Porosität beim Hartlöten ist ein häufiger Fehler, der die Verbindung erheblich schwächen und ihre Integrität beeinträchtigen kann.Sie entsteht, wenn Gas oder Luft in der Lötverbindung eingeschlossen wird und Hohlräume oder Blasen bildet.Die Ursachen für Porosität sind vielfältig und können auf Faktoren wie unsachgemäße Oberflächenvorbereitung, unzureichende Reinigung, schlechten Lotfluss, falsche Heizraten und unzureichende Verweildauer oder Temperatur zurückgeführt werden.Das Verständnis dieser Ursachen ist für die Optimierung des Lötprozesses und die Gewährleistung qualitativ hochwertiger, dauerhafter Verbindungen von entscheidender Bedeutung.
Die wichtigsten Punkte erklärt:
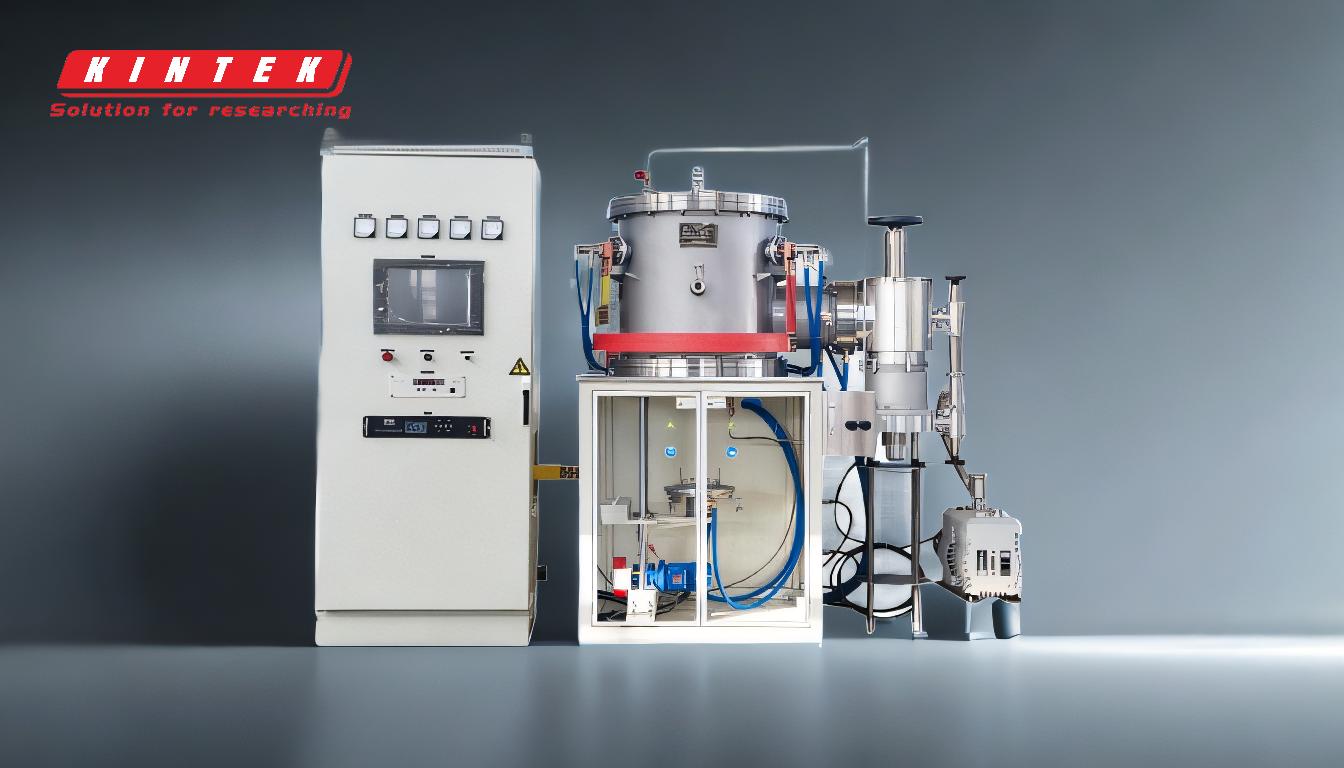
-
Unsachgemäße Oberflächenvorbereitung:
- Die Oberflächenvorbereitung ist entscheidend für das Erreichen einer festen Lötverbindung.Wenn die zu verbindenden Oberflächen nicht eben, glatt oder frei von Verunreinigungen sind, können die Kapillarwirkung und der Fluss des Füllmaterials behindert werden.Dies kann zu einer unvollständigen Benetzung und zur Bildung von Hohlräumen führen.
- Oxidfilme, Öl, Fett oder andere Rückstände auf der Oberfläche können eine ordnungsgemäße Bindung verhindern, Gase einschließen und Porosität verursachen.
- Lösung :Achten Sie auf eine gründliche Reinigung und Oberflächenvorbereitung, einschließlich der Entfernung von Oxidschichten und Verunreinigungen, vor dem Löten.
-
Unzureichende Reinigung:
- Die Wirksamkeit der Reinigung hängt vom Material, den atmosphärischen Bedingungen und der Handhabung ab.Wenn das Material nicht richtig gereinigt wird oder nach der Reinigung Verunreinigungen ausgesetzt ist, kann Porosität auftreten.
