Stickstoff wird häufig in Wärmebehandlungsverfahren eingesetzt, da er eine kontrollierte Atmosphäre schafft, die die Oxidation und Entkohlung von Metallteilen verhindert.Er fungiert als Schutzgas, um bestehende Atmosphären zu spülen, und kann als Trägergas für kohlenstoffgesteuerte Umgebungen dienen.Stickstoff ist zwar nicht völlig inert, wird aber häufig mit geringen Mengen Wasserstoff gemischt, um seine Schutzeigenschaften zu verbessern.Diese Kombination gewährleistet eine stabile und kontrollierte Umgebung, die für das Erreichen der gewünschten Materialeigenschaften während der Wärmebehandlung entscheidend ist.
Die wichtigsten Punkte werden erklärt:
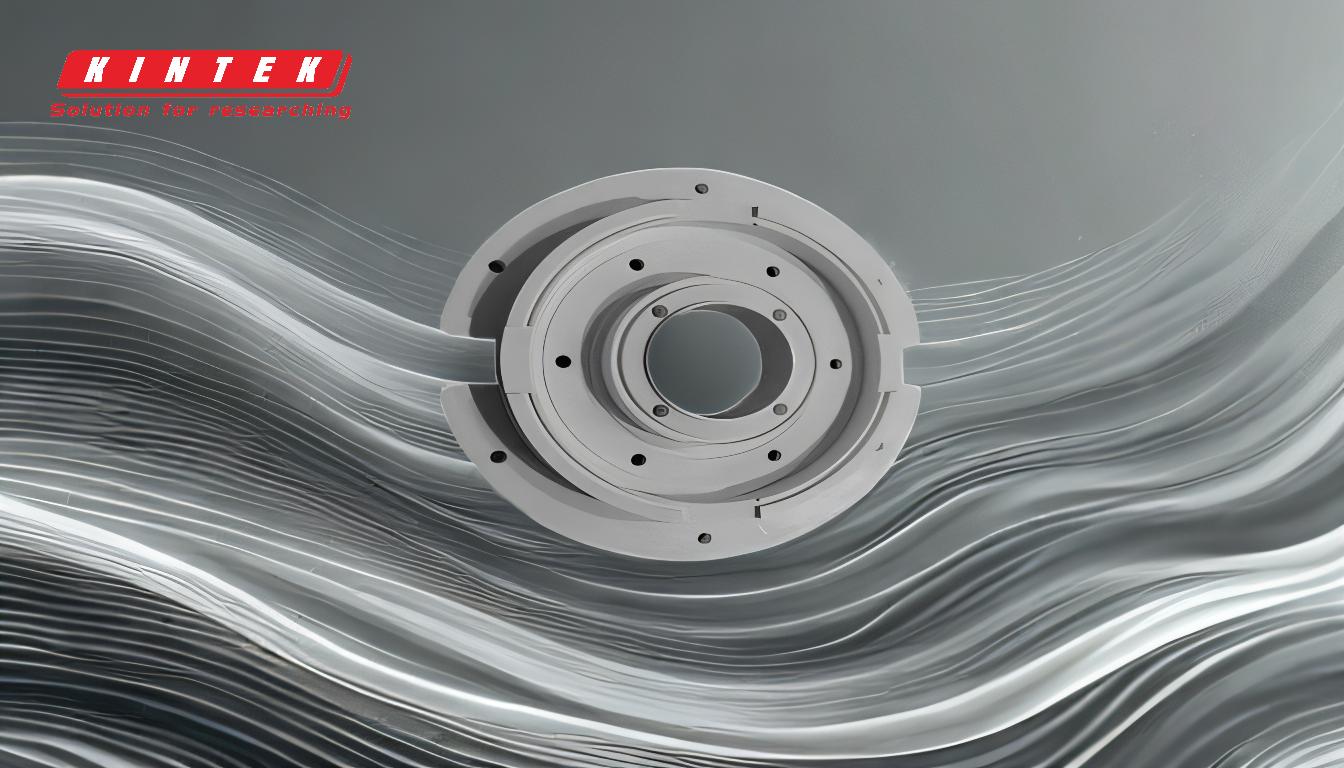
-
Blanketing-Effekt von Stickstoff
- Stickstoff bildet eine Schutzschicht um das wärmezubehandelnde Teil, die es vor Sauerstoff und anderen reaktiven Gasen abschirmt.
- Dies verhindert die Oxidation, die zu einer Verschlechterung der Oberfläche führen kann, und die Entkohlung, die das Material durch Verringerung des Kohlenstoffgehalts schwächt.
