Thermisches Cracken ist ein Verfahren, das in der Erdölindustrie eingesetzt wird, um große Kohlenwasserstoffmoleküle durch Wärmezufuhr in kleinere, wertvollere Moleküle aufzuspalten. Dieser Prozess ist entscheidend für die Herstellung leichterer Fraktionen wie Benzin, Diesel und andere Petrochemikalien. Die Bedingungen für das thermische Cracken werden von mehreren Faktoren beeinflusst, darunter Temperatur, Druck, Verweilzeit und die Art des Ausgangsmaterials. Die Kenntnis dieser Bedingungen ist entscheidend für die Optimierung des Prozesses und die Erzielung der gewünschten Produktausbeute. Im Folgenden werden die Schlüsselfaktoren, die das thermische Cracken beeinflussen, und ihr Zusammenspiel zur Erzielung des gewünschten Ergebnisses erläutert.
Schlüsselpunkte erklärt:
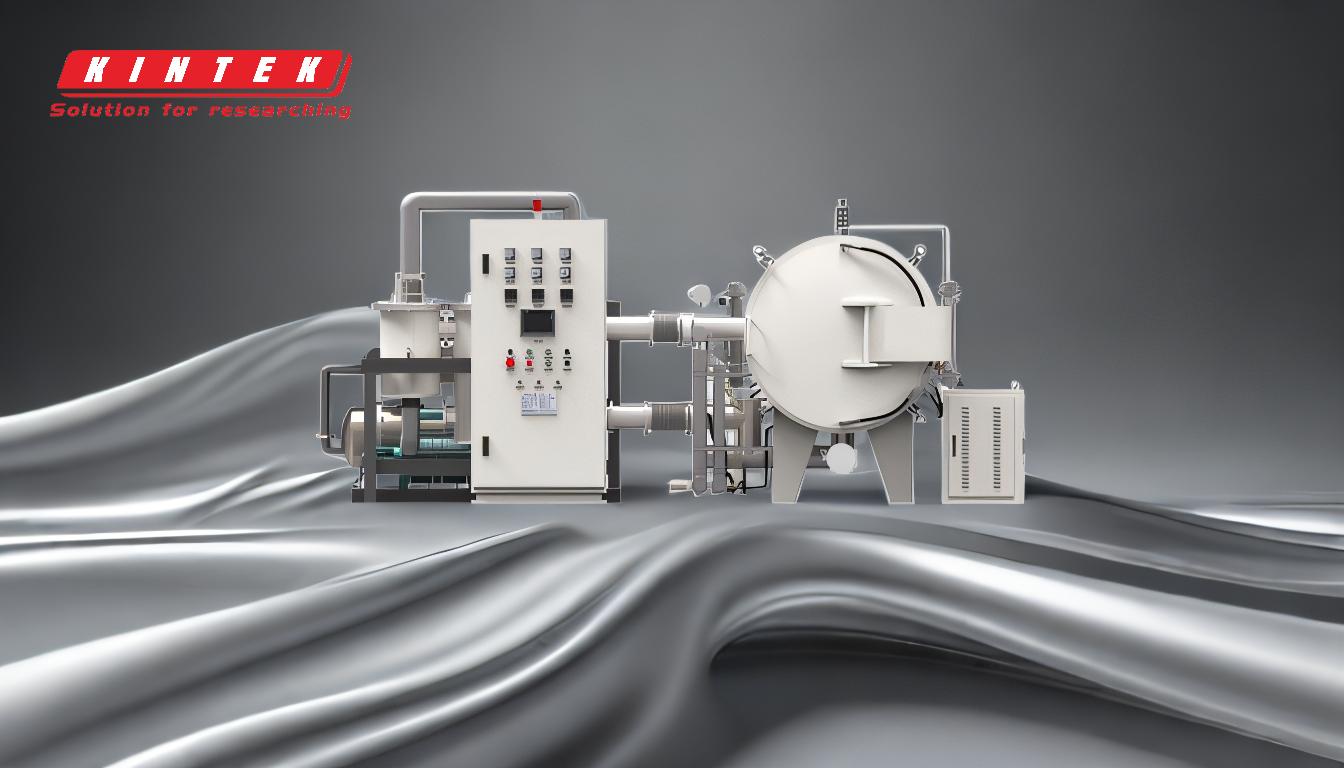
-
Temperatur:
- Rolle: Die Temperatur ist einer der wichtigsten Faktoren beim thermischen Cracken. Höhere Temperaturen liefern die nötige Energie, um die chemischen Bindungen in großen Kohlenwasserstoffmolekülen aufzubrechen.
