Obwohl das Induktionslöten in vielen industriellen Anwendungen vorteilhaft ist, weist es mehrere bemerkenswerte Nachteile auf. Dazu gehören hohe Anschaffungskosten, Komplexität im Betrieb, Materialbeschränkungen und Herausforderungen im Zusammenhang mit der Verfeinerung und Aufrechterhaltung der Materialzusammensetzung. Im Folgenden gehen wir detailliert auf diese Nachteile ein und vermitteln ein umfassendes Verständnis der mit dem Induktionslöten verbundenen Einschränkungen.
Wichtige Punkte erklärt:
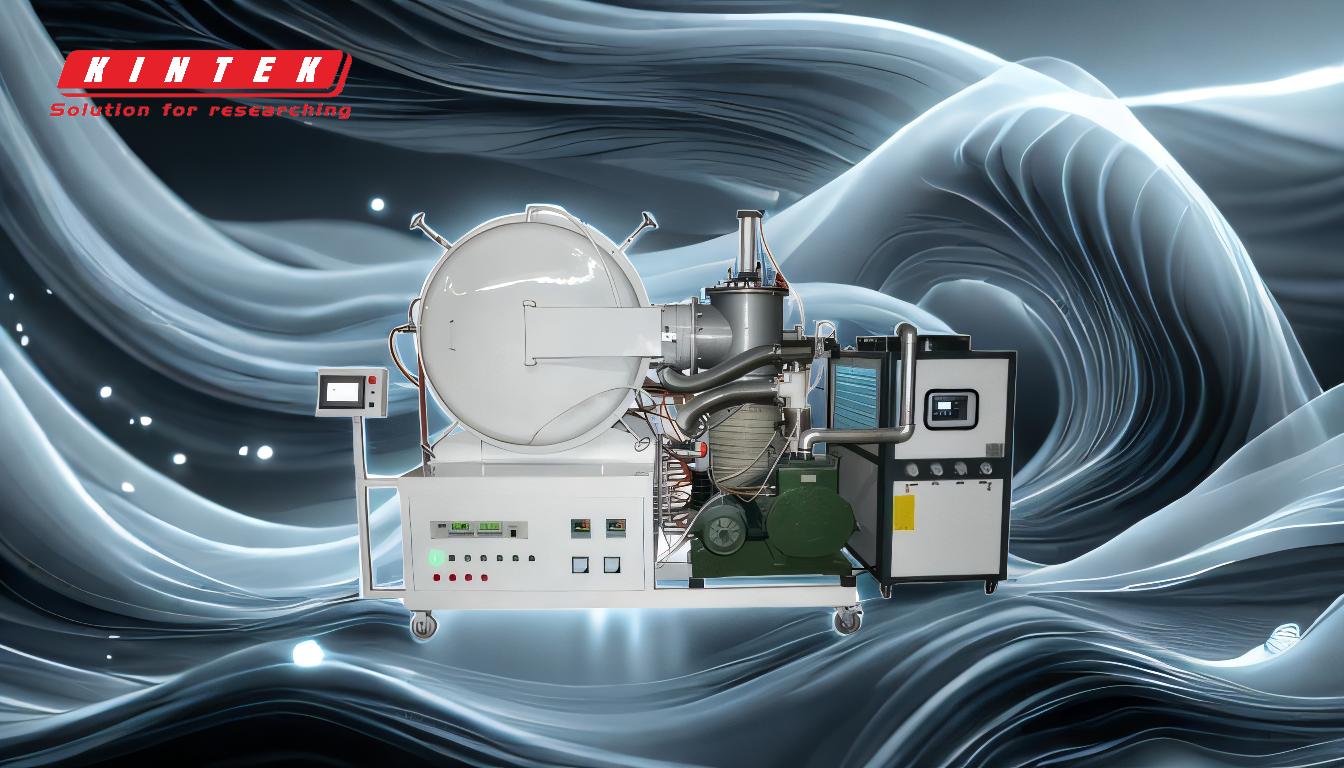
-
Hohe Anschaffungskosten
- Induktionslötgeräte sind im Vergleich zu herkömmlichen Lötmethoden deutlich teurer.
- Die Kosten umfassen nicht nur die Maschine selbst, sondern auch die dazugehörige Infrastruktur, wie etwa Netzteile und Kühlsysteme.
- Für kleine Betriebe oder Unternehmen mit begrenzten Budgets können diese hohen Vorabinvestitionen ein großes Hindernis für die Einführung darstellen.
-
Komplexer Prozess und Betrieb
- Für einen effektiven Betrieb sind beim Induktionslöten spezielle Kenntnisse und Schulungen erforderlich.
- Der Prozess erfordert eine präzise Steuerung von Parametern wie Frequenz, Leistung und Heizzeit, was für unerfahrene Bediener eine Herausforderung sein kann.
