Das pulvermetallurgische Sintern ist ein hocheffizientes und vielseitiges Herstellungsverfahren, das zahlreiche Vorteile bietet und daher bevorzugt für die Herstellung komplexer und leistungsfähiger Bauteile eingesetzt wird.Zu den wichtigsten Vorteilen gehören Energieeffizienz, Kosteneffizienz und die Fähigkeit, Teile mit außergewöhnlicher Präzision und Gleichmäßigkeit herzustellen.Das Verfahren ist umweltfreundlich, verursacht nur minimalen Materialabfall und eignet sich besonders für Materialien mit hohem Schmelzpunkt oder schlechter Gießbarkeit.Darüber hinaus verbessert das Sintern die Materialeigenschaften, z. B. Festigkeit und Haltbarkeit, und ermöglicht die Herstellung komplizierter Formen und Strukturen, die auf spezifische Anforderungen zugeschnitten sind.
Die wichtigsten Punkte erklärt:
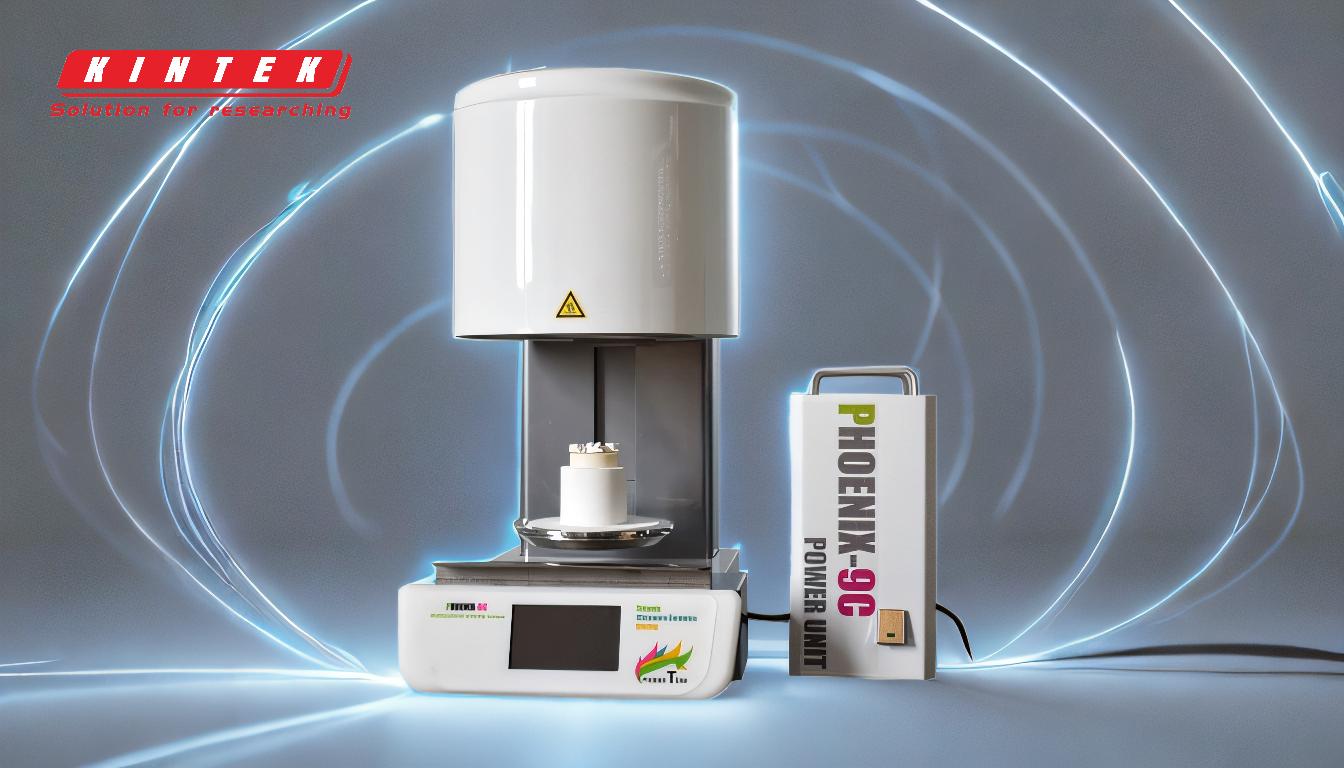
-
Energie-Effizienz und niedrige Prozesstemperatur:
- Das pulvermetallurgische Sintern arbeitet im Vergleich zu herkömmlichen Schmelzverfahren mit niedrigeren Temperaturen, was den Energieverbrauch senkt.Dies macht es zu einer umweltfreundlichen Option, insbesondere für Materialien mit hohem Schmelzpunkt.
- Die niedrigere Prozesstemperatur minimiert auch die thermische Belastung und den Verzug des Endprodukts und gewährleistet eine bessere Maßgenauigkeit.
-
Hohe Sinterkompaktheit und Materialausnutzung:
- Das Sintern führt zu hochdichten Teilen mit minimaler Porosität, die die mechanischen Eigenschaften des Endprodukts, wie Festigkeit und Haltbarkeit, verbessern.
- Das Verfahren ist hocheffizient, da bis zu 97 % des verwendeten Materials in das Endprodukt eingehen, wodurch Abfall und Materialkosten erheblich reduziert werden.
-
Kurze Sinterzeit und Prozesseffizienz:
- Der Sinterprozess ist relativ schnell und ermöglicht im Vergleich zu herkömmlichen Fertigungsmethoden schnellere Produktionszyklen.
- Diese kurze Verarbeitungszeit in Verbindung mit der Möglichkeit, endkonturnahe Teile herzustellen, verringert den Bedarf an zusätzlicher Bearbeitung und spart so Zeit und Ressourcen.
-
Fähigkeit zur Herstellung komplexer und komplizierter Formen:
- Das pulvermetallurgische Sintern ermöglicht die Herstellung von hochkomplexen Außen- und Innengeometrien mit außergewöhnlicher Präzision.Erreicht wird dies durch den Einsatz von Formen und Gesenken, die durch Drahterodieren (Electrical Discharge Machining) mit Toleranzen im Zentimeterbereich hergestellt werden.
- Diese Fähigkeit ist besonders wertvoll in Branchen wie der Automobilindustrie und der Luft- und Raumfahrt, wo komplizierte und leichte Komponenten unerlässlich sind.
-
Maßgeschneiderte Materialeigenschaften und Vielseitigkeit:
- Das Verfahren ermöglicht eine präzise Steuerung der Materialzusammensetzung und -struktur und damit die Herstellung von Teilen mit maßgeschneiderten Eigenschaften, die den spezifischen Anforderungen der Anwendung entsprechen.
- Es ist besonders vorteilhaft für Werkstoffe mit großen Unterschieden im Schmelzpunkt oder schlechter Gießbarkeit, da es die mit herkömmlichen Schmelz- und Gießverfahren verbundenen Herausforderungen vermeidet.
-
Kosteneffizienz und wirtschaftlicher Nutzen:
- Das pulvermetallurgische Sintern reduziert den Materialabfall und macht eine umfangreiche Bearbeitung überflüssig, was die Produktionskosten insgesamt senkt.
- Die Fähigkeit, Teile mit hoher Präzision und Konsistenz herzustellen, verringert die Wahrscheinlichkeit von Defekten, was die Kosteneinsparungen und die Produktzuverlässigkeit weiter erhöht.
-
Umweltfreundlichkeit:
- Das Verfahren erzeugt nur minimale Abfälle und benötigt weniger Energie als herkömmliche Herstellungsverfahren, was es zu einer nachhaltigen Wahl für die moderne Fertigung macht.
- Sein umweltfreundlicher Charakter entspricht der wachsenden Nachfrage nach umweltfreundlichen Fertigungstechnologien.
-
Verbesserte Festigkeit und Langlebigkeit:
- Durch das Sintern wird die Oberflächenporosität minimiert, was zu Teilen mit verbesserten mechanischen Eigenschaften führt, wie z. B. höhere Festigkeit und Verschleißfestigkeit.
- Dadurch eignen sich gesinterte Bauteile für anspruchsvolle Anwendungen, bei denen Haltbarkeit und Leistung entscheidend sind.
-
Breite Palette von Anwendungen:
- Das pulvermetallurgische Sintern ist in Branchen wie der Automobilindustrie, der Luft- und Raumfahrt, der Elektronik und der Medizintechnik weit verbreitet, da sich damit hochwertige Präzisionskomponenten herstellen lassen.
- Seine Vielseitigkeit und Anpassungsfähigkeit machen es zu einer Schlüsseltechnologie für die moderne Fertigung.
Zusammenfassend lässt sich sagen, dass das pulvermetallurgische Sintern eine Kombination aus technischen, wirtschaftlichen und ökologischen Vorteilen bietet, die es zu einem äußerst effektiven und nachhaltigen Fertigungsverfahren machen.Seine Fähigkeit, komplexe, leistungsstarke Teile mit minimalem Abfall und Energieverbrauch herzustellen, macht es zu einem Eckpfeiler fortschrittlicher Fertigungstechnologien.
Zusammenfassende Tabelle:
Vorteil | Beschreibung |
---|---|
Energie-Effizienz | Der Betrieb erfolgt bei niedrigeren Temperaturen, was den Energieverbrauch und die thermische Belastung reduziert. |
Hohe Sinterkompaktheit | Erzeugt Teile mit hoher Dichte, minimaler Porosität und hoher Festigkeit. |
Kurze Sinterzeit | Schnellere Produktionszyklen und geringerer Bedarf an zusätzlicher Bearbeitung. |
Komplexe Formen | Ermöglicht komplizierte Geometrien mit außergewöhnlicher Präzision. |
Maßgeschneiderte Materialeigenschaften | Maßgeschneiderte Materialzusammensetzung für spezifische Anwendungsanforderungen. |
Kosteneffizienz | Reduziert den Materialabfall und die Bearbeitungskosten. |
Umweltfreundlichkeit | Minimaler Abfall und Energieverbrauch im Einklang mit umweltfreundlicher Produktion. |
Verbesserte Festigkeit und Langlebigkeit | Verbessert die mechanischen Eigenschaften wie die Verschleißfestigkeit. |
Breite Palette von Anwendungen | Einsatz in der Automobil-, Luft- und Raumfahrt-, Elektronik- und Medizinindustrie. |
Nutzen Sie das Potenzial des pulvermetallurgischen Sinterns für Ihre Fertigungsanforderungen. Kontaktieren Sie unsere Experten noch heute !