Sputtern ist eine Technik der physikalischen Gasphasenabscheidung (PVD), mit der dünne Schichten auf Substrate aufgebracht werden.Dabei wird in einer Vakuumkammer durch Ionisierung eines Inertgases, in der Regel Argon, ein Plasma erzeugt.Das Plasma erzeugt hochenergetische Ionen, die ein Zielmaterial beschießen und Atome oder Moleküle von dessen Oberfläche lösen.Diese abgelösten Teilchen bilden einen Dampfstrom, der sich auf einem Substrat ablagert und eine dünne Schicht bildet.Das Sputtern ist in Branchen wie der Halbleiter-, Optik- und Solarindustrie weit verbreitet, da sich damit gleichmäßige, hochwertige Schichten mit präziser Kontrolle über Dicke und Zusammensetzung herstellen lassen.
Die wichtigsten Punkte werden erklärt:
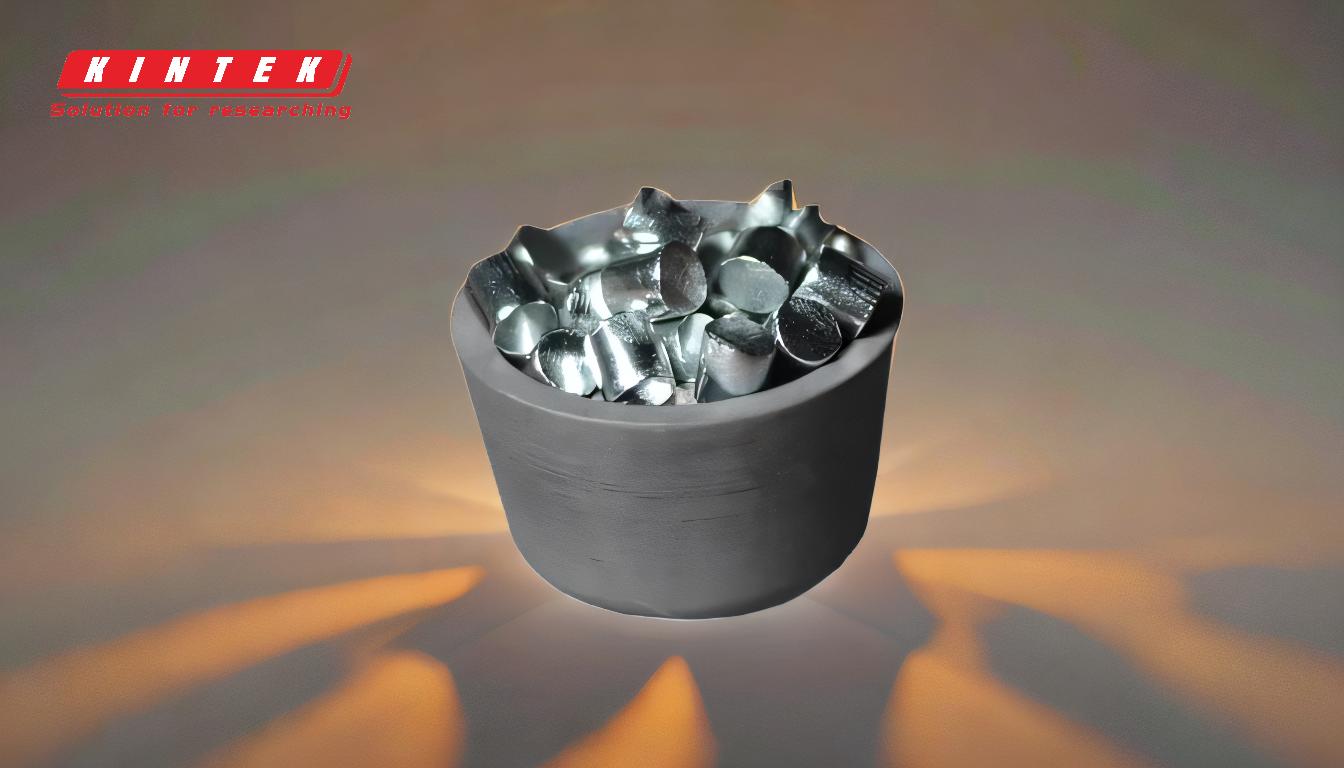
-
Grundlegender Mechanismus des Sputterns:
- Das Sputtern erfolgt in einer Vakuumkammer, in die ein inertes Gas, in der Regel Argon, eingeleitet wird.
- Eine Kathode wird elektrisch erregt, um ein Plasma zu erzeugen, das die Gasatome ionisiert.
- Die positiv geladenen Argon-Ionen werden aufgrund des elektrischen Feldes auf ein Zielmaterial beschleunigt.
- Beim Aufprall lösen die Ionen Atome oder Moleküle aus dem Zielmaterial heraus und erzeugen einen Dampfstrom.
- Dieser Dampfstrom lagert sich auf einem Substrat ab und bildet einen dünnen Film.
-
Die Rolle des Plasmas und der Kollisionskaskade:
- Das Plasma ist eine Schlüsselkomponente beim Sputtern, da es die Energie liefert, die zur Ionisierung des Gases und zur Beschleunigung der Ionen auf das Target benötigt wird.