- Optimaler Bereich: In der Regel erfolgt das thermische Cracken bei Temperaturen zwischen 450°C und 750°C. Die genaue Temperatur hängt von der Art des Ausgangsmaterials und den gewünschten Produkten ab.
- Auswirkungen: Höhere Temperaturen erhöhen im Allgemeinen die Crackrate, was zur Produktion leichterer Kohlenwasserstoffe führt. Zu hohe Temperaturen können jedoch zu unerwünschten Nebenreaktionen führen, wie z. B. Verkokung (Bildung von festen Kohlenstoffablagerungen).
-
Druck:
- Rolle: Der Druck beeinflusst die Phase der Kohlenwasserstoffe und die Geschwindigkeit der Spaltreaktionen. Niedrige Drücke begünstigen die Bildung von gasförmigen Produkten, während höhere Drücke zu mehr flüssigen Produkten führen können.
- Optimaler Bereich: Thermisches Cracken wird häufig bei niedrigem bis mittlerem Druck durchgeführt, typischerweise zwischen 1 und 10 Atmosphären. Die Wahl des Drucks hängt von dem gewünschten Schieferprodukt und dem spezifischen Crackverfahren ab.
- Aufschlag: Niedrigere Drücke können die Bildung leichterer Kohlenwasserstoffe fördern, erhöhen aber auch das Risiko der Verkokung. Höhere Drücke können die Verkokung verringern, aber auch die Ausbeute an leichteren Produkten reduzieren.
-
Verweilzeit:
- Rolle: Die Verweilzeit bezieht sich auf die Dauer, die das Einsatzmaterial den Crackbedingungen ausgesetzt ist. Sie ist entscheidend für die Kontrolle des Ausmaßes der Krackung und der Verteilung der Produkte.
- Optimaler Bereich: Die Verweilzeiten können je nach Verfahren stark variieren und reichen von einigen Sekunden bis zu mehreren Minuten. Kürzere Verweilzeiten werden in der Regel bei Verfahren wie dem Dampfkracken verwendet, während längere Zeiten bei der verzögerten Verkokung eingesetzt werden können.
- Auswirkungen: Längere Verweilzeiten ermöglichen ein umfangreicheres Cracken, was die Ausbeute an leichteren Produkten erhöhen kann. Zu lange Verweilzeiten können jedoch zu einem Übercracken führen, bei dem unerwünschte Nebenprodukte entstehen und die Verkokung zunimmt.
-
Zusammensetzung des Rohmaterials:
- Rolle: Die Art des Kohlenwasserstoff-Einsatzmaterials hat einen erheblichen Einfluss auf den Crackprozess. Verschiedene Einsatzstoffe haben unterschiedliche Molekularstrukturen, die ihr Crackverhalten beeinflussen.
- Arten von Rohstoffen: Zu den gängigen Rohstoffen gehören Naphtha, Gasöl und Rückstände. Leichtere Einsatzstoffe wie Naphtha lassen sich leichter cracken und liefern eine höhere Ausbeute an leichteren Produkten, während schwerere Einsatzstoffe wie Rückstände härtere Bedingungen erfordern und mehr Nebenprodukte erzeugen.
- Auswirkung: Die Wahl des Einsatzmaterials wirkt sich auf die für ein optimales Cracken erforderliche Temperatur, den Druck und die Verweilzeit aus. Schwerere Einsatzstoffe erfordern möglicherweise höhere Temperaturen und längere Verweilzeiten, können aber auch das Risiko der Verkokung erhöhen und komplexere Produktschiefer erzeugen.
-
Katalysator (falls zutreffend):
- Rolle: Während beim traditionellen thermischen Cracken kein Katalysator verwendet wird, werden bei einigen modernen Verfahren wie dem katalytischen Cracken Katalysatoren eingesetzt, um die Crackreaktionen zu verbessern.
- Auswirkung: Katalysatoren können die für das Cracken erforderliche Aktivierungsenergie senken, so dass der Prozess bei niedrigeren Temperaturen und Drücken ablaufen kann. Dadurch kann die Selektivität des Crackprozesses verbessert werden, was zu einer höheren Ausbeute an gewünschten Produkten und einer Verringerung unerwünschter Nebenprodukte führt.
