Physical Vapour Deposition (PVD) ist eine Dünnschicht-Abscheidungstechnik, mit der hochpräzise und gleichmäßige Beschichtungen auf verschiedenen Substraten erzeugt werden. Dabei handelt es sich um die physikalische Übertragung von Material von einer festen Quelle auf ein Substrat in einer Vakuumumgebung. PVD wird aufgrund seiner Fähigkeit, langlebige, hochwertige Dünnschichten herzustellen, häufig in Branchen wie Elektronik, Optik und Schneidwerkzeugen eingesetzt. Im Gegensatz dazu ist die chemische Gasphasenabscheidung (CVD), einschließlich fortschrittlicher Methoden wie Chemische Gasphasenabscheidung mit Mikrowellenplasma , beruht auf chemischen Reaktionen, um dünne Filme abzuscheiden. Sowohl PVD als auch CVD haben sich seit ihrer frühen Entwicklung erheblich weiterentwickelt, wie im Buch von 1966 dokumentiert Aufdampfen von Powell, Oxley und Blocher.
Wichtige Punkte erklärt:
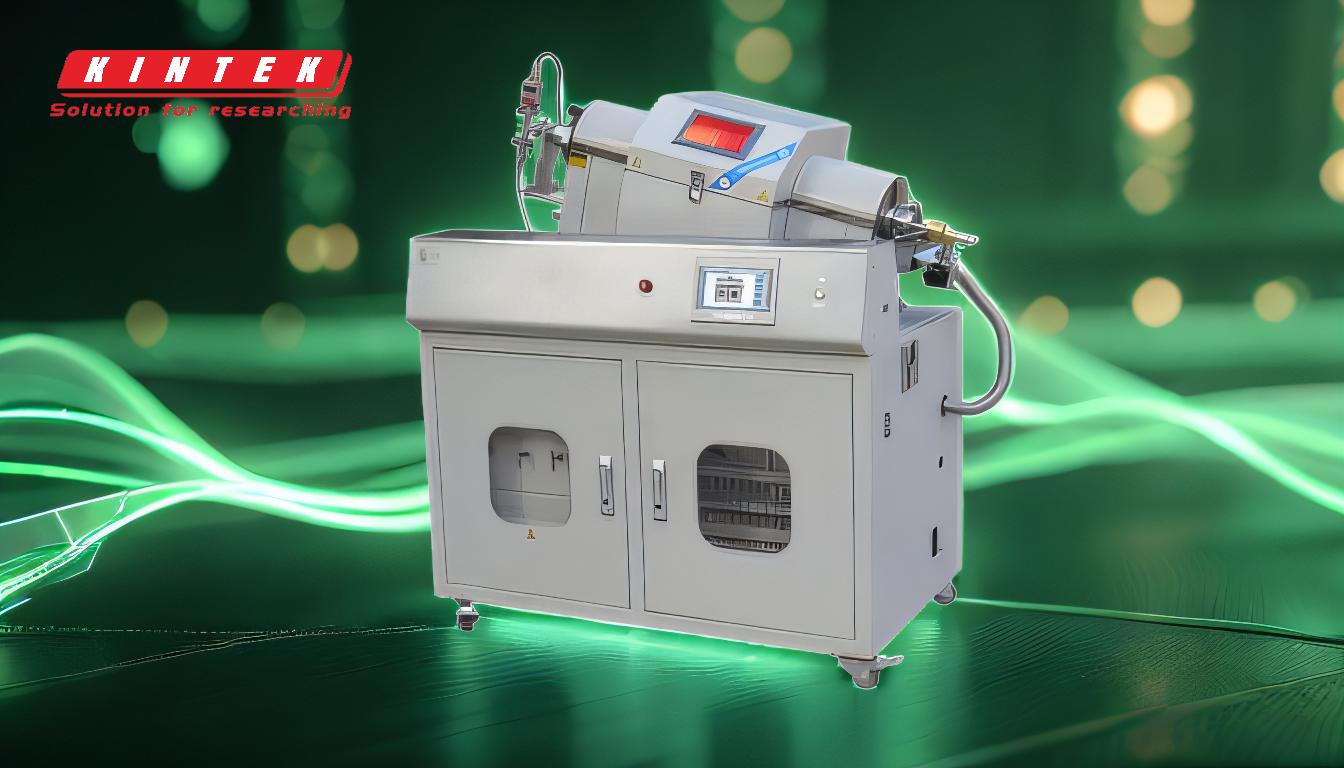
-
Definition und Prozess von PVD:
- PVD ist ein vakuumbasierter Prozess, bei dem ein festes Material verdampft und dann auf einem Substrat kondensiert wird, um einen dünnen Film zu bilden.
