Die Sintertemperatur spielt eine entscheidende Rolle bei der Bestimmung der Dichte und Härte eines gesinterten Materials.Optimale Sintertemperaturen gewährleisten maximale Dichte und Härte, indem sie die Porosität minimieren und ein gleichmäßiges Kornwachstum fördern.Abweichungen vom idealen Temperaturbereich können zu Defekten wie übermäßigem Kornwachstum oder unzureichender Verdichtung führen, die die Materialeigenschaften beeinträchtigen.So wird beispielsweise beim Sintern von Zirkoniumdioxid bei etwa 1500℃ die Festigkeit maximiert, während Abweichungen von 150℃ über oder unter dieser Temperatur die Festigkeit aufgrund von Kornwachstum erheblich verringern können.Darüber hinaus beeinflussen auch die Sinteratmosphäre und die Sinterzeit diese Eigenschaften, da ungeeignete Bedingungen zu Oxidation oder unvollständiger Verdichtung führen können.
Die wichtigsten Punkte erklärt:
