Beim Aufkohlen handelt es sich um einen Wärmebehandlungsprozess, bei dem Kohlenstoff in die Oberfläche von kohlenstoffarmem Stahl eingebracht wird, wodurch dessen Härte erhöht wird und gleichzeitig ein weicherer, duktilerer Kern erhalten bleibt. Dieses Verfahren bietet zwar erhebliche Vorteile, wie z. B. eine verbesserte Verschleißfestigkeit und Oberflächenhärte, kann jedoch auch zu verschiedenen Arten von Schäden führen, wenn es nicht richtig kontrolliert wird. Zu diesen Schäden zählen Versprödung, verringerte Ermüdungsfestigkeit und mögliche Risse oder Verformungen des Materials. Das Verständnis dieser Risiken ist entscheidend für die Gewährleistung der Langlebigkeit und Leistung aufgekohlter Komponenten.
Wichtige Punkte erklärt:
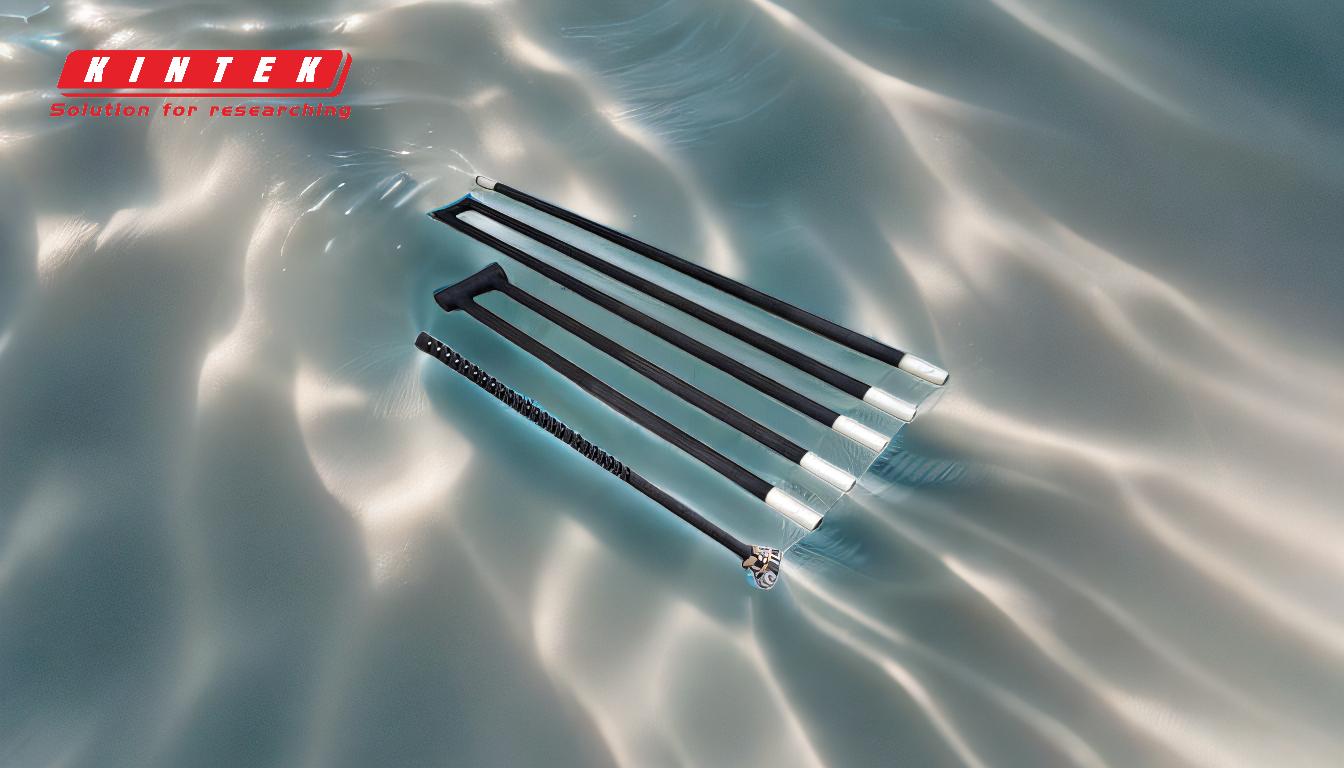
-
Versprödung:
- Erläuterung: Durch die Aufkohlung erhöht sich der Kohlenstoffgehalt an der Oberfläche, was zur Bildung spröder Phasen wie Martensit führen kann. Obwohl Martensit hart ist, neigt es unter Belastung auch zur Rissbildung.
- Auswirkungen: Diese Versprödung kann die Widerstandsfähigkeit der Komponente gegenüber Stößen oder zyklischer Belastung beeinträchtigen und sie anfälliger für plötzliche Ausfälle machen.
- Schadensbegrenzung: Richtiges Anlassen nach der Aufkohlung kann die Sprödigkeit verringern, indem etwas Martensit in härtere Mikrostrukturen umgewandelt wird.
-
Reduzierte Ermüdungsfestigkeit:
- Erläuterung: Die durch Aufkohlung erreichte hohe Oberflächenhärte kann eine scharfe Übergangszone zwischen der gehärteten Oberfläche und dem weicheren Kern erzeugen. Diese Übergangszone kann als Spannungskonzentrator wirken.
- Auswirkungen: Spannungskonzentrationen können Ermüdungsrisse auslösen, insbesondere unter zyklischen Belastungsbedingungen, wodurch die Gesamtermüdungslebensdauer der Komponente verkürzt wird.
- Schadensbegrenzung: Allmähliche Kohlenstoffgradienten und Nachaufkohlungsbehandlungen wie Kugelstrahlen können dazu beitragen, die Spannungen gleichmäßiger zu verteilen.
