Einführung in die Ofenatmosphäre
Ofenatmosphären spielen eine wesentliche Rolle im Wärmebehandlungsprozess von Materialien. Die Atmosphäre in einem Ofen kann die Eigenschaften des Endprodukts wie Festigkeit und Haltbarkeit erheblich beeinflussen. Eine Atmosphäre ist ein Gas oder eine Gasmischung, die das in einem Ofen behandelte Material umgibt. Zu den am häufigsten verwendeten Ofenatmosphären gehören Luft, Stickstoff, Wasserstoff und Argon. Das Verständnis der Eigenschaften jeder Atmosphäre und ihrer Auswirkungen auf das Material ist für die Herstellung hochwertiger Produkte von entscheidender Bedeutung. Die Verwendung inerter Atmosphären wie Stickstoff und Argon ist wichtig, um unerwünschte Reaktionen und Oxidation während des Wärmebehandlungsprozesses zu verhindern.
Inhaltsverzeichnis
- Einführung in die Ofenatmosphäre
- Was ist eine inerte Atmosphäre?
- Warum ist es wichtig, inerte Atmosphären zu verwenden?
- Häufige Gase in Ofenatmosphären
- Wärmebehandlungsprozesse, die inerte Atmosphären erfordern
- So messen Sie die Ofenatmosphäre
- Werkzeuge zur Messung und Probenahme
- Schlussfolgerung zur Bedeutung inerter Atmosphären
Was ist eine inerte Atmosphäre?
Bei Laborarbeiten ist es wichtig, eine kontrollierte Umgebung für bestimmte Reaktionen oder Prozesse zu schaffen. Eine solche Umgebung ist eine inerte Atmosphäre, die durch die Abwesenheit reaktiver Gase gekennzeichnet ist, die das gewünschte Ergebnis beeinträchtigen könnten. Zur Schaffung dieser Umgebung werden üblicherweise Inertgase wie Stickstoff, Argon und Helium verwendet, was durch Techniken wie Spülen, Abdecken oder den Einsatz von Handschuhboxen erreicht werden kann.
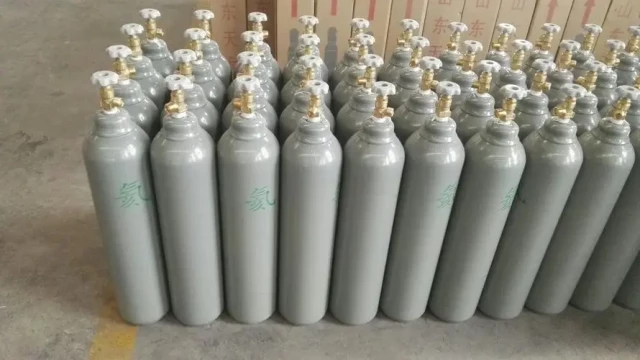
Definition der inerten Atmosphäre
Eine Inertatmosphäre ist eine kontrollierte Umgebung für verschiedene Labor- und Industrieanwendungen, in der die Atmosphäre frei von reaktiven Gasen ist, die unerwünschte chemische Reaktionen hervorrufen könnten. Zur Schaffung einer solchen Umgebung werden üblicherweise Inertgase wie Stickstoff, Argon und Helium verwendet. Diese Gase gelten als inert, da sie nicht chemisch mit anderen Substanzen reagieren, was sie ideal für die Schaffung einer kontrollierten Umgebung macht.
Eine inerte Atmosphäre schaffen
Es gibt verschiedene Möglichkeiten, eine inerte Atmosphäre zu schaffen, darunter Spülen, Abdecken und die Verwendung von Handschuhboxen. Beim Spülen wird die gesamte Luft aus einem Behälter oder System entfernt und durch ein Inertgas ersetzt. Beim Überdecken wird ein Behälter mit einem Inertgas gefüllt, um eine Gasschicht zu erzeugen, die das Eindringen von Luft oder anderen reaktiven Gasen verhindert. Handschuhkästen sind geschlossene Arbeitsbereiche, die eine Inertgasatmosphäre nutzen, um eine kontrollierte Umgebung zu schaffen.
