Zielfertigung
Herstellungsmethoden
Sputtertargetplatten und -rohre werden mit herkömmlichen, auf das jeweilige Materialsystem zugeschnittenen Verfahren hergestellt. Diese Verfahren umfassen eine Reihe von Techniken, darunter Gießen, Walzen und maschinelle Bearbeitung, die auf der Grundlage der Materialeigenschaften und der gewünschten Targetspezifikationen ausgewählt werden. So erfordern beispielsweise Werkstoffe mit hohem Schmelzpunkt, wie Wolfram und Molybdän, oft spezielle Verfahren wie die Pulvermetallurgie, um die erforderliche Dichte und Homogenität zu erreichen.
Bei Verbundwerkstoffen, die in der Regel aus zwei oder mehr verschiedenen Materialien bestehen, ist der Herstellungsprozess noch komplizierter. Die Pulvermetallurgie, ein vielseitiges Verfahren, wird häufig eingesetzt, um diese Materialien zu einer zusammenhängenden Struktur zu verbinden. Dieser Prozess umfasst mehrere Schritte: Die Rohstoffe werden zunächst zu einer homogenen Pulvermischung vermischt, die dann unter hohem Druck in die gewünschte Form gepresst wird. Die verdichtete Form wird anschließend bei hohen Temperaturen gesintert, um eine Bindung zwischen den Partikeln zu erreichen, so dass ein dichtes und einheitliches Ziel entsteht.
Für Materialien, die einen noch höheren Grad an Reinheit und Kontrolle erfordern, werden fortschrittliche Techniken wie das Vakuum-Lichtbogenschmelzen oder das Elektronenstrahlschmelzen eingesetzt. Diese Verfahren verbessern nicht nur die Reinheit des Targets, sondern verfeinern auch seine Mikrostruktur, was für eine optimale Sputterleistung entscheidend ist. Die Wahl des Herstellungsverfahrens ist daher ein entscheidender Faktor für die endgültige Qualität und Leistung des Sputtertargets.
Reinigungstechniken
Um ultrahochreine Sputtertargets zu erhalten, ist die Entfernung von Verunreinigungen von entscheidender Bedeutung. Dieser Prozess kann durch zwei Hauptmethoden erreicht werden: Elektronenstrahlschmelzen in einem Hochvakuumsystem und Auslaugen in reaktiven Salzen. Jede Methode bietet einzigartige Vorteile und eignet sich für unterschiedliche Materialtypen und Fertigungsanforderungen.
Elektronenstrahlschmelzen
Das Elektronenstrahlschmelzen (EBM) arbeitet unter Hochvakuumbedingungen, wodurch das Risiko einer Verunreinigung durch atmosphärische Gase minimiert wird. Bei diesem Verfahren wird ein fokussierter Elektronenstrahl auf das Zielmaterial gerichtet, wodurch es schmilzt und anschließend erstarrt. Diese Methode eignet sich besonders gut für Materialien mit hohem Schmelzpunkt, da die vom Elektronenstrahl erzeugte intensive Hitze die Schmelztemperatur leicht übersteigen kann. Die Hochvakuumumgebung sorgt dafür, dass alle Restgase evakuiert werden und das Material weiter gereinigt wird.
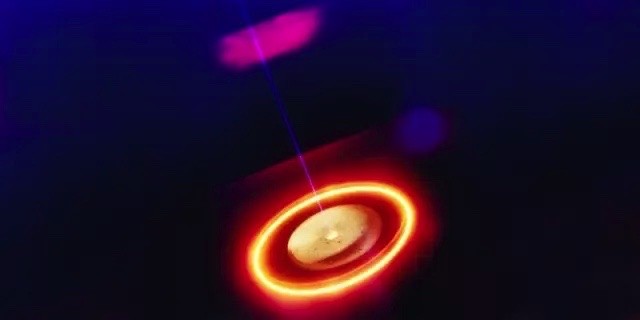
Auslaugen in reaktiven Salzen
Beim Auslaugen hingegen wird das Zielmaterial in ein Bad mit reaktiven Salzen getaucht. Diese Salze reagieren selektiv mit Verunreinigungen und lösen diese auf, so dass das reine Material zurückbleibt. Diese Technik wird häufig für Materialien verwendet, die empfindlich auf hohe Temperaturen reagieren oder für solche, die einen kontrollierteren Reinigungsprozess erfordern. Die Wahl des Salzes und die Dauer des Auslaugungsprozesses sind entscheidende Faktoren, die die Reinheit des Endprodukts erheblich beeinflussen können.
