Der Sinterprozess ist eine äußerst vorteilhafte Fertigungstechnik, die eine Vielzahl von Vorteilen bietet und daher in verschiedenen Branchen eine beliebte Wahl ist. Es ermöglicht die Herstellung von Bauteilen mit komplexen Formen und komplizierten Designs und verbessert gleichzeitig mechanische Eigenschaften wie Festigkeit, Leitfähigkeit und Korrosionsbeständigkeit. Sintern ist kostengünstig, vielseitig in der Materialauswahl und umweltfreundlich, da es den Materialabfall reduziert und häufig eine zusätzliche Bearbeitung überflüssig macht. Darüber hinaus ermöglicht es eine hohe Produktionseffizienz, hervorragende Oberflächengüten und eine präzise Toleranzkontrolle, sodass es sowohl für die Produktion kleiner als auch großer Stückzahlen geeignet ist. Insgesamt handelt es sich beim Sintern um einen vielseitigen und effizienten Prozess, der den Anforderungen moderner Fertigung gerecht wird.
Wichtige Punkte erklärt:
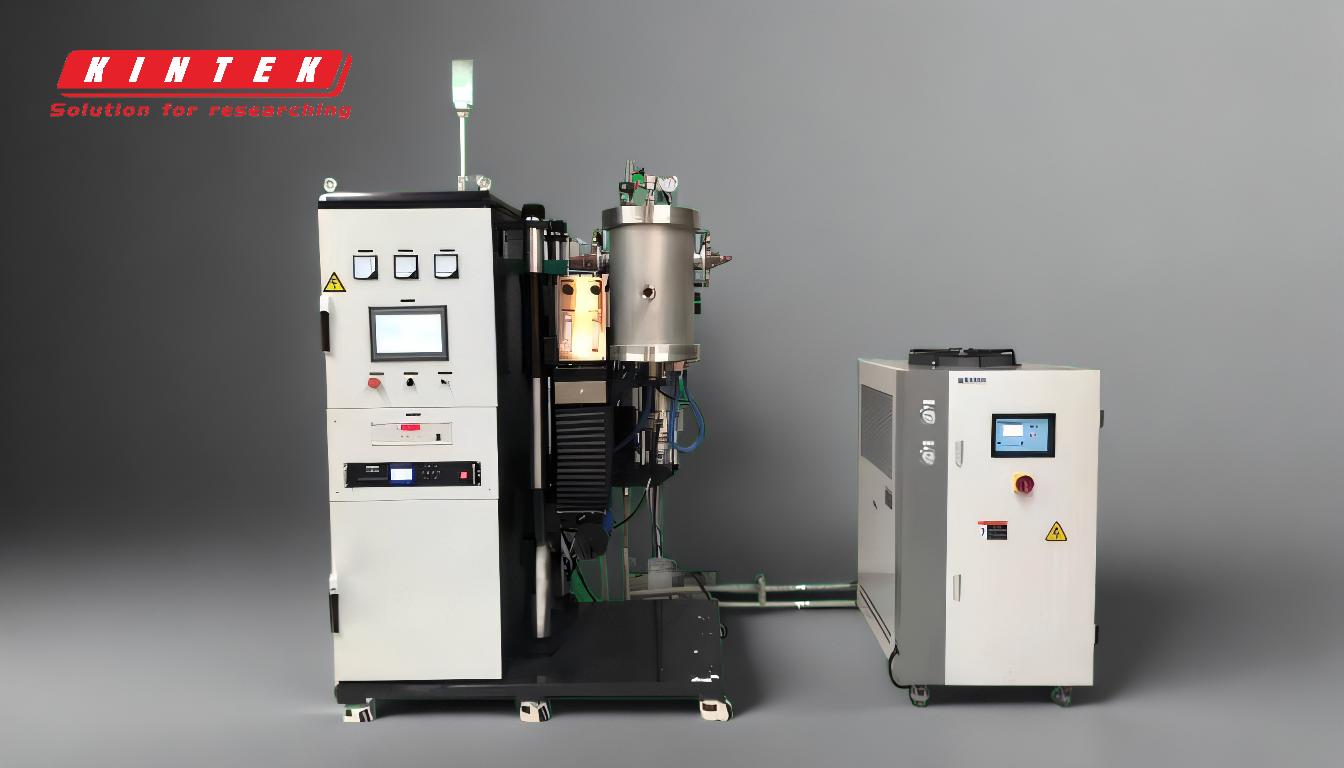
-
Fähigkeit zur Herstellung komplexer Formen und komplizierter Designs
- Durch Sintern können hochkomplexe Teile und Formen hergestellt werden, die mit herkömmlichen Fertigungsmethoden nur schwer oder gar nicht zu erreichen wären. Dies ist besonders nützlich in Branchen wie der Luft- und Raumfahrt, der Automobilindustrie und der Medizintechnik, in denen häufig komplizierte Designs erforderlich sind.
- Der Prozess reduziert den Bedarf an weiterer Bearbeitung, spart Zeit und Ressourcen und behält gleichzeitig die Präzision bei.
-
Verbesserte mechanische Eigenschaften
- Durch Sintern werden die mechanischen Eigenschaften von Materialien wie Zugfestigkeit, Härte und Verschleißfestigkeit verbessert. Dies wird durch eine Verringerung der Oberflächenporosität und die Schaffung dichterer, gleichmäßigerer Strukturen erreicht.
