Die elektrolytische Abscheidung ist zwar für die Beschichtung und Materialherstellung weit verbreitet, hat jedoch mehrere Nachteile, die sich auf die Effizienz, die Kosten und den ökologischen Fußabdruck auswirken können.Zu den wichtigsten Nachteilen gehören die eingeschränkte Materialkompatibilität, der hohe Energieverbrauch, die ungleichmäßige Schichtdicke, Umweltbedenken aufgrund giftiger Nebenprodukte und die Schwierigkeit, eine gleichmäßige Abscheidung auf komplexen Geometrien zu erreichen.Darüber hinaus erfordert das Verfahren häufig eine präzise Steuerung der Parameter, was die Komplexität des Betriebs und die Kosten erhöhen kann.Aufgrund dieser Einschränkungen ist die Elektroabscheidung für bestimmte Anwendungen weniger geeignet, insbesondere für solche, die hohe Präzision, Umweltverträglichkeit oder Kosteneffizienz erfordern.
Die wichtigsten Punkte werden erklärt:
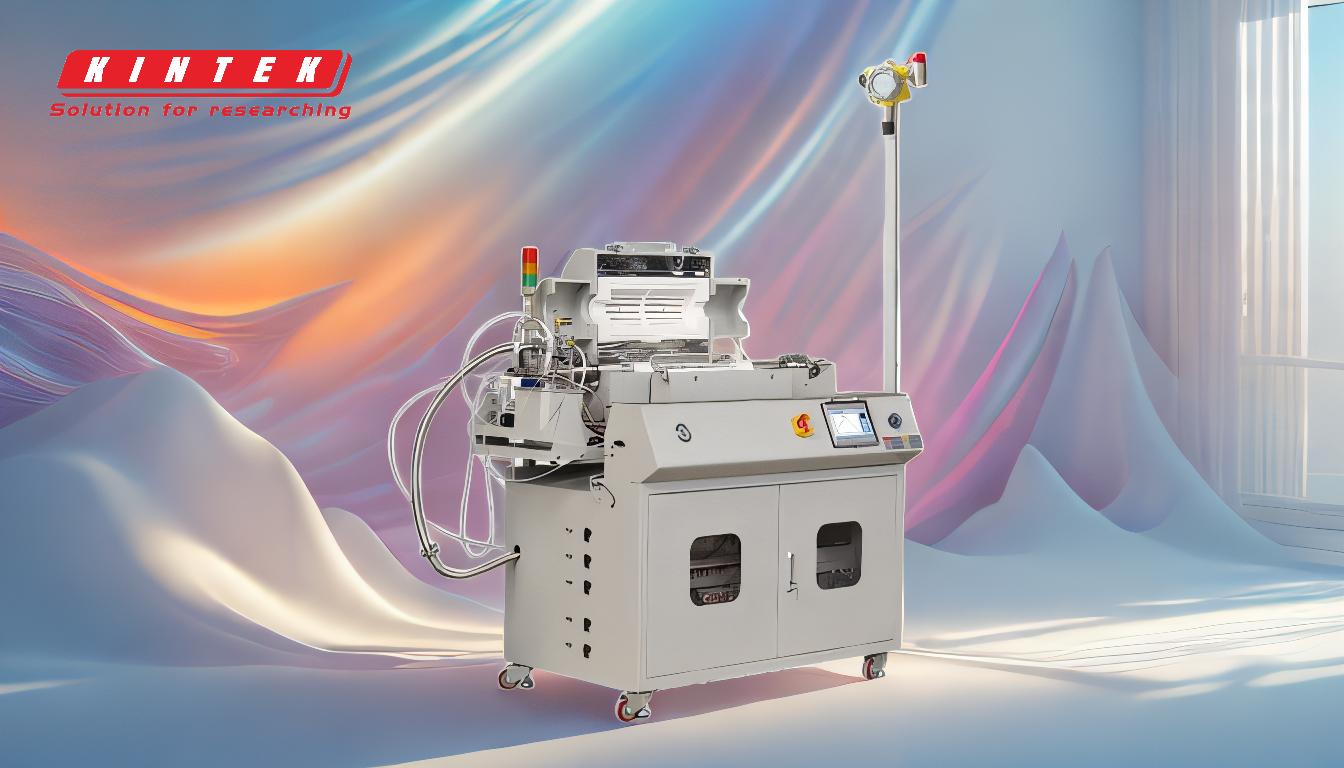
-
Begrenzte Materialkompatibilität
- Die elektrolytische Abscheidung ist in erster Linie für leitfähige Materialien geeignet, da sie auf dem Fluss von elektrischem Strom beruht, um Ionen auf einem Substrat abzuscheiden.