Beide Methoden sind wesentliche Bestandteile des Herstellungsprozesses für ultrahochreine Sputtertargets und gewährleisten, dass das Endprodukt die strengen Reinheitsanforderungen erfüllt, die für Hochleistungsanwendungen erforderlich sind.
Backing Plates/Tubing, Löten und Diffusionsbonden
Trägerplatten spielen eine entscheidende Rolle für die Leistung von Sputtertargets, da sie Eigenschaften wie einen niedrigen spezifischen Widerstand, eine hohe magnetische Permeabilität und eine gute Wärmeleitfähigkeit aufweisen müssen. Diese Eigenschaften sind unerlässlich, um einen effizienten Energietransfer und eine optimale Magnetfeldverteilung während des Sputterprozesses zu gewährleisten.
Zur Befestigung der Targets an diesen Trägerplatten werden zwei Haupttechniken eingesetzt: Löten und Diffusionskleben.Löten erfordert die Verwendung eines Zusatzmetalls mit einem niedrigeren Schmelzpunkt als die Materialien des Targets und der Trägerplatte. Diese Methode ermöglicht eine genaue Kontrolle über die Festigkeit und die thermischen Eigenschaften der Verbindung und eignet sich daher für Anwendungen, die ein spezielles Wärmemanagement erfordern.
Im Gegensatz dazu,Diffusionskleben ist ein Festkörperverbindungsverfahren, bei dem die Materialien nicht geschmolzen werden. Stattdessen werden hoher Druck und hohe Temperaturen eingesetzt, um eine starke metallurgische Verbindung zwischen dem Target und der Trägerplatte herzustellen. Diese Technik ist besonders vorteilhaft für Hochtemperaturanwendungen und Materialien, die sich bei hohen Temperaturen zersetzen können, da sie thermische Schäden minimiert und eine stabile Verbindung gewährleistet.
Die Wahl zwischen Löten und Diffusionskleben hängt oft von den spezifischen Anforderungen der Anwendung ab, einschließlich der Materialeigenschaften des Targets und der Trägerplatte, den Betriebsbedingungen und den gewünschten Klebeeigenschaften. Beide Methoden sind für die erfolgreiche Integration von Targets mit Trägerplatten unerlässlich und gewährleisten die Langlebigkeit und Effizienz des Sputterprozesses.
Gleichmäßigkeit des Sputtertargets und Filmqualität
Makroskopische und mikroskopische Überlegungen
Die Gleichmäßigkeit von Sputtertargets ist nicht nur eine wünschenswerte Eigenschaft, sondern ein entscheidender Faktor, der die Qualität der abgeschiedenen Schichten direkt beeinflusst. Diese Gleichmäßigkeit wird durch eine Kombination von makroskopischen und mikroskopischen Merkmalen beeinflusst, die jeweils eine wichtige Rolle bei der Bestimmung der Sputterrate und des gesamten Schichtbildungsprozesses spielen.
Makroskopische Faktoren:
- Porosität: Das Vorhandensein von Poren im Targetmaterial kann zu Unregelmäßigkeiten im Sputterprozess führen. Poren wirken wie Barrieren und stören den gleichmäßigen Fluss der Atome vom Target zum Substrat. Dies kann zu einer ungleichmäßigen Schichtdicke und -zusammensetzung führen, was sich nachteilig auf die Leistung des Endprodukts auswirkt.
- Korngröße: Die Größe der Körner im Targetmaterial ist ein weiterer makroskopischer Faktor, der die Gleichmäßigkeit beeinflusst. Größere Körner können zu ungleichmäßigen Sputterraten führen, da der Materialabtrag über die gesamte Oberfläche des Targets weniger gleichmäßig erfolgt.
