Wärmebehandlungsvorgänge sind für die Veränderung der mechanischen, physikalischen und chemischen Eigenschaften von Materialien von entscheidender Bedeutung, aber sie sind anfällig für Fehler, wenn sie nicht ordnungsgemäß durchgeführt werden. Diese Ausfälle können auf unsachgemäße Oberflächenvorbereitung, falsche Temperaturkontrolle, unzureichende Abkühlraten oder Verunreinigungen während des Prozesses zurückzuführen sein. Solche Probleme können zu Mängeln wie Abblättern der Beschichtung, Blasenbildung, Lochfraß oder Verfärbung sowie zu strukturellen Schwächen, verringerter Haltbarkeit oder inkonsistenten Materialeigenschaften führen. Um die Qualität und Zuverlässigkeit wärmebehandelter Komponenten sicherzustellen, ist es wichtig, die häufigsten Fehler und ihre Ursachen zu verstehen.
Wichtige Punkte erklärt:
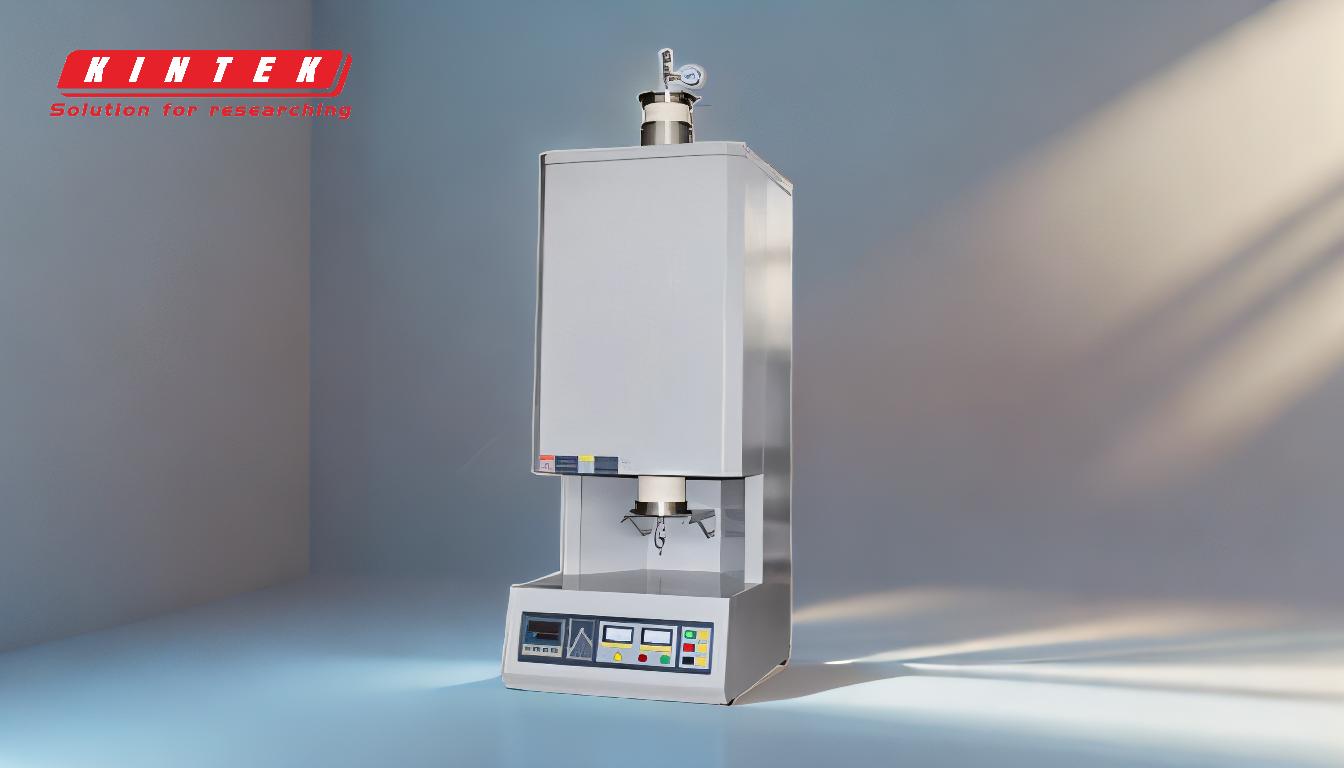
-
Unsachgemäße Oberflächenvorbereitung:
- Ausgabe: Eine unzureichende Oberflächenvorbereitung vor der Wärmebehandlung kann zu Beschichtungsfehlern wie Abblättern, Blasenbildung, Lochfraß und Farbveränderungen führen.
