Die chemische Gasphasenabscheidung (CVD) ist eine weit verbreitete Methode zur Herstellung hochwertiger dünner Filme und Beschichtungen. Es bietet zahlreiche Vorteile, wie z. B. hohe Vielseitigkeit, präzise Kontrolle der Materialeigenschaften und die Möglichkeit, ultradünne Schichten auf verschiedenen Substraten abzuscheiden. Es weist jedoch auch einige Nachteile auf, darunter hohe Betriebstemperaturen, Einschränkungen bei der Beschichtung großer Oberflächen und die Notwendigkeit spezieller Ausrüstung. Im Folgenden gehen wir detailliert auf die wichtigsten Vor- und Nachteile der CVD-Methode ein.
Wichtige Punkte erklärt:
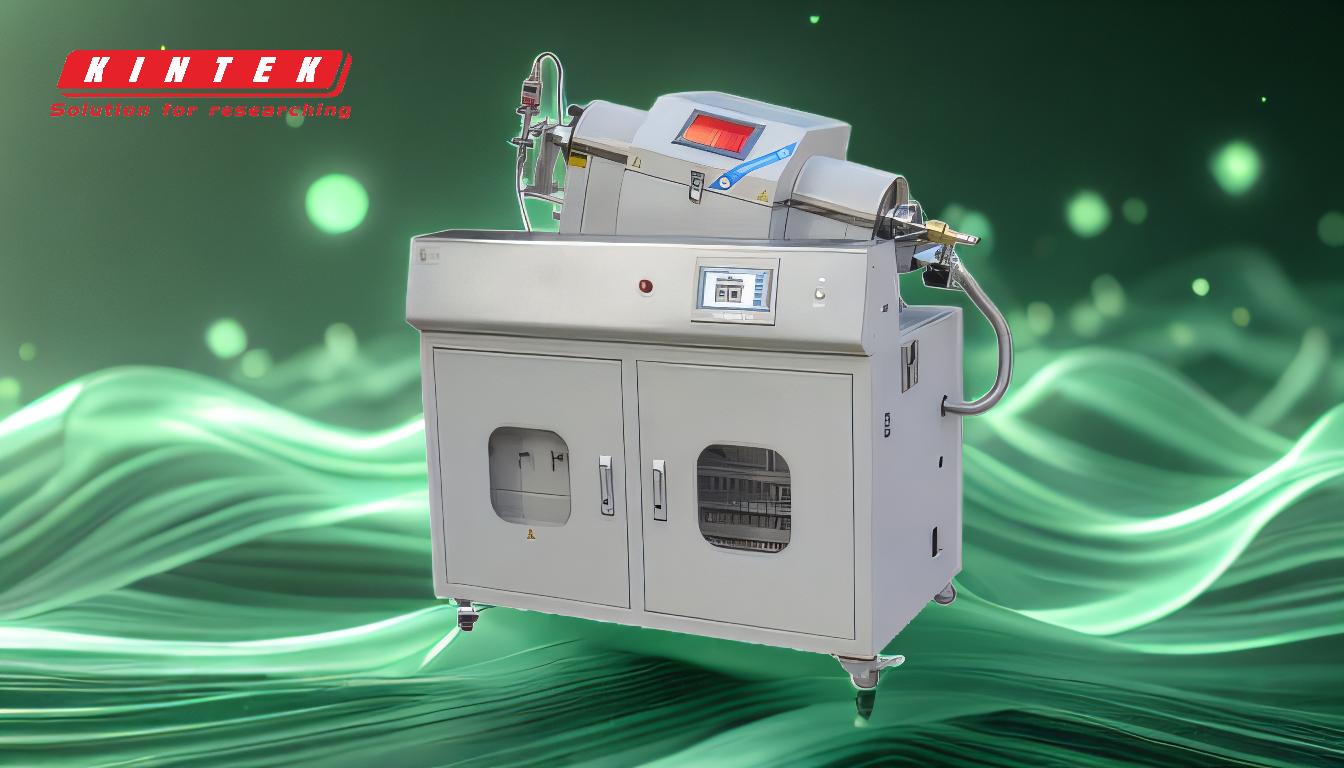
-
Vorteile der chemischen Gasphasenabscheidung:
-
Hohe Vielseitigkeit und Materialkompatibilität:
- CVD kann zur Abscheidung einer breiten Palette von Materialien verwendet werden, darunter Keramik, Metalle und Glas. Dadurch eignet es sich für vielfältige Anwendungen, von der Elektronik bis zur Luft- und Raumfahrt.
- Das Verfahren ermöglicht die Synthese sowohl reiner als auch komplexer Materialien und ermöglicht so maßgeschneiderte Eigenschaften wie Korrosionsbeständigkeit, Abriebfestigkeit oder hohe Reinheit.
-
Präzision und Kontrolle:
- CVD bietet vollständige Kontrolle über Abscheidungsparameter wie Temperatur, Druck, Gasdurchflussrate und Gaskonzentration. Dies ermöglicht eine präzise Einstellung der chemischen und physikalischen Eigenschaften der abgeschiedenen Filme.