Mikroskopische Faktoren:
- Kristallausrichtung: Auf mikroskopischer Ebene spielt die Ausrichtung der Kristallkörner innerhalb des Zielmaterials eine entscheidende Rolle. Unterschiedliche Kristallorientierungen weisen unterschiedliche Sputterraten auf, ein Phänomen, das als bevorzugtes Sputtern bekannt ist. Dies kann zu lokalen Schwankungen in der Zusammensetzung und Struktur der Schicht führen, was sich auf ihre Gesamtqualität und Leistung auswirkt.
Durch eine sorgfältige Kontrolle sowohl der makroskopischen als auch der mikroskopischen Faktoren können die Hersteller einen gleichmäßigeren Sputterprozess gewährleisten, der zu qualitativ hochwertigeren Schichten mit gleichbleibenden Eigenschaften führt.
Porosität und Hohlräume
Porosität und Hohlräume sind kritische Defekte, die in verschiedenen Phasen des Herstellungsprozesses auftreten können und die Gleichmäßigkeit der Sputterrate und die Gesamtqualität der abgeschiedenen Schicht erheblich beeinträchtigen. Diese Defekte entstehen oft durch die inhärenten Grenzen herkömmlicher Herstellungsverfahren wie Gießen, Pulvermetallurgie und sogar während der Reinigungsphasen, in denen Hochtemperaturprozesse zu mikrostrukturellen Unstimmigkeiten führen können.
Bei der Pulvermetallurgie beispielsweise kann die Konsolidierung von Metallpulvern zu einer festen Form mikroskopisch kleine Hohlräume hinterlassen, wenn der Sinterprozess nicht perfekt kontrolliert wird. Auch beim Gießen kann Gaseinschluss zu Porosität führen, insbesondere bei Materialien mit hohem Schmelzpunkt, bei denen die Viskosität des geschmolzenen Metalls das Entweichen von Gasen verhindern kann. Diese Hohlräume und Poren können als bevorzugte Stellen für die Entstehung von Rissen dienen, was zu ungleichmäßigen Sputteringraten und schlechter Schichtqualität führt.
Darüber hinaus kann das Vorhandensein von Porosität und Hohlräumen auch die thermische und elektrische Leitfähigkeit des Targetmaterials beeinträchtigen, was den Sputterprozess weiter erschwert. So können beispielsweise Bereiche mit hoher Porosität im Vergleich zu dichteren Bereichen mit unterschiedlichen Raten sputtern, was zu Schwankungen in der Schichtdicke und -zusammensetzung führt. Diese Ungleichmäßigkeit ist besonders problematisch bei Anwendungen, bei denen es auf präzise Schichteigenschaften ankommt, wie z. B. bei der Halbleiterherstellung.
Bevorzugtes Sputtern und Kornmorphologie
Unterschiedliche Kristallorientierungen weisen unterschiedliche Sputteringraten auf, ein Phänomen, das alspräferentielles Sputtern. Diese selektive Erosion kann einen erheblichen Einfluss auf dieMorphologie der Körner undGröße des Materials beeinflussen, die unmittelbar von den angewandten Herstellungsverfahren beeinflusst werden.
Im Zusammenhang mit derPhysikalischen Gasphasenabscheidung (PVD) Verfahren hängt die Gleichmäßigkeit des gesputterten Films stark von der Konsistenz des Zielmaterials ab. DieKornstruktur des Targets, die durch ihre Ausrichtung und Größe gekennzeichnet ist, spielt eine entscheidende Rolle bei der Bestimmung der Sputtereffizienz und der resultierenden Schichtqualität. So können beispielsweise Körner mit bestimmten Ausrichtungen schneller erodieren, was zu einer ungleichmäßigen Zerstäubung führt und die Integrität der abgeschiedenen Schicht beeinträchtigen kann.
