Das DC-Magnetron-Sputtern wird zwar häufig für die Dünnschichtabscheidung eingesetzt, weist jedoch mehrere bemerkenswerte Nachteile auf. Dazu gehören Einschränkungen bei der Materialkompatibilität, etwa die Unfähigkeit, Materialien mit geringer Leitfähigkeit und isolierende Materialien aufgrund der Ladungsansammlung zu sputtern. Darüber hinaus kann der Prozess aufgrund des intensiven Ionenbeschusses zu einer stärkeren Erwärmung des Substrats und zu strukturellen Defekten führen. Die Optimierung von Folieneigenschaften ist aufgrund der zahlreichen Steuerungsparameter oft komplex und zeitaufwändig. Darüber hinaus weist das Verfahren Einschränkungen hinsichtlich der Plasmastabilität, der Targetausnutzung und der Kosteneffizienz auf. Diese Nachteile machen es für bestimmte Anwendungen weniger geeignet, insbesondere für solche, die eine präzise Kontrolle der Materialeigenschaften erfordern oder nichtleitende Materialien verwenden.
Wichtige Punkte erklärt:
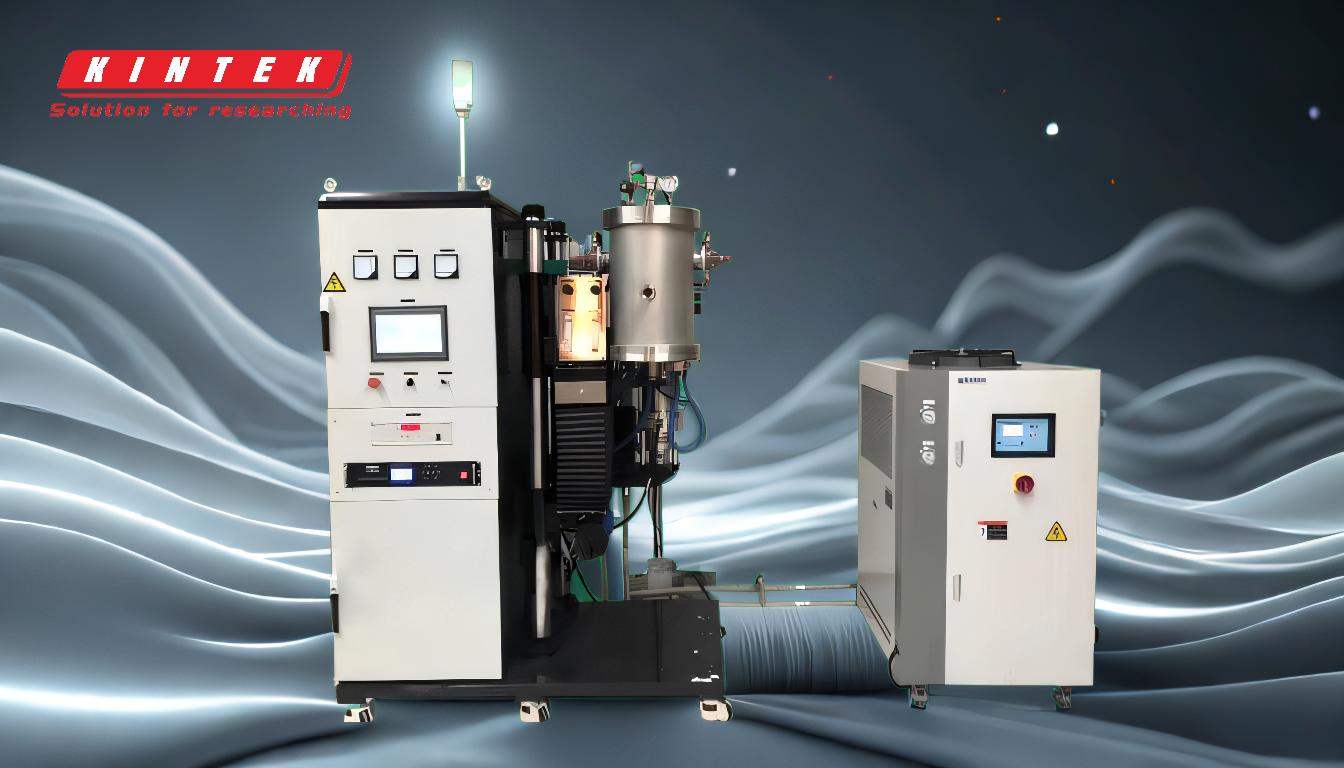
-
Unfähigkeit, Materialien mit geringer Leitfähigkeit und Isoliermaterialien zu zerstäuben:
- Beim DC-Magnetronsputtern wird Strom durch das Targetmaterial geleitet. Dies macht es für Materialien mit geringer Leitfähigkeit oder Isoliermaterialien ungeeignet, da die Ladungsansammlung auf der Targetoberfläche den Sputterprozess stört. Diese Einschränkung wird durch HF-Magnetronsputtern behoben, bei dem Wechselstrom zur effektiven Bearbeitung solcher Materialien eingesetzt wird.
