Magnetronsputtern ist eine weit verbreitete Technik bei der Dünnschichtabscheidung und bietet Vorteile wie hohe Abscheidungsraten, präzise Steuerung und Vielseitigkeit. Allerdings steht es auch vor mehreren Herausforderungen, darunter Einschränkungen bei der effektiven Beschichtungsfläche, schlechte Haftfestigkeit, hohe Systemkosten und Probleme mit der Gleichmäßigkeit der Abscheidung und der Substraterwärmung. Diese Probleme können die Qualität und Anwendbarkeit der hergestellten Filme beeinträchtigen, insbesondere für großflächige oder temperaturempfindliche Anwendungen. Trotz dieser Herausforderungen wird die Technik durch laufende Forschung und Fortschritte weiter verbessert, sodass sie für ein breites Spektrum von Anwendungen in der Mikroelektronik, Halbleitern und dekorativen Beschichtungen geeignet ist.
Wichtige Punkte erklärt:
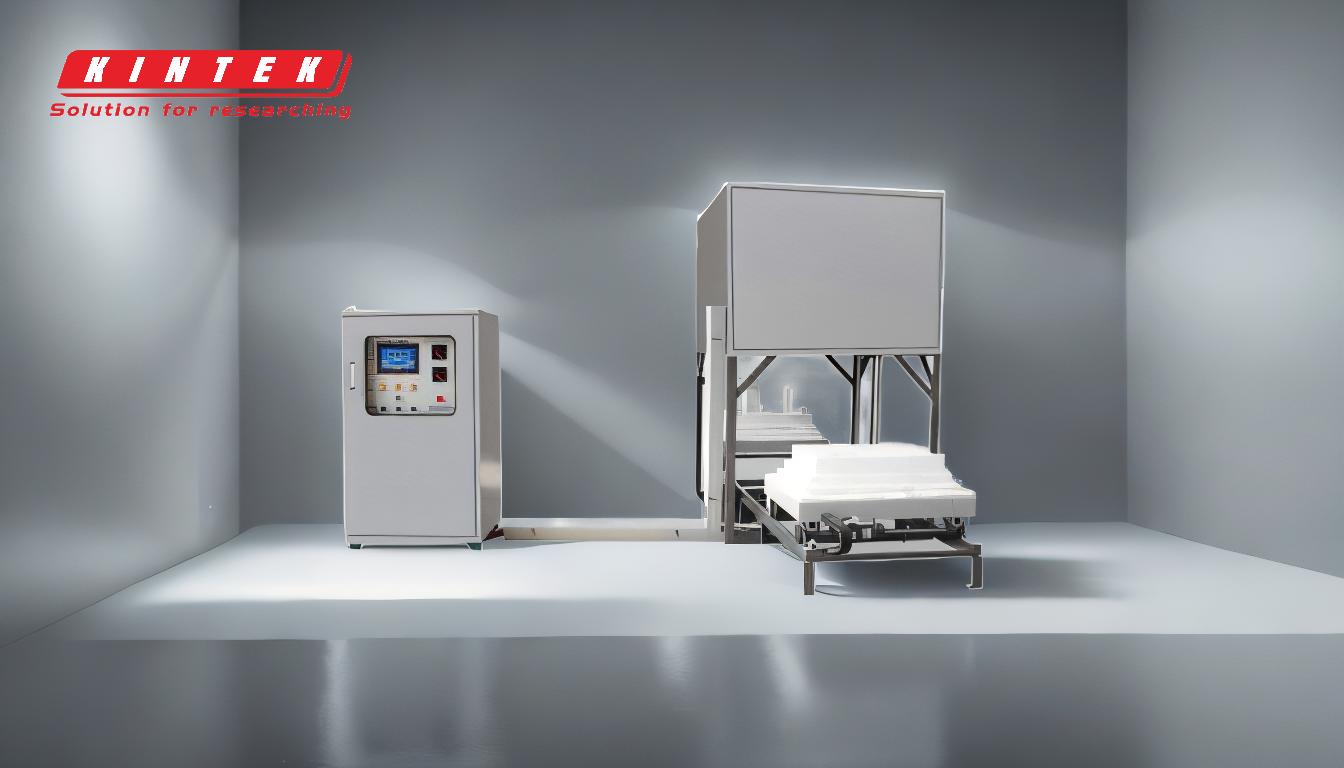
-
Begrenzte effektive Beschichtungsfläche:
- Die effektive Beschichtungsfläche beim Balanced-Magnetron-Sputtern ist relativ klein, was die geometrische Größe der Werkstücke, die plattiert werden können, einschränkt. Ab einer Entfernung von 60 mm von der Zieloberfläche nimmt die Plasmakonzentration schnell ab, was die Platzierung von Werkstücken einschränkt. Bei großflächigen Anwendungen oder der Beschichtung komplexer Geometrien kann dies ein erheblicher Nachteil sein.
-
Schlechte Haftfestigkeit und Filmqualität:
- Die Energie der fliegenden Targetpartikel beim Magnetronsputtern ist oft niedrig, was zu einer schlechten Bindungsfestigkeit zwischen der Folie und dem Substrat führt. Dies kann zur Bildung poröser und rauer Säulenstrukturen führen, die die mechanischen und funktionellen Eigenschaften der Folie beeinträchtigen können. Eine Erhöhung der Werkstücktemperatur kann die Filmeigenschaften verbessern, dieser Ansatz ist jedoch für Materialien, die hohen Temperaturen nicht standhalten können, nicht durchführbar.