Die Herstellungsverfahren, wie zum Beispiel diePulvermetallurgie undHeißisostatisches Pressen (HIP)sind entscheidend für die Gestaltung der Kornstruktur des Zielmaterials. Diese Prozesse beeinflussen nicht nur die Dichte und Porosität des Targets, sondern bestimmen auch die endgültige Kornmorphologie, die wiederum das Sputterverhalten beeinflusst. Daher ist das Verständnis und die Kontrolle dieser Herstellungsparameter von entscheidender Bedeutung für die Optimierung der Leistung von PVD-Sputtertargets.
Heiß-Isostatisches Pressen (HIP) und Hochdruck-Wärmebehandlung (HPHT)
HIP-Anwendungen
Heiß-Isostatisches Pressen (HIP) ist ein entscheidender Prozess bei der Herstellung hochwertiger Sputtertargets, insbesondere für Materialien, die durch Gießen und Pulvermetallurgie hergestellt werden. Die Hauptfunktion des HIP besteht darin, Porosität und Hohlräume in diesen Materialien zu beseitigen und dadurch ihre Dichte und Gleichmäßigkeit zu verbessern. Bei diesem Verfahren wird das Material in einer kontrollierten Umgebung einem hohen Druck und einer hohen Temperatur ausgesetzt, wodurch das Material komprimiert wird und eine nahezu perfekte Dichte erreicht.
Die Bedeutung von HIP für die Verringerung der Porosität kann gar nicht hoch genug eingeschätzt werden. Porosität, die durch verschiedene Herstellungsprozesse entstehen kann, hat einen erheblichen Einfluss auf die Sputterrate und die Gesamtqualität der gebildeten Schicht. Durch die Entfernung dieser mikroskopisch kleinen Hohlräume gewährleistet HIP, dass sich das Sputtertarget während des Sputterprozesses gleichmäßig verhält, was zu einer gleichmäßigeren Schichtabscheidung führt.
Außerdem trägt HIP zur strukturellen Integrität der Sputtertargets bei. Materialien, die HIP unterzogen werden, weisen bessere mechanische Eigenschaften auf, einschließlich einer höheren Festigkeit und Zähigkeit. Dies ist besonders wichtig für Hochleistungsanwendungen, bei denen die Zuverlässigkeit und Langlebigkeit der Sputtertargets von entscheidender Bedeutung sind.
Zusammenfassend lässt sich sagen, dass HIP ein unverzichtbares Verfahren für die Herstellung von Sputtertargets ist, das sicherstellt, dass sie die strengen Anforderungen an hohe Dichte, Gleichmäßigkeit und strukturelle Integrität erfüllen.
Vorteile von HPHT
Die Hochdruck-Hochtemperatur-Behandlung (HPHT) bietet mehrere Vorteile bei der Herstellung verschiedener Materialsysteme. Einer der wichtigsten Vorteile ist die verbesserte Temperaturgleichmäßigkeit, die gewährleistet, dass das gesamte Materialsystem gleichmäßigen thermischen Bedingungen ausgesetzt ist. Diese Gleichmäßigkeit ist entscheidend für die Integrität und Leistungsfähigkeit des Endprodukts.
HPHT ermöglicht auch kontrollierte Abkühlungsraten, was für die Vermeidung von thermischen Spannungen und Rissen in den Werkstoffen unerlässlich ist. Durch eine präzise Steuerung des Abkühlungsprozesses können die Hersteller die gewünschten mechanischen Eigenschaften erreichen und Defekte minimieren. Dieses Maß an Kontrolle ist besonders wichtig bei der Herstellung hochwertiger Materialien wie Diamanten, bei denen selbst kleine Mängel die Qualität und den Marktwert erheblich beeinträchtigen können.
Darüber hinaus ermöglicht HPHT wiederholbare Prozesszeiten, die sicherstellen, dass jede Materialcharge unter identischen Bedingungen hergestellt wird. Diese Wiederholbarkeit ist für eine gleichbleibende Produktqualität und -leistung von entscheidender Bedeutung. In der Diamantenindustrie kann HPHT beispielsweise weniger attraktive Diamanten in hochwertige farblose, rosafarbene, blaue oder kanariengelbe Diamanten verwandeln und so deren Marktwert erheblich steigern.
