Das Induktionshärten ist zwar wirksam zur Verbesserung der Verschleiß- und Ermüdungsbeständigkeit einfacher Werkstücke, weist jedoch mehrere Nachteile auf. Für komplexe mechanische Werkstücke ist es aufgrund der schlechten Anpassungsfähigkeit nicht geeignet, so dass seine Anwendung auf einfachere Teile in der Fließbandproduktion beschränkt ist. Darüber hinaus mangelt es dem Verfahren an Raffinationskapazität, sodass die Einsatzmaterialien frei von Oxiden und bekannter Zusammensetzung sein müssen. Auch Legierungselemente können während des Prozesses durch Oxidation verloren gehen und müssen daher erneut der Schmelze zugesetzt werden. Diese Einschränkungen machen die Induktionshärtung weniger vielseitig und in bestimmten Fertigungsszenarien schwieriger zu handhaben.
Wichtige Punkte erklärt:
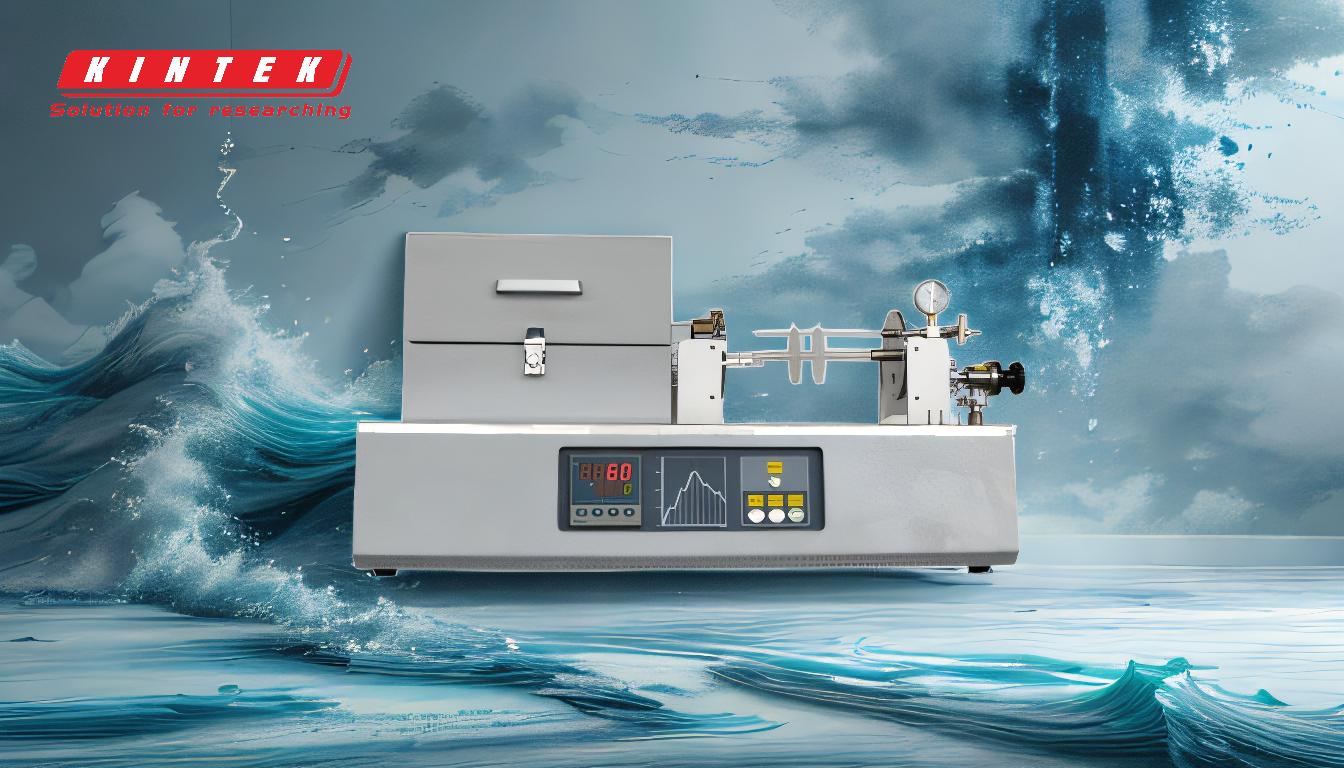
-
Schlechte Anpassungsfähigkeit für komplexe Werkstücke:
- Das Induktionshärten eignet sich vor allem für einfache Werkstücke, wie sie beispielsweise in der Fließbandfertigung zum Einsatz kommen. Aufgrund seiner begrenzten Anpassungsfähigkeit hat es jedoch Probleme mit komplexen mechanischen Teilen. Der Prozess erfordert eine präzise Steuerung des Heizens und Kühlens, was bei komplizierten Geometrien schwierig zu erreichen sein kann. Diese Einschränkung beschränkt die Verwendung auf einfachere Komponenten und verringert so die Vielseitigkeit bei der Herstellung.
