Sputtern und Pulsed Laser Deposition (PLD) sind beides Verfahren der physikalischen Gasphasenabscheidung (PVD), die zur Herstellung dünner Schichten eingesetzt werden, sich aber in ihren Mechanismen, Anwendungen und Ergebnissen deutlich unterscheiden.Beim Sputtern werden energiereiche Ionen verwendet, um Atome aus einem Zielmaterial auszustoßen, die sich dann auf einem Substrat ablagern.Da dieses Verfahren ohne Wärmezufuhr auskommt, eignet es sich für Anwendungen bei niedrigen Temperaturen und für eine breite Palette von Materialien, darunter Kunststoffe und organische Stoffe.Beim PLD-Verfahren hingegen wird mit einem hochenergetischen Laserpuls Material von einem Ziel abgetragen, wodurch eine Plasmafahne entsteht, die sich auf dem Substrat ablagert.PLD ist für seine Fähigkeit bekannt, die Stöchiometrie des Zielmaterials beizubehalten, wodurch es sich ideal für komplexe Materialien wie Oxide eignet und eine präzise Kontrolle über die Mikrostruktur des Films ermöglicht.Beide Verfahren bieten je nach den spezifischen Anforderungen der Dünnschichtanwendung einzigartige Vorteile.
Die wichtigsten Punkte werden erklärt:
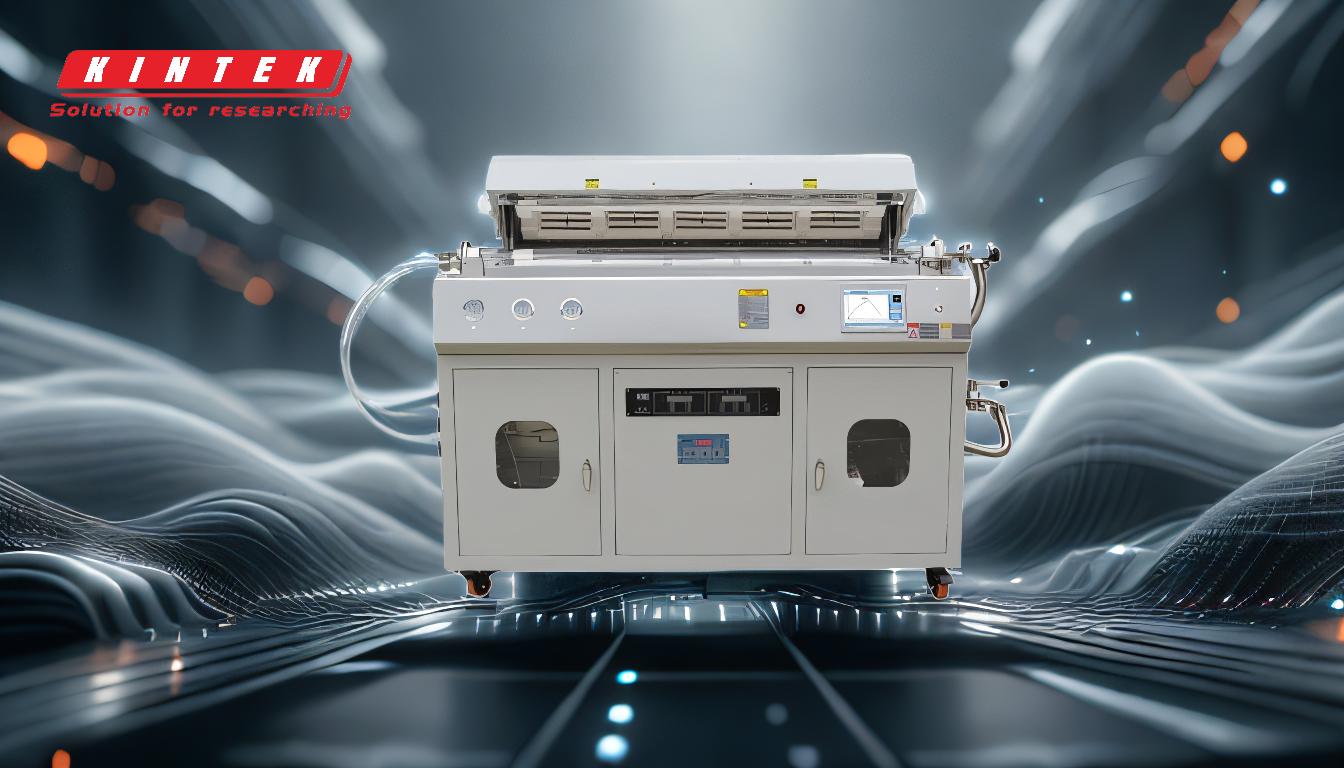
-
Mechanismus des Materialauswurfs:
- Sputtern: Beim Sputtern wird ein Plasma zwischen dem Targetmaterial und dem Substrat erzeugt.Die energiereichen Ionen des Plasmas beschießen das Target und bewirken, dass Atome durch Impulsübertragung herausgeschleudert werden.Bei diesem Verfahren wird das Targetmaterial nicht geschmolzen, weshalb es sich für Materialien eignet, die empfindlich auf hohe Temperaturen reagieren.
- PLD: Beim PLD wird ein hochenergetischer Laserpuls verwendet, um Material vom Target abzutragen.Der Laserimpuls erzeugt eine Plasmastrahlung aus Ionen, Atomen und Molekülen aus dem Target, die dann auf dem Substrat kondensiert.Diese Methode ist hochpräzise und kann so gesteuert werden, dass bestimmte Schichteigenschaften erzielt werden.
-
Temperaturanforderungen:
- Sputtern: Das Sputtern kann bei relativ niedrigen Temperaturen durchgeführt werden, was für die Beschichtung temperaturempfindlicher Materialien wie Kunststoffe und organische Stoffe von Vorteil ist.Das Verfahren beruht nicht auf thermischer Verdampfung, wodurch das Risiko einer thermischen Schädigung des Substrats verringert wird.
- PLD: PLD ermöglicht ebenfalls die Abscheidung bei niedrigen Substrattemperaturen, aber der Laserabtragungsprozess selbst kann örtlich hohe Temperaturen erzeugen.Die Gesamttemperatur des Substrats bleibt jedoch niedrig, so dass es sich für empfindliche Materialien eignet.
-
Stöchiometrie und Filmzusammensetzung:
- Sputtern: Durch Sputtern können zwar qualitativ hochwertige Schichten hergestellt werden, doch kann es schwierig sein, die genaue Stöchiometrie komplexer Materialien (z. B. Mehrkomponenten-Oxide) einzuhalten.Das Verfahren kann zu geringfügigen Abweichungen in der Zusammensetzung führen, die auf Unterschiede in der Sputterausbeute der einzelnen Elemente zurückzuführen sind.
- PLD: Einer der Hauptvorteile von PLD ist die Fähigkeit, die Stöchiometrie des Zielmaterials in der abgeschiedenen Schicht beizubehalten.Dies ist besonders wichtig für komplexe Materialien, bei denen eine genaue Kontrolle der Zusammensetzung erforderlich ist.PLD wird häufig für die Abscheidung von Oxiden, Nitriden und anderen Mehrkomponentenmaterialien eingesetzt.
-
Film-Mikrostruktur und Korngröße:
- Sputtern: Beim Sputtern entstehen in der Regel Schichten mit kleineren Korngrößen und gleichmäßigeren Mikrostrukturen.Das Verfahren ermöglicht eine gute Kontrolle über die Homogenität und Haftung der Schichten und eignet sich daher für Anwendungen, die dichte, gut haftende Schichten erfordern.
- PLD: PLD bietet eine hervorragende Kontrolle über Korngröße und Mikrostruktur und ermöglicht die Abscheidung von Schichten mit spezifischen strukturellen Eigenschaften.Dies macht PLD ideal für Forschungsanwendungen, bei denen die Untersuchung der Beziehungen zwischen Mikrostruktur und Eigenschaften wichtig ist.
-
Abscheiderate und Effizienz:
- Sputtern: Die Abscheiderate beim Sputtern kann je nach Zielmaterial und Prozessbedingungen variieren.Bei reinen Metallen kann die Rate relativ hoch sein, bei komplexen Materialien kann sie jedoch niedriger sein.Sputtern ist im Allgemeinen effizient für großflächige Beschichtungen und industrielle Anwendungen.