Verwendung inerter Atmosphären
Inerte Atmosphären werden in verschiedenen Labor- und Industrieanwendungen eingesetzt, einschließlich Wärmebehandlungsprozessen wie Sintern, Blankglühen und Karbonitrieren. Diese Prozesse erfordern streng kontrollierte Atmosphären, um hochwertige Teile für Branchen wie Luft- und Raumfahrt, Automobil und Petrochemie herzustellen. Inerte Atmosphären werden auch bei der Herstellung von Halbleitern verwendet, wo die Reinheit von entscheidender Bedeutung ist.
Gängige Inertgase
Die am häufigsten verwendeten Inertgase zur Schaffung einer Inertatmosphäre sind Stickstoff, Argon und Helium. Stickstoff ist das kostengünstigste und am weitesten verbreitete Inertgas und wird häufig in Anwendungen eingesetzt, bei denen Feuchtigkeit und Sauerstoff entfernt werden müssen. Argon ist ein dichteres Gas und wird häufig in Anwendungen verwendet, die eine stärkere Inertgasbarriere erfordern. Helium ist das leichteste Edelgas und wird in Anwendungen eingesetzt, bei denen eine geringe Dichte und eine hohe Wärmeleitfähigkeit erforderlich sind.
Zusammenfassend lässt sich sagen, dass eine inerte Atmosphäre eine kontrollierte Umgebung ist, in der die Atmosphäre frei von reaktiven Gasen ist, die das gewünschte Ergebnis beeinträchtigen könnten. Diese Umgebung ist bei Labor- und Industrieanwendungen von entscheidender Bedeutung, bei denen es auf Präzision und Kontrolle ankommt. Die Verwendung inerter Atmosphärengase wie Stickstoff, Argon und Helium ist entscheidend für die Schaffung dieser Umgebung und die Gewährleistung der Qualität, Zuverlässigkeit und Reproduzierbarkeit von Laborexperimenten und industriellen Prozessen.
Warum ist es wichtig, inerte Atmosphären zu verwenden?
Inerte Atmosphärengase sind für viele Wärmebehandlungsprozesse unerlässlich, da sie eine kontrollierte Umgebung schaffen können, die unerwünschte chemische Reaktionen, Oxidation und Kontamination des Produkts verhindert. In diesem Abschnitt werden wir die Gründe diskutieren, warum es wichtig ist, in Ofenatmosphären Inertatmosphären zu verwenden.
Verhinderung unerwünschter chemischer Reaktionen
Bei der Wärmebehandlung, dem Sintern oder Hartlöten kann die Anwesenheit bestimmter Gase wie Sauerstoff oder Wasserdampf zu Oxidation oder anderen unerwünschten chemischen Reaktionen führen. Inerte Gase wie Stickstoff, Argon und Helium werden verwendet, um Sauerstoff und Wasserdampf aus der Ofenkammer zu verdrängen und so eine Atmosphäre ohne reaktive Gase zu schaffen. Dadurch wird sichergestellt, dass der Prozess kontrolliert wird und das gewünschte Ergebnis erzielt wird.
Verbesserung der Produktqualität
Der Einsatz von Inertgasen kann die Effizienz des Prozesses steigern, indem die zum Erreichen der gewünschten Temperatur erforderliche Energiemenge reduziert und der Abkühlprozess beschleunigt wird. Darüber hinaus trägt die inerte Atmosphäre dazu bei, Oxidation und Kontamination des Produkts zu verhindern, was zu einem qualitativ hochwertigeren Endergebnis führt. Dies ist besonders wichtig für Branchen wie die Luft- und Raumfahrt, die Automobilindustrie oder die Petrochemie, in denen geschäftskritische Teile hergestellt werden.