-
Reaktorkonstruktion:
- Rolle: Die Konstruktion des für das thermische Cracken verwendeten Reaktors kann die Effizienz und Effektivität des Prozesses beeinflussen. Das Reaktordesign wirkt sich auf die Wärmeübertragung, die Durchmischung und die Verteilung der Verweilzeiten aus.
- Typen von Reaktoren: Zu den gängigen Reaktortypen gehören Rohrreaktoren, Wirbelschichtreaktoren und Trommeln mit verzögerter Verkokung. Jeder Reaktortyp hat seine Vor- und Nachteile in Bezug auf die Wärmeübertragung, die Steuerung der Verweilzeit und die einfache Bedienung.
- Aufschlag: Die Wahl der Reaktorkonstruktion kann sich auf die Temperatur- und Druckprofile innerhalb des Reaktors auswirken und so das Ausmaß der Spaltung und die Verteilung der Produkte beeinflussen. Die richtige Reaktorkonstruktion ist entscheidend für das Erreichen optimaler Crackbedingungen und die Minimierung unerwünschter Nebenreaktionen.
-
Abschrecken:
- Rolle: Unter Abschrecken versteht man das schnelle Abkühlen der gecrackten Produkte, um weitere Crackreaktionen zu verhindern. Dies ist entscheidend für die Kontrolle der Verteilung des Endprodukts.
- Methoden: Das Abschrecken kann mit Wasser, Dampf oder anderen Kühlmitteln erfolgen. Die Methode und die Geschwindigkeit des Abschreckens hängen von dem jeweiligen Prozess und dem gewünschten Produkt ab.
- Aufschlag: Eine wirksame Abschreckung trägt dazu bei, die gewünschte Produktverteilung zu erhalten, indem sie eine übermäßige Rissbildung und die Bildung unerwünschter Nebenprodukte verhindert. Sie trägt auch dazu bei, das Risiko der Verkokung in nachgeschalteten Anlagen zu verringern.
Zusammenfassend lässt sich sagen, dass die Bedingungen für das thermische Cracken durch eine Kombination aus Temperatur, Druck, Verweilzeit, Zusammensetzung des Einsatzmaterials und Reaktordesign bestimmt werden. Jeder dieser Faktoren spielt eine entscheidende Rolle bei der Bestimmung der Effizienz des Crackprozesses und der Qualität der Endprodukte. Durch sorgfältige Kontrolle dieser Bedingungen können die Betreiber den Crackprozess optimieren, um die gewünschte Mischung leichterer Kohlenwasserstoffe zu erzeugen und gleichzeitig unerwünschte Nebenprodukte und betriebliche Probleme wie Verkokung zu minimieren.
Zusammenfassende Tabelle:
Faktor | Rolle | Optimaler Bereich | Auswirkung |
---|---|---|---|
Temperatur | Liefert Energie zum Aufbrechen von Kohlenwasserstoffbindungen | 450°C bis 750°C | Höhere Temperaturen erhöhen die Rissbildung, können aber Verkokungen verursachen |
Druck | Beeinflusst Phase und Geschwindigkeit der Crackreaktionen | 1 bis 10 Atmosphären | Niedrigerer Druck begünstigt leichtere Kohlenwasserstoffe, kann aber das Verkokungsrisiko erhöhen |
Verweilzeit | Steuert das Ausmaß des Crackens und die Produktverteilung | Sekunden bis Minuten | Längere Zeiten erhöhen die Ausbeute an leichteren Kohlenwasserstoffen, bergen aber die Gefahr des Übercrackens |
Ausgangsstoff | Beeinflusst das Crackverhalten aufgrund der Molekularstruktur | Naphtha, Gasöl, Rückstände | Leichtere Einsatzstoffe lassen sich leichter cracken; schwerere erfordern strengere Bedingungen |
Konstruktion des Reaktors | Beeinflusst Wärmeübertragung, Durchmischung und Verweilzeitverteilung | Rohrreaktor, Wirbelschichtreaktor, Trommeln mit verzögerter Verkokung | Beeinflusst Effizienz und Produktverteilung |
Abschrecken | Schnelles Abkühlen der Produkte, um weiteres Cracken zu verhindern | Wasser, Dampf oder andere Kühlmedien | Bewahrt die Produktverteilung und reduziert das Verkokungsrisiko |
Optimieren Sie Ihr thermisches Krackverfahren mit fachkundiger Beratung. Kontaktieren Sie uns noch heute !