Das Sintern ist ein wichtiger Prozess in der Pulvermetallurgie und der Keramik, bei dem pulverförmige Materialien erhitzt werden, um eine feste Masse zu bilden, ohne zu schmelzen. Die beiden Hauptarten des Sinterns sind das Flüssigphasensintern und das Festphasensintern. Beim Flüssigphasensintern wird ein Material mit niedrigem Schmelzpunkt zugegeben, das während des Prozesses schmilzt, die Umlagerung und Bindung der Partikel unterstützt und die erforderliche Sintertemperatur senkt. Dieses Verfahren eignet sich besonders für schwer zu sinternde Materialien. Im Gegensatz dazu findet das Festphasensintern vollständig im festen Zustand statt, wobei sich die Partikel durch Diffusion ohne Flüssigphase verbinden. Die Wahl zwischen diesen Methoden hängt von den Materialeigenschaften und den gewünschten Ergebnissen ab.
Die wichtigsten Punkte erklärt:
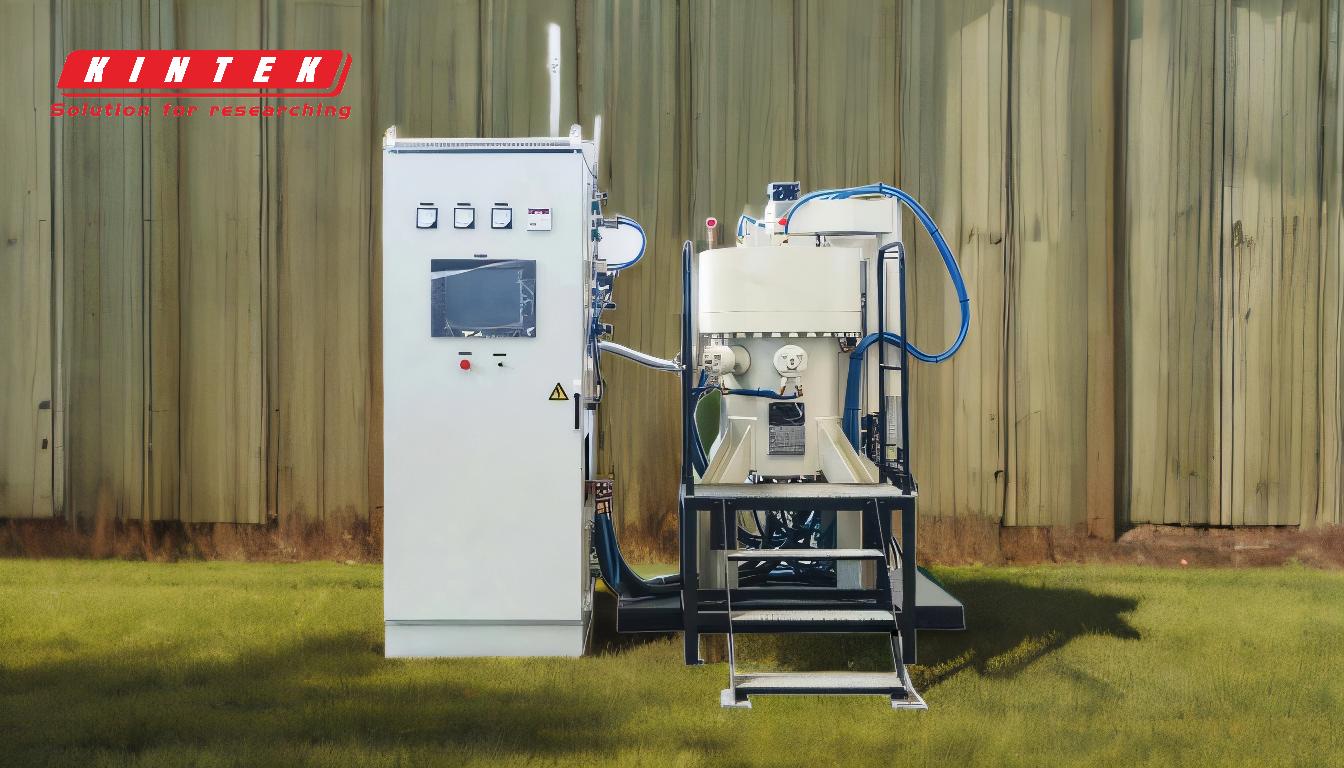
-
Definition und Mechanismus:
- Flüssigphasensintern: Bei diesem Verfahren wird dem Pulver ein Material mit niedrigem Schmelzpunkt zugesetzt. Beim Erhitzen schmilzt dieser Zusatzstoff und bildet eine flüssige Phase, die die Umlagerung und Bindung der Partikel unterstützt. Die flüssige Phase wirkt als Bindemittel oder Flussmittel, wodurch die erforderliche Sintertemperatur gesenkt und die Verdichtung verbessert wird. Dieses Verfahren eignet sich besonders für schwer zu sinternde Materialien.
- Festphasensintern: Bei diesem Verfahren wird der Pulverpressling vollständig im festen Zustand bei der Sintertemperatur verdichtet. Es ist keine flüssige Phase vorhanden; stattdessen verbinden sich die Partikel durch Festkörperdiffusionsmechanismen. Dieses Verfahren wird in der Regel für Materialien verwendet, die eine ausreichende Verdichtung ohne Flüssigphase erreichen können.