Präzision und Wiederholbarkeit erreichen
Bei Wärmebehandlungsprozessen, die eine stark kontrollierte Atmosphäre erfordern, wie z. B. Blankglühen, Sintern und Karbonitrieren, ist das Erreichen von Präzision und Wiederholbarkeit von entscheidender Bedeutung. Die in diesen Prozessen verwendeten Öfen müssen eine kontrollierte Atmosphäre unterstützen, um erfolgreiche, hochpräzise und wiederholbare Ergebnisse für diese Teile zu erzielen. Um sicherzustellen, dass der Prozess kontrolliert wird und das gewünschte Ergebnis erzielt wird, werden inerte Atmosphären verwendet.
Reduzierung von Ofenschäden und Verletzungen von Mitarbeitern
Eine nicht ordnungsgemäß kontrollierte Atmosphäre kann zu einer Beschädigung des Ofens oder, noch schlimmer, zu Verletzungen der Mitarbeiter führen. Inertgase werden verwendet, um chemische Reaktionen auf der Oberfläche eines Teils zu verhindern, die dessen Qualität und Leistung beeinträchtigen und zu Ausschussteilen führen würden. Dies wiederum führt zu finanziellen Verlusten, Zeitverschwendung und möglicherweise gefährlichen Auswirkungen für diejenigen, die das Teil verwenden, wenn die Probleme nicht erkannt werden.
Zusammenfassend lässt sich sagen, dass die Verwendung inerter Atmosphärengase in Ofenatmosphären unerlässlich ist, um einen kontrollierten und effizienten Prozess sicherzustellen, unerwünschte chemische Reaktionen zu verhindern und qualitativ hochwertige Produkte herzustellen. Es ist wichtig zu verstehen, warum wir sie verwenden und welche Atmosphäre für eine bestimmte Anwendung am besten ist, um erfolgreiche, hochpräzise und wiederholbare Ergebnisse zu erzielen.
Häufige Gase in Ofenatmosphären
Inerte Atmosphärengase spielen in der Ofenatmosphäre eine entscheidende Rolle, um unerwünschte chemische Reaktionen oder Oxidation von Materialien während der Hochtemperaturverarbeitung zu verhindern. Zu den am häufigsten für Anwendungen in inerter Atmosphäre verwendeten Gasen gehören Stickstoff, Argon und Helium.
Stickstoff
Aufgrund seiner Verfügbarkeit und Erschwinglichkeit ist Stickstoff das am häufigsten verwendete Gas. Es handelt sich um ein reaktionsträges Gas, das für eine Schutzatmosphäre sorgt. Sein Gehalt an Kohlenstoff, Sauerstoff und Stickstoff reagiert nicht mit Stahl, was es zu einem idealen Gas für Ofenatmosphären macht. Stickstoff wird zur Verhinderung von Oxidation bei Wärmebehandlungsanwendungen eingesetzt und verdrängt effektiv Sauerstoff aus der Atmosphäre.
Argon
Argon wird häufig für Prozesse verwendet, die einen höheren Reinheitsgrad oder einen längeren Zeitraum der Hochtemperaturverarbeitung erfordern. Argon ist ein völlig inertes „Edelgas“ und reagiert nicht mit Materialien, mit denen es in Kontakt kommt. Es verdrängt Sauerstoff und ist somit ein ideales Gas für Anwendungen, bei denen Oxidation unerwünscht ist. Argon ist teurer als Stickstoff, hat aber den Vorteil, dass es bei Temperaturen über 1800 °C ohne Reaktionsgefahr eingesetzt werden kann.
Helium
Helium wird verwendet, wenn eine geringe Löslichkeit erforderlich ist, da es das am wenigsten reaktive Gas ist. Seine geringe Dichte und hohe Wärmeleitfähigkeit machen es zu einem idealen Gas für bestimmte Anwendungen. Helium wird häufig in der Gaschromatographie, Lecksuche und Kühlanwendungen eingesetzt.