- Wenn die Ionen mit dem Target kollidieren, lösen sie eine "Kollisionskaskade" aus, bei der Energie durch das Targetmaterial übertragen wird und Atome von dessen Oberfläche ausgestoßen werden.
- Durch diesen Prozess wird sichergestellt, dass die ausgestoßenen Partikel eine atomare Größe haben, was eine präzise und gleichmäßige Abscheidung ermöglicht.
-
Vorteile des Sputterns:
- Einheitliche Ablagerung:Das Sputtern erzeugt sehr gleichmäßige dünne Schichten und eignet sich daher ideal für Anwendungen, die eine gleichmäßige Schichtdicke erfordern.
- Niedrige Eigenspannung:Das Verfahren verdichtet die abgeschiedene Schicht und reduziert Eigenspannungen, insbesondere bei niedrigeren Abscheidetemperaturen.
- Präzise Kontrolle:Die Schichtdicke kann durch Anpassung der Abscheidungszeit und anderer Parameter präzise gesteuert werden.
- Vielseitigkeit:Durch Sputtern kann eine breite Palette von Materialien, darunter Metalle, Legierungen und Keramiken, auf verschiedene Substrate aufgebracht werden.
-
Anwendungen des Sputterns:
- Halbleiter:Zur Abscheidung dünner Schichten aus leitenden und isolierenden Materialien auf Siliziumwafern.
- Optik:Wird bei der Herstellung von Antireflexionsbeschichtungen, Spiegeln und optischen Filtern verwendet.
- Solarpaneele:Für die Abscheidung dünner Schichten aus photovoltaischen Materialien zur effizienten Energieumwandlung.
- Dekorative Beschichtungen:Wird eingesetzt, um haltbare und ästhetisch ansprechende Beschichtungen auf Konsumgütern herzustellen.
-
Schlüsselkomponenten eines Sputtering-Systems:
- Vakuumkammer:Hält eine kontrollierte Umgebung frei von Verunreinigungen.
- Ziel-Material:Die Quelle des Materials, das aufgebracht werden soll.
- Substrat:Die Oberfläche, auf die die dünne Schicht aufgebracht wird.
- Inertes Gas (Argon):Liefert die für den Sputterprozess erforderlichen Ionen.
- Energieversorgung:Erzeugt das elektrische Feld zur Ionisierung des Gases und zur Beschleunigung der Ionen.
-
Prozess-Optimierung:
- Gasdruck:Ein optimaler Gasdruck gewährleistet eine effiziente Ionisierung und Kollisionsrate.
- Leistungsaufnahme:Eine höhere Leistung erhöht die Energie der Ionen, was die Abscheidungsraten verbessert, aber eine sorgfältige Kontrolle erfordert, um eine Beschädigung des Targets oder des Substrats zu vermeiden.
- Temperatur des Substrats:Niedrigere Temperaturen verringern die Eigenspannung, während höhere Temperaturen die Schichthaftung und die Kristallinität verbessern können.
-
Vergleich mit anderen Dünnschichtabscheidungstechniken:
- Das Sputtern wird oft mit dem Verdampfen, einer anderen PVD-Technik, verglichen.Während das Verdampfen einfacher und schneller ist, bietet das Sputtern eine bessere Kontrolle über die Schichtzusammensetzung und Gleichmäßigkeit, insbesondere bei komplexen Materialien.
- Das Sputtern eignet sich auch besser für die Abscheidung von Materialien mit hohen Schmelzpunkten, da das Target nicht auf Verdampfungstemperaturen erhitzt werden muss.
-
Herausforderungen und Überlegungen:
- Ziel Erosion:Durch den kontinuierlichen Beschuss kann das Zielmaterial erodieren und muss regelmäßig ausgetauscht werden.
- Kontamination:Verunreinigungen im Gas oder in der Kammer können die Filmqualität beeinträchtigen, weshalb hochreine Materialien und Reinraumumgebungen erforderlich sind.
- Kosten:Sputtersysteme können teuer sein, da sie eine Vakuumausrüstung und präzise Steuerungen benötigen.
Wenn die Käufer von Geräten und Verbrauchsmaterialien diese wichtigen Punkte verstehen, können sie fundierte Entscheidungen über Sputtersysteme treffen und sicherstellen, dass sie die richtigen Komponenten und Parameter für ihre spezifischen Anwendungen auswählen.
Zusammenfassende Tabelle:
Aspekt | Einzelheiten |
---|---|
Mechanismus | Das Plasma ionisiert ein Inertgas, wodurch sich die Zielatome lösen und einen dünnen Film bilden. |
Die wichtigsten Vorteile | Gleichmäßige Abscheidung, geringe Eigenspannung, präzise Kontrolle und Vielseitigkeit. |
Anwendungen | Halbleiter, Optik, Sonnenkollektoren, dekorative Beschichtungen. |
Wichtige Komponenten | Vakuumkammer, Targetmaterial, Substrat, Inertgas, Stromversorgung. |
Faktoren für die Optimierung | Gasdruck, Leistungsaufnahme, Substrattemperatur. |
Herausforderungen | Targeterosion, Verunreinigung und hohe Kosten. |
Sind Sie bereit, Sputtering in Ihren Prozess zu integrieren? Kontaktieren Sie noch heute unsere Experten für maßgeschneiderte Lösungen!