Das Sintern von Keramik bietet zahlreiche Vorteile, die es zu einem wichtigen Verfahren bei der Herstellung moderner Werkstoffe machen.Es verbessert die Materialeigenschaften wie Festigkeit, Haltbarkeit und Leitfähigkeit und ermöglicht die Herstellung komplexer Formen mit hoher Präzision.Bei diesem Verfahren werden keramische Pulver auf hohe Temperaturen erhitzt, was zu einer Verdichtung, geringerer Porosität und verbesserten mechanischen und thermischen Eigenschaften führt.Das Sintern ermöglicht auch die Herstellung maßgeschneiderter Materialzusammensetzungen, eine kostengünstige Produktion und die Verarbeitung anspruchsvoller Materialien.Diese Vorteile machen das Sintern unverzichtbar für Anwendungen, die Hochleistungskeramik erfordern, wie z. B. in der Luft- und Raumfahrt, in der Elektronik und in medizinischen Geräten.
Die wichtigsten Punkte werden erklärt:
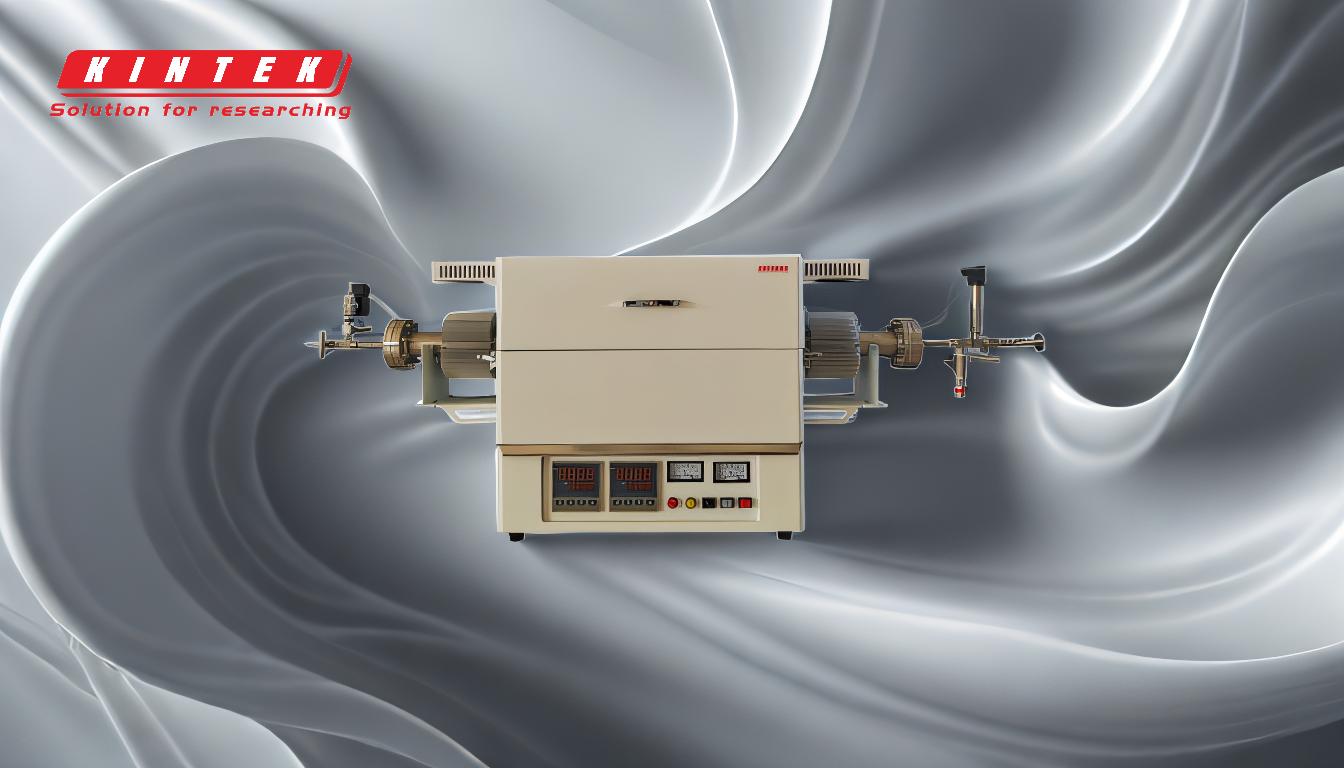
-
Verbesserte mechanische Eigenschaften:
- Das Sintern verbessert die Festigkeit, Zähigkeit und Härte von Keramik, indem es die Porosität verringert und Sinterhälse zwischen den Partikeln bildet.
- Das Ergebnis sind Werkstoffe mit hoher mechanischer Belastbarkeit, die sich für anspruchsvolle Anwendungen wie Turbinenschaufeln und Strukturbauteile eignen.
-
Verbesserte Materialgleichmäßigkeit und -reinheit:
- Das Verfahren gewährleistet ein hohes Maß an Reinheit und Gleichmäßigkeit der Ausgangsmaterialien, was zu konsistenten und wiederholbaren Vorgängen führt.
- Kontrollierte Korngröße und Mikrostruktur tragen zu stabilen Formen und hervorragenden Eigenschaften bei.