- Nicht leitende Materialien erfordern eine zusätzliche Vorbehandlung (z. B. Metallisierung), was die Kosten und den Aufwand erhöht.
- Bestimmte Materialien können auch ungünstig mit dem Elektrolyten reagieren, was zu schlechter Haftung oder Verunreinigung führt.
-
Hoher Energieverbrauch
- Das Verfahren erfordert eine kontinuierliche Versorgung mit elektrischer Energie, um die elektrochemischen Reaktionen aufrechtzuerhalten.
- Die Energiekosten können beträchtlich sein, insbesondere bei groß angelegten oder lang andauernden Verfahren.
- Ineffizienzen im Prozess, wie z. B. Widerstand im Elektrolyt oder im Substrat, können den Energieverbrauch noch weiter erhöhen.
-
Ungleichmäßige Beschichtungsdicke
- Die Elektroabscheidung führt häufig zu einer ungleichmäßigen Schichtdicke, insbesondere an Kanten, Ecken oder komplexen Geometrien.
- Dieses als "Kanteneffekt" bekannte Phänomen tritt auf, weil sich die elektrischen Felder an scharfen Merkmalen konzentrieren, was zu einer schnelleren Abscheidung in diesen Bereichen führt.
- Um eine gleichmäßige Schichtdicke zu erreichen, sind unter Umständen zusätzliche Schritte erforderlich, z. B. Maskierung oder Nachbearbeitung, die Zeit und Kosten erhöhen.
-
Umweltaspekte
- Bei dem Prozess entstehen giftige Nebenprodukte, darunter Schwermetalle und gefährliche Chemikalien, die sorgfältig behandelt werden müssen, um eine Verschmutzung der Umwelt zu verhindern.
- Die Abwasseraufbereitung und die Entsorgung von verbrauchten Elektrolyten erhöhen die Betriebskosten und den Aufwand für die Einhaltung von Vorschriften.
- Die Verwendung umweltschädlicher Stoffe, wie z. B. Elektrolyte auf Zyanidbasis, verschärft diese Probleme zusätzlich.
-
Herausforderungen bei komplizierten Geometrien
- Bei Substraten mit komplizierten Formen oder tiefen Vertiefungen ist es schwierig, gleichmäßige Beschichtungen aufzubringen.
- Abschirmungseffekte können eine angemessene Abscheidung in schwer zugänglichen Bereichen verhindern, was zu einer unvollständigen Beschichtung führt.
- Dies schränkt den Einsatz bei Anwendungen ein, die eine präzise und gleichmäßige Beschichtung auf allen Oberflächen erfordern.
-
Betriebskomplexität und Kosten
- Der Prozess erfordert eine präzise Steuerung von Parametern wie Spannung, Stromdichte, Temperatur und Elektrolytzusammensetzung.
- Um diese Bedingungen aufrechtzuerhalten, sind moderne Geräte und qualifiziertes Personal erforderlich, was die Betriebskosten erhöht.
- Die regelmäßige Wartung der Geräte und das Nachfüllen von Elektrolyten erhöhen die Kosten zusätzlich.
-
Mögliche Defekte
- Zu den häufigen Mängeln gehören Nadellöcher, Blasenbildung und schlechte Haftung, die die Qualität und Haltbarkeit der Beschichtung beeinträchtigen können.
