Der Sinterprozess wird von mehreren entscheidenden Variablen beeinflusst, die die endgültigen Eigenschaften des gesinterten Materials bestimmen.Zu diesen Variablen gehören die Temperatur, die Heizrate, der angewandte Druck, die Partikelgröße, die Zusammensetzung und die Sinteratmosphäre (wie Luft, Vakuum oder Inertgase wie Argon/Stickstoff).Jeder dieser Faktoren spielt eine einzigartige Rolle für die Sinterkinetik, die Verdichtung und das allgemeine Materialverhalten.So verbessern höhere Temperaturen und feinere Partikelgrößen im Allgemeinen die Verdichtung, während die Wahl der Atmosphäre die Oxidation oder Verunreinigung beeinflussen kann.Das Verständnis und die Optimierung dieser Variablen sind entscheidend für das Erreichen der gewünschten Materialeigenschaften wie Zugfestigkeit, Biegewechselfestigkeit und Kerbschlagarbeit.
Die wichtigsten Punkte werden erklärt:
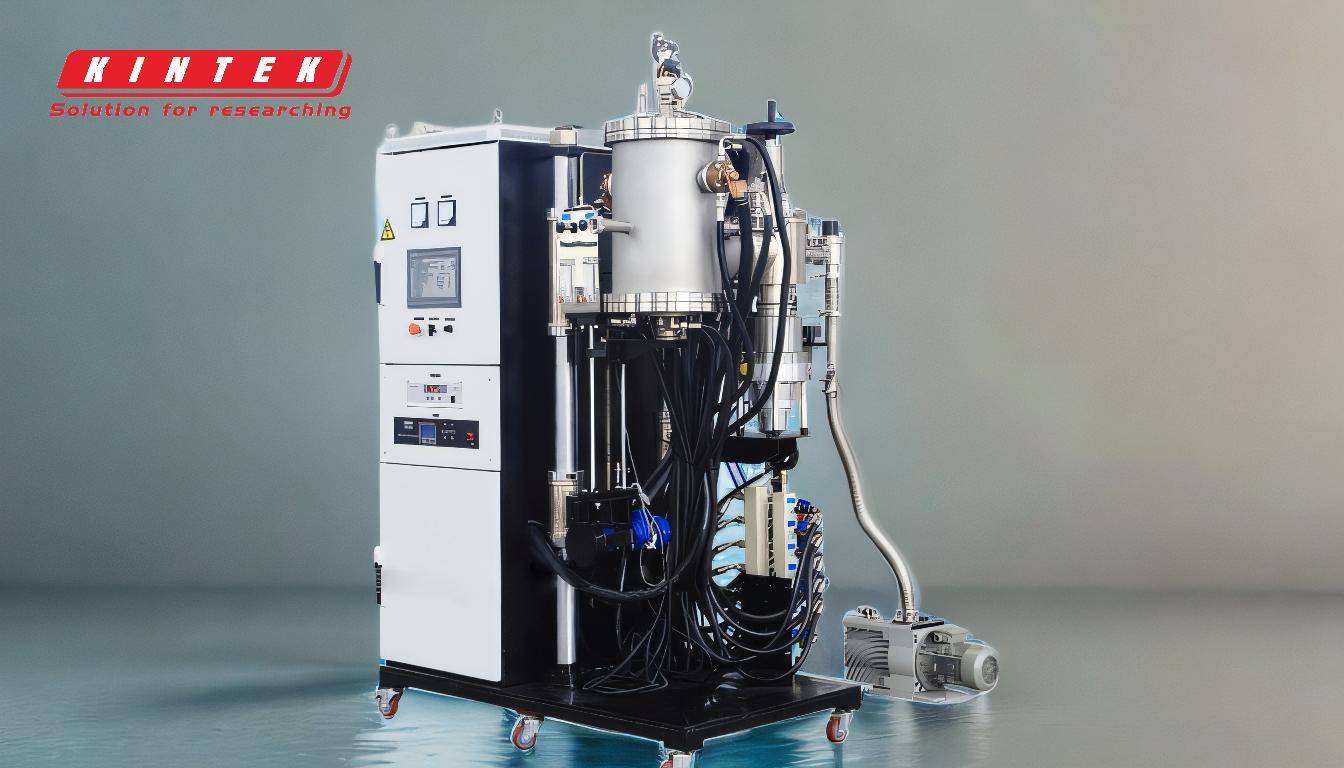
-
Temperatur:
- Die Temperatur ist eine der wichtigsten Variablen bei der Sinterung.Sie beeinflusst direkt die Sinterkinetik und die endgültigen Materialeigenschaften.
- Höhere Temperaturen beschleunigen im Allgemeinen die atomare Diffusion, was zu einer besseren Partikelbindung und Verdichtung führt.
- Zu hohe Temperaturen können jedoch unerwünschtes Kornwachstum oder Schmelzen verursachen, was die Materialintegrität beeinträchtigen kann.
-
Aufheizrate:
- Die Aufheizgeschwindigkeit bestimmt, wie schnell das Material die Sintertemperatur erreicht.
- Eine kontrollierte Aufheizrate ist wichtig, um einen Temperaturschock zu vermeiden, der zu Rissen oder ungleichmäßiger Verdichtung führen kann.
- Schnellere Erhitzungsgeschwindigkeiten können manchmal die Produktivität verbessern, müssen aber gegen das Risiko von Defekten abgewogen werden.
-
Angewandter Druck:
- Druck fördert die Umlagerung der Partikel und trägt zur Beseitigung von Porosität während des Sinterns bei.