- Zu den gängigen PVD-Methoden gehören Sputtern, Verdampfen und Ionenplattieren.
- Beim Sputtern, einer weit verbreiteten PVD-Technik, wird ein Zielmaterial mit Ionen bombardiert, um Atome auszustoßen, die sich dann auf dem Substrat ablagern.
-
Anwendungen von PVD:
- PVD wird in Branchen wie Elektronik, Optik und Schneidwerkzeugen eingesetzt.
- Es ist ideal für die Herstellung von Hochtemperaturbeschichtungen, leitfähigen Beschichtungen für REM-Proben und Beschichtungen für wärmeempfindliche Materialien wie Kunststoffe oder biologische Proben.
- PVD-Beschichtungen verbessern Eigenschaften wie Verschleißfestigkeit, Korrosionsbeständigkeit und elektrische Leitfähigkeit.
-
Vergleich mit CVD:
- Bei der CVD handelt es sich um chemische Reaktionen zur Abscheidung dünner Filme, die oft hohe Temperaturen und spezielle Vorläufer erfordern.
- Im Gegensatz zu PVD können mit CVD komplexe Strukturen wie Kohlenstoffnanoröhren und GaN-Nanodrähte wachsen.
- CVD wird in der Elektronik für Halbleiterdünnschichten, in Schneidwerkzeugen für verschleißfeste Beschichtungen und in der Solarzellenherstellung für photovoltaische Materialien eingesetzt.
-
Historische Entwicklung:
- Die Techniken der PVD und CVD wurden erstmals im Buch von 1966 dokumentiert Aufdampfen von Powell, Oxley und Blocher.
- Dieses Buch beleuchtet die frühen Anwendungen dieser Methoden bei der Herstellung dünner Filme für verschiedene Branchen.
-
Vorteile von PVD:
- PVD erzeugt äußerst gleichmäßige und präzise dünne Filme mit hervorragender Haftung auf dem Substrat.
- Es arbeitet bei niedrigeren Temperaturen als CVD und eignet sich daher für wärmeempfindliche Materialien.
- PVD-Beschichtungen sind langlebig und können maßgeschneidert werden, um bestimmte funktionelle Eigenschaften zu erreichen.
-
Industrielle Relevanz:
- PVD und CVD sind integraler Bestandteil moderner Fertigungs- und Lieferketten.
- Sie ermöglichen die Herstellung fortschrittlicher Materialien und Beschichtungen, die für technologische Fortschritte in den Bereichen Elektronik, erneuerbare Energien und Materialwissenschaften von entscheidender Bedeutung sind.
Durch das Verständnis der Prinzipien und Anwendungen von PVD und CVD können Hersteller die geeignete Technik basierend auf ihren spezifischen Anforderungen auswählen und so eine optimale Leistung und Qualität von Dünnschichtprodukten gewährleisten.
Übersichtstabelle:
Aspekt | Einzelheiten |
---|---|
Definition | Vakuumbasiertes Verfahren zur Abscheidung dünner Filme durch physikalischen Materialtransfer. |
Gängige Methoden | Sputtern, Verdampfen, Ionenplattieren. |
Anwendungen | Elektronik, Optik, Schneidwerkzeuge, REM-Proben, wärmeempfindliche Materialien. |
Vorteile | Gleichmäßige Beschichtungen, niedrigere Temperaturen, langlebige, maßgeschneiderte Funktionseigenschaften. |
Vergleich mit CVD | PVD: Physischer Transfer; CVD: Chemische Reaktionen, höhere Temperaturen. |
Historischer Kontext | Dokumentiert in Aufdampfen (1966) von Powell, Oxley und Blocher. |
Entdecken Sie, wie PVD Ihre Dünnschichtanwendungen verbessern kann – Kontaktieren Sie uns noch heute für fachkundige Beratung!