Die PVD-Beschichtung (Physical Vapor Deposition) ist ein hochentwickeltes Verfahren, mit dem dünne, gut haftende und dauerhafte Schichten auf verschiedene Substrate aufgebracht werden.Das Verfahren umfasst mehrere wichtige Schritte, darunter die Reinigung und Vorbehandlung des Substrats, die Verdampfung des Zielmaterials, den Transport der verdampften Atome, die Reaktion mit Gasen (falls erforderlich) und die Abscheidung auf dem Substrat.Das Ergebnis ist eine mikrometerdicke Schicht, die das darunter liegende Material durchdringt und eine hervorragende Haftung und Beständigkeit gegen Abblättern oder Abplatzen bietet.Das Verfahren wird in einer Vakuumumgebung unter Verwendung von Inertgasen wie Argon durchgeführt, um eine chemisch nicht reaktive Atmosphäre zu gewährleisten, was die Qualität und Haltbarkeit der Beschichtung verbessert.
Die wichtigsten Punkte werden erklärt:
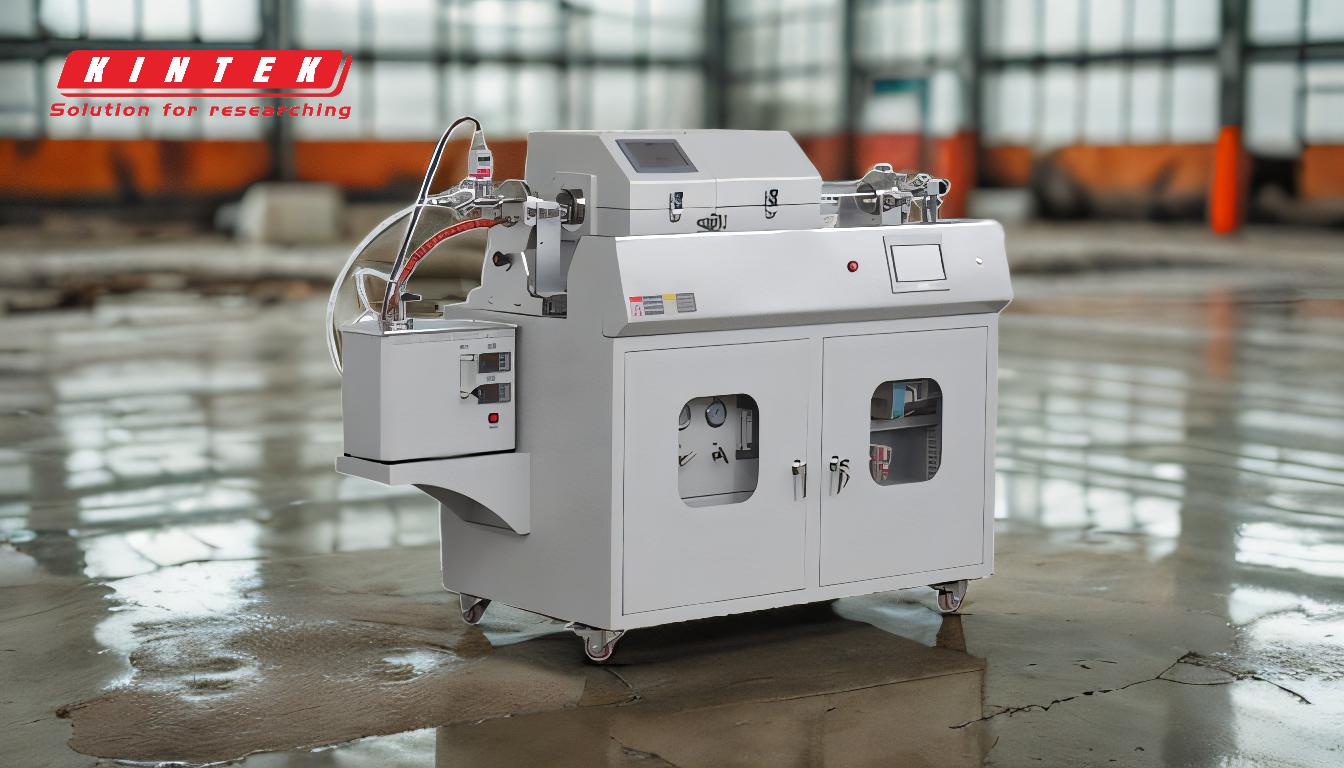
-
Reinigung und Vorbehandlung des Substrats:
- Reinigung: Das Substrat muss gründlich gereinigt werden, um alle Verunreinigungen wie Öle, Staub oder Oxide zu entfernen.Dies ist von entscheidender Bedeutung, da Verunreinigungen auf der Oberfläche die Haftung und Qualität der Beschichtung negativ beeinflussen können.Zu den Reinigungsmethoden gehören Ultraschallreinigung, chemische Reinigung oder Plasmareinigung.