- Diese Defekte entstehen oft durch Verunreinigungen im Elektrolyt, unsachgemäße Substratvorbereitung oder Schwankungen der Prozessparameter.
- Die Beseitigung von Fehlern kann eine Nacharbeit oder Verschrottung von Teilen erforderlich machen, was zu Materialverschwendung und höheren Kosten führt.
-
Begrenzte Abscheidungsrate
- Die elektrolytische Abscheidung ist im Allgemeinen langsamer als andere Beschichtungsmethoden wie die physikalische Gasphasenabscheidung (PVD) oder das thermische Spritzen.
- Die langsame Abscheidungsrate kann ein Engpass in der Großserienproduktion sein.
- Eine Erhöhung der Abscheidungsrate erfordert oft höhere Stromdichten, was zu Qualitätsproblemen wie Rauheit oder Porosität führen kann.
-
Abhängigkeit von der Leitfähigkeit des Substrats
- Das Substrat muss elektrisch leitfähig sein, damit das Verfahren effektiv funktioniert.
- Nichtleitende Substrate erfordern Vorbehandlungsschritte, wie das Aufbringen einer leitfähigen Schicht, was zusätzlichen Zeit- und Kostenaufwand bedeutet.
- Selbst mit Vorbehandlung kann es schwierig sein, eine gute Haftung und Gleichmäßigkeit zu erreichen.
-
Gesundheits- und Sicherheitsrisiken
- Der Einsatz von gefährlichen Chemikalien und Hochspannungsgeräten birgt Risiken für die Arbeitnehmer.
- Angemessene Sicherheitsmaßnahmen, wie Schutzkleidung und Belüftungssysteme, sind unerlässlich, erhöhen jedoch die Komplexität und die Kosten des Betriebs.
- Der versehentliche Kontakt mit giftigen Substanzen oder elektrischen Gefahren kann zu ernsthaften Gesundheits- und Sicherheitsvorfällen führen.
Wenn die Käufer von Geräten und Verbrauchsmaterialien diese Nachteile kennen, können sie fundierte Entscheidungen darüber treffen, ob die Elektroabscheidung für ihre spezifischen Anwendungen geeignet ist.In Fällen, in denen Kosten, Umweltauswirkungen oder Präzision kritische Faktoren sind, können alternative Beschichtungsmethoden besser geeignet sein.
Zusammenfassende Tabelle:
Benachteiligung | Wichtige Details |
---|---|
Eingeschränkte Materialkompatibilität | Funktioniert nur mit leitenden Materialien; nicht leitende Substrate müssen vorbehandelt werden. |
Hoher Energieverbrauch | Benötigt kontinuierlich elektrische Energie, was die Betriebskosten erhöht. |
Ungleichmäßige Beschichtungsdicke | Ungleichmäßige Ablagerung, insbesondere an Kanten und komplexen Geometrien. |
Umweltbedenken | Erzeugt giftige Nebenprodukte, die eine kostspielige Abfallentsorgung erfordern. |
Komplexe Geometrien - eine Herausforderung | Schwierigkeiten bei der gleichmäßigen Beschichtung komplizierter Formen oder tiefer Vertiefungen. |
Betriebliche Komplexität | Erfordert eine genaue Kontrolle der Parameter, was Kosten und Komplexität erhöht. |
Mögliche Defekte | Zu den Risiken gehören Nadellöcher, Blasenbildung und schlechte Haftung. |
Begrenzte Abscheidungsrate | Im Vergleich zu anderen Beschichtungsmethoden langsamer, was sich auf die Produktion großer Mengen auswirkt. |
Abhängigkeit von der Leitfähigkeit des Substrats | Nicht leitende Substrate müssen vorbehandelt werden, was Zeit und Kosten verursacht. |
Gesundheits- und Sicherheitsrisiken | Gefährliche Chemikalien und Hochspannungsgeräte, die Sicherheitsmaßnahmen erfordern. |
Benötigen Sie eine bessere Beschichtungslösung für Ihre Anwendung? Kontaktieren Sie noch heute unsere Experten um Alternativen zu erkunden!