Die Abscheidung von Dünnschichten ist ein wichtiger Prozess in verschiedenen Branchen, darunter Elektronik, Optik und Beschichtungen. Es ist jedoch mit einigen Nachteilen und Herausforderungen verbunden, die die Qualität, Leistung und Skalierbarkeit des Endprodukts beeinträchtigen können. Zu diesen Herausforderungen gehören Probleme in Bezug auf Gleichmäßigkeit, Haftung, Verunreinigung, Substratkompatibilität, Stressmanagement, Reinheit und Kosteneffizienz. Darüber hinaus erschweren Temperaturbeschränkungen während der Abscheidung und Kühlung sowie die Schwierigkeit, eine gleichmäßige Dicke und Reinheit zu erreichen, den Prozess zusätzlich. Die Behebung dieser Nachteile erfordert eine sorgfältige Optimierung und fortschrittliche Techniken, um die gewünschten Schichteigenschaften und Leistungen zu gewährleisten.
Die wichtigsten Punkte werden erklärt:
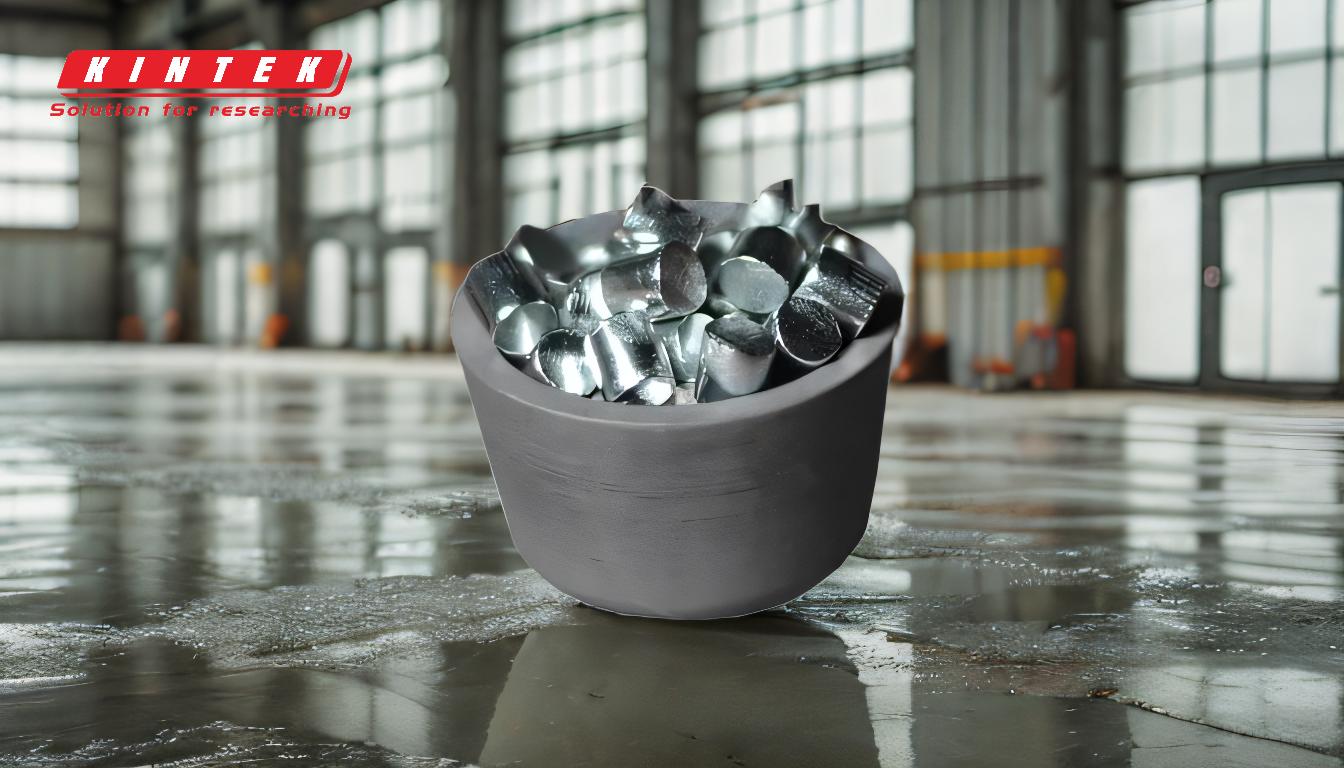
-
Kontrolle der Gleichmäßigkeit und der Schichtdicke:
- Das Erreichen einer gleichmäßigen Schichtdicke über das gesamte Substrat ist eine große Herausforderung bei der Abscheidung dünner Schichten. Eine ungleichmäßige Schichtdicke kann zu Schwankungen der Schichteigenschaften führen, die die Leistung bei Anwendungen wie Elektronik und Optik beeinträchtigen.
