Spark-Plasma-Sintern (SPS) ist eine fortschrittliche Sintertechnik, die die Anwendung von Druck und gepulstem elektrischen Strom kombiniert, um im Vergleich zu herkömmlichen Sintermethoden eine schnelle Verdichtung von Materialien bei relativ niedrigeren Temperaturen zu erreichen. Dieses Verfahren ist besonders effektiv für die Herstellung hochdichter, feinkörniger Materialien mit verbesserten mechanischen Eigenschaften. Der Hauptvorteil von SPS liegt in seiner Fähigkeit, schnelle Aufheiz- und Abkühlraten zu erreichen, was das Kornwachstum minimiert und die Erhaltung von Nanostrukturen ermöglicht. Dadurch eignet es sich hervorragend für fortschrittliche Materialien wie Keramik, Metalle und Verbundwerkstoffe.
Wichtige Punkte erklärt:
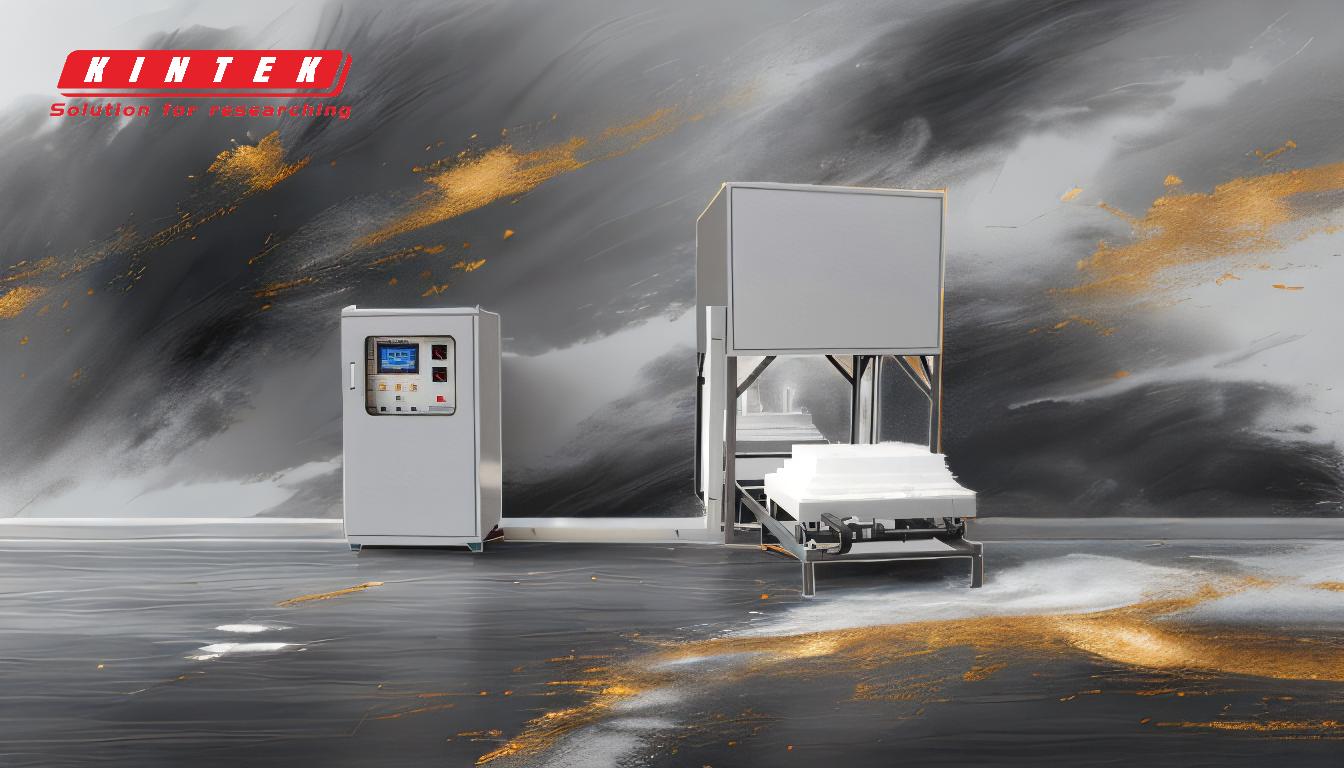
-
Grundprinzipien des Spark-Plasma-Sinterns:
- SPS nutzt einen gepulsten Gleichstrom (DC), der durch das Material und die Matrize fließt und durch Joulesche Erwärmung und Funkenplasmaentladung eine lokale Erwärmung erzeugt.
- Die gleichzeitige Anwendung von uniaxialem Druck und elektrischem Strom ermöglicht eine schnelle Partikelbindung und -verdichtung.