-
Höhere Substraterwärmung und Strukturfehler:
- Der Prozess kann zu einer erheblichen Erwärmung des Substrats führen, wobei die Temperaturen bis zu 250 °C ansteigen können. Dies ist auf den hochenergetischen Ionenbeschuss des Substrats zurückzuführen, der auch zu Strukturdefekten in den abgeschiedenen Filmen führen kann. Solche Mängel können die Qualität und Leistung der dünnen Filme beeinträchtigen.
-
Komplexe Optimierung von Filmeigenschaften:
- Beim DC-Magnetronsputtern sind zahlreiche Steuerparameter wie Leistung, Druck und Gaszusammensetzung erforderlich, die sorgfältig optimiert werden müssen, um die gewünschten Filmeigenschaften zu erreichen. Dieser Optimierungsprozess kann zeitaufwändig sein und erfordert umfangreiches Fachwissen, wodurch der Prozess für bestimmte Anwendungen weniger effizient ist.
-
Begrenzte Plasmastabilität und Zielausnutzung:
- Das beim DC-Magnetron-Sputtern verwendete Plasma kann instabil sein und die Konsistenz des Abscheidungsprozesses beeinträchtigen. Darüber hinaus wird das Zielmaterial häufig nicht ausreichend genutzt, was zu höheren Kosten und Materialverschwendung führt.
-
Hohe Prozesskosten:
- Die mit dem DC-Magnetron-Sputtern verbundenen Ausrüstungs- und Betriebskosten sind relativ hoch. Dazu gehören die Kosten für die Aufrechterhaltung der Vakuumbedingungen, spezielle Ziele und die für den Prozess erforderliche Energie. Diese Faktoren können dazu führen, dass das Verfahren für Anwendungen im großen Maßstab oder mit geringem Budget weniger wirtschaftlich ist.
-
Geometrische Einschränkungen und schlechte Filmbindung:
- Die effektive Beschichtungsfläche beim DC-Magnetron-Sputtern ist begrenzt, was die Größe und Form der zu beschichtenden Werkstücke einschränkt. Darüber hinaus ist die Energie der gesputterten Partikel oft niedrig, was zu einer schlechten Bindungsfestigkeit zwischen Film und Substrat führt. Dies kann zur Bildung poröser und rauer Säulenstrukturen führen, die den Anforderungen für bestimmte Hochleistungsanwendungen möglicherweise nicht genügen.
Durch das Verständnis dieser Nachteile können Benutzer fundierte Entscheidungen darüber treffen, ob DC-Magnetron-Sputtern für ihre spezifischen Anforderungen geeignet ist oder ob alternative Abscheidungsmethoden wie RF-Magnetron-Sputtern in Betracht gezogen werden sollten.
Übersichtstabelle:
Nachteil | Beschreibung |
---|---|
Unfähigkeit, Materialien mit geringer Leitfähigkeit zu sputtern | Die Ladungsansammlung stört das Sputtern isolierender oder schlecht leitender Materialien. |
Höhere Substraterwärmung | Temperaturen bis zu 250 °C können zu Strukturfehlern in Folien führen. |
Komplexe Optimierung | Zahlreiche Steuerparameter machen das Erreichen gewünschter Filmeigenschaften zeitaufwändig. |
Begrenzte Plasmastabilität | Instabiles Plasma beeinträchtigt die Abscheidungskonsistenz und die Zielausnutzung. |
Hohe Prozesskosten | Ausrüstungs-, Energie- und Materialkosten machen es für einige Anwendungen weniger wirtschaftlich. |
Geometrische Einschränkungen | Eine begrenzte Beschichtungsfläche und eine schlechte Filmbindung verringern die Eignung für bestimmte Anwendungen. |
Benötigen Sie Hilfe bei der Auswahl der richtigen Sputtermethode? Kontaktieren Sie noch heute unsere Experten für maßgeschneiderte Lösungen!