- Die Wartung der Ausrüstung erfordert auch technisches Fachwissen, was die betriebliche Komplexität erhöht.
-
Materialbeschränkungen
- Induktionslöten ist nicht für alle Materialien geeignet. Es funktioniert am besten mit leitfähigen Metallen wie Kupfer, Messing und Stahl.
- Nicht leitende Materialien oder solche mit schlechter Wärmeleitfähigkeit erwärmen sich möglicherweise nicht gleichmäßig oder effizient, was zu inkonsistenten Ergebnissen führt.
- Bestimmte Materialien können sich unter den hohen Temperaturen, die durch Induktionserwärmung entstehen, auch zersetzen oder oxidieren.
-
Mangel an Raffinationskapazität
- Beim Induktionslöten können Materialien während des Prozesses nicht verfeinert oder gereinigt werden.
- Die verwendeten Materialien müssen zuvor frei von Oxiden und Verunreinigungen sein, da diese die Qualität der Lötverbindung negativ beeinflussen können.
- Diese Einschränkung erfordert zusätzliche Vorverarbeitungsschritte, was Zeit und Kosten erhöht.
-
Oxidation und Verlust von Legierungselementen
- Hohe Temperaturen beim Induktionslöten können zur Oxidation bestimmter Materialien führen, insbesondere solcher mit reaktiven Legierungselementen.
- Oxidation kann zum Verlust kritischer Legierungselemente führen, die möglicherweise erneut hinzugefügt werden müssen, um die gewünschten Materialeigenschaften aufrechtzuerhalten.
- Dieses Problem kann die Integrität und Leistung des Endprodukts beeinträchtigen.
-
Energieverbrauch und Effizienz
- Induktionslötanlagen können energieintensiv sein, insbesondere wenn sie mit hohen Frequenzen oder Leistungsniveaus betrieben werden.
- Während die Induktionserwärmung im Allgemeinen effizient ist, kann der Gesamtenergieverbrauch im Vergleich zu anderen Lötmethoden je nach Anwendung dennoch höher sein.
-
Begrenzte Flexibilität für kleine oder komplexe Teile
- Induktionslöten ist bei kleinen, komplizierten oder unregelmäßig geformten Teilen weniger effektiv, da es schwierig ist, eine gleichmäßige Erwärmung zu erreichen.
- Für bestimmte Anwendungen können kundenspezifische Spulendesigns erforderlich sein, was die Komplexität und die Kosten erhöht.
-
Sicherheitsbedenken
- Die beim Induktionslöten entstehenden hohen Temperaturen und elektromagnetischen Felder stellen ein Sicherheitsrisiko für das Bedienpersonal dar.
- Um diese Risiken zu mindern, sind geeignete Sicherheitsmaßnahmen wie Abschirmungen und Schutzausrüstung erforderlich.
Zusammenfassend lässt sich sagen, dass das Induktionslöten zwar Vorteile wie Geschwindigkeit, Präzision und lokale Erwärmung bietet, seine Nachteile – einschließlich hoher Kosten, Materialbeschränkungen und betrieblicher Komplexität – jedoch sorgfältig abgewogen werden müssen. Diese Faktoren machen es für bestimmte Anwendungen oder Unternehmen mit begrenzten Ressourcen weniger geeignet. Das Verständnis dieser Einschränkungen ist entscheidend, um fundierte Entscheidungen darüber treffen zu können, ob Induktionslöten für einen bestimmten Anwendungsfall die richtige Wahl ist.
Übersichtstabelle:
Nachteil | Einzelheiten |
---|---|
Hohe Anschaffungskosten | Teure Ausrüstung und Infrastruktur; Barriere für Kleinbetriebe. |
Komplexer Prozess und Betrieb | Erfordert spezielle Schulung und präzise Parameterkontrolle. |
Materialbeschränkungen | Am besten für leitfähige Metalle geeignet; Herausforderungen mit nichtleitenden Materialien. |
Mangel an Raffinationskapazität | Keine Materialreinigung während des Prozesses; Vorbearbeitung erforderlich. |
Oxidations- und Legierungsverlust | Hohe Temperaturen führen zu Oxidation und Verlust kritischer Legierungselemente. |
Energieverbrauch | Kann besonders bei hohen Frequenzen energieintensiv sein. |
Begrenzte Flexibilität | Weniger effektiv bei kleinen oder komplexen Teilen; Möglicherweise sind kundenspezifische Spulen erforderlich. |
Sicherheitsbedenken | Hohe Temperaturen und elektromagnetische Felder stellen eine Gefahr für den Bediener dar. |
Benötigen Sie Hilfe bei der Entscheidung, ob Induktionslöten für Ihre Anwendung geeignet ist? Kontaktieren Sie noch heute unsere Experten für persönliche Beratung!