- Vorbehandlung: Nach der Reinigung wird das Substrat häufig einer Vorbehandlung unterzogen, um die Haftung der Beschichtung zu verbessern.Dies kann eine Aufrauhung der Oberfläche, Ionenbeschuss oder das Aufbringen einer Grundierungsschicht beinhalten.Die Vorbehandlung stellt sicher, dass die Oberfläche chemisch und physikalisch für die Aufnahme der Beschichtung vorbereitet ist.
-
Verdampfung des Zielmaterials:
- Verdampfung/Ablation: Das Zielmaterial, die Quelle der Beschichtung, wird in eine Vakuumkammer gebracht.Mit Hilfe von Hochenergiequellen wie Elektronen, Ionen oder Lasern wird das Zielmaterial beschossen, wodurch es verdampft.Durch diesen Prozess wird das feste Zielmaterial in eine Dampfphase überführt.
- Transport: Die verdampften Atome oder Moleküle werden dann durch die Vakuumkammer zum Substrat transportiert.Die Vakuumumgebung sorgt dafür, dass die verdampften Partikel sich ohne Störungen durch Luftmoleküle fortbewegen, was eine kontrolliertere und gleichmäßigere Abscheidung ermöglicht.
-
Reaktion mit Gasen (falls erforderlich):
- Reaktion: In einigen Fällen reagieren die verdampften Atome mit ausgewählten Gasen (wie Stickstoff, Sauerstoff oder Methan), die in die Kammer eingeleitet werden.Bei dieser Reaktion entstehen Verbindungen wie Metalloxide, Nitride oder Karbide, die die endgültigen Eigenschaften der Beschichtung wie Härte, Farbe und chemische Beständigkeit bestimmen.
- Kontrolle der Reaktionsbedingungen: Die Reaktionsbedingungen, einschließlich Gaszusammensetzung, Druck und Temperatur, werden sorgfältig kontrolliert, um die gewünschten Beschichtungseigenschaften zu erzielen.So kann beispielsweise das Einleiten von Stickstoffgas zur Bildung von Metallnitriden führen, die für ihre Härte und Verschleißfestigkeit bekannt sind.
-
Abscheidung auf dem Substrat:
- Kondensation: Die verdampften Atome oder Moleküle kondensieren auf der Substratoberfläche und bilden einen dünnen Film.Der Abscheidungsprozess wird kontrolliert, um eine gleichmäßige Abdeckung und Dicke zu gewährleisten.Die Beschichtung baut sich Schicht für Schicht auf und verbindet sich fest mit dem Substrat.
- Adhäsion: Die Beschichtung durchdringt das darunter liegende Material und schafft eine starke Verbindung, die ein Abblättern oder Abplatzen verhindert.Dies ist einer der Hauptvorteile von PVD-Beschichtungen, da sie eine hervorragende Haftung und Haltbarkeit bieten.
-
Qualitätskontrolle und Endbearbeitung:
- Qualitätskontrolle: Nach der Beschichtung wird das beschichtete Substrat einer Qualitätskontrolle unterzogen, um sicherzustellen, dass die Beschichtung den erforderlichen Spezifikationen entspricht.Dazu können Messungen von Dicke, Härte, Haftung und Oberflächenrauheit gehören.Alle Mängel oder Unstimmigkeiten werden ermittelt und behoben.
- Endbearbeitung: Je nach Anwendung kann das beschichtete Substrat zusätzlichen Veredelungsprozessen unterzogen werden, um sein Aussehen oder seine Leistung zu verbessern.Dazu können Polieren, Glühen oder das Aufbringen einer Deckschicht zur Verbesserung der Korrosionsbeständigkeit oder des ästhetischen Erscheinungsbildes gehören.