- Ursache: Raue oder unbehandelte Oberflächen verhindern die Bildung starker, gleichmäßiger und korrosionsbeständiger Beschichtungen.
- Lösung: Sorgen Sie vor der Wärmebehandlung für eine gründliche Reinigung, Politur und Oberflächenveredelung, um eine optimale Haftung und Beschichtungsqualität zu erreichen.
-
Fehler bei der Temperaturregelung:
- Ausgabe: Falsche Temperatureinstellungen oder Schwankungen während der Wärmebehandlung können zu inkonsistenten Materialeigenschaften führen.
- Ursache: Überhitzung oder Unterhitzung kann zu fehlerhaften Phasenumwandlungen führen, was zu weichen Stellen, Sprödigkeit oder ungleichmäßiger Härte führt.
- Lösung: Verwenden Sie präzise Temperaturkontrollsysteme und kalibrieren Sie die Geräte regelmäßig, um konstante Heizbedingungen aufrechtzuerhalten.
-
Missmanagement der Kühlrate:
- Ausgabe: Falsche Abkühlraten können zu thermischen Spannungen, Verformungen oder Rissen im Material führen.
- Ursache: Schnelles Abkühlen (Abschrecken) oder langsames Abkühlen (Glühen) müssen sorgfältig kontrolliert werden, um die gewünschte Mikrostruktur und die gewünschten mechanischen Eigenschaften zu erreichen.
- Lösung: Wählen Sie geeignete Kühlmedien (z. B. Öl, Wasser, Luft) und überwachen Sie die Kühlraten, um Defekte zu vermeiden.
-
Kontamination während der Wärmebehandlung:
- Ausgabe: Verunreinigungen wie Öl, Fett oder Oxide auf der Materialoberfläche können zu Oberflächenfehlern oder ungleichmäßiger Wärmeverteilung führen.
- Ursache: Verunreinigungen beeinträchtigen den Wärmeübertragungsprozess und können zu örtlicher Überhitzung oder Unterhitzung führen.
- Lösung: Reinigen Sie das Material vor der Wärmebehandlung gründlich und sorgen Sie für eine kontrollierte Atmosphäre (z. B. Inertgas oder Vakuum), um eine Kontamination zu verhindern.
-
Inkonsistente Materialeigenschaften:
- Ausgabe: Aufgrund einer ungleichmäßigen Wärmebehandlung können im gesamten Material Schwankungen in der Härte, Festigkeit oder Duktilität auftreten.
- Ursache: Ungleichmäßiges Erhitzen oder Abkühlen kann zu inkonsistenten Phasenumwandlungen und mechanischen Eigenschaften führen.
- Lösung: Verwenden Sie gleichmäßige Heizmethoden (z. B. Induktionserwärmung) und sorgen Sie für eine gleichmäßige Kühlung, um konsistente Ergebnisse zu erzielen.
-
Fehler beim Stressabbau:
- Ausgabe: Eine unsachgemäße Spannungsentlastung kann Restspannungen im Material hinterlassen, die zu Verformungen oder Rissen während der Bearbeitung oder des Gebrauchs führen.
- Ursache: Eine unzureichende Erwärmung oder Kühlung während des Spannungsabbauprozesses kann dazu führen, dass interne Spannungen nicht beseitigt werden.
