Die Schichtdicke bei der Elektronenstrahlverdampfung wird durch mehrere Faktoren beeinflusst, darunter die Geometrie der Verdampfungskammer, der Druck in der Vakuumkammer und die Substrattemperatur. Diese Faktoren können zu Schwankungen in der Schichtdicke führen, da die Abscheidung durch Zusammenstöße mit Restgasen und die Bewegung der verdampften Atome ungleichmäßig ist. Die richtige Steuerung dieser Faktoren, wie die Aufrechterhaltung eines hohen Vakuums und die Erwärmung des Substrats, kann dazu beitragen, eine gleichmäßigere und qualitativ hochwertigere Dünnschicht zu erhalten. Die Dicke kann je nach den spezifischen Bedingungen und Parametern des Verdampfungsprozesses stark schwanken.
Die wichtigsten Punkte werden erklärt:
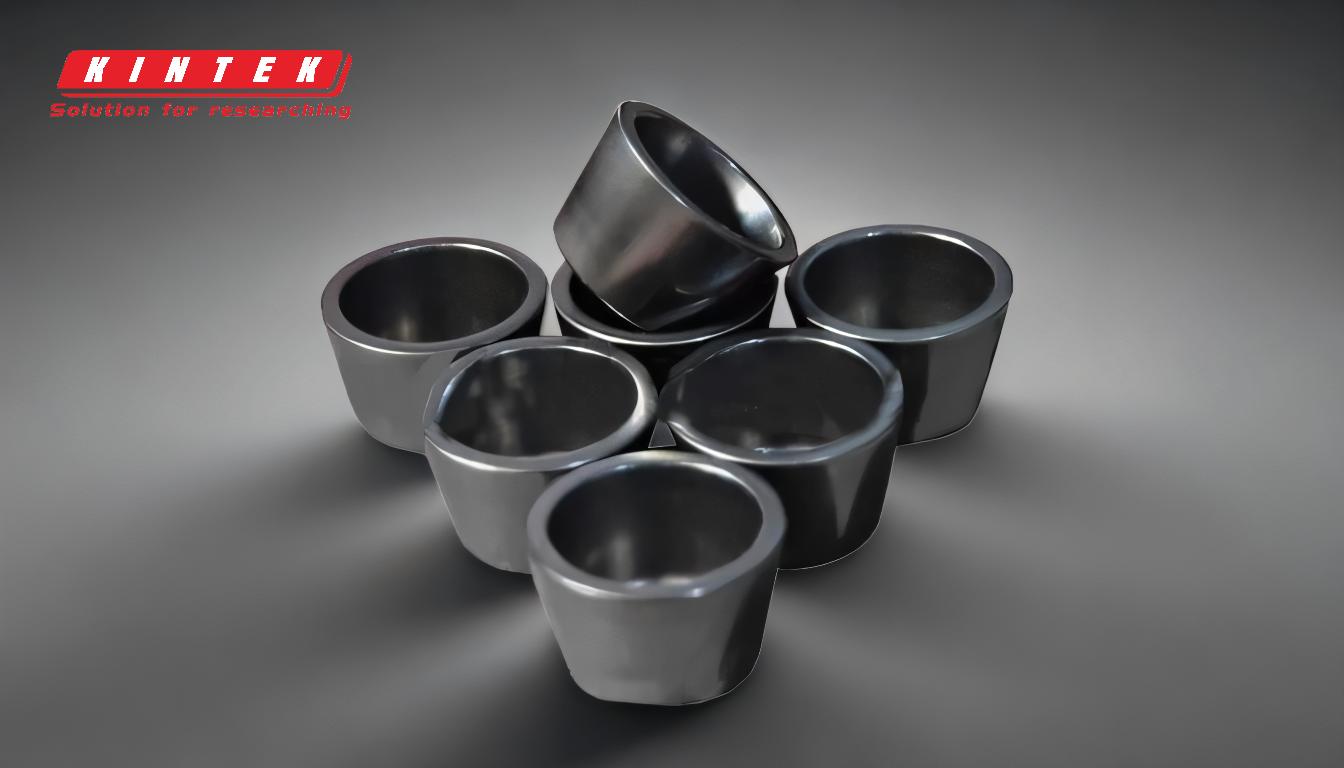
-
Einfluss der Geometrie der Verdunstungskammer:
- Die Geometrie der Verdampfungskammer spielt eine wichtige Rolle bei der Bestimmung der Schichtdicke. Aufgrund der unterschiedlichen Abstände und Winkel zwischen dem Ausgangsmaterial und verschiedenen Teilen des Substrats kann es zu einer ungleichmäßigen Abscheidung kommen. Dies kann zu dickeren Schichten in einigen Bereichen und dünneren Schichten in anderen führen.