-
Mangel an Raffinationskapazität:
- Im Gegensatz zu anderen Härteverfahren erfolgt beim Induktionshärten keine Veredelung des Materials. Das bedeutet, dass die eingesetzten Einsatzstoffe bereits oxidfrei sein und eine bekannte Zusammensetzung haben müssen. Jegliche Verunreinigungen oder Inkonsistenzen im Material können zu suboptimalen Ergebnissen führen, wodurch der Prozess weniger fehlerverzeihend und abhängiger von hochwertigen Eingangsmaterialien wird.
-
Verlust von Legierungselementen:
- Während des Induktionshärtungsprozesses können einige Legierungselemente durch Oxidation verloren gehen. Dadurch können sich die Materialeigenschaften verändern und die Wirksamkeit des Härtungsprozesses verringern. Um dem entgegenzuwirken, müssen Hersteller diese Elemente möglicherweise erneut der Schmelze hinzufügen, was den Prozess komplexer und teurer macht. Dieses Problem ist besonders problematisch, wenn mit Materialien gearbeitet wird, die für eine optimale Leistung präzise Legierungszusammensetzungen erfordern.
-
Begrenzter Anwendungsbereich:
- Die Einschränkungen der Technologie bei der Handhabung komplexer Formen und die Abhängigkeit von hochwertigen Ausgangsmaterialien schränken ihren Anwendungsbereich ein. Es eignet sich am besten für die Massenproduktion einfacher Teile, bei denen die Vorteile einer verbesserten Verschleiß- und Ermüdungsbeständigkeit maximiert werden können. Für speziellere oder kompliziertere Anwendungen können jedoch andere Härtungsmethoden besser geeignet sein.
-
Herausforderungen in der Prozesssteuerung:
- Um beim Induktionshärten konsistente Ergebnisse zu erzielen, ist eine präzise Steuerung der Heiz- und Abkühlraten erforderlich. Abweichungen können zu einer ungleichmäßigen Aushärtung führen und die Effektivität des Prozesses verringern. Diese Notwendigkeit einer strengen Kontrolle kann die Komplexität des Herstellungsprozesses erhöhen und anspruchsvollere Ausrüstung und Fachwissen erfordern.
Zusammenfassend lässt sich sagen, dass die Induktionshärtung zwar erhebliche Vorteile hinsichtlich der Verschleiß- und Ermüdungsbeständigkeit einfacher Werkstücke bietet, ihre Nachteile – wie schlechte Anpassungsfähigkeit an komplexe Teile, mangelnde Veredelungskapazität und potenzieller Verlust von Legierungselementen – jedoch ihre breitere Anwendung einschränken. Diese Faktoren machen es für bestimmte Fertigungsszenarien weniger geeignet, insbesondere für solche mit komplizierten Geometrien oder speziellen Materialien.
Übersichtstabelle:
Nachteil | Beschreibung |
---|---|
Schlechte Anpassungsfähigkeit für komplexe Teile | Begrenzte Wirksamkeit bei komplizierten Geometrien, wodurch die Verwendung auf einfachere Komponenten beschränkt ist. |
Mangel an Raffinationskapazität | Erfordert hochwertige, oxidfreie Materialien; Keine Raffinierung während des Prozesses. |
Verlust von Legierungselementen | Oxidation während des Härtens kann zum Verlust von Legierungselementen führen, die eine erneute Zugabe erforderlich machen. |
Begrenzter Anwendungsbereich | Bestens geeignet für die Massenproduktion einfacher Teile; bei Spezialmaterialien weniger effektiv. |
Herausforderungen in der Prozesssteuerung | Erfordert eine präzise Steuerung der Heiz- und Kühlraten für konsistente Ergebnisse. |
Benötigen Sie eine auf Ihre Bedürfnisse zugeschnittene Härtelösung? Kontaktieren Sie uns noch heute Alternativen erkunden!