Widerstandslöten und Induktionslöten sind zwei verschiedene Verfahren zum Verbinden von Metallen unter Verwendung eines Zusatzwerkstoffs, die sich jedoch in ihren Erwärmungsmechanismen, Anwendungen und Betriebseigenschaften erheblich unterscheiden. Beim Widerstandslöten wird die Wärme direkt an der Verbindungsstelle durch elektrischen Widerstand erzeugt, wodurch es sich für eine örtlich begrenzte Erwärmung und eine präzise Steuerung eignet. Beim Induktionslöten hingegen wird das Werkstück durch elektromagnetische Induktion erwärmt. Es bietet schnellere Erwärmungsraten und eignet sich besser für komplexe Geometrien oder Großserien. Beide Verfahren haben einzigartige Vorteile und Einschränkungen, die sie für unterschiedliche industrielle Anwendungen geeignet machen.
Die wichtigsten Punkte werden erklärt:
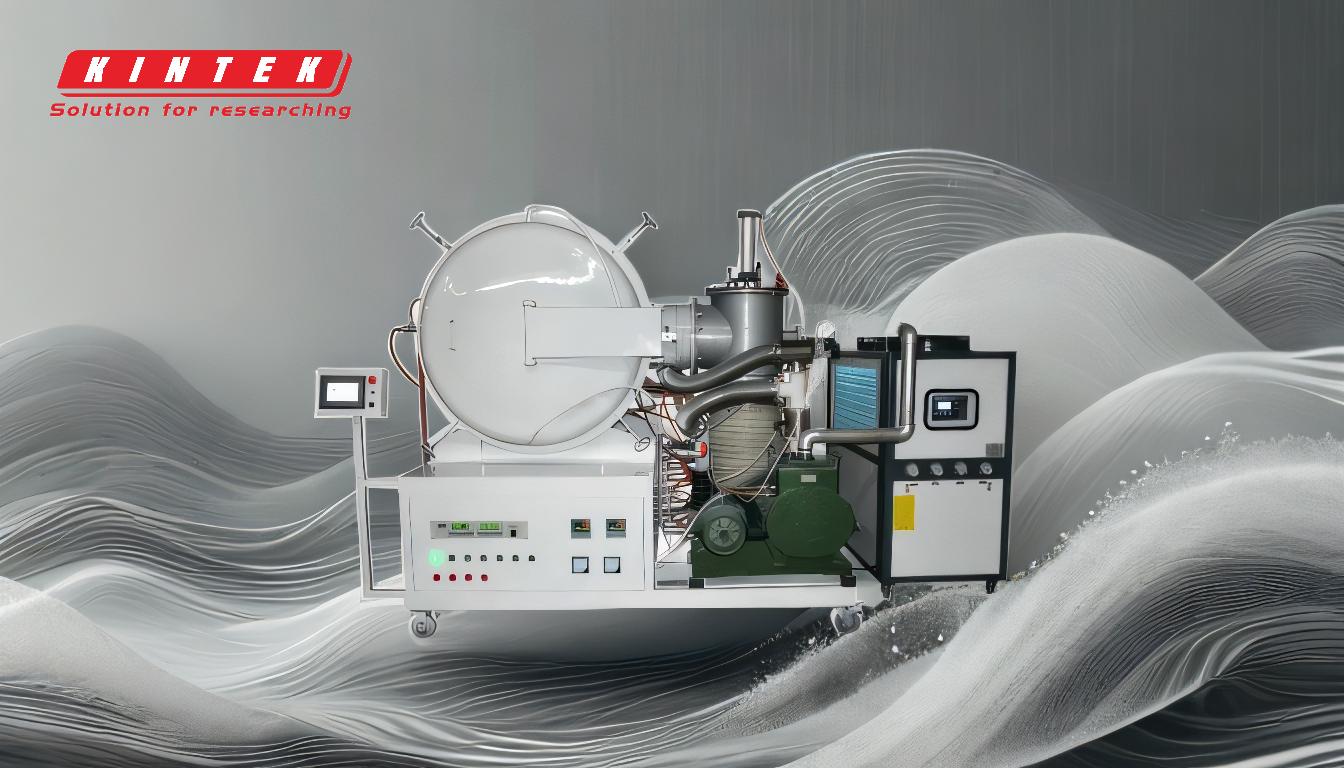
-
Mechanismus der Heizung:
-
Widerstandslöten:
- Die Wärme wird erzeugt, indem ein elektrischer Strom durch die Fuge geleitet wird, der einen Widerstand erzeugt und eine örtliche Erwärmung bewirkt.
- Die Wärme konzentriert sich auf die Verbindungsstelle, wodurch die Wärmeeinflusszonen in den umliegenden Bereichen minimiert werden.
-
Induktionslöten:
- Die Wärme wird durch die Induktion von Wirbelströmen im Werkstück mit Hilfe eines magnetischen Wechselfeldes erzeugt.
- Die Erwärmung ist gleichmäßiger und kann tiefer in das Material eindringen, wodurch sie sich für größere oder komplexere Teile eignet.
-
Widerstandslöten:
-
Energie-Effizienz:
-
Widerstandslöten:
- Äußerst energieeffizient für kleine, örtlich begrenzte Fugen durch direkte Wärmeerzeugung an der Fuge.
- Erfordert eine präzise Steuerung von Strom und Druck, um Überhitzung oder unzureichende Erwärmung zu vermeiden.
-
Induktionslöten:
- Energieeffizienter für größere Teile oder Großserienproduktion, da das Werkstück direkt und ohne nennenswerte Energieverluste erhitzt wird.