Zusammenfassend lässt sich sagen, dass diese Gase eine sauerstofffreie Umgebung schaffen, die die verarbeiteten Materialien schützt und konsistente und genaue Ergebnisse gewährleistet. Ohne den Einsatz inerter Atmosphärengase kann es zu unerwünschten Reaktionen kommen, die zu Produktfehlern, einer verminderten Produktqualität und sogar zu Geräteschäden führen. Die Wahl des Gases hängt von den spezifischen Anforderungen des Wärmebehandlungsprozesses ab, und die Art der erforderlichen Atmosphäre bestimmt die Art des für die Durchführung erforderlichen Ofens.
Wärmebehandlungsprozesse, die inerte Atmosphären erfordern
Wärmebehandlungsprozesse, die hohe Temperaturen und kontrollierte Atmosphären erfordern, basieren häufig auf inerten Atmosphärengasen wie Stickstoff, Argon und Helium. Diese Gase spielen eine entscheidende Rolle bei der Schaffung einer Umgebung, die frei von Sauerstoff und anderen reaktiven Gasen ist, die chemische Reaktionen oder Oxidation der behandelten Materialien verursachen könnten.
Warum inerte Atmosphären unerlässlich sind
Die Abwesenheit von Sauerstoff und anderen reaktiven Gasen in der Ofenatmosphäre trägt dazu bei, die Reinheit der Materialien aufrechtzuerhalten und Verunreinigungen oder unerwünschte Reaktionen zu verhindern. Inerte Atmosphären sind für eine Vielzahl von Anwendungen unerlässlich, darunter die Wärmebehandlung von Metallen, das Glühen von Glas und das Sintern von Keramik. Die Verwendung inerter Atmosphärengase in Ofenatmosphären ist entscheidend für die Gewährleistung der Qualität und Konsistenz der Endprodukte. Jegliche Abweichungen in der Ofenatmosphäre können erhebliche Auswirkungen auf die Eigenschaften des Endprodukts haben. Daher ist eine strenge Kontrolle der Ofenumgebung unerlässlich.
Inerte Gase, die in Wärmebehandlungsprozessen verwendet werden
Argon, Helium und Stickstoff sind die in Wärmebehandlungsprozessen am häufigsten verwendeten Inertgase. Die Wahl des Inertgases hängt von der Art des zu behandelnden Materials und den spezifischen Anforderungen des Wärmebehandlungsprozesses ab. Im Allgemeinen sind Argon und Helium inerter als Wasserstoff. Eine reine Stickstoffatmosphäre schützt das wärmebehandelte Teil und kann zum Spülen der vorhandenen Atmosphäre oder als Trägergas für kohlenstoffkontrollierte Atmosphären verwendet werden.
Wärmebehandlungsprozesse, die inerte Atmosphären verwenden
Inerte Atmosphären werden in einer Vielzahl von Wärmebehandlungsprozessen eingesetzt, darunter:
- Glühen (Nichteisenmetalle, legierter Stahl und Entkohlung)
- Neutrale Härtung
- Temperieren
- Nitrieren (legierte Stähle, rostfreie Stähle und Nitrierstähle)
- Sintern
- Hartlöten (Stickstoff fungiert als Trägergas)
- Vakuumprozesse
Inertgaskombinationen
In einigen Fällen kann bei Wärmebehandlungsprozessen eine Kombination von Inertgasen verwendet werden. Beispielsweise eignet sich eine Atmosphäre aus Wasserstoff + Stickstoff gut zum Blankglühen; Glühen von Edelstahl, legiertem Stahl und Nichteisenstahl; neutrale Härtung; und Sintern. Die Verwendung einer Atmosphäre aus Wasserstoff + Argon funktioniert beim Blankglühen; Glühen von Edelstahl, legiertem Stahl und Nichteisenstahl; und Sintern.
Abschluss
Zusammenfassend lässt sich sagen, dass inerte Atmosphärengase eine entscheidende Rolle bei Wärmebehandlungsprozessen spielen, die hohe Temperaturen und kontrollierte Atmosphären erfordern. Die Verwendung dieser Gase trägt dazu bei, die Reinheit der Materialien aufrechtzuerhalten und Verunreinigungen oder unerwünschte Reaktionen zu verhindern. Die Wahl des Inertgases hängt vom spezifischen Wärmebehandlungsprozess und der Art des zu behandelnden Materials ab. Inerte Atmosphären sind für die Gewährleistung hochwertiger Endprodukte in der Wärmebehandlungsindustrie unerlässlich.