- Höhere Drücke können zu einer gleichmäßigeren Verdichtung und besseren mechanischen Eigenschaften führen.
- Druckunterstützte Sintertechniken, wie Heißpressen oder Funkenplasmasintern, werden häufig eingesetzt, um Materialien mit hoher Dichte zu erhalten.
-
Partikelgröße:
- Kleinere Partikelgrößen begünstigen im Allgemeinen eine bessere Verdichtung aufgrund einer größeren Oberfläche und höherer Antriebskräfte für die Sinterung.
- Feine Pulver können zu einem homogeneren Gefüge und besseren mechanischen Eigenschaften führen.
- Zu feine Partikel können jedoch agglomerieren und erfordern eine sorgfältige Handhabung und Verarbeitung.
-
Zusammensetzung:
- Die chemische Zusammensetzung des Materials wirkt sich auf sein Sinterverhalten und seine endgültigen Eigenschaften aus.
- Homogene Zusammensetzungen neigen dazu, gleichmäßiger zu sintern, während heterogene Zusammensetzungen zu ungleichmäßiger Verdichtung oder Phasentrennung führen können.
- Auch das Vorhandensein von Additiven oder Dotierstoffen kann die Sinterkinetik und die Leistungsfähigkeit des Materials beeinflussen.
-
Sinteratmosphäre:
- Die Wahl der Sinteratmosphäre (z. B. Luft, Vakuum oder Inertgase wie Argon/Stickstoff) kann die endgültigen Materialeigenschaften erheblich beeinflussen.
- Eine inerte Atmosphäre verhindert Oxidation und Verunreinigung, was besonders bei reaktiven Materialien wichtig ist.
- Das Vakuumsintern kann dazu beitragen, flüchtige Verunreinigungen zu entfernen und die Porosität zu verringern, erfordert aber möglicherweise spezielle Anlagen.
-
Abkühlungsrate:
- Die Abkühlungsgeschwindigkeit nach dem Sintern wirkt sich auf das Mikrogefüge und die mechanischen Eigenschaften des Materials aus.
- Eine kontrollierte Abkühlung kann dazu beitragen, die gewünschten Phasenumwandlungen zu erreichen und die Eigenspannungen zu minimieren.
- Eine schnelle Abkühlung kann zu einer feineren Kornstruktur führen, aber auch thermische Spannungen verursachen.
-
Kontrolle der flüssigen Phase:
- Bei einigen Sinterverfahren kann sich eine flüssige Phase bilden, die die Verdichtung verbessern kann, aber sorgfältig kontrolliert werden muss.
- Ein Übermaß an flüssiger Phase kann zu einer Schwächung der Korngrenzen oder einer Phasentrennung führen, was die Materialeigenschaften beeinträchtigt.
- Die Menge der flüssigen Phase wird häufig auf der Grundlage der gewünschten Mikrostruktur und mechanischen Leistung optimiert.
Durch die sorgfältige Steuerung dieser Variablen können die Hersteller den Sinterprozess so anpassen, dass bestimmte Materialeigenschaften erzielt werden, z. B. eine höhere Zugfestigkeit, Biegewechselfestigkeit und Kerbschlagarbeit.Jede Variable steht in Wechselwirkung mit den anderen, so dass bei der Optimierung des Prozesses das gesamte Sintersystem berücksichtigt werden muss.
Zusammenfassende Tabelle:
Variable | Rolle bei der Sinterung | Wichtige Überlegungen |
---|---|---|
Temperatur | Beeinflusst die Sinterkinetik und die Verdichtung | Höhere Temperaturen verbessern die Bindung; bei zu hohen Temperaturen besteht die Gefahr von Kornwachstum oder Schmelzen. |
Aufheizrate | Bestimmt die Geschwindigkeit bis zur Sintertemperatur | Kontrollierte Geschwindigkeiten verhindern einen thermischen Schock; schnellere Geschwindigkeiten erhöhen die Produktivität, bergen aber das Risiko von Defekten. |
Angewandter Druck | Verbessert die Umlagerung von Partikeln und die Beseitigung von Porosität | Höhere Drücke verbessern die Verdichtung; Techniken wie Heißpressen werden für Ergebnisse mit hoher Dichte eingesetzt. |
Partikelgröße | Kleinere Partikel fördern eine bessere Verdichtung | Feine Pulver verbessern die Mikrostruktur; ein zu feines Pulver kann zu Agglomeration führen. |
Zusammensetzung | Beeinflusst das Sinterverhalten und die endgültigen Eigenschaften | Homogene Zusammensetzungen sintern gleichmäßig; Zusatzstoffe oder Dotiermittel beeinflussen die Leistung. |
Sinter-Atmosphäre | Beeinflusst Oxidation, Verunreinigung und Porosität | Inerte Gase verhindern Oxidation; Vakuum reduziert Verunreinigungen, erfordert jedoch spezielle Ausrüstung. |
Abkühlungsrate | Beeinflusst das Mikrogefüge und die mechanischen Eigenschaften | Kontrollierte Abkühlung minimiert Spannungen; schnelle Abkühlung kann das Korngefüge verfeinern, führt aber zu Spannungen. |
Kontrolle der flüssigen Phase | Verbessert die Verdichtung, muss aber kontrolliert werden | Eine übermäßige Flüssigphase kann die Korngrenzen schwächen; Optimierung ist der Schlüssel zu den gewünschten Eigenschaften. |
Optimieren Sie Ihren Sinterprozess für hervorragende Materialeigenschaften - Kontaktieren Sie unsere Experten noch heute !