- Im Gegensatz zum herkömmlichen Sintern erreicht SPS eine Verdichtung bei niedrigeren Temperaturen und kürzeren Verarbeitungszeiten, was dazu beiträgt, die mikrostrukturelle Integrität des Materials zu bewahren.
-
Phasen des SPS-Prozesses:
- Pulverzubereitung: Das Rohmaterial wird in Form eines feinen Pulvers vorbereitet, das dann in eine Graphitform gefüllt wird.
- Verdichtung: Das Pulver wird unter mäßigem Druck verdichtet, um eine gleichmäßige Verteilung zu gewährleisten und Hohlräume zu vermeiden.
- Erhitzen und Sintern: Es wird ein gepulster Gleichstrom angelegt, der im Inneren des Materials Wärme erzeugt. Dieses schnelle Erhitzen fördert die Partikelbindung und -verdichtung.
- Kühlung: Nach dem Sintern kühlt das Material schnell ab, was zur Erhaltung der feinkörnigen Struktur beiträgt und das Kornwachstum verhindert.
-
Vorteile des Spark-Plasma-Sinterns:
- Schnelle Bearbeitung: SPS kann die vollständige Verdichtung in wenigen Minuten erreichen, im Vergleich zu Stunden oder sogar Tagen, die bei herkömmlichen Sintermethoden erforderlich sind.
- Niedrigere Sintertemperaturen: Der Prozess läuft bei Temperaturen ab, die deutlich unter dem Schmelzpunkt des Materials liegen, wodurch das Risiko einer thermischen Zersetzung verringert wird.
- Verbesserte Materialeigenschaften: SPS produziert Materialien mit hoher Dichte, feiner Korngröße und verbesserten mechanischen Eigenschaften wie Härte, Festigkeit und Verschleißfestigkeit.
- Vielseitigkeit: SPS ist auf eine Vielzahl von Materialien anwendbar, darunter Keramik, Metalle, Verbundwerkstoffe und sogar Nanomaterialien.
-
Anwendungen des Spark-Plasma-Sinterns:
- Hochleistungskeramik: SPS wird häufig zur Herstellung von Hochleistungskeramik mit hervorragenden mechanischen und thermischen Eigenschaften verwendet.
- Metalle und Legierungen: Das Verfahren ist wirksam beim Sintern von Metallen und Legierungen, insbesondere solchen, die mit herkömmlichen Methoden schwer zu verdichten sind.
- Nanomaterialien: SPS ist ideal für die Konsolidierung von Nanomaterialien unter Beibehaltung ihrer Nanostruktur, was für Anwendungen in der Elektronik, Katalyse und Energiespeicherung von entscheidender Bedeutung ist.
- Verbundwerkstoffe: SPS ermöglicht die Herstellung von Verbundwerkstoffen mit maßgeschneiderten Eigenschaften durch die Kombination verschiedener Materialien in einem einzigen Sinterschritt.
-
Vergleich mit konventionellem Sintern:
- Konventionelles Sintern ist auf externe Heizquellen und längere Verarbeitungszeiten angewiesen, was zu Kornwachstum und verringerten Materialeigenschaften führen kann.
- SPS hingegen nutzt die interne Erwärmung durch elektrischen Strom, was zu einer schnelleren Verdichtung und einer besseren Kontrolle der Mikrostruktur führt.
- Die Möglichkeit, beim Sintern in SPS Druck auszuüben, verbessert die Verdichtung weiter und verringert die Porosität.
Zusammenfassend ist das Funkenplasmasintern eine hocheffiziente und vielseitige Sintertechnik, die gegenüber herkömmlichen Methoden erhebliche Vorteile bietet. Seine Fähigkeit, hochdichte, feinkörnige Materialien mit verbesserten Eigenschaften herzustellen, macht es zu einem wertvollen Werkzeug in der Herstellung fortschrittlicher Materialien.
Übersichtstabelle:
Aspekt | Einzelheiten |
---|---|
Verfahren | Kombiniert Druck und gepulsten elektrischen Strom für eine schnelle Verdichtung. |
Hauptvorteile | Schnelle Verarbeitung, niedrigere Sintertemperaturen, verbesserte Materialeigenschaften. |
Anwendungen | Hochleistungskeramik, Metalle, Legierungen, Nanomaterialien und Verbundwerkstoffe. |
Vergleich | Schneller und effizienter als herkömmliche Sintermethoden. |
Erfahren Sie, wie Spark-Plasma-Sintern Ihre Materialproduktion revolutionieren kann – Kontaktieren Sie noch heute unsere Experten !