So messen Sie die Ofenatmosphäre
Die Messung der Ofenatmosphäre ist ein entscheidender Schritt, um sicherzustellen, dass die Gase der Inertatmosphäre ordnungsgemäß funktionieren und der Prozess reibungslos abläuft. Im Folgenden sind die Schritte zur Messung der Ofenatmosphäre aufgeführt.
Schritt 1: Bestimmen Sie den Typ des Analysegeräts
Es gibt verschiedene Möglichkeiten, die Ofenatmosphäre zu messen, darunter Wärmeleitfähigkeits-, Infrarot- und Zirkonoxidanalysatoren. Jede Methode hat ihre Stärken und Schwächen und die Wahl des geeigneten Analysators hängt von der spezifischen Anwendung und der Art der verwendeten Gase ab.
Schritt 2: Kalibrieren Sie den Analysator
Vor der Verwendung des Analysegeräts ist es wichtig, es zu kalibrieren, um sicherzustellen, dass es genaue Messwerte liefert. Bei der Kalibrierung wird der Analysator einem bekannten Gasgemisch ausgesetzt und so lange eingestellt, bis die richtigen Werte angezeigt werden.
Schritt 3: Installieren Sie den Analysator
Installieren Sie den Analysator je nach Analysatortyp im Ofen oder an der Entnahmestelle im Rauchgasstrom.
Schritt 4: Nehmen Sie die Messung vor
Sobald der Analysator installiert ist, führen Sie die Messung durch. Die Häufigkeit der Messungen hängt von der jeweiligen Anwendung ab. Es ist jedoch wichtig, die Ofenatmosphäre regelmäßig zu überwachen, um ihre Integrität aufrechtzuerhalten und eine gleichbleibende Produktqualität sicherzustellen.
Schritt 5: Interpretieren Sie die Ergebnisse
Interpretieren Sie die vom Analysegerät erhaltenen Ergebnisse und ergreifen Sie gegebenenfalls Korrekturmaßnahmen. Wenn die Ergebnisse darauf hinweisen, dass die Ofenatmosphäre nicht ordnungsgemäß funktioniert, passen Sie die Inertatmosphärengase an, um das richtige Gleichgewicht aufrechtzuerhalten.
Durch die Befolgung dieser Schritte können Hersteller ihre Prozesse optimieren und qualitativ hochwertige Produkte präzise und effizient herstellen.
Werkzeuge zur Messung und Probenahme
Inerte Atmosphärengase sind entscheidende Bestandteile der Ofenatmosphären und die Gewährleistung ihrer Sicherheit und Wirksamkeit bei Hochtemperaturvorgängen ist von entscheidender Bedeutung. Die Messung und Probenahme dieser Gase ist daher eine wichtige Aufgabe im Labor.
Gasanalysatoren
Gasanalysatoren sind hochentwickelte Werkzeuge, die eine präzise Analyse von Gasproben durchführen und Verunreinigungen und Konzentrationsänderungen erkennen. Sie werden zur Messung einer Vielzahl von Parametern verwendet, darunter Sauerstoff, Kohlendioxid und Wasserdampf. Gasanalysatoren sind hochempfindlich und können selbst kleinste Änderungen in der Gaszusammensetzung erkennen, was sie ideal für die Überwachung inerter Atmosphärengase macht.
Gaschromatographen
Gaschromatographen sind leistungsstarke Werkzeuge, die einzelne Komponenten einer Gasprobe trennen und analysieren können. Sie sind in der Lage, Spuren von Verunreinigungen zu erkennen und die Konzentrationen verschiedener Gase genau zu messen. Gaschromatographen werden häufig in Laborumgebungen eingesetzt und können zur Analyse inerter Atmosphärengase aus Sicherheits- und Qualitätskontrollgründen verwendet werden.
