Selektives Lasersintern (SLS) ist eine leistungsstarke additive Fertigungstechnologie, die einzigartige Vor- und Nachteile bietet. Es eignet sich hervorragend für die Herstellung komplexer, funktionaler Formen, die mit herkömmlichen Sinterverfahren nur schwer zu erreichen sind. Es ist jedoch mit hohen Kosten verbunden, einschließlich teurer Maschinen und Materialien, und erfordert qualifiziertes Personal. Im Gegensatz dazu ist die Pulvermetallurgie für die Massenproduktion mittelkomplexer Formen kostengünstiger, kann aber aufgrund der Reibung zwischen Pulver und Werkzeug zu ungleichmäßigen Komponenten führen. Im Folgenden werden die wichtigsten Vor- und Nachteile des SLS-Verfahrens im Detail erläutert.
Die wichtigsten Punkte werden erklärt:
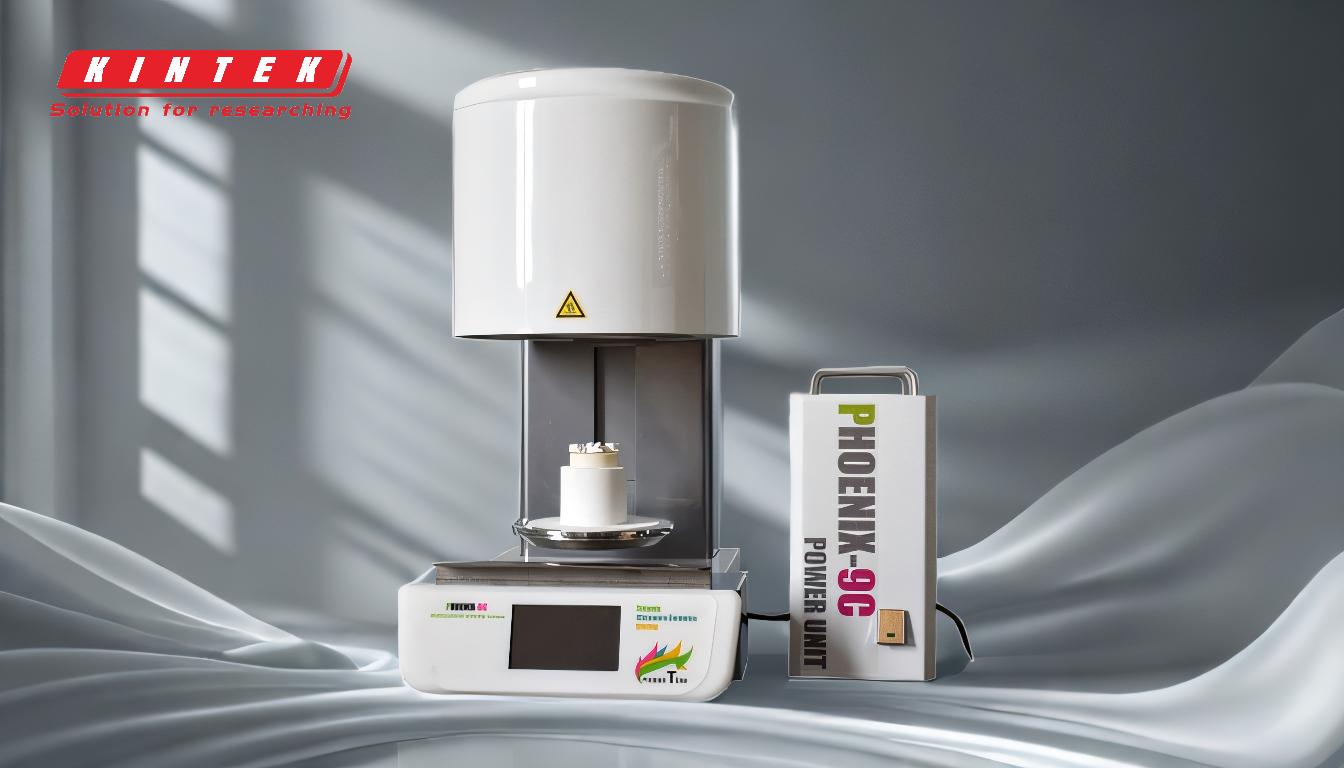
-
Vorteile des Selektiven Laser-Sinterns (SLS):
-
Komplexe und funktionelle Formen:
- SLS ermöglicht die Herstellung hochkomplexer und funktionaler Geometrien, die mit herkömmlichen Sinter- oder Bearbeitungsmethoden nur schwer oder gar nicht zu erreichen sind. Dies ist besonders nützlich für Branchen, die komplizierte Designs benötigen, wie die Luft- und Raumfahrt, die Medizintechnik und die Automobilindustrie.
-
Vielseitigkeit der Materialien:
- SLS kann mit einer Vielzahl von Materialien arbeiten, darunter Polymere, Metalle und Keramiken, und ermöglicht die Herstellung von Teilen mit unterschiedlichen mechanischen und thermischen Eigenschaften.
-
Keine Stützkonstruktionen erforderlich:
- Im Gegensatz zu einigen anderen additiven Fertigungsverfahren sind beim SLS-Verfahren keine Stützstrukturen während des Bauprozesses erforderlich, da das ungesinterte Pulver als natürlicher Träger fungiert. Dies reduziert die Nachbearbeitungszeit und den Materialabfall.