-
Herstellung komplexer Formen:
- Das Sintern ermöglicht die Herstellung von Bauteilen mit komplizierten Designs und nahezu netzförmigen Objekten, die mit herkömmlichen Fertigungsmethoden nur schwer zu erreichen sind.
- Diese Fähigkeit ist besonders nützlich für die Herstellung von Teilen mit präzisen Geometrien und komplizierten Details.
-
Maßgeschneiderte Materialzusammensetzungen:
- Das Verfahren ermöglicht die Diffusion von Elementen wie Nickel, Kupfer und Graphit, wodurch maßgeschneiderte Materialzusammensetzungen mit spezifischen Eigenschaften geschaffen werden können.
- Diese Vielseitigkeit ist von Vorteil für Anwendungen, die einzigartige Kombinationen von Zähigkeit, Abriebfestigkeit und anderen Eigenschaften erfordern.
-
Kosteneffizienz und Massenproduktion:
- Das Sintern reduziert den Bedarf an teuren Werkzeugen und ermöglicht eine schnelle Massenproduktion bei gleichbleibender Präzision und Wiederholbarkeit.
- Dies macht es zu einer kostengünstigen Lösung für die Herstellung von Hochleistungskeramik in großen Mengen.
-
Verbesserte thermische und elektrische Eigenschaften:
- Das Verfahren verbessert Eigenschaften wie die Wärmeleitfähigkeit und die elektrische Leitfähigkeit, so dass sich gesinterte Keramik für Anwendungen in der Elektronik und in Energiesystemen eignet.
- Es verbessert auch die Transparenz bestimmter keramischer Werkstoffe, was deren Einsatz in optischen Anwendungen erweitert.
-
Vielseitigkeit bei anspruchsvollen Materialien:
- Beim Sintern können Werkstoffe mit sehr hohem Schmelzpunkt verarbeitet werden, z. B. hochschmelzende Metalle und Hochleistungskeramiken.
- Dies macht es zu einer wertvollen Technik für die Verarbeitung von Materialien, die sonst nur schwer herzustellen sind.
-
Reduktion von Oberflächensauerstoff und Schmierstoffen:
- Der Sinterprozess beseitigt Schmiermittel in den verdichteten Pulvern und reduziert den Oberflächensauerstoff, was zu saubereren und haltbareren Bauteilen führt.
- Dies trägt zur allgemeinen Verbesserung der Eigenschaften des Teils bei.
-
Anwendungsspezifische Vorteile:
- In einigen Fällen wird das Sintern eingesetzt, um die Festigkeit zu erhöhen und gleichzeitig die Gasaufnahmefähigkeit zu erhalten, was es ideal für Filter oder Katalysatoren macht.
- Das Verfahren ist auch entscheidend für die Herstellung von Bauteilen mit großer Härte, Zähigkeit und Präzision, die in Branchen wie der Luft- und Raumfahrt und der Medizintechnik unerlässlich sind.
-
Umwandlung von keramischen Pulvern:
- Das Sintern verwandelt Keramikpulver in polykristalline keramische Werkstoffe mit spezifischen Eigenschaften und ist damit der wichtigste Schritt bei der Herstellung von Hochleistungskeramik.
- Diese Umwandlung erfolgt durch Diffusion und Stoffübertragung, was zu einer Verdichtung und einem einheitlichen Gefüge führt.
Durch die Nutzung dieser Vorteile bietet das Sintern von Keramik eine robuste und vielseitige Lösung für die Herstellung von Hochleistungswerkstoffen, die den Anforderungen der modernen Industrie gerecht werden.
Zusammenfassende Tabelle:
Leistungen | Beschreibung |
---|---|
Verbesserte mechanische Eigenschaften | Erhöht die Festigkeit, Zähigkeit und Härte durch Verringerung der Porosität. |
Verbesserte Gleichmäßigkeit und Reinheit | Garantiert hohe Reinheit und Gleichmäßigkeit für gleichbleibende Ergebnisse. |
Herstellung komplexer Formen | Produziert komplizierte Designs und präzise Geometrien mit hoher Genauigkeit. |
Maßgeschneiderte Materialkombinationen | Ermöglicht die Anpassung an spezifische Eigenschaften wie Abriebfestigkeit. |
Kosteneffizienz | Reduziert die Werkzeugkosten und ermöglicht die Massenproduktion mit Präzision. |
Verbesserte thermische/elektrische Stützen | Verbessert die Leitfähigkeit und Transparenz für Elektronik- und Energieanwendungen. |
Vielseitigkeit bei anspruchsvollen Matten | Verarbeitet hochschmelzende Materialien wie hochschmelzende Metalle und Keramiken. |
Reduktion von Oberflächensauerstoff | Eliminiert Schmiermittel und reduziert den Oberflächensauerstoff für saubere, langlebige Komponenten. |
Anwendungsspezifische Vorteile | Ideal für Filter, Katalysatoren und Komponenten in der Luft- und Raumfahrt sowie in medizinischen Geräten. |
Umwandlung von keramischen Pulvern | Umwandlung von Pulvern in polykristalline Keramiken mit gleichmäßigem Gefüge. |
Sind Sie bereit, die Sinterkeramik für Ihr nächstes Projekt zu nutzen? Kontaktieren Sie noch heute unsere Experten um loszulegen!