- Lösung: Befolgen Sie genaue Protokolle zum Spannungsabbau, einschließlich ordnungsgemäßem Erhitzen und langsamem Abkühlen, um Restspannungen zu minimieren.
-
Fehler bei der Einsatzhärtung:
- Ausgabe: Bei Einsatzhärtungsprozessen wie Aufkohlen oder Nitrieren kann eine ungleichmäßige Einsatztiefe oder Oberflächenhärte auftreten.
- Ursache: Eine ungleichmäßige Kohlenstoff- oder Stickstoffdiffusion kann durch unsachgemäße Temperaturkontrolle oder unzureichende Prozesszeit verursacht werden.
- Lösung: Überwachen und steuern Sie den Diffusionsprozess sorgfältig, um eine gleichmäßige Einsatztiefe und Härte zu erreichen.
-
Glühfehler:
- Ausgabe: Unsachgemäßes Glühen kann zu einer übermäßigen Erweichung oder einem unzureichenden Spannungsabbau im Material führen.
- Ursache: Falsche Glühtemperaturen oder Abkühlraten können dazu führen, dass die gewünschte Mikrostruktur nicht erreicht wird.
- Lösung: Befolgen Sie die spezifischen Glührichtlinien für das Material und die Anwendung, um eine ordnungsgemäße Erweichung und Spannungsentlastung sicherzustellen.
Durch die Behebung dieser häufigen Fehler und die Implementierung bewährter Verfahren können Hersteller die Qualität und Zuverlässigkeit wärmebehandelter Komponenten verbessern und sicherstellen, dass sie die erforderlichen Leistungsstandards erfüllen.
Übersichtstabelle:
Fehlertyp | Ausgabe | Ursache | Lösung |
---|---|---|---|
Unsachgemäße Oberflächenvorbereitung | Beschichtungsfehler (Abblättern, Blasenbildung, Lochfraß, Verfärbung) | Raue oder unbehandelte Oberflächen | Gründliche Reinigung, Politur und Oberflächenveredelung |
Fehler bei der Temperaturregelung | Inkonsistente Materialeigenschaften | Überhitzung oder Unterhitzung | Verwenden Sie präzise Temperaturkontrollsysteme und kalibrieren Sie Geräte |
Missmanagement der Kühlrate | Thermische Spannungen, Verformungen oder Risse | Falsche Kühlraten | Wählen Sie geeignete Kühlmedien aus und überwachen Sie die Kühlraten |
Kontamination | Oberflächenfehler oder ungleichmäßige Wärmeverteilung | Öl, Fett oder Oxide auf der Materialoberfläche | Gründlich reinigen und eine kontrollierte Atmosphäre verwenden |
Inkonsistente Materialeigenschaften | Variationen in Härte, Festigkeit oder Duktilität | Ungleichmäßige Erwärmung oder Abkühlung | Verwenden Sie gleichmäßige Heizmethoden und sorgen Sie für eine gleichmäßige Kühlung |
Fehler beim Stressabbau | Eigenspannungen, die zu Verformungen oder Rissen führen | Unzureichende Erwärmung oder Kühlung während des Stressabbaus | Befolgen Sie genaue Stressabbauprotokolle mit ordnungsgemäßem Erhitzen und langsamem Abkühlen |
Fehler bei der Einsatzhärtung | Inkonsistente Härtetiefe oder Oberflächenhärte | Ungleichmäßige Kohlenstoff- oder Stickstoffdiffusion | Überwachen und steuern Sie den Diffusionsprozess sorgfältig |
Glühfehler | Übermäßige Erweichung oder unzureichender Spannungsabbau | Falsche Glühtemperaturen oder Abkühlraten | Befolgen Sie bestimmte Glührichtlinien |
Stellen Sie sicher, dass Ihre Wärmebehandlungsprozesse einwandfrei sind – Kontaktieren Sie noch heute unsere Experten für maßgeschneiderte Lösungen!