Die Frequenz beim Induktionshärten bezieht sich auf die Geschwindigkeit, mit der der Wechselstrom (AC) in der Induktionsspule schwingt, gemessen in Hertz (Hz).Sie spielt eine entscheidende Rolle bei der Bestimmung der Tiefe der Erwärmung und Härtung im Werkstück.Höhere Frequenzen führen aufgrund des Skin-Effekts, bei dem die Stromdichte an der Oberfläche höher ist und zum Inneren hin abnimmt, zu einer dünneren Heizschicht.Dadurch lässt sich die Tiefe der gehärteten Schicht genau steuern, was das Induktionshärten zu einer vielseitigen und effizienten Wärmebehandlungsmethode für die Oberflächenhärtung macht.
Die wichtigsten Punkte werden erklärt:
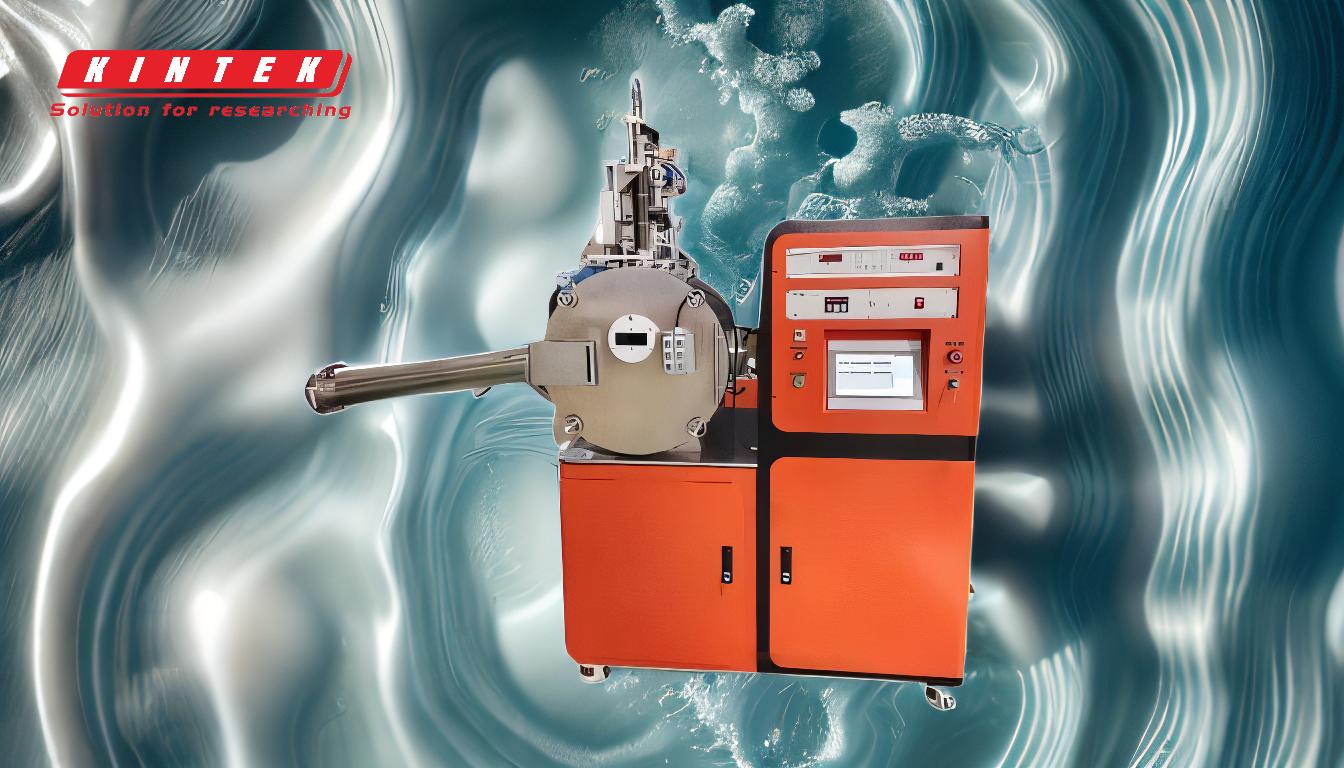
-
Definition der Frequenz beim Induktionshärten:
- Die Frequenz bezieht sich auf die Schwingungsrate des in der Induktionsspule verwendeten Wechselstroms (AC), gemessen in Hertz (Hz).
- Sie hat einen direkten Einfluss auf die Eindringtiefe des Stroms und die Wärmeentwicklung im Werkstück.
-
Skin-Effekt und Stromdichte:
- Der Skin-Effekt ist ein Phänomen, bei dem der Wechselstrom bei höheren Frequenzen dazu neigt, in der Nähe der Oberfläche eines Leiters zu fließen.
- Höhere Frequenzen führen zu einem größeren Stromdichteunterschied zwischen der Oberfläche und dem Inneren des Werkstücks.
- Dies führt zu einer dünneren Heizschicht an der Oberfläche, was ideal für Anwendungen ist, die eine flache Härtung erfordern.
-
Verhältnis zwischen Frequenz und Erwärmungstiefe:
- Höhere Frequenzen erzeugen eine geringere Erwärmungstiefe und eignen sich daher für dünne oder kleine Werkstücke.
- Niedrigere Frequenzen ermöglichen ein tieferes Eindringen und sind daher ideal für dickere oder größere Werkstücke.
- Diese Einstellbarkeit ist ein entscheidender Vorteil des Induktionshärtens, da sie eine präzise Steuerung der gehärteten Schichttiefe ermöglicht.
-
Kritische Temperatur und schnelle Abkühlung:
- Wenn die Heizschicht die kritische Temperatur erreicht (der Punkt, an dem sich der Stahl in Austenit umwandelt), erfolgt eine schnelle Abkühlung (Abschreckung).
- Durch diesen Prozess wird das gehärtete Gefüge verfestigt, was zu einer dauerhaften und verschleißfesten Oberfläche führt.
-
Anwendungen der Frequenzanpassung:
- Das Hochfrequenz-Induktionshärten wird für dünne Schichten, wie Zahnräder, Lager und kleine Werkzeuge, verwendet.
- Mittlere und niedrige Frequenzen werden für tiefere Härtungen bei größeren Bauteilen wie Wellen oder schweren Maschinenteilen eingesetzt.
-
Vorteile des Induktionshärtens:
- Präzise Steuerung der Härtetiefe durch Frequenzeinstellung.
- Energieeffiziente und lokalisierte Erwärmung, die Verzug und Energieverbrauch reduziert.
- Schnellere Bearbeitungszeiten im Vergleich zu herkömmlichen Wärmebehandlungsmethoden.
Wenn die Hersteller die Rolle der Frequenz beim Induktionshärten verstehen, können sie das Verfahren für bestimmte Anwendungen optimieren und die gewünschte Härte und Haltbarkeit der Werkstückoberfläche sicherstellen.
Zusammenfassende Tabelle:
Aspekt | Einzelheiten |
---|---|
Definition der Frequenz | Schwingungsrate des Wechselstroms in der Induktionsspule, gemessen in Hertz (Hz). |
Skin-Effekt | Höhere Frequenzen erzeugen aufgrund des Oberflächenstroms dünnere Heizschichten. |
Steuerung der Erwärmungstiefe | Hohe Frequenz = flache Erwärmung; niedrige Frequenz = tieferes Eindringen. |
Kritische Temperatur | Schnelle Abkühlung sorgt für ein gehärtetes Gefüge und damit für Verschleißfestigkeit. |
Anwendungen | Hochfrequenz: Zahnräder, Lager; Niederfrequenz: Wellen, schwere Maschinen. |
Vorteile | Präzise Steuerung, Energieeffizienz, schnellere Verarbeitung. |
Optimieren Sie Ihren Induktionshärteprozess - Kontaktieren Sie noch heute unsere Experten für maßgeschneiderte Lösungen!