- Zu den Faktoren, die zur Ungleichmäßigkeit beitragen, gehören ungleichmäßige Abscheidungsraten, Unregelmäßigkeiten auf der Substratoberfläche und Schwankungen der Temperatur oder des Gasflusses während des Abscheidungsprozesses.
- Fortgeschrittene Techniken wie die Atomlagenabscheidung (ALD) und eine verbesserte Prozesssteuerung können diese Probleme abmildern, sind aber oft mit höheren Kosten verbunden.
-
Adhäsion und Delamination:
- Die ordnungsgemäße Haftung zwischen der dünnen Folie und dem Substrat ist entscheidend für die Haltbarkeit und Funktionalität der Beschichtung. Eine schlechte Haftung kann zu einer Delamination führen, bei der sich die Folie vom Substrat ablöst.
- Delamination wird oft durch unterschiedliche Wärmeausdehnungskoeffizienten, Oberflächenverschmutzung oder unzureichende Oberflächenvorbereitung verursacht.
- Zu den Lösungen gehören Oberflächenbehandlungen wie die Plasmareinigung oder die Verwendung von haftungsfördernden Schichten, um die Haftung zwischen Folie und Substrat zu verbessern.
-
Kontamination und Reinheit:
- Verunreinigungen während des Abscheidungsprozesses können die Qualität der Dünnschicht erheblich beeinträchtigen. Verunreinigungen können die elektrischen, optischen oder mechanischen Eigenschaften der Schicht verändern.
- Zu den Verunreinigungsquellen gehören Restgase in der Abscheidekammer, Partikel vom Substrat oder Verunreinigungen im Abscheidungsmaterial.
- Die Aufrechterhaltung eines hohen Reinheitsgrades, die Verwendung ultrahochreiner Materialien und die Durchführung strenger Prozesskontrollen sind für die Minimierung von Verunreinigungen unerlässlich.
-
Kompatibilität der Substrate:
- Die Wahl des Substratmaterials ist von entscheidender Bedeutung, da es mit dem Abscheideverfahren und dem Filmmaterial kompatibel sein muss. Inkompatibilität kann zu Problemen wie schlechter Haftung, spannungsbedingter Rissbildung oder chemischen Reaktionen zwischen Folie und Substrat führen.
- So sind beispielsweise Hochtemperatur-Beschichtungsverfahren für Substrate mit geringer thermischer Stabilität möglicherweise nicht geeignet.
- Um die Kompatibilität zu gewährleisten und die gewünschten Schichteigenschaften zu erreichen, ist eine sorgfältige Auswahl der Substratmaterialien und der Abscheidungsbedingungen erforderlich.
-
Stress- und Belastungsmanagement:
- Bei dünnen Schichten treten häufig innere Spannungen auf, die auf die unterschiedlichen Wärmeausdehnungskoeffizienten von Schicht und Substrat oder auf den Abscheidungsprozess selbst zurückzuführen sind. Diese Spannungen können zu Rissen, Knicken oder Delaminationen in der Folie führen.
- Zu den Techniken des Spannungsmanagements gehören die Optimierung von Abscheidungsparametern wie Temperatur und Druck sowie der Einsatz von Entspannungsschichten oder Glühverfahren zur Reduzierung von Eigenspannungen.
- Diese Techniken können jedoch die Komplexität und die Kosten des Abscheidungsprozesses erhöhen.
-
Temperatur-Einschränkungen:
- Viele Verfahren zur Abscheidung von Dünnschichten erfordern hohe Temperaturen, was die Auswahl der Substratmaterialien einschränken und das Risiko thermischer Schäden erhöhen kann.
- So sind beispielsweise Hochtemperaturverfahren für Polymere oder andere temperaturempfindliche Materialien möglicherweise nicht geeignet.
- Niedertemperatur-Beschichtungsverfahren, wie die plasmaunterstützte chemische Gasphasenabscheidung (PECVD), können als Alternative eingesetzt werden, haben aber möglicherweise Einschränkungen in Bezug auf die Schichtqualität und die Abscheidungsrate.