- Verbesserte Eigenschaften wie Leitfähigkeit, Korrosionsbeständigkeit und Wärmeleitfähigkeit machen Sinterteile für anspruchsvolle Anwendungen geeignet.
-
Maßgeschneiderte Materialkompositionen
- Der Sinterprozess ermöglicht die individuelle Anpassung der Materialzusammensetzungen und ermöglicht es Herstellern, Teile mit spezifischen Eigenschaften herzustellen, die auf ihre Anwendung zugeschnitten sind. Dazu gehört das Mischen verschiedener Pulver, um gewünschte Eigenschaften wie eine verbesserte Festigkeit oder Leitfähigkeit zu erzielen.
-
Kosteneffizienz
- Insbesondere für die Großserienfertigung ist das Sintern eine kostengünstige Fertigungsmethode. Es minimiert Materialverschwendung, da überschüssiges Pulver häufig wiederverwendet werden kann, und reduziert den Bedarf an zusätzlichen Nachbearbeitungsprozessen.
- Die Möglichkeit, Teile mit minimalem Bearbeitungsaufwand herzustellen, senkt die Produktionskosten weiter.
-
Vielseitigkeit bei der Materialauswahl
- Sintern kann bei einer Vielzahl von Materialien eingesetzt werden, darunter Metalle, Keramik und Verbundwerkstoffe. Diese Vielseitigkeit macht es für verschiedene Anwendungen in allen Branchen geeignet.
- Dies ist besonders vorteilhaft für Materialien, die durch Schmelzen und Gießen schwer zu verarbeiten sind, beispielsweise solche mit hohen Schmelzpunkten oder komplexen Zusammensetzungen.
-
Hohe Produktionseffizienz
- Der Sinterprozess ist äußerst effizient und ermöglicht eine schnelle Herstellung von Teilen mit gleichbleibender Qualität. Diese Effizienz ist sowohl bei Klein- als auch bei Großserien von Vorteil.
- Schnellere Inbetriebnahmen und weniger Prozessunterbrechungen tragen zu einer gesteigerten Produktivität bei.
-
Umweltfreundlich
- Sintern ist ein umweltfreundlicher Prozess, da dabei nur minimaler Abfall entsteht und häufig keine schädlichen Chemikalien oder Endbehandlungen erforderlich sind.
- Die Möglichkeit, überschüssiges Pulver zu recyceln, verringert die Umweltbelastung zusätzlich.
-
Hervorragende Oberflächengüte und Toleranzkontrolle
- Gesinterte Teile weisen oft eine hervorragende Oberflächengüte auf, wodurch zusätzliche Nachbearbeitungsprozesse weniger oder gar nicht erforderlich sind.
- Der Prozess ermöglicht eine präzise Kontrolle der Toleranzen und stellt sicher, dass die Teile strenge Maßanforderungen erfüllen.
-
Nicht bearbeitbare Geometrien für die Massenproduktion
- Sintern ermöglicht die Herstellung von Teilen mit nicht bearbeitbaren Geometrien und eignet sich daher ideal für die Massenproduktion komplexer Komponenten.
- Diese Fähigkeit ist besonders wertvoll in Branchen, in denen herkömmliche Bearbeitungsmethoden unpraktisch oder zu kostspielig sind.
Zusammenfassend bietet der Sinterprozess eine einzigartige Kombination von Vorteilen, einschließlich der Möglichkeit, komplexe Teile herzustellen, die Materialeigenschaften zu verbessern und eine kostengünstige Produktion in großen Stückzahlen zu erreichen. Seine Vielseitigkeit, Effizienz und Umweltvorteile machen es zur bevorzugten Wahl für Hersteller in verschiedenen Branchen.
Übersichtstabelle:
Vorteil | Hauptvorteile |
---|---|
Komplexe Formen und komplizierte Designs | Ermöglicht die Produktion schwer herzustellender Teile und reduziert den Bearbeitungsaufwand. |
Verbesserte mechanische Eigenschaften | Verbessert Festigkeit, Leitfähigkeit und Korrosionsbeständigkeit. |
Maßgeschneiderte Materialkompositionen | Passt Materialeigenschaften für bestimmte Anwendungen an. |
Kosteneffizienz | Reduziert Materialverschwendung und minimiert die Bearbeitungskosten. |
Vielseitigkeit bei der Materialauswahl | Funktioniert mit Metallen, Keramik und Verbundwerkstoffen für verschiedene Anwendungen. |
Hohe Produktionseffizienz | Gewährleistet eine schnelle und konsistente Produktion bei Klein- und Großserien. |
Umweltfreundlich | Minimiert Abfall und eliminiert schädliche Chemikalien. |
Hervorragende Oberflächenbeschaffenheit | Reduziert oder eliminiert die Notwendigkeit zusätzlicher Nachbearbeitungsprozesse. |
Präzise Toleranzkontrolle | Stellt sicher, dass Teile strenge Maßanforderungen erfüllen. |
Nicht bearbeitbare Geometrien | Ideal für die Massenproduktion komplexer Bauteile. |
Sind Sie bereit, den Sinterprozess für Ihre Fertigungsanforderungen zu nutzen? Kontaktieren Sie uns noch heute um mehr zu erfahren!