-
Risse und Verzerrungen:
- Erläuterung: Die hohen Temperaturen beim Aufkohlen können zu thermischen Spannungen führen, die zu Verformungen oder Verwerfungen des Bauteils führen. Darüber hinaus kann schnelles Abkühlen (Abschrecken) zur Rissbildung führen.
- Auswirkungen: Risse und Verformungen können die Komponente unbrauchbar machen und kostspielige Reparaturen oder Ersatz erfordern.
- Schadensbegrenzung: Kontrollierte Heiz- und Kühlraten sowie die richtige Konstruktion der Vorrichtungen können diese Risiken minimieren.
-
Oxidation und Entkohlung:
- Erläuterung: Während des Aufkohlungsprozesses kann die Einwirkung von Sauerstoff zu Oberflächenoxidation oder Entkohlung führen, wobei Kohlenstoff von der Oberfläche verloren geht.
- Auswirkungen: Oxidation und Entkohlung können die Oberflächeneigenschaften verschlechtern und die Härte und Verschleißfestigkeit verringern.
- Schadensbegrenzung: Der Einsatz von Schutzatmosphären oder Vakuumaufkohlung kann Oxidation und Entkohlung verhindern.
-
Ungleichmäßige Gehäusetiefe:
- Erläuterung: Eine inkonsistente Aufkohlung kann zu ungleichmäßigen Einsatztiefen führen, wobei einige Bereiche zu stark aufgekohlt sind, während andere zu wenig aufgekohlt sind.
- Auswirkungen: Ungleichmäßige Härtetiefen können zu inkonsistenten mechanischen Eigenschaften führen und die Leistung der Komponente beeinträchtigen.
- Schadensbegrenzung: Die präzise Steuerung der Prozessparameter wie Temperatur und Gaszusammensetzung gewährleistet eine gleichmäßige Härtetiefe.
-
Eigenspannungen:
- Erläuterung: Der Aufkohlungsprozess, insbesondere das Abschrecken, kann Eigenspannungen im Material hervorrufen.
- Auswirkungen: Diese Spannungen können zu Dimensionsinstabilität oder vorzeitigem Versagen unter Belastung führen.
- Schadensbegrenzung: Stressabbauende Behandlungen, wie z. B. Tempern, können Eigenspannungen lindern.
-
Kosten und Komplexität:
- Erläuterung: Die Aufkohlung erfordert spezielle Ausrüstung und eine präzise Steuerung der Prozessparameter, was die Produktionskosten und die Komplexität erhöht.
- Auswirkungen: Höhere Kosten und Komplexität können die Aufkohlung für bestimmte Anwendungen weniger machbar machen.
- Schadensbegrenzung: Die Optimierung der Prozessparameter und die Auswahl geeigneter Materialien können dabei helfen, Kosten und Leistung in Einklang zu bringen.
Durch das Verständnis dieser potenziellen Schäden und die Umsetzung geeigneter Schadensminderungsstrategien können die Vorteile der Aufkohlung maximiert und gleichzeitig die Risiken minimiert werden. Dadurch wird sichergestellt, dass aufgekohlte Komponenten die gewünschte Balance aus Härte, Haltbarkeit und Leistung erreichen.
Übersichtstabelle:
Schadensart | Erläuterung | Auswirkungen | Schadensbegrenzung |
---|---|---|---|
Versprödung | Durch den erhöhten Kohlenstoffgehalt bilden sich spröde Phasen wie Martensit. | Unter Belastung kann es zu Rissen kommen, die zu einem plötzlichen Ausfall führen. | Richtiges Anlassen, um Martensit in härtere Mikrostrukturen umzuwandeln. |
Reduzierte Ermüdungsfestigkeit | Scharfe Übergangszonen wirken als Spannungskonzentratoren. | Es entstehen Ermüdungsrisse, die die Lebensdauer der Komponenten verkürzen. | Allmähliche Kohlenstoffgradienten und Kugelstrahlen. |
Risse und Verzerrungen | Hohe Temperaturen verursachen thermische Spannungen; Schnelles Abkühlen führt zu Rissen. | Komponenten verziehen sich oder reißen, was kostspielige Reparaturen erfordert. | Kontrollierte Heiz-/Kühlraten und richtiges Vorrichtungsdesign. |
Oxidation und Entkohlung | Die Einwirkung von Sauerstoff führt zu Oberflächenoxidation oder Kohlenstoffverlust. | Verschlechterte Oberflächeneigenschaften, wodurch Härte und Verschleißfestigkeit verringert werden. | Schutzatmosphären oder Vakuumaufkohlung. |
Ungleichmäßige Gehäusetiefe | Eine inkonsistente Aufkohlung führt zu ungleichmäßigen Härtetiefen. | Inkonsistente mechanische Eigenschaften, beeinträchtigte Leistung. | Präzise Kontrolle von Temperatur und Gaszusammensetzung. |
Eigenspannungen | Durch das Abschrecken entstehen Eigenspannungen. | Dimensionsinstabilität oder vorzeitiger Ausfall unter Last. | Stressabbauende Behandlungen wie Temperieren. |
Kosten und Komplexität | Erfordert spezielle Ausrüstung und präzise Prozesssteuerung. | Höhere Kosten und höhere Komplexität machen es für einige Anwendungen weniger machbar. | Optimieren Sie Prozessparameter und wählen Sie geeignete Materialien aus. |
Stellen Sie sicher, dass Ihre aufgekohlten Komponenten optimal funktionieren – Kontaktieren Sie noch heute unsere Experten für maßgeschneiderte Lösungen!