Die chemische Gasphasenabscheidung (Chemical Vapor Deposition, CVD) ist eine weit verbreitete Technik für die Abscheidung von dünnen Schichten und Beschichtungen, die jedoch mit einigen erheblichen Nachteilen verbunden ist.Dazu gehören betriebliche Einschränkungen wie hohe Temperaturen, die empfindliche Substrate beschädigen können, und der Bedarf an speziellen Geräten und Anlagen.Außerdem werden bei diesem Verfahren häufig toxische und korrosive Vorprodukte und Nebenprodukte verwendet, was eine Herausforderung für Sicherheit und Umwelt darstellt.Die begrenzte Größe von Vakuumkammern und die Schwierigkeit, gleichmäßige Beschichtungen zu erzielen, erschweren die Anwendung zusätzlich.Darüber hinaus ist die Synthese von Mehrkomponentenmaterialien aufgrund von Schwankungen des Dampfdrucks und der Wachstumsraten eine Herausforderung, die zu heterogenen Zusammensetzungen führt.Diese Faktoren schränken insgesamt die Vielseitigkeit und Zugänglichkeit der CVD in bestimmten Anwendungen ein.
Die wichtigsten Punkte erklärt:
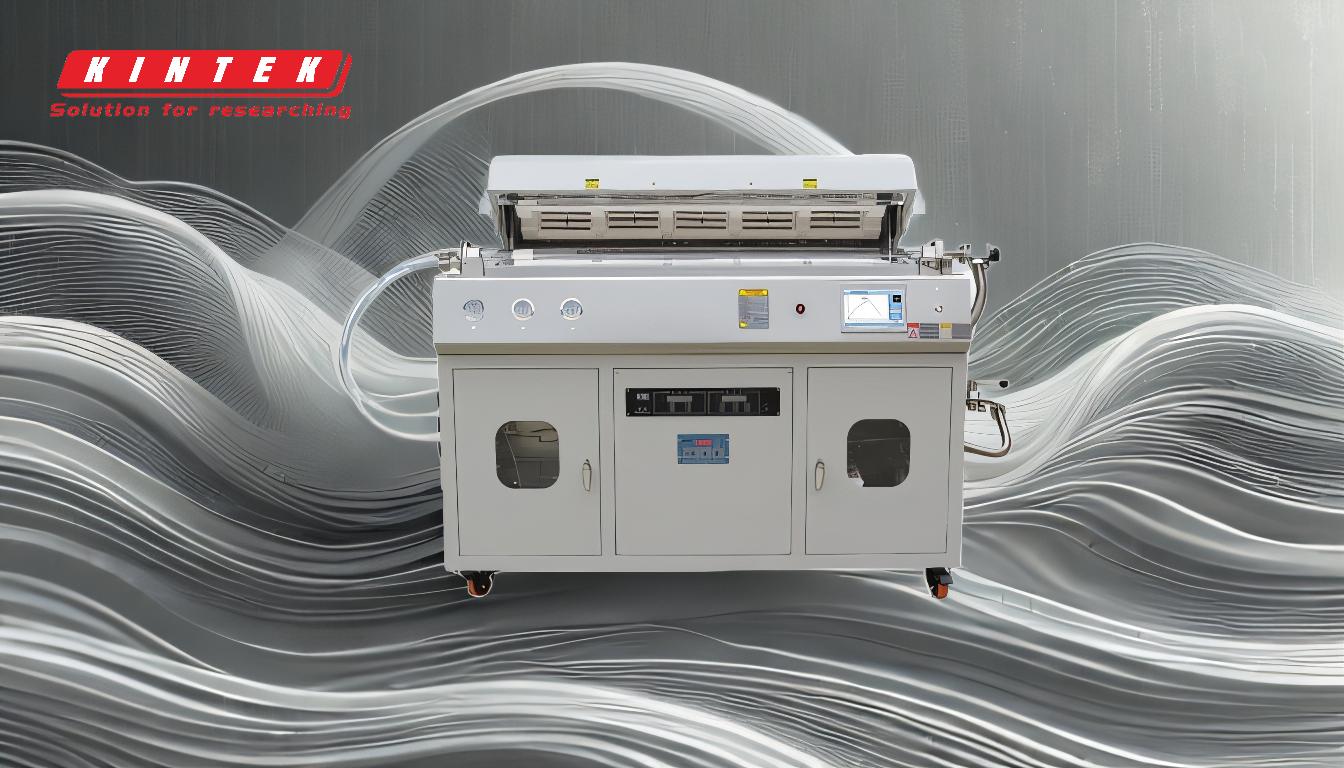
-
Anforderungen bei hohen Temperaturen:
- CVD arbeitet in der Regel bei hohen Temperaturen, was bei vielen Substraten zu thermischer Instabilität führen kann.Dies macht das Verfahren ungeeignet für Materialien, die großer Hitze nicht standhalten können, was seine Anwendbarkeit in bestimmten Branchen einschränkt.