- Schnellere Aufheizraten reduzieren den Gesamtenergieverbrauch für sich wiederholende Aufgaben.
-
Widerstandslöten:
-
Kontrolle und Präzision:
-
Widerstandslöten:
- Bietet eine hervorragende Kontrolle über den Erhitzungsprozess und ist daher ideal für empfindliche oder präzise Arbeiten.
- Erfordert eine sorgfältige Ausrichtung der Elektroden und gleichmäßigen Druck, um eine korrekte Verbindungsbildung zu gewährleisten.
-
Induktionslöten:
- Ermöglicht eine schnelle und gleichmäßige Erwärmung, aber die Steuerung hängt stärker von der Konstruktion der Induktionsspule und den Frequenzeinstellungen ab.
- Geeignet für automatisierte oder Hochgeschwindigkeits-Produktionslinien.
-
Widerstandslöten:
-
Anwendungen:
-
Widerstandslöten:
- Häufig verwendet für kleine Komponenten, wie elektrische Kontakte, Schmuck oder medizinische Geräte.
- Ideal für Anwendungen, die eine örtlich begrenzte Erwärmung und minimale thermische Verformung erfordern.
-
Induktionslöten:
- Weit verbreitet in der Automobilindustrie, der Luft- und Raumfahrt und der industriellen Fertigung für größere oder komplexere Baugruppen.
- Geeignet für Großserienproduktion und Teile mit komplizierten Geometrien.
-
Widerstandslöten:
-
Ausrüstung und Einrichtung:
-
Widerstandslöten:
- Für die Anwendung von Druck und Strom sind spezielle Elektroden und Vorrichtungen erforderlich.
- Die Ausrüstung ist im Allgemeinen einfacher und kostengünstiger als bei Induktionssystemen.
-
Induktionslöten:
- Erfordert eine Induktionsspule und eine Stromversorgung, die komplexer und kostspieliger sein können.
- Bietet größere Flexibilität bei der Spulenkonstruktion zur Anpassung an unterschiedliche Teileformen und -größen.
-
Widerstandslöten:
-
Kompatibilität der Materialien:
-
Widerstandslöten:
- Gut geeignet für leitende Materialien wie Kupfer, Messing und Stahl.
- Begrenzt durch die Notwendigkeit eines direkten elektrischen Kontakts mit dem Werkstück.
-
Induktionslöten:
- Kompatibel mit einer breiteren Palette von Materialien, einschließlich nichtleitender oder niedrig leitender Metalle bei Verwendung von Suszeptoren.
- Kann Materialien mit unterschiedlichen thermischen und elektrischen Eigenschaften verarbeiten.
-
Widerstandslöten:
-
Vorteile und Beschränkungen:
-
Widerstandslöten:
- Vorteile: Präzise Steuerung, örtlich begrenzte Erwärmung und minimale Wärmeeinflusszonen.
- Beschränkungen: Begrenzt auf kleine oder einfache Verbindungen, erfordert direkten elektrischen Kontakt und ist langsamer für die Produktion großer Mengen.
-
Induktionslöten:
- Vorteile: Schnelle Erwärmung, geeignet für komplexe Geometrien und skalierbar für die Großserienproduktion.
- Beschränkungen: Höhere Anschaffungskosten, erfordert sorgfältige Spulenkonstruktion und ist möglicherweise nicht ideal für sehr kleine oder empfindliche Teile.
-
Widerstandslöten:
Durch das Verständnis dieser Unterschiede können Käufer von Geräten und Verbrauchsmaterialien fundierte Entscheidungen darüber treffen, welches Lötverfahren für ihre spezifischen Anwendungsanforderungen am besten geeignet ist.
Zusammenfassende Tabelle:
Aspekt | Widerstandslöten | Induktionslöten |
---|---|---|
Mechanismus der Heizung | Wärme, die durch den elektrischen Widerstand an der Verbindungsstelle entsteht. | Durch elektromagnetische Induktion im Werkstück erzeugte Wärme. |
Energie-Effizienz | Äußerst effizient für kleine, lokalisierte Fugen. | Effizient für größere Teile oder Großserienproduktion. |
Kontrolle und Präzision | Hervorragende Kontrolle bei feinen oder präzisen Arbeiten. | Schnelle Erwärmung, geeignet für die automatisierte oder Hochgeschwindigkeits-Produktion. |
Anwendungen | Kleinteile (z. B. elektrische Kontakte, Schmuck). | Größere oder komplexe Baugruppen (z. B. in der Automobil-, Luft- und Raumfahrtindustrie). |
Ausrüstung und Einrichtung | Einfachere und billigere Ausrüstung. | Komplexere und kostspieligere Geräte mit flexiblen Spulenausführungen. |
Kompatibilität der Materialien | Arbeitet mit leitenden Materialien (z. B. Kupfer, Messing). | Kompatibel mit einer breiteren Palette von Materialien, einschließlich nicht leitender Metalle. |
Vorteile | Präzise Steuerung, lokalisierte Heizung, minimale Wärmeeinflusszonen. | Schnelle Erwärmung, skalierbar für Großserienproduktion, geeignet für komplexe Geometrien. |
Beschränkungen | Begrenzt auf kleine Verbindungen, erfordert direkten elektrischen Kontakt. | Höhere Anschaffungskosten, erfordert eine sorgfältige Auslegung der Spule. |
Sind Sie noch unsicher, welches Lötverfahren für Ihre Anwendung am besten geeignet ist? Kontaktieren Sie unsere Experten noch heute für eine persönliche Beratung!