-
Verwendung von Inertgasen:
- Inertgasatmosphäre: Während des gesamten PVD-Verfahrens werden inerte Gase wie Argon verwendet, um eine chemisch unreaktive Atmosphäre zu schaffen.Dies verhindert unerwünschte Reaktionen zwischen dem Beschichtungsmaterial und der Umgebung und gewährleistet die Reinheit und Qualität der Beschichtung.Das Inertgas trägt auch dazu bei, dass nach Abschluss des Beschichtungsvorgangs die restlichen Dämpfe aus der Kammer entfernt werden.
-
Vakuumumgebung:
-
Hoch-Vakuum-Bedingungen:
Der gesamte PVD-Prozess findet in einer Hochvakuumumgebung statt.Dies ist aus mehreren Gründen wichtig:
- Minimierung von Verunreinigungen: Das Vakuum reduziert das Vorhandensein von Verunreinigungen, die den Beschichtungsprozess stören könnten.
- Kontrollierte Abscheidung: Das Vakuum ermöglicht eine präzise Steuerung des Abscheidungsprozesses und gewährleistet gleichmäßige und hochwertige Beschichtungen.
- Energie-Effizienz: Die Vakuumumgebung minimiert die Energieverluste und macht den Prozess effizienter.
-
Hoch-Vakuum-Bedingungen:
Der gesamte PVD-Prozess findet in einer Hochvakuumumgebung statt.Dies ist aus mehreren Gründen wichtig:
-
Anwendungen und Vorteile:
- Breites Spektrum an Anwendungen: PVD-Beschichtungen werden in verschiedenen Industriezweigen eingesetzt, z. B. in der Automobilindustrie, der Luft- und Raumfahrt, der Medizintechnik und der Unterhaltungselektronik.Sie werden wegen ihrer Fähigkeit, die Leistung, Haltbarkeit und Ästhetik von Komponenten zu verbessern, geschätzt.
- Vorteile: PVD-Beschichtungen bieten zahlreiche Vorteile, darunter hohe Härte, Verschleißfestigkeit, Korrosionsbeständigkeit und die Möglichkeit, dekorative Oberflächen zu erzeugen.Außerdem sind sie umweltfreundlich, da sie keine schädlichen Chemikalien enthalten und keinen Sondermüll produzieren.
Zusammenfassend lässt sich sagen, dass das PVD-Beschichtungsverfahren eine hochgradig kontrollierte und präzise Methode zum Aufbringen dünner, haltbarer und haftender Beschichtungen auf eine breite Palette von Substraten ist.Wenn man jeden Schritt des Verfahrens versteht, von der Reinigung und Vorbehandlung bis zur Abscheidung und Qualitätskontrolle, kann man die Komplexität und Raffinesse bei der Herstellung von Hochleistungs-PVD-Beschichtungen verstehen.
Zusammenfassende Tabelle:
Schritt | Beschreibung |
---|---|
Reinigung & Vorbehandlung | Entfernt Verunreinigungen und bereitet das Substrat für eine bessere Haftung vor. |
Verdampfung | Das Zielmaterial wird mit Hilfe von Hochenergiequellen in einer Vakuumkammer verdampft. |
Reaktion mit Gasen | Verdampfte Atome reagieren mit Gasen und bilden Verbindungen wie Nitride oder Karbide. |
Abscheidung | Die verdampften Atome kondensieren auf dem Substrat und bilden eine dünne, dauerhafte Beschichtung. |
Qualitätskontrolle | Stellt sicher, dass die Beschichtung den Spezifikationen für Dicke, Härte und Haftung entspricht. |
Inerte Gase | Argon oder andere inerte Gase schaffen eine chemisch nicht reaktive Atmosphäre für hochwertige Beschichtungen. |
Vakuumumgebung | Hochvakuumbedingungen minimieren die Verunreinigung und gewährleisten eine präzise, gleichmäßige Abscheidung. |
Anwendungen | Einsatz in der Automobil-, Luft- und Raumfahrtindustrie, in medizinischen Geräten und in der Unterhaltungselektronik zur Leistungssteigerung. |
Vorteile | Hohe Härte, Verschleißfestigkeit, Korrosionsbeständigkeit und dekorative Oberflächen. |
Sind Sie bereit, Ihre Komponenten mit PVD-Beschichtungen zu veredeln? Kontaktieren Sie uns noch heute um mehr zu erfahren!