Sie noch heute unsere Experten !