-
Kühlungsinduzierte Spannungen:
- Während der Abkühlungsphase nach der Abscheidung können unerwünschte Spannungen in der dünnen Schicht aufgrund von Unterschieden in der thermischen Kontraktion zwischen der Schicht und dem Substrat entstehen.
- Diese Spannungen können zu Defekten wie Rissen oder Delaminationen führen, die die Integrität der Folie beeinträchtigen.
- Eine allmähliche Abkühlung oder ein Glühen nach der Abscheidung kann dazu beitragen, diese Spannungen abzumildern, aber diese Schritte erhöhen den Zeitaufwand und die Komplexität des Prozesses.
-
Kosten und Skalierbarkeit:
- Dünnschichtabscheidungsverfahren können teuer sein, insbesondere wenn fortschrittliche Techniken oder hochreine Materialien erforderlich sind. Die Kosten für die Ausrüstung, die Wartung und die Prozessoptimierung können ein erhebliches Hindernis darstellen, insbesondere für die Produktion in großem Maßstab.
- Eine weitere Herausforderung ist die Vergrößerung des Abscheidungsprozesses bei gleichbleibender Schichtqualität. Schwankungen bei den Abscheidungsbedingungen, wie Temperatur oder Gasfluss, können bei größeren Maßstäben deutlicher werden und zu Ungleichmäßigkeiten oder Defekten führen.
- Das Gleichgewicht zwischen Kosten und Skalierbarkeit erfordert eine sorgfältige Optimierung der Abscheidungsparameter und die Verwendung kosteneffizienter Materialien und Techniken, ohne die Filmqualität zu beeinträchtigen.
Zusammenfassend lässt sich sagen, dass die Dünnschichtabscheidung zwar eine leistungsstarke Technologie mit breit gefächerten Anwendungsmöglichkeiten ist, aber auch mit einigen Herausforderungen verbunden ist. Die Bewältigung von Problemen im Zusammenhang mit Gleichmäßigkeit, Haftung, Verunreinigung, Substratkompatibilität, Stressmanagement und Kosteneffizienz ist für die Herstellung hochwertiger Schichten, die den Anforderungen moderner Anwendungen gerecht werden, unerlässlich. Fortgeschrittene Techniken und eine sorgfältige Prozessoptimierung können helfen, diese Nachteile zu überwinden, sind aber oft mit einem höheren Aufwand und höheren Kosten verbunden.
Zusammenfassende Tabelle:
Herausforderung | Beschreibung | Lösung |
---|---|---|
Gleichmäßigkeit & Dicke | Eine ungleichmäßige Dicke beeinträchtigt die Leistung der Folie. | Einsatz fortschrittlicher Techniken wie ALD und verbesserte Prozesskontrolle. |
Adhäsion und Delamination | Schlechte Haftung führt zum Ablösen der Folie. | Aufbringen von Oberflächenbehandlungen (z. B. Plasmareinigung) oder haftungsfördernden Schichten. |
Kontamination und Reinheit | Verunreinigungen verschlechtern die Filmqualität. | Sauberkeit, Verwendung ultrahochreiner Materialien und strenge Kontrollen. |
Kompatibilität der Substrate | Unverträgliche Substrate führen zu schlechter Haftung oder Rissbildung. | Wählen Sie kompatible Materialien und optimieren Sie die Ablagerungsbedingungen. |
Stress und Dehnung | Innere Spannungen führen zu Rissbildung oder Delamination. | Optimieren Sie die Abscheidungsparameter und verwenden Sie spannungsabbauende Schichten oder Glühvorgänge. |
Temperatur-Einschränkungen | Hohe Temperaturen schränken die Substratoptionen ein. | Verwenden Sie Niedertemperaturtechniken wie PECVD. |
Kühlungsinduzierte Spannungen | Spannungen während der Abkühlung verursachen Fehler. | Führen Sie eine allmähliche Abkühlung oder ein Glühen nach der Abscheidung durch. |
Kosten & Skalierbarkeit | Hohe Kosten und Skalierungsprobleme beeinträchtigen die Produktion in großem Maßstab. | Optimieren Sie die Parameter und verwenden Sie kostengünstige Materialien, ohne die Qualität zu beeinträchtigen. |
Benötigen Sie Hilfe bei der Bewältigung der Herausforderungen bei der Dünnschichtabscheidung? Kontaktieren Sie unsere Experten noch heute für maßgeschneiderte Lösungen!