-
Hohe Systemkosten und Komplexität:
- Magnetron-Sputtersysteme sind im Allgemeinen teuer und komplex im Betrieb. Die hohen Anfangsinvestitions- und Wartungskosten können ein Hindernis für kleinere Betriebe oder Forschungseinrichtungen darstellen. Darüber hinaus erfordert die Komplexität des Systems qualifiziertes Personal für den Betrieb und die Fehlerbehebung.
-
Probleme mit der Substraterwärmung:
- Der Prozess kann aufgrund des energiereichen Targetmaterials zu einer erheblichen Erwärmung des Substrats führen. Dies kann bei temperaturempfindlichen Materialien oder Anwendungen, bei denen eine präzise Temperaturregelung erforderlich ist, problematisch sein. Die Erwärmung des Substrats kann auch zu thermischer Belastung und Verformung führen, was die Qualität des abgeschiedenen Films beeinträchtigt.
-
Abscheidungsrate und Direktionalität:
- Während das Magnetronsputtern bei vielen Materialien hohe Abscheidungsraten bietet, kann es bei Dielektrika, die möglicherweise niedrigere Abscheidungsraten aufweisen, weniger effektiv sein. Darüber hinaus weist die Technik oft den Nachteil einer geringen Direktionalität auf, die zwar durch die Systemgeometrie verbessert werden kann, jedoch weiterhin eine Herausforderung für die Erzielung gleichmäßiger Beschichtungen auf komplexen oder dreidimensionalen Substraten darstellt.
-
Homogenität und großflächige Anwendbarkeit:
- Das Erreichen einer Homogenität des abgeschiedenen Films kann insbesondere bei großen Oberflächen eine Herausforderung darstellen. Bei dieser Technik kann es schwierig sein, eine gleichmäßige Dicke und Zusammensetzung über das gesamte Substrat hinweg zu gewährleisten, was für Anwendungen, die konsistente Filmeigenschaften erfordern, von entscheidender Bedeutung ist. Diese Einschränkung macht das Magnetronsputtern für bestimmte großtechnische oder hochpräzise Anwendungen weniger geeignet.
-
Hochtemperatur-Nachbeschichtungsprozesse:
- Einige Anwendungen erfordern Hochtemperaturprozesse nach der Beschichtung, um die Filmeigenschaften wie Haftung und Dichte zu verbessern. Allerdings können diese Hochtemperaturbehandlungen für hitzeempfindliche Materialien oder für Anwendungen, bei denen das Wärmebudget eine Rolle spielt, von Nachteil sein.
-
Vorteile und laufende Verbesserungen:
- Trotz dieser Herausforderungen bleibt das Magnetronsputtern eine hocheffiziente und vielseitige Technik. Es bietet hohe Abscheidungsraten, eine gründliche Materialabdeckung, eine hohe Reinheit der Filme und die Möglichkeit, bei niedrigen Temperaturen zu arbeiten. Kontinuierliche Forschung und technologische Fortschritte beseitigen weiterhin viele dieser Einschränkungen und machen es zu einem wertvollen Werkzeug für die Dünnschichtvorbereitung in verschiedenen Branchen.
Zusammenfassend lässt sich sagen, dass Magnetronsputtern zwar eine leistungsstarke und vielseitige Technik zur Dünnschichtabscheidung ist, aber nicht ohne Herausforderungen. Das Verständnis dieser Einschränkungen ist entscheidend für die Optimierung des Prozesses und die Ausweitung seiner Anwendbarkeit auf ein breiteres Spektrum von Materialien und Anwendungen.
Übersichtstabelle:
Herausforderung | Beschreibung |
---|---|
Begrenzte effektive Beschichtungsfläche | Die Plasmakonzentration nimmt über 60 mm ab, was großtechnische Anwendungen einschränkt. |
Schlechte Haftfestigkeit | Eine niedrige Energie der Zielpartikel führt zu porösen, rauen Filmen mit schwacher Haftung. |
Hohe Systemkosten und Komplexität | Teure Anfangsinvestition und Wartung; erfordert qualifiziertes Personal. |
Probleme mit der Substraterwärmung | Energetisches Targetmaterial führt zu einer Erwärmung, was für temperaturempfindliche Materialien problematisch ist. |
Abscheidungsrate und Direktionalität | Geringe Direktionalität und langsamere Geschwindigkeiten für Dielektrika; Herausforderungen für komplexe Substrate. |
Homogenität und großflächige Anwendbarkeit | Es ist schwierig, auf großen Flächen eine gleichmäßige Dicke und Zusammensetzung zu erreichen. |
Hochtemperatur-Nachbeschichtungsprozesse | Wärmebehandlungen können temperaturempfindliche Materialien beschädigen. |
Laufende Verbesserungen | Die Forschung befasst sich weiterhin mit Einschränkungen und verbessert die Vielseitigkeit und Effizienz. |
Entdecken Sie, wie Sie die Herausforderungen beim Magnetronsputtern meistern und Ihre Dünnschichtprozesse optimieren können – Kontaktieren Sie noch heute unsere Experten !