-
Auswirkungen des Drucks in der Vakuumkammer:
- Der Druck in der Vakuumkammer beeinflusst den freien Weg der Moleküle des Ausgangsmaterials. Ein höherer Vakuumgrad verringert die Anzahl der Zusammenstöße mit Restgasen, die andernfalls zu einer ungleichmäßigen Schichtdicke führen können. Ein geringerer Druck minimiert auch den Einschluss von Verunreinigungen, was zu einem reineren und gleichmäßigeren Film führt.
-
Die Rolle der Substrattemperatur:
- Die Temperatur des Substrats ist entscheidend für die Bildung einer gleichmäßigen Schicht. Die Erwärmung des Substrats sorgt dafür, dass die verdampften Atome genügend Energie haben, um sich frei zu bewegen und eine gleichmäßigere Schicht zu bilden. Substrattemperaturen über 150 °C können die Haftung zwischen dem Film und dem Substrat verbessern, was zu einer besseren Qualität und Gleichmäßigkeit des Films beiträgt.
-
Einfluss von Ausgangsmaterial und Verdunstungsrate:
- Auch das Molekulargewicht und die Verdampfungsrate des Ausgangsmaterials beeinflussen die Schichtdicke. Verschiedene Materialien haben unterschiedliche Abscheidungsraten, und die Verdampfungsrate muss sorgfältig gesteuert werden, um die gewünschte Dicke zu erreichen. Höhere Abscheidungsraten bei einem bestimmten Vakuumdruck können die Reinheit der Schicht verbessern, indem sie den Einschluss gasförmiger Verunreinigungen minimieren.
-
Die Bedeutung der Oberflächenvorbereitung des Substrats:
- Die Vorbereitung der Substratoberfläche ist für das Erreichen einer gleichmäßigen Schichtdicke von wesentlicher Bedeutung. Eine raue oder unebene Substratoberfläche kann zu einer ungleichmäßigen Abscheidung führen, während eine glatte und ordnungsgemäß vorbereitete Oberfläche eine gleichmäßige Schichtbildung fördert.
-
Variabilität aufgrund von Prozessparametern:
- Die Schichtdicke kann in Abhängigkeit von bestimmten Prozessparametern wie der Dauer des Verdampfungsprozesses, der dem Elektronenstrahl zugeführten Leistung und der Masse des Ausgangsmaterials erheblich variieren. Diese Parameter müssen sorgfältig kontrolliert werden, um die gewünschte Schichtdicke und Qualität zu erreichen.
Wenn man diese Faktoren versteht und kontrolliert, ist es möglich, durch Elektronenstrahlverdampfung eine gleichmäßigere und hochwertigere Dünnschicht zu erzielen. Die Dicke der Schicht kann sehr unterschiedlich sein, aber mit einer angemessenen Prozesssteuerung kann sie auf die spezifischen Anforderungen zugeschnitten werden.
Zusammenfassende Tabelle:
Faktor | Auswirkungen auf die Filmdicke |
---|---|
Geometrie der Verdunstungskammer | Ungleichmäßige Ablagerung aufgrund unterschiedlicher Abstände und Winkel zwischen Quelle und Substrat. |
Vakuumkammer Druck | Ein höheres Vakuum reduziert Kollisionen mit Restgasen und verbessert die Gleichmäßigkeit und Reinheit des Films. |
Temperatur des Substrats | Das Erhitzen auf über 150 °C verbessert die Beweglichkeit der Atome, die Haftung und die Gleichmäßigkeit des Films. |
Ausgangsmaterial & Verdunstungsrate | Das Molekulargewicht und die Verdampfungsrate beeinflussen die Abscheidungsrate und die Reinheit des Films. |
Vorbereitung der Oberfläche des Substrats | Glatte Oberflächen begünstigen eine gleichmäßige Ablagerung; raue Oberflächen verursachen Ungleichmäßigkeiten. |
Prozess-Parameter | Dauer, Leistung und Masse des Ausgangsmaterials müssen auf die gewünschte Dicke abgestimmt werden. |
Benötigen Sie Hilfe bei der Optimierung Ihres E-Beam-Verdampfungsprozesses? Kontaktieren Sie unsere Experten noch heute für maßgeschneiderte Lösungen!