Die Dichte eines Sintermaterials ist ein entscheidender Parameter, der seine mechanischen, thermischen und elektrischen Eigenschaften beeinflusst.Sintern ist ein Verfahren, bei dem pulverförmige Materialien verdichtet und erhitzt werden, um eine feste Masse zu bilden, ohne dass das Material vollständig schmilzt.Die Dichte eines Sinters wird in der Regel als Prozentsatz der theoretischen Dichte des Materials ausgedrückt, d. h. der Dichte des Materials, wenn es völlig dicht und ohne Porosität wäre.Das Erreichen einer hohen relativen Dichte ist für die Gewährleistung der Leistungsfähigkeit des Sinters in der vorgesehenen Anwendung von wesentlicher Bedeutung.Der Sinterprozess umfasst mehrere Stufen, darunter die Entfernung von Poren und das Erreichen einer gleichmäßigen Schrumpfung, was sich direkt auf die endgültige Dichte des Sinters auswirkt.
Die wichtigsten Punkte werden erklärt:
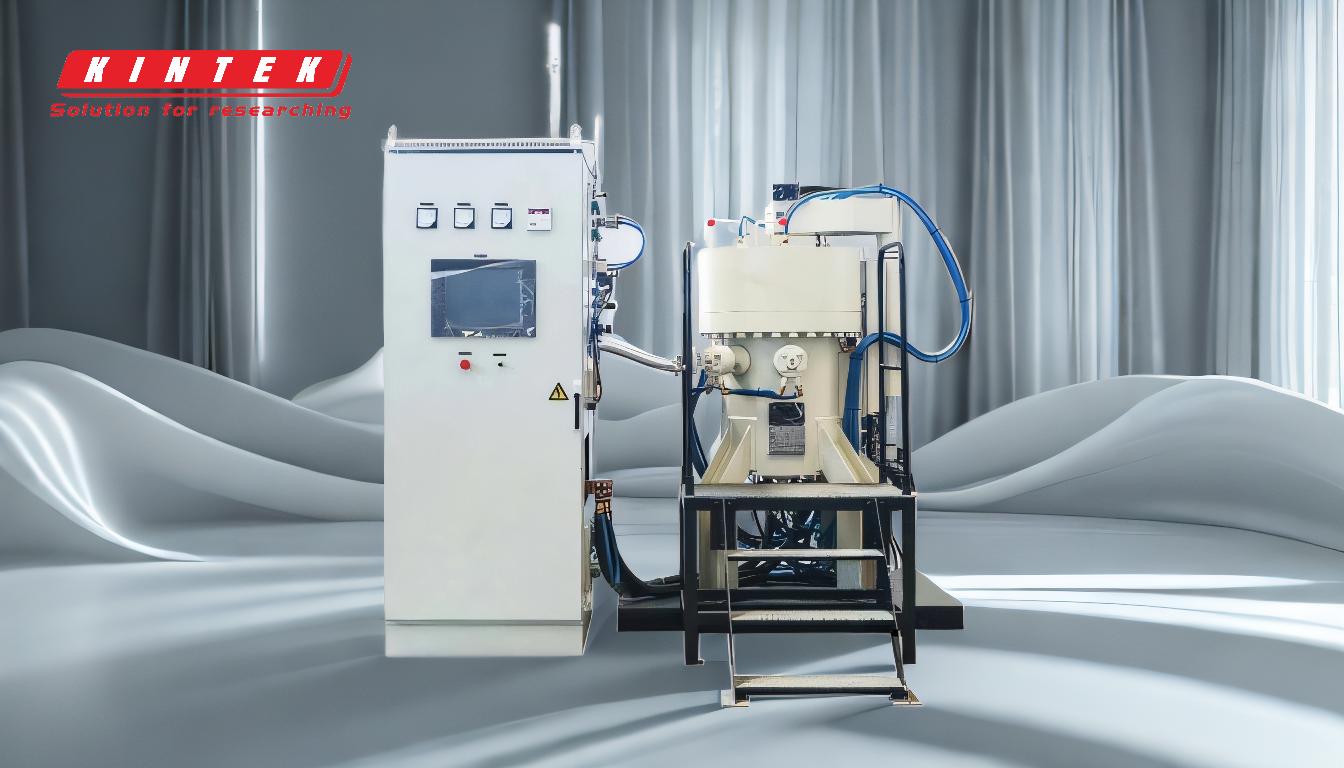
-
Definition der Sinterdichte:
- Die Dichte eines Sinters bezieht sich auf die Masse pro Volumeneinheit des gesinterten Materials.Sie wird häufig als Prozentsatz der theoretischen Dichte ausgedrückt, die die maximal mögliche Dichte des Materials ohne Porosität ist.
- Die theoretische Dichte wird auf der Grundlage der Kristallstruktur und des Atomgewichts des Materials berechnet.Die theoretische Dichte von Aluminiumoxid (Al₂O₃) beträgt zum Beispiel etwa 3,98 g/cm³.
-
Bedeutung der relativen Dichte:
- Die relative Dichte ist ein Maß dafür, wie nahe die Dichte des gesinterten Materials an seiner theoretischen Dichte liegt.In der ersten Sinterphase wird häufig eine relative Dichte von mehr als 75 % angestrebt, um die Beseitigung überkritischer Poren zu gewährleisten.
- Überkritische Poren sind große Hohlräume, die das Material erheblich schwächen können.Die Beseitigung dieser Poren in der ersten Sinterstufe ist entscheidend für die Erzielung eines festen und dichten Endprodukts.
-
Sinterprozess und Dichtheitskontrolle:
- Der Sinterprozess umfasst in der Regel zwei Hauptphasen: eine erste Sinterphase und eine letzte Verdichtungsphase.
- In der Anfangsphase wird das Material auf eine Temperatur erhitzt, die eine relative Dichte von mindestens 75 % gewährleistet.In dieser Phase werden große Poren entfernt und der Verdichtungsprozess eingeleitet.
- Nach dem Abkühlen wird das Material einer zweiten Sintertemperatur unterzogen, bei der es bis zum Abschluss der Verdichtung gehalten wird.In dieser Phase wird sichergestellt, dass das Material seine höchstmögliche Dichte bei minimaler Porosität erreicht.
-
Die Rolle der grünen Dichte:
- Die Rohdichte bezieht sich auf die Dichte des verdichteten Pulvers vor dem Sintern.Eine gleichmäßige Rohdichte ist entscheidend, um eine kontrollierte und gleichmäßige Schrumpfung während des Sinterns zu erreichen.
- Hochleistungskeramik beispielsweise schrumpft während des Sinterns in der Regel um 20-25 %.Wenn die Rohdichte nicht gleichmäßig ist, wird die Schrumpfung ungleichmäßig sein, was zu Defekten wie Verformungen oder Rissen im Endprodukt führt.
-
Faktoren, die die Sinterdichte beeinflussen:
- Partikelgröße und -verteilung:Kleinere Partikel mit einer engen Größenverteilung neigen dazu, effektiver zu sintern, was zu höheren Dichten führt.
- Sintertemperatur und Sinterzeit:Höhere Temperaturen und längere Sinterzeiten führen in der Regel zu höheren Dichten, aber es muss darauf geachtet werden, dass eine Übersinterung vermieden wird, die zu Kornwachstum und schlechteren mechanischen Eigenschaften führen kann.
- Druck:Bei einigen Sinterverfahren, wie z. B. dem Heißpressen oder dem Funkenplasmasintern, wird zur Verbesserung der Verdichtung externer Druck angewendet.
-
Messung der Sinterdichte:
- Die Dichte eines Sinters kann mit Techniken wie dem archimedischen Prinzip gemessen werden, bei dem die Probe in Luft und anschließend in einer Flüssigkeit gewogen wird, um ihr Volumen zu bestimmen.
- Mit Hilfe der Röntgenbeugung (XRD) kann auch die theoretische Dichte auf der Grundlage der Kristallstruktur des Materials geschätzt und mit der gemessenen Dichte verglichen werden, um die relative Dichte zu bestimmen.
-
Anwendungen und Implikationen der Sinterdichte:
- Sinter mit hoher Dichte ist unerlässlich für Anwendungen, die eine hohe Festigkeit, Verschleißfestigkeit und thermische Stabilität erfordern, wie z. B. bei Schneidwerkzeugen, Komponenten für die Luft- und Raumfahrt und elektronischen Substraten.
- Im Gegensatz dazu kann eine kontrollierte Porosität (geringere Dichte) bei einigen Anwendungen wie Filtern oder Katalysatoren, bei denen eine große Oberfläche erforderlich ist, wünschenswert sein.
Zusammenfassend lässt sich sagen, dass die Dichte eines Sinters ein kritischer Faktor ist, der seine Leistung in verschiedenen Anwendungen bestimmt.Das Erreichen einer hohen relativen Dichte erfordert eine sorgfältige Kontrolle des Sinterprozesses, einschließlich der Anfangs- und Endsintertemperaturen sowie der Gleichmäßigkeit der Rohdichte.Das Verständnis und die Optimierung dieser Faktoren können zur Herstellung hochwertiger gesinterter Materialien mit den gewünschten Eigenschaften führen.
Zusammenfassende Tabelle:
Aspekt | Einzelheiten |
---|---|
Definition | Masse pro Volumeneinheit des gesinterten Materials, ausgedrückt als % der theoretischen Dichte. |
Theoretische Dichte | Maximale Dichte ohne Porosität (z. B. Al₂O₃: ~3,98 g/cm³). |
Relative Dichte | Ziel >75% in der Anfangsphase, um überkritische Poren zu entfernen. |
Sinterstadien | 1.Anfangsstadium (75%+ Dichte), 2. endgültige Verdichtung (minimale Porosität). |
Grüne Dichte | Die Gleichmäßigkeit gewährleistet eine kontrollierte Schrumpfung (z. B. 20-25 % bei Keramik). |
Schlüsselfaktoren | Partikelgröße, Sintertemperatur/-zeit, Außendruck. |
Messmethoden | Archimedes'sches Prinzip, Röntgenbeugung (XRD). |
Anwendungen | Hohe Dichte: Schneidwerkzeuge, Luft- und Raumfahrt; geringere Dichte: Filter, Katalysatoren. |
Benötigen Sie Hilfe bei der Optimierung Ihres Sinterprozesses? Kontaktieren Sie unsere Experten noch heute!