Beim HPHT-Verfahren werden die Diamanten hohem Druck und hohen Temperaturen ausgesetzt, was nicht nur ihre Farbe, sondern auch ihre Klarheit verbessert. Dies macht HPHT-Diamanten in der Schmuckindustrie sehr begehrt, wo Klarheit und Farbe die entscheidenden Faktoren für die Qualität eines Diamanten sind. Trotz einiger Unterschiede zwischen HPHT- und CVD-Diamanten (Chemical Vapor Deposition) wird die HPHT-Behandlung häufig eingesetzt, um die Oberflächenbeschaffenheit von CVD-Diamanten zu verbessern und sicherzustellen, dass sie den hohen Qualitätsstandards entsprechen.
Zusammenfassend lässt sich sagen, dass die HPHT-Behandlung eine Reihe von Vorteilen bietet, die für die Herstellung hochwertiger Materialien unerlässlich sind. Ihre Fähigkeit, eine verbesserte Temperaturgleichmäßigkeit, kontrollierte Abkühlungsraten und wiederholbare Prozesszeiten zu bieten, macht sie zu einem unschätzbaren Verfahren in verschiedenen Industriezweigen, insbesondere bei der Herstellung von hochwertigen Materialien wie Diamanten.
Kanüliertes HIP und Diffusionsbonden
Das kanülierte Heiß-Isostatische Pressen (HIP) und die Diffusionsbondierung sind unverzichtbar für die Herstellung komplizierter Formen und die Gewährleistung einer stabilen Verbindung zwischen dem Target und der Trägerplatte. Diese Verfahren sind besonders vorteilhaft, wenn es um hochwertige Materialien geht, die hervorragende Eigenschaften wie Korrosions- und Verschleißfestigkeit aufweisen müssen, und die oft auf kostengünstigeren Substraten aufgebracht werden, um die Kosteneffizienz zu optimieren.
HIP kann mehrere Diffusionsverbindungen in einem einzigen Prozesszyklus ermöglichen und ist damit eine vielseitige und effiziente Lösung für komplexe Fertigungsanforderungen. Das Verfahren ist mit einer Vielzahl von Werkstoffen kompatibel, darunter Metalle wie Nickel, Kobalt, Wolfram, Titan, Molybdän, Aluminium, Kupfer und Eisenlegierungen sowie Keramiken, Gläser, Intermetallics und Hochleistungskunststoffe.
Das Verfahren erfordert eine strenge Kontrolle der Reinheit des Inertgases, in der Regel Argon, um die Spezifikationen von Kunden, Militär und Industrie zu erfüllen oder zu übertreffen. Reproduzierbare, automatisierte HIP-Zyklen werden auf die spezifischen Kundenbedürfnisse zugeschnitten und gewährleisten die Rückverfolgbarkeit der Komponenten von Anfang bis Ende. Darüber hinaus steht technische Unterstützung für das HIP-Verfahren für neuartige Materialien oder Legierungen zur Verfügung, und das Verfahren kann an verschiedene Werkzeuganforderungen angepasst werden, um die Kompatibilität mit dem HIP-Zyklus und den Materialspezifikationen sicherzustellen.
Durch den Einsatz von kanüliertem HIP und Diffusionskleben können Hersteller nicht nur starke und zuverlässige Verbindungen erzielen, sondern auch komplexe Geometrien herstellen, die mit anderen Methoden nur schwer zu realisieren wären. Diese Vielseitigkeit und Präzision machen diese Verfahren für die Herstellung hochwertiger Sputtertargets unverzichtbar.
Kontaktieren Sie uns für eine kostenlose Beratung
Die Produkte und Dienstleistungen von KINTEK LAB SOLUTION werden von Kunden auf der ganzen Welt anerkannt. Unsere Mitarbeiter helfen Ihnen gerne bei allen Fragen weiter. Kontaktieren Sie uns für eine kostenlose Beratung und sprechen Sie mit einem Produktspezialisten, um die am besten geeignete Lösung für Ihre Anwendungsanforderungen zu finden!