- Es ist ideal für die Herstellung ultradünner Schichten, die für Anwendungen wie elektrische Schaltkreise und die Halbleiterfertigung unerlässlich sind.
-
Hochwertige Beschichtungen:
- Die durch CVD erzeugten Filme sind typischerweise hochrein, dicht und gleichmäßig, mit geringer Restspannung und guter Kristallinität.
- Das Verfahren bietet hervorragende Wrap-Around-Eigenschaften und eignet sich daher für die Beschichtung komplexer und präziser Oberflächen.
-
Haltbarkeit und Leistung:
- CVD-Beschichtungen sind äußerst langlebig und halten Umgebungen mit hoher Beanspruchung, extremen Temperaturen und Temperaturschwankungen stand.
- Im Vergleich zu anderen Abscheidungsmethoden bietet CVD glattere Oberflächen, eine bessere Dickenkontrolle sowie eine verbesserte elektrische und thermische Leitfähigkeit.
-
Vorteile für die Umwelt:
- CVD führt im Vergleich zu alternativen Technologien wie der Pechbeschichtung häufig zu einem geringeren CO2-Fußabdruck.
-
Hohe Vielseitigkeit und Materialkompatibilität:
-
Nachteile der chemischen Gasphasenabscheidung:
-
Hohe Betriebstemperaturen:
- CVD erfordert typischerweise hohe Temperaturen, was für temperaturempfindliche Materialien oder Substrate problematisch sein kann.
-
Einschränkungen bei der Beschichtung großer Flächen:
- Die Größe der beim CVD verwendeten Vakuumkammer ist begrenzt, was die Beschichtung großer oder sperriger Bauteile zu einer Herausforderung macht.
-
Komplexe Setup- und Prozessanforderungen:
- CVD kann nicht vor Ort durchgeführt werden und erfordert oft spezielle Beschichtungszentren. Dies bringt logistische Herausforderungen und Kosten mit sich.
- Für die Beschichtung müssen alle Teile in einzelne Komponenten zerlegt werden, was zeit- und arbeitsintensiv sein kann.
-
Alles-oder-Nichts-Prozess:
- CVD ist für partielle Beschichtungen schwierig anzuwenden. Das Verfahren beschichtet entweder die gesamte Oberfläche oder gar nichts, was die Flexibilität bei bestimmten Anwendungen einschränkt.
-
Ausrüstungs- und Wartungskosten:
- Obwohl die Geräte relativ einfach zu bedienen sind, können Anschaffung und Wartung teuer sein, insbesondere bei Hochtemperatur- und Vakuumsystemen.
-
Hohe Betriebstemperaturen:
Zusammenfassend ist die chemische Gasphasenabscheidung eine äußerst vielseitige und präzise Methode zur Herstellung hochwertiger Beschichtungen und dünner Filme. Seine Fähigkeit, ein breites Spektrum an Materialien abzuscheiden und die Filmeigenschaften zu steuern, macht es in Branchen wie Elektronik, Luft- und Raumfahrt und Fertigung von unschätzbarem Wert. Allerdings sind die hohen Betriebstemperaturen, die Einschränkungen bei der Beschichtung großer Flächen und die logistischen Herausforderungen bemerkenswerte Nachteile. Das Verständnis dieser Vor- und Nachteile ist entscheidend für die Auswahl der richtigen Abscheidungsmethode für bestimmte Anwendungen. Weitere Einzelheiten finden Sie hier chemische Gasphasenabscheidung .
Übersichtstabelle:
Aspekt | Vorteile | Nachteile |
---|---|---|
Vielseitigkeit | Lagert Keramik, Metalle, Glas ab; geeignet für Elektronik, Luft- und Raumfahrt usw. | Hohe Betriebstemperaturen können die Verwendung mit temperaturempfindlichen Materialien einschränken. |
Präzision und Kontrolle | Volle Kontrolle über die Abscheidungsparameter; Ideal für ultradünne Schichten. | Aufgrund der Kammergröße auf die Beschichtung kleiner oder mittelgroßer Bauteile beschränkt. |
Beschichtungsqualität | Hochreine, dichte, gleichmäßige Folien mit hervorragenden Wickeleigenschaften. | Erfordert spezielle Ausrüstung und kann nicht vor Ort durchgeführt werden. |
Haltbarkeit | Hält hohen Belastungen, extremen Temperaturen und Temperaturschwankungen stand. | Alles-oder-Nichts-Prozess; Teilbeschichtungen sind nicht möglich. |
Umweltauswirkungen | Reduzierter CO2-Fußabdruck im Vergleich zu Alternativen wie Pechbeschichtung. | Hohe Ausrüstungs- und Wartungskosten. |
Benötigen Sie Hilfe bei der Auswahl der richtigen Abscheidungsmethode für Ihr Projekt? Kontaktieren Sie noch heute unsere Experten für eine individuelle Beratung!