-
Hohe Präzision und Reproduzierbarkeit:
- SLS bietet eine hohe Präzision und Wiederholbarkeit und eignet sich daher für die Herstellung von Teilen mit engen Toleranzen und gleichbleibender Qualität.
-
Komplexe und funktionelle Formen:
-
Nachteile des Selektiven Laser-Sinterns (SLS):
-
Hohe Anschaffungs- und Betriebskosten:
- SLS-Maschinen sind teuer und kosten oft mehr als 250.000 Dollar, was sie für kleine Unternehmen oder Neugründungen unerschwinglich macht. Außerdem sind die bei SLS verwendeten Materialien teuer, was die Gesamtkosten weiter erhöht.
-
Erforderliche Fachkräfte:
- Die Bedienung einer SLS-Maschine erfordert spezielle Kenntnisse und Schulungen, was für Unternehmen, die nicht über qualifiziertes Personal verfügen, ein Hindernis darstellen kann.
-
Nachbearbeitungsanforderungen:
- Durch SLS hergestellte Teile müssen häufig nachbearbeitet werden, z. B. durch Reinigung, Wärmebehandlung oder Oberflächenveredelung, um die gewünschten Eigenschaften und das gewünschte Aussehen zu erhalten.
-
Begrenzte Baugröße:
- Die Baukammer von SLS-Maschinen hat Größenbeschränkungen, wodurch die maximalen Abmessungen der Teile, die in einem einzigen Druck hergestellt werden können, begrenzt sind.
-
Hohe Anschaffungs- und Betriebskosten:
-
Vergleich mit Pulvermetallurgie:
-
Kosteneffizienz für die Großserienproduktion:
- Die Pulvermetallurgie ist für die Großproduktion mittelkomplexer Formen kostengünstiger, da sie im Vergleich zum SLS-Verfahren geringere Maschinen- und Materialkosten verursacht.
-
Keine qualifizierten Bediener erforderlich:
- Pulvermetallurgische Verfahren sind im Allgemeinen einfacher zu bedienen und erfordern keine hochqualifizierten Bediener, was die Arbeitskosten senkt.
-
Ungleichmäßigkeitsprobleme:
- Ein potenzieller Nachteil der Pulvermetallurgie ist das Risiko ungleichmäßiger Komponenten aufgrund der Reibung zwischen dem Pulver und dem Werkzeug, was die mechanischen Eigenschaften des Endprodukts beeinträchtigen kann.
-
Kosteneffizienz für die Großserienproduktion:
-
Anwendungen und Eignung:
-
SLS für das Prototyping und die Kleinserienfertigung:
- SLS ist ideal für das Prototyping und die Kleinserienfertigung komplexer Teile, bei denen die Flexibilität des Designs und die Materialeigenschaften entscheidend sind.
-
Pulvermetallurgie für die Massenproduktion:
- Die Pulvermetallurgie eignet sich besser für die Massenproduktion einfacherer Formen, bei denen Kosteneffizienz und Produktionsgeschwindigkeit Vorrang vor der Komplexität des Designs haben.
-
SLS für das Prototyping und die Kleinserienfertigung:
Zusammenfassend lässt sich sagen, dass SLS erhebliche Vorteile in Bezug auf Designflexibilität und Materialvielfalt bietet, jedoch mit hohen Kosten und betrieblichen Herausforderungen verbunden ist. Die Pulvermetallurgie hingegen ist für die Großserienproduktion wirtschaftlicher, kann aber Abstriche bei der Designkomplexität und Einheitlichkeit machen. Die Wahl zwischen diesen Technologien hängt von den spezifischen Anforderungen des Projekts ab, einschließlich Budget, Produktionsvolumen und Komplexität der Teile.
Zusammenfassende Tabelle:
Aspekt | Selektives Laser-Sintern (SLS) | Pulvermetallurgie |
---|---|---|
Design-Komplexität | Hoch - Ideal für komplexe, funktionelle Formen | Mittel - Geeignet für einfachere Formen |
Vielseitigkeit der Materialien | Hoch - Geeignet für Polymere, Metalle und Keramik | Begrenzt - Hauptsächlich Metalle |
Kosten | Hoch - Teure Maschinen und Materialien | Gering - Kostengünstig für Großserienproduktion |
Erforderliche Fähigkeiten des Bedieners | Hoch - Erfordert eine spezielle Ausbildung | Gering - Einfacher zu bedienen |
Nachbearbeitung | Erforderlich - Reinigung, Wärmebehandlung, Oberflächenbehandlung | Minimal - Weniger Nachbearbeitung erforderlich |
Baugröße | Begrenzt - Begrenzt durch die Größe der Maschinenkammer | Flexibel - größere Teile realisierbar |
Gleichmäßigkeit | Hoch - Gleichbleibende Qualität | Gering - Risiko von ungleichmäßigen Komponenten |
Anwendungen | Prototyping, Kleinserienproduktion von komplexen Teilen | Massenproduktion von einfacheren Formen |
Benötigen Sie Hilfe bei der Entscheidung zwischen SLS und Pulvermetallurgie? Kontaktieren Sie noch heute unsere Experten für eine maßgeschneiderte Beratung!