-
Toxische und korrosive Vorläuferstoffe:
- Das Verfahren erfordert chemische Ausgangsstoffe mit hohem Dampfdruck, die oft giftig, gefährlich und schwer zu handhaben sind.Dies wirft Sicherheitsbedenken auf und erhöht die Komplexität des Prozesses.
-
Gefährliche Nebenprodukte:
- Die Neutralisierung von CVD-Nebenprodukten, die häufig giftig und korrosiv sind, ist sowohl problematisch als auch kostspielig.Die ordnungsgemäße Entsorgung und das Management dieser Nebenprodukte sind unerlässlich, erhöhen aber die Gesamtkosten und die Komplexität.
-
Größenbeschränkungen von Vakuumkammern:
- Die Größe der bei der CVD verwendeten Vakuumkammer ist begrenzt, was die Beschichtung größerer Oberflächen oder Bauteile erschwert.Dies schränkt den Maßstab ein, in dem CVD effektiv angewendet werden kann.
-
Schwierigkeit, gleichmäßige Beschichtungen zu erzielen:
- CVD führt häufig zu einer "Alles-oder-Nichts"-Beschichtung, was eine vollständige und gleichmäßige Abdeckung der Materialien erschwert.Dies kann zu Unregelmäßigkeiten im Endprodukt führen.
-
Herausforderungen bei der Synthese von Multikomponentenmaterialien:
- Schwankungen bei Dampfdruck, Keimbildung und Wachstumsraten während der Umwandlung von Gas in Partikel können zu heterogenen Zusammensetzungen führen.Dies erschwert die Synthese von hochwertigen Mehrkomponentenmaterialien.
-
Bildung von harten Aggregaten:
- Die Agglomeration in der Gasphase kann zur Bildung harter Aggregate führen, was die Synthese hochwertiger Massenmaterialien erschwert und die Gesamtqualität der Abscheidung beeinträchtigt.
-
Mangel an geeigneten Vorläufern:
- Bei der thermisch aktivierten CVD gibt es keine extrem flüchtigen, ungiftigen und nicht-pyrophoren Ausgangsstoffe.Dies schränkt die Palette der Materialien ein, die mit dieser Methode effektiv abgeschieden werden können.
-
Operative Einschränkungen:
- CVD kann in der Regel nicht vor Ort durchgeführt werden und erfordert, dass die Teile zur Bearbeitung in einzelne Komponenten zerlegt werden.Dies macht spezialisierte Beschichtungszentren erforderlich, was die logistische Komplexität und die Kosten erhöht.
Diese Nachteile verdeutlichen die Herausforderungen, die mit CVD verbunden sind, und machen es unerlässlich, diese Faktoren bei der Auswahl einer Beschichtungsmethode für bestimmte Anwendungen sorgfältig zu berücksichtigen.
Zusammenfassende Tabelle:
Benachteiligung | Beschreibung |
---|---|
Anforderungen bei hohen Temperaturen | Erhöhte Temperaturen können empfindliche Substrate beschädigen und die Anwendbarkeit einschränken. |
Toxische und korrosive Vorläuferstoffe | Erfordert gefährliche Chemikalien, die Sicherheits- und Handhabungsprobleme aufwerfen. |
Gefährliche Nebenprodukte | Toxische und korrosive Nebenprodukte erhöhen die Entsorgungskosten und den Aufwand. |
Größenbeschränkungen von Vakuumkammern | Die begrenzte Größe der Kammern schränkt die Beschichtung größerer Oberflächen ein. |
Schwierigkeit, gleichmäßige Beschichtungen zu erzielen | Dies führt zu einer uneinheitlichen oder unvollständigen Abdeckung. |
Herausforderungen bei der Synthese von Multikomponentenmaterialien | Schwankungen des Dampfdrucks und der Wachstumsraten führen zu heterogenen Zusammensetzungen. |
Bildung von harten Aggregaten | Die Agglomeration in der Gasphase erschwert die Synthese von Schüttgut. |
Mangel an geeigneten Vorläufern | Begrenzte Verfügbarkeit von ungiftigen, flüchtigen Ausgangsstoffen. |
Operative Einschränkungen | Erfordert spezielle Einrichtungen, was die logistische Komplexität und die Kosten erhöht. |
Benötigen Sie Hilfe bei der Auswahl der richtigen Abscheidungsmethode? Kontaktieren Sie noch heute unsere Experten für eine persönliche Beratung!