Probenahmeausrüstung
Für die Messung und Überwachung inerter Atmosphärengase ist eine geeignete Probenahmeausrüstung unerlässlich. Gasprobenbeutel werden beispielsweise zum Sammeln von Gasproben zur Analyse verwendet, während Gasspritzen verwendet werden, um Proben direkt aus einem Gasstrom zu entnehmen. Andere Arten von Probenahmegeräten umfassen Gasdetektoren, die das Vorhandensein bestimmter Gase erkennen können, und Gassensoren, die Gaskonzentrationen in Echtzeit messen können.
Kalibrierungsausrüstung
Kalibriergeräte sind für die Gewährleistung der Genauigkeit von Gasanalysatoren und anderen Gasmessgeräten unerlässlich. Kalibriergase wie Stickstoff und Sauerstoff werden zur Kalibrierung von Gasanalysatoren und zur Gewährleistung genauer Messwerte verwendet. Kalibriergeräte werden auch zur Überprüfung der Genauigkeit von Gassensoren und anderen Gasmessgeräten eingesetzt.
Vorteile der Messung und Probenahme von inerten Atmosphärengasen
Die Messung und Probenahme von inerten Atmosphärengasen ist wichtig für die Aufrechterhaltung der Sicherheit und Qualität von Wärmebehandlungsprozessen. Regelmäßige Probenahmen und Analysen von Inertatmosphärengasen können dabei helfen, potenzielle Probleme im Ofenbetrieb zu erkennen und kostspielige Schäden an der Ausrüstung zu verhindern. Es kann Laborfachkräften und Ingenieuren auch dabei helfen, ihre Wärmebehandlungsprozesse zu optimieren, was zu einer verbesserten Produktqualität und geringeren Produktionskosten führt.
Zusammenfassend lässt sich sagen, dass die Messung und Probenahme von inerten Atmosphärengasen eine wichtige Aufgabe in Laborumgebungen ist. Gasanalysatoren, Gaschromatographen, Probenahmegeräte, Kalibriergeräte und andere Werkzeuge sind wesentliche Bestandteile dieses Prozesses. Durch die regelmäßige Messung und Überwachung inerter Atmosphärengase können Laborfachleute die Sicherheit und Wirksamkeit von Wärmebehandlungsprozessen gewährleisten und die Qualität ihrer Produkte aufrechterhalten.
Schlussfolgerung zur Bedeutung inerter Atmosphären
Inerte Atmosphären spielen eine entscheidende Rolle bei der Wärmebehandlung von Materialien. Sie tragen dazu bei, Oxidation, Entkohlung oder andere unerwünschte Reaktionen zu verhindern, die in Gegenwart von Sauerstoff oder anderen reaktiven Gasen auftreten können. Durch die Verwendung von Inertgasen wie Stickstoff oder Argon in Ofenatmosphären können Materialien in einer kontrollierten Umgebung erhitzt und abgekühlt werden, wodurch konsistente und zuverlässige Ergebnisse gewährleistet werden. Es ist wichtig, die Atmosphäre im Ofen zu messen und zu überwachen, um sicherzustellen, dass die gewünschten Bedingungen aufrechterhalten werden. Der ordnungsgemäße Einsatz inerter Atmosphären kann zu einer verbesserten Produktqualität, geringeren Ausschussraten und einer höheren Produktivität in der Wärmebehandlungsindustrie führen.
Kontaktieren Sie uns für eine kostenlose Beratung
Die Produkte und Dienstleistungen von KINTEK LAB SOLUTION werden von Kunden auf der ganzen Welt anerkannt. Unsere Mitarbeiter helfen Ihnen gerne bei allen Fragen weiter. Kontaktieren Sie uns für eine kostenlose Beratung und sprechen Sie mit einem Produktspezialisten, um die am besten geeignete Lösung für Ihre Anwendungsanforderungen zu finden!