- Lösung :Reinigen Sie die Materialien unmittelbar vor dem Löten und minimieren Sie die Handhabung, um eine Rekontamination zu vermeiden.
-
Schlechter Fluss des Zusatzwerkstoffs:
- Das Spachtelmaterial muss gleichmäßig und vollständig in die Fuge fließen, um eine feste Verbindung zu bilden.Wenn das Spachtelmaterial die Oberflächen nicht richtig benetzt oder wenn es Lücken in der Fuge gibt, kann Gas eingeschlossen werden, was zu Porosität führt.
- Lösung :Optimieren Sie die Lötparameter, wie z.B. Temperatur, Verweilzeit und Heizrate, um einen ordnungsgemäßen Fluss des Zusatzwerkstoffs zu gewährleisten.
-
Falsche Heizrate:
- Zu schnelles oder ungleichmäßiges Erhitzen kann zu örtlicher Überhitzung oder unzureichender Erwärmung führen, was ein unvollständiges Schmelzen des Füllmaterials oder eingeschlossene Gase zur Folge hat.
- Lösung :Kontrollieren Sie die Aufheizgeschwindigkeit, um eine gleichmäßige Temperaturverteilung und ein ordnungsgemäßes Aufschmelzen des Füllmaterials zu gewährleisten.
-
Unzureichende Verweilzeit oder Temperatur:
- Die Verweiltemperatur und -zeit sind entscheidend für das Erreichen einer vollständigen Lötung.Wenn die Temperatur zu niedrig oder die Verweilzeit zu kurz ist, schmilzt oder fließt der Zusatzwerkstoff möglicherweise nicht vollständig, was zu Lunkern führt.
- Lösung :Halten Sie sich an die empfohlenen Verweiltemperaturen und -zeiten für die verwendeten Materialien und Zusatzwerkstoffe.
-
Vakuumniveau und -atmosphäre:
- Beim Vakuumlöten muss das Vakuum so hoch sein, dass die Gase aus dem Verbindungsbereich entfernt werden.Wenn das Vakuum zu niedrig ist, können Restgase zu Porosität führen.
- Lösung :Stellen Sie sicher, dass das Vakuumniveau für die verwendeten Materialien und den Lötprozess geeignet ist.
-
Materialspezifische Faktoren:
- Die Art des Grundmetalls und der Zusatzwerkstofflegierung kann die Porosität beeinflussen.So neigen Aluminiumlegierungen beispielsweise zur Oxidbildung, die Gase einschließen kann, wenn sie nicht ordnungsgemäß entfernt wird.
- Lösung :Wählen Sie kompatible Werkstoffe und verwenden Sie geeignete Reinigungs- und Löttechniken für die jeweilige Legierung.
-
Verbindungsdesign und Geometrie:
- Form und Größe der zu verbindenden Teile können den Füllstofffluss und den Gaseinschluss beeinflussen.Komplexe Geometrien oder enge Spalten können das Risiko von Porosität erhöhen.
- Lösung :Konstruieren Sie die Fugen so, dass ein ausreichender Freiraum und eine gute Zugänglichkeit für das Fließen des Füllmaterials gewährleistet sind.
-
Abkühlungsrate:
- Eine schnelle Abkühlung kann Gase in der Verbindung einschließen, während eine langsame Abkühlung Gase entweichen lässt.Unangemessene Abkühlungsraten können zu Porosität beitragen.
- Lösung :Kontrollieren Sie die Abkühlgeschwindigkeit, damit die Gase entweichen können, ohne die Festigkeit der Verbindung zu beeinträchtigen.
Durch die Berücksichtigung dieser Faktoren und die Optimierung des Lötprozesses kann die Porosität minimiert werden, was zu stärkeren, zuverlässigeren Verbindungen führt.
Zusammenfassende Tabelle:
Ursache der Porosität | Lösung |
---|---|
Unsachgemäße Oberflächenvorbereitung | Reinigen und bereiten Sie die Oberflächen gründlich vor und entfernen Sie Oxide und Verunreinigungen. |
Unzureichende Reinigung | Reinigen Sie die Materialien unmittelbar vor dem Löten und minimieren Sie die Handhabung. |
Schlechter Fluss des Zusatzwerkstoffs | Optimieren Sie die Lötparameter (Temperatur, Verweilzeit, Heizrate). |
Falsche Heizrate | Kontrollieren Sie die Heizrate für eine gleichmäßige Temperaturverteilung. |
Unzureichende Verweilzeit/Temperatur | Befolgen Sie die empfohlenen Richtlinien für Verweildauer und Temperatur. |
Vakuumniveau und -atmosphäre | Sorgen Sie für ein angemessenes Vakuumniveau für die Materialien und den Prozess. |
Materialspezifische Faktoren | Wählen Sie kompatible Materialien und verwenden Sie geeignete Reinigungs-/Löttechniken. |
Verbindungsdesign und Geometrie | Entwerfen Sie Fugen mit ausreichendem Freiraum und Zugänglichkeit für den Füllstofffluss. |
Abkühlungsrate | Steuern Sie die Abkühlgeschwindigkeit, damit Gase entweichen können, ohne die Verbindung zu schwächen. |
Benötigen Sie Hilfe bei der Minimierung von Porosität in Ihrem Lötprozess? Kontaktieren Sie noch heute unsere Experten für maßgeschneiderte Lösungen!