- Der Abschirmungseffekt ist für die Erhaltung der Integrität und Qualität des behandelten Teils von wesentlicher Bedeutung.
-
Spülen vorhandener Atmosphären
- Stickstoff wird verwendet, um unerwünschte Gase, wie z. B. Sauerstoff, aus der Wärmebehandlungskammer zu verdrängen.
- Dadurch wird eine saubere und kontrollierte Umgebung gewährleistet, die frei von Verunreinigungen ist, die den Wärmebehandlungsprozess negativ beeinflussen könnten.
- Das Spülen ist besonders wichtig bei Prozessen wie dem Glühen, wo eine genaue Kontrolle der Atmosphäre entscheidend ist.
-
Trägergas für kohlenstoffkontrollierte Atmosphären
- Stickstoff kann als Trägergas für kohlenstoffreiche Atmosphären dienen und so das Einbringen von Kohlenstoff in das Material bei Verfahren wie dem Aufkohlen erleichtern.
- Dies trägt dazu bei, die gewünschte Oberflächenhärte und Verschleißfestigkeit der behandelten Teile zu erreichen.
- Die Verwendung von Stickstoff als Trägergas gewährleistet eine gleichmäßige Verteilung des Kohlenstoffs, was zu gleichmäßigen Ergebnissen führt.
-
Stickstoffs begrenzte Inertheit
- Obwohl Stickstoff oft als inertes Gas bezeichnet wird, ist er nicht völlig inert und kann unter bestimmten Bedingungen reagieren.
- Um seine Schutzeigenschaften zu verbessern, wird Stickstoff normalerweise mit einem niedrigen Taupunkt (zwischen -75°F und -110°F) geliefert, um den Feuchtigkeitsgehalt zu minimieren.
- Dadurch wird das Risiko unerwünschter Reaktionen während der Wärmebehandlung verringert.
-
Wasserstoffmischung für verbesserte Leistung
- Stickstoff wird häufig mit Wasserstoff in einem Verhältnis von 90/10 gemischt, um seine Wirksamkeit als Schutzatmosphäre zu verbessern.
- Wasserstoff trägt zur Reduzierung von Oberflächenoxiden bei und verbessert die Gesamtqualität des behandelten Teils.
- Jüngste Richtlinien empfehlen, den Wasserstoffgehalt auf 3 % oder weniger zu begrenzen, um sicherzustellen, dass das Gasgemisch inert und sicher bleibt.
-
Bedeutung von kontrollierten Atmosphären
- Die Verwendung von Stickstoff und Stickstoff-Wasserstoff-Gemischen gewährleistet eine stabile und kontrollierte Umgebung während der Wärmebehandlung.
- Dies ist entscheidend für das Erreichen gleichbleibender Materialeigenschaften wie Härte, Festigkeit und Haltbarkeit.
- Kontrollierte Atmosphären minimieren auch das Risiko von Defekten und sorgen für qualitativ hochwertige Ergebnisse bei industriellen Anwendungen.
Wenn man diese Kernpunkte versteht, wird klar, warum Stickstoff bei Wärmebehandlungsprozessen bevorzugt wird.Seine Fähigkeit, eine kontrollierte, schützende Umgebung zu schaffen, macht ihn unentbehrlich, um bei verschiedenen industriellen Anwendungen optimale Ergebnisse zu erzielen.
Zusammenfassende Tabelle:
Schlüsselrolle von Stickstoff in der Wärmebehandlung | Vorteile |
---|---|
Blanketing-Effekt | Verhindert Oxidation und Entkohlung und gewährleistet die Integrität der Teile. |
Spülung bestehender Atmosphären | Verdrängt Sauerstoff und Verunreinigungen und sorgt so für eine saubere Umgebung. |
Trägergas für kohlenstoffkontrollierte Atmosphären | Sorgt für eine gleichmäßige Kohlenstoffverteilung und damit für Härte und Verschleißfestigkeit. |
Begrenzte Inertheit | Wird mit niedrigem Taupunkt geliefert, um Feuchtigkeit und Reaktionen zu minimieren. |
Wasserstoff-Mischung | Verbessert die Schutzeigenschaften durch Reduzierung von Oberflächenoxiden. |
Kontrollierte Atmosphären | Erzielt konstante Materialeigenschaften und minimiert Defekte. |
Optimieren Sie Ihren Wärmebehandlungsprozess mit Stickstoff. Kontaktieren Sie noch heute unsere Experten um mehr zu erfahren!