- PLD: PLD hat in der Regel eine geringere Abscheiderate als das Sputtern, insbesondere bei großflächigen Beschichtungen.Es zeichnet sich jedoch durch Präzision und Kontrolle aus und eignet sich daher besser für Forschungszwecke und kleinere Anwendungen, bei denen die Qualität der Schichten von größter Bedeutung ist.
-
Anwendungen und Materialkompatibilität:
- Sputtern: Das Sputtern ist in der Industrie für die Beschichtung einer Vielzahl von Materialien weit verbreitet, darunter Metalle, Halbleiter und Isolatoren.Es ist besonders effektiv für Anwendungen, die eine gute Haftung und Gleichmäßigkeit erfordern, wie z. B. bei der Herstellung von optischen Beschichtungen, harten Schichten und elektronischen Geräten.
- PLD: PLD wird häufig in der Forschung und für spezielle Anwendungen eingesetzt, bei denen eine präzise Kontrolle der Schichtzusammensetzung und Mikrostruktur erforderlich ist.Es eignet sich besonders gut für die Abscheidung komplexer Materialien wie Hochtemperatursupraleiter, ferroelektrische Schichten und Mehrkomponenten-Oxide.
-
Vakuum-Anforderungen:
- Sputtern: Im Vergleich zu anderen PVD-Verfahren wie der E-Beam-Verdampfung wird beim Sputtern in der Regel mit einem niedrigeren Vakuum gearbeitet.Dies kann für bestimmte Anwendungen von Vorteil sein, bei denen die Aufrechterhaltung eines hohen Vakuums eine Herausforderung darstellt.
- PLD: PLD erfordert in der Regel eine Hochvakuumumgebung, um die Reinheit und Qualität der abgeschiedenen Schichten zu gewährleisten.Das Hochvakuum trägt dazu bei, die Verunreinigung zu minimieren, und ermöglicht eine bessere Kontrolle des Abscheidungsprozesses.
Zusammenfassend lässt sich sagen, dass sowohl das Sputtern als auch das PLD PVD-Verfahren für die Dünnschichtabscheidung sind. Sie unterscheiden sich jedoch in ihren Mechanismen, Temperaturanforderungen, der Fähigkeit, die Stöchiometrie aufrechtzuerhalten, der Kontrolle über die Mikrostruktur, den Abscheideraten und den Anwendungen.Das Sputtern ist vielseitiger für industrielle Anwendungen und großflächige Beschichtungen, während das PLD-Verfahren eine höhere Präzision und Kontrolle bietet und damit ideal für Forschung und Spezialanwendungen ist.
Zusammenfassende Tabelle:
Blickwinkel | Sputtern | PLD |
---|---|---|
Mechanismus | Energetische Ionen stoßen durch Impulsübertragung Atome aus einem Ziel aus. | Hochenergetische Laserpulse tragen das Material ab und erzeugen eine Plasmafahne. |
Temperatur | Niedrigtemperaturverfahren, geeignet für wärmeempfindliche Materialien. | Niedrige Substrattemperatur, aber lokal hohe Temperaturen während des Abtrags. |
Stöchiometrie | Anspruchsvoll bei komplexen Materialien; leichte Abweichungen können auftreten. | Behält die Stöchiometrie des Zielmaterials bei, ideal für komplexe Oxide. |
Mikrostruktur | Kleinere Korngrößen, gleichmäßige Filme, gute Haftung. | Genaue Kontrolle über Korngröße und Mikrostruktur. |
Abscheiderate | Hoch für Metalle, niedriger für komplexe Materialien; effizient für große Flächen. | Geringere Abscheidungsrate, besser geeignet für Präzisions- und Kleinserienanwendungen. |
Anwendungen | Industrielle Beschichtungen, optische Filme, Elektronik. | Forschung, Hochtemperatursupraleiter, ferroelektrische Schichten. |
Vakuum-Anforderungen | Niedrigeres Vakuum, leichter zu halten. | Höheres Vakuum für Reinheit und Qualitätskontrolle. |
Benötigen Sie Hilfe bei der Auswahl des richtigen Verfahrens zur Dünnschichtabscheidung? Kontaktieren Sie noch heute unsere Experten für eine maßgeschneiderte Beratung!