-
Anforderungen an die Temperatur:
- Flüssigphasensintern: Durch das Vorhandensein einer flüssigen Phase wird die Sintertemperatur erheblich gesenkt, wodurch der Prozess energieeffizienter wird. Die flüssige Phase ermöglicht eine schnellere Umlagerung und Bindung der Partikel, was bei Materialien, die niedrigere Verarbeitungstemperaturen erfordern, von Vorteil sein kann.
- Festphasensintern: Dieses Verfahren erfordert im Allgemeinen höhere Temperaturen als das Flüssigphasensintern, da sich die Partikel durch Festkörperdiffusion verbinden müssen, was ein langsamerer Prozess ist und oft mehr thermische Energie erfordert.
-
Materialeignung:
- Flüssig-Phasen-Sintern: Ideal für Materialien, die schwer zu sintern sind oder eine höhere Verdichtung erfordern. Die flüssige Phase hilft beim Füllen der Poren und bei der Neuanordnung der Körner, was zu einer günstigeren Packungsanordnung führt.
- Festphasensintern: Geeignet für Materialien, die allein durch Festkörperdiffusion eine ausreichende Verdichtung erreichen können. Dieses Verfahren wird häufig für Werkstoffe verwendet, die die zusätzlichen Vorteile einer flüssigen Phase nicht benötigen.
-
Prozess-Effizienz:
- Flüssigphasensintern: Das Verfahren ist im Allgemeinen aufgrund der niedrigeren Sintertemperaturen und der schnelleren Verdichtungsraten effizienter. Die flüssige Phase ermöglicht eine schnellere Umlagerung und Bindung der Partikel, was zu kürzeren Verarbeitungszeiten führt.
- Festphasensintern: Dieses Verfahren kann zwar höhere Temperaturen und längere Verarbeitungszeiten erfordern, ist aber einfacher und weniger komplex, da es keine flüssige Phase beinhaltet.
-
Anwendungen:
- Flüssig-Phasen-Sintern: Wird häufig bei der Herstellung von Keramiken, Hartmetallen und bestimmten Metalllegierungen eingesetzt, bei denen eine höhere Verdichtung und niedrigere Verarbeitungstemperaturen von Vorteil sind.
- Festphasensintern: Wird in der Regel für Metalle und Keramiken verwendet, die die gewünschte Dichte und Eigenschaften allein durch Festkörperdiffusion erreichen können.
-
Überlegungen zur Ausrüstung:
- Flüssig-Phasen-Sintern: Das Verfahren erfordert möglicherweise spezielle Sinteröfen die eine präzise Temperaturkontrolle ermöglichen, um die flüssige Phase effektiv zu steuern.
- Festphasensintern: Standard-Sinteröfen sind in der Regel ausreichend, da der Prozess keine flüssige Phase beinhaltet und bei höheren Temperaturen durchgeführt werden kann, ohne dass eine präzise Steuerung der flüssigen Phase erforderlich ist.
Zusammenfassend lässt sich sagen, dass die Wahl zwischen Flüssigphasen- und Festphasensintern von den Materialeigenschaften, den gewünschten Ergebnissen und den Verarbeitungsbedingungen abhängt. Das Flüssigphasensintern bietet Vorteile in Form von niedrigeren Temperaturen und schnellerer Verdichtung, während das Festphasensintern einfacher ist und sich für Materialien eignet, die durch Festkörperdiffusion eine ausreichende Verdichtung erreichen können.
Zusammenfassende Tabelle:
Aspekt | Flüssig-Phasen-Sintern | Festphasensintern |
---|---|---|
Definition | Es handelt sich um ein Material mit niedrigem Schmelzpunkt, das schmilzt und so die Umlagerung und Bindung der Partikel unterstützt. | Findet vollständig im festen Zustand statt; die Partikel verbinden sich durch Festkörperdiffusion. |
Temperatur | Niedrigere Sintertemperatur aufgrund der flüssigen Phase. | Für die Festkörperdiffusion sind höhere Temperaturen erforderlich. |
Material Eignung | Ideal für schwer zu sinternde Werkstoffe oder solche, die eine erhöhte Verdichtung erfordern. | Geeignet für Materialien, die durch Festkörperdiffusion verdichtet werden. |
Prozess-Effizienz | Effizienter durch schnellere Verdichtung und niedrigere Temperaturen. | Langsamer, aber unkomplizierter, ohne die Komplexität der Verwaltung einer flüssigen Phase. |
Anwendungen | Einsatz in Keramik, Hartmetallen und bestimmten Metalllegierungen. | Wird häufig für Metalle und Keramiken verwendet, die ihre Eigenschaften durch Festkörperdiffusion erhalten. |
Ausrüstung | Erfordert spezielle Sinteröfen mit präziser Temperaturregelung. | Standard-Sinteröfen sind ausreichend. |
Benötigen Sie Hilfe bei der Auswahl des richtigen Sinterverfahrens für Ihre Materialien? Kontaktieren Sie noch heute unsere Experten für eine persönliche Beratung!