Reaktoren für die chemische Gasphasenabscheidung (Chemical Vapor Deposition, CVD) werden nach ihrer Bauart, ihren Betriebsbedingungen und ihren Anwendungen eingeteilt.Die beiden wichtigsten Reaktortypen sind Heißwandreaktoren und Kaltwandreaktoren , die jeweils unterschiedliche Vor- und Nachteile haben.Darüber hinaus können CVD-Verfahren unterteilt werden in geschlossene Reaktoren und offene Reaktoren je nach Gasflusssystem.Darüber hinaus sind CVD-Reaktoren oft auf bestimmte Verfahren zugeschnitten, wie z. B. Atmosphärendruck-CVD (APCVD), Niederdruck-CVD (LPCVD), Ultrahochvakuum-CVD (UHV/CVD) und plasmaunterstützte CVD (PECVD), die jeweils für unterschiedliche Materialien und Anforderungen an die Schichtabscheidung optimiert sind.Das Verständnis dieser Reaktortypen ist entscheidend für die Auswahl des geeigneten Systems für bestimmte Anwendungen, z. B. in der Halbleiterfertigung, Beschichtung oder Nanotechnologie.
Die wichtigsten Punkte erklärt:
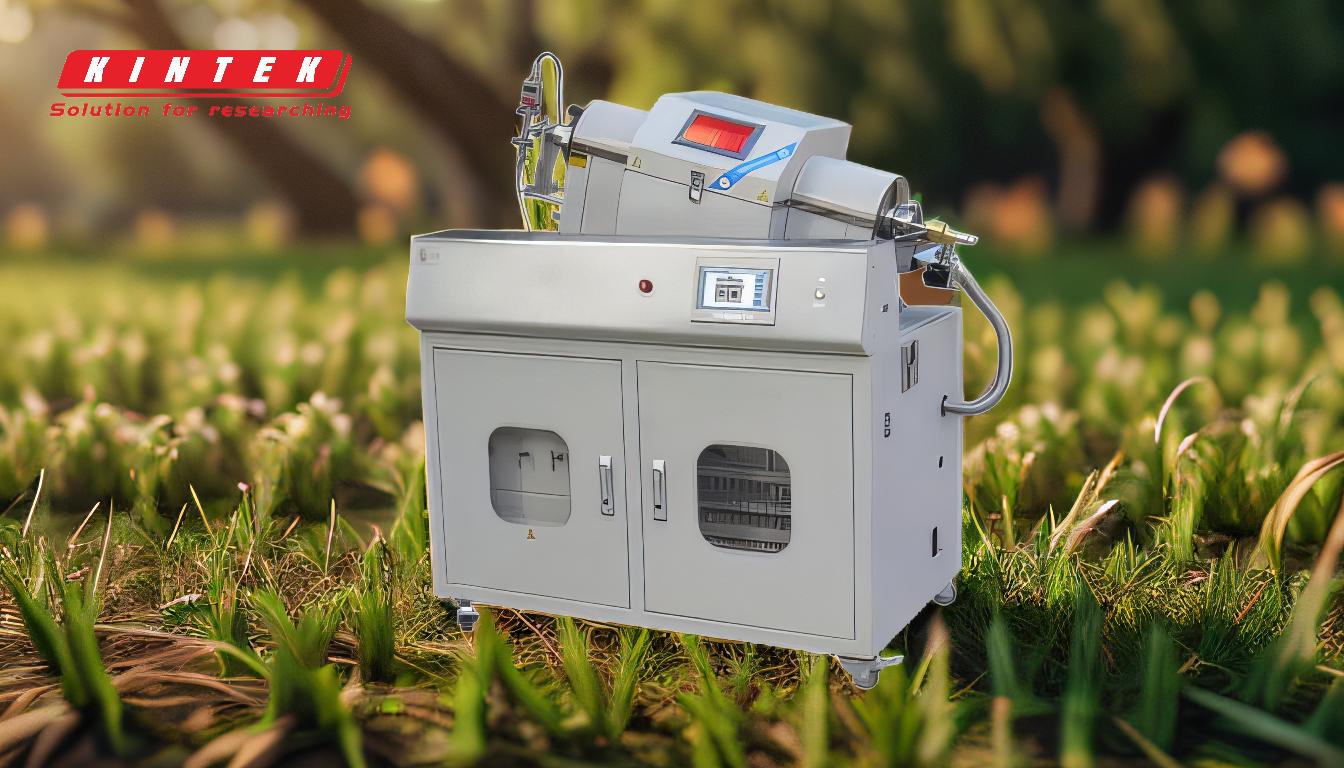
-
Heißwandreaktoren vs. Kaltwandreaktoren
-
Heißwandreaktoren:
- Die gesamte Reaktorkammer, einschließlich der Wände, wird gleichmäßig beheizt.
- Üblicherweise verwendet in Stapelverarbeitung bei der mehrere Wafer (100-200) gleichzeitig bearbeitet werden.
-
Vorteile:
- Die gleichmäßige Temperaturverteilung gewährleistet eine gleichmäßige Schichtabscheidung.
- Geeignet für Hochtemperaturprozesse wie LPCVD.
-
Benachteiligungen:
- Höherer Energieverbrauch durch die Beheizung der gesamten Kammer.
- Möglichkeit unerwünschter Ablagerungen an den Kammerwänden.
-
Kaltwandreaktoren:
- Nur das Substrat wird erhitzt, während die Kammerwände kühl bleiben.
- Häufig verwendet bei Einzel-Wafer-Verarbeitung und integriert in Cluster-Tools für fortgeschrittene Anwendungen wie die Gate-Stack-Verarbeitung.
-
Vorteile:
- Energieeffizient, da nur das Substrat erwärmt wird.
- Verringert unerwünschte Ablagerungen an den Kammerwänden.
-
Benachteiligungen:
- Temperaturgradienten können zu einer ungleichmäßigen Schichtabscheidung führen.
- Erfordert eine präzise Steuerung der Heizsysteme.
-
Heißwandreaktoren:
-
Geschlossene Reaktoren vs. offene Reaktoren
-
Geschlossene Reaktoren:
- Die Reaktanten befinden sich in einem versiegelten Behälter, und die Reaktion findet in diesem geschlossenen System statt.
- Geeignet für kleine oder spezielle Anwendungen.
-
Vorteile:
- Minimaler Reaktantenverlust.
- Kontrollierte Umgebung reduziert Kontaminationsrisiken.
-
Benachteiligungen:
- Begrenzte Skalierbarkeit für die Produktion in großem Maßstab.
- Es ist schwierig, die Reaktanten während des Prozesses aufzufüllen.
-
Offene Reaktoren (Fließgas-CVD):
- Die Reaktanten werden kontinuierlich in das System eingeleitet, und die Nebenprodukte werden in einem fließenden Gasstrom entfernt.
- Häufig in industriellen Anwendungen eingesetzt.
-
Vorteile:
- Skalierbar für die Produktion großer Mengen.
- Ermöglicht eine kontinuierliche Auffüllung der Reaktanten.
-
Nachteile:
- Höherer Reaktantenverbrauch.
- Erfordert eine genaue Kontrolle der Gasdurchflussmengen.
-
Geschlossene Reaktoren:
-
Arten von CVD-Verfahren und ihre Reaktoren
-
Atmosphärendruck-CVD (APCVD):
- Arbeitet bei Umgebungsdruck.
- Wird für die Abscheidung von Materialien wie Siliziumdioxid und Siliziumnitrid verwendet.
- Reaktortyp:In der Regel Kaltwandreaktoren zur Minimierung des Energieverbrauchs.
-
Niederdruck-CVD (LPCVD):
- Arbeitet bei reduziertem Druck (0,1-10 Torr).
- Wird für die Abscheidung von Materialien wie Polysilizium und Siliziumnitrid verwendet.
- Reaktortyp:Heißwandreaktoren für gleichmäßige Temperaturverteilung.
-
Ultrahochvakuum CVD (UHV/CVD):
- Funktioniert bei extrem niedrigen Drücken (unter 10^-6 Torr).
- Wird für hochreine Schichten in modernen Halbleiteranwendungen verwendet.
- Reaktortyp:Kaltwandreaktoren zur Minimierung der Kontamination.
-
Plasmaunterstützte CVD (PECVD):
- Nutzt Plasma zur Aktivierung chemischer Reaktionen bei niedrigeren Temperaturen.
- Wird für die Abscheidung von Materialien wie Siliziumdioxid und Siliziumnitrid bei niedrigen Temperaturen verwendet.
- Reaktortyp:Kaltwandreaktoren zur Vermeidung von Plasmaschäden an den Kammerwänden.
-
Atomlagenabscheidung (ALD):
- Eine Variante des CVD-Verfahrens, bei dem die Schichten atomar nacheinander abgeschieden werden.
- Wird für ultradünne, konforme Schichten in der Nanotechnologie verwendet.
- Reaktortyp:Kaltwandreaktoren für präzise Kontrolle.
-
Atmosphärendruck-CVD (APCVD):
-
Anwendungen und Materialüberlegungen
-
Hochtemperatur-CVD:
- Für die Abscheidung von Materialien wie Silizium und Titannitrid bei Temperaturen bis zu 1500°C.
- Reaktortyp:Heißwandreaktoren für Hochtemperaturstabilität.
-
Niedertemperatur-CVD:
- Für die Abscheidung von Isolierschichten wie Siliziumdioxid bei niedrigen Temperaturen.
- Reaktortyp:Kaltwandreaktoren zur Vermeidung von Substratschäden.
-
Plasma-unterstützte CVD:
- Für die Abscheidung von Materialien wie diamantartigem Kohlenstoff (DLC) und Siliziumkarbid.
- Reaktortyp:Kaltwandreaktoren zur Vermeidung von Plasmaschäden.
-
Photo-unterstützte CVD:
- Nutzt Laserphotonen zur Aktivierung chemischer Reaktionen.
- Wird für präzise, örtlich begrenzte Ablagerungen verwendet.
- Reaktortyp:Kaltwandreaktoren für kontrollierte Laserinteraktion.
-
Hochtemperatur-CVD:
-
Auswahlkriterien für CVD-Reaktoren
-
Anforderungen an das Material:
- Hochtemperaturmaterialien wie Siliziumkarbid können Heißwandreaktoren erfordern, während für Niedertemperaturmaterialien wie Siliziumdioxid Kaltwandreaktoren verwendet werden können.
-
Prozess-Skala:
- Stapelverarbeitung (Heißwandreaktoren) für die Großserienproduktion.
- Einzelwafer-Verarbeitung (Kaltwandreaktoren) für fortgeschrittene Anwendungen mit geringen Stückzahlen.
-
Energie-Effizienz:
- Kaltwandreaktoren sind energieeffizienter bei Prozessen, die eine örtlich begrenzte Erwärmung erfordern.
-
Gleichmäßigkeit des Films:
- Heißwandreaktoren bieten eine bessere Gleichmäßigkeit bei der Verarbeitung großer Mengen.
-
Anforderungen an das Material:
Durch die Kenntnis dieser Reaktortypen und ihrer Anwendungen können Käufer von Anlagen fundierte Entscheidungen auf der Grundlage ihrer spezifischen Material-, Prozess- und Produktionsanforderungen treffen.
Zusammenfassende Tabelle:
Reaktortyp | Wesentliche Merkmale | Anwendungen |
---|---|---|
Heißwandreaktoren | Gleichmäßige Beheizung, hoher Energieverbrauch, Batch-Verfahren | LPCVD, Hochtemperaturprozesse |
Kaltwand-Reaktoren | Energieeffizient, Single-Wafer-Verarbeitung, präzise Steuerung | PECVD, UHV/CVD, ALD |
Geschlossene Reaktoren | Minimaler Reaktantenverlust, kontrollierte Umgebung, begrenzte Skalierbarkeit | Kleiner Maßstab oder spezialisierte Anwendungen |
Offene Reaktoren | Skalierbar, kontinuierlicher Nachschub, höherer Reaktantenverbrauch | Industrielle Anwendungen, Großserienproduktion |
APCVD | Umgebungsdruck, Kaltwandreaktoren | Abscheidung von Siliziumdioxid und Siliziumnitrid |
LPCVD | Reaktoren mit reduziertem Druck und heißer Wand | Abscheidung von Polysilizium und Siliziumnitrid |
UHV/CVD | Ultrahochvakuum, Kaltwandreaktoren | Hochreine Schichten in modernen Halbleiteranwendungen |
PECVD | Plasmaaktivierung, Kaltwandreaktoren | Niedertemperaturabscheidung von Siliziumdioxid, Siliziumnitrid |
ALD | Atomare Schichtabscheidung, Kaltwandreaktoren | Ultradünne, konforme Schichten in der Nanotechnologie |
Suchen Sie den richtigen CVD-Reaktor für Ihre Anwendung? Kontaktieren Sie noch heute unsere Experten um die perfekte Lösung zu finden!