Das Funkenplasmasintern (SPS) ist eine fortschrittliche Sintertechnik, die zahlreiche Vorteile gegenüber herkömmlichen Sinterverfahren bietet.Besonders geschätzt wird es für seine Fähigkeit, in kurzer Zeit hochwertige, dichte Werkstoffe mit feinen Mikrostrukturen herzustellen.Das Verfahren nutzt die schnelle Erwärmung, die gleichmäßige Temperaturverteilung und das kontrollierte Kornwachstum, um Materialien mit hervorragenden mechanischen, elektrischen und thermischen Eigenschaften zu erhalten.SPS ist außerdem energie- und kosteneffizient und eignet sich daher für eine Vielzahl von Anwendungen, darunter Hochleistungskeramik, Metalle und Verbundwerkstoffe.Im Folgenden werden die wichtigsten Vorteile von SPS im Detail erläutert.
Die wichtigsten Punkte werden erklärt:
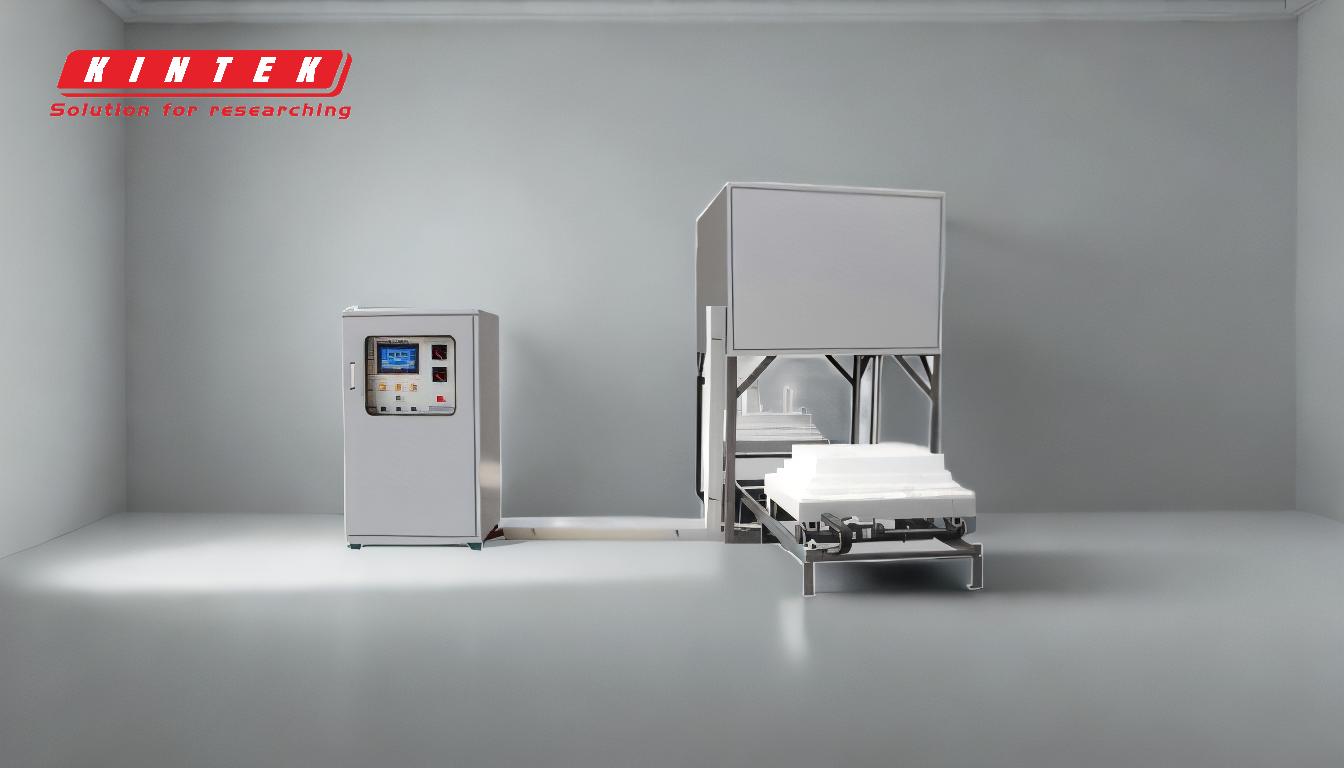
-
Schnelle Aufheizgeschwindigkeit und kurze Sinterzeit
- SPS nutzt Gleichstromimpulse, um eine schnelle Erwärmung zu erzeugen, wodurch die Sinterzeit im Vergleich zu herkömmlichen Verfahren erheblich verkürzt wird.Diese schnelle Erwärmung minimiert das Kornwachstum, was zu einem feinen und gleichmäßigen Gefüge führt.
- Die kurze Sinterzeit steigert auch die Produktionseffizienz und macht SPS ideal für industrielle Anwendungen, bei denen Zeit ein kritischer Faktor ist.
-
Niedrige Sintertemperatur
- SPS arbeitet im Vergleich zu herkömmlichen Sintertechniken mit niedrigeren Temperaturen.Dies ist auf die kombinierten Effekte der Joule-Erwärmung und der Plasmaerzeugung zurückzuführen, die die Verdichtung verbessern, ohne übermäßig hohe Temperaturen zu erfordern.
- Niedrigere Sintertemperaturen verringern den Energieverbrauch und verhindern thermische Schäden an empfindlichen Materialien wie nanostrukturierten Keramiken oder Verbundwerkstoffen.
-
Gleichmäßige Erwärmung und hohe Dichte
- Das SPS-Verfahren gewährleistet eine gleichmäßige Erwärmung der gesamten Probe, wodurch Temperaturgradienten, die zu Defekten oder ungleichmäßiger Verdichtung führen können, vermieden werden.
- Diese Gleichmäßigkeit in Verbindung mit der Anwendung von Druck führt zu Materialien mit hoher Dichte und minimaler Porosität, die für das Erreichen hervorragender mechanischer und funktioneller Eigenschaften entscheidend sind.
-
Hemmung des Kornwachstums
- Eines der herausragenden Merkmale von SPS ist seine Fähigkeit, übermäßiges Kornwachstum während des Sinterns zu verhindern.Dies wird durch die schnellen Erwärmungs- und Abkühlungszyklen erreicht, die die für die Kornvergröberung verfügbare Zeit begrenzen.
- Durch die Beibehaltung feiner Korngrößen werden die mechanische Festigkeit, die Härte und die Verschleißfestigkeit des Sintermaterials verbessert.
-
Energieeffizienz und Kosteneffizienz
- Die schnellen Verarbeitungszeiten und niedrigeren Sintertemperaturen von SPS führen zu erheblichen Energieeinsparungen.Dies macht das Verfahren umweltfreundlicher und kosteneffizienter, insbesondere für die Großserienproduktion.
- Außerdem werden durch die Möglichkeit, endkonturnahe Komponenten herzustellen, der Materialabfall und die Nachbearbeitungsanforderungen reduziert, was die Kosten weiter senkt.
-
Vielseitigkeit bei schwierigen Materialien
- SPS eignet sich besonders gut für das Sintern von Werkstoffen, die mit herkömmlichen Methoden nur schwer zu verarbeiten sind, wie z. B. hochschmelzende Metalle, Keramik und Verbundwerkstoffe.
- Mit dem Verfahren kann eine vollständige Verdichtung dieser Materialien erreicht werden, ohne dass ihre einzigartigen Eigenschaften beeinträchtigt werden. Dadurch eignet es sich für fortschrittliche Anwendungen wie Luft- und Raumfahrtkomponenten, biomedizinische Implantate und elektronische Geräte.
-
Verbesserte Materialeigenschaften
- SPS verbessert wichtige Materialeigenschaften, wie Festigkeit, elektrische Leitfähigkeit, Wärmeleitfähigkeit und Transparenz.So weisen beispielsweise piezoelektrische Keramiken, die mit SPS hergestellt werden, aufgrund der Beseitigung von Defekten und der gleichmäßigen Porenverteilung eine optimierte Leistung auf.
- Das Verfahren ermöglicht auch die Herstellung von Materialien mit maßgeschneiderter Porosität, was für Anwendungen wie Filter oder Katalysatoren von Vorteil ist.
-
Einfache Bedienung und hohe Reproduzierbarkeit
- SPS-Systeme sind relativ einfach zu bedienen und erfordern nur minimale technische Kenntnisse.Die Prozessparameter, wie z. B. Temperatur, Druck und Heizrate, können präzise gesteuert werden, was eine hohe Wiederholbarkeit und Konsistenz der Endprodukte gewährleistet.
- Diese Wiederholbarkeit ist entscheidend für Branchen, die hohe Präzision und Zuverlässigkeit verlangen, wie die Automobil- und Elektronikindustrie.
-
Produktion komplexer Geometrien
- SPS ermöglicht die Herstellung komplexer, nicht zerspanbarer Geometrien mit hoher Genauigkeit.Diese Fähigkeit ist besonders wertvoll für die Massenproduktion, wo herkömmliche Bearbeitungsverfahren zeitaufwändig und kostspielig wären.
- Die Möglichkeit, endkonturnahe Bauteile herzustellen, reduziert auch den Bedarf an zusätzlichen Nachbearbeitungsprozessen, was die Effizienz weiter erhöht.
Zusammenfassend lässt sich sagen, dass das Spark-Plasma-Sintern eine Kombination aus Geschwindigkeit, Präzision und Materialvielfalt bietet, die es zu einer hervorragenden Wahl für die moderne Fertigung und Forschung macht.Seine Fähigkeit, Hochleistungswerkstoffe mit feinen Mikrostrukturen und minimalen Defekten herzustellen, macht es zu einer Schlüsseltechnologie für den Fortschritt in der Materialwissenschaft und -technik.
Zusammenfassende Tabelle:
Vorteil | Hauptvorteil |
---|---|
Schnelles Aufheizen & kurzes Sintern | Reduziert die Sinterzeit, minimiert das Kornwachstum und steigert die Produktionseffizienz. |
Niedrige Sintertemperatur | Senkt den Energieverbrauch und verhindert thermische Schäden an empfindlichen Materialien. |
Gleichmäßige Erwärmung und hohe Dichte | Gewährleistet gleichmäßige Erwärmung, hohe Dichte und minimale Porosität für hervorragende Eigenschaften. |
Hemmung des Kornwachstums | Erhält feine Korngrößen und verbessert die Festigkeit, Härte und Verschleißfestigkeit. |
Energieeffizienz und Kosteneinsparungen | Spart Energie und senkt die Kosten, vor allem bei Großserien. |
Vielseitigkeit bei schwierigen Materialien | Wirksam bei hochschmelzenden Metallen, Keramiken und Verbundwerkstoffen. |
Verbesserte Materialeigenschaften | Verbessert die Festigkeit, Leitfähigkeit und Transparenz und ermöglicht gleichzeitig eine maßgeschneiderte Porosität. |
Einfache Bedienung und Reproduzierbarkeit | Einfache Bedienung mit präziser Steuerung für hohe Wiederholbarkeit und Konsistenz. |
Produktion komplexer Geometrien | Ermöglicht die Herstellung komplexer, nicht zerspanbarer Geometrien mit hoher Genauigkeit. |
Sind Sie bereit, Ihre Materialleistung mit Spark-Plasma-Sintern zu verbessern? Kontaktieren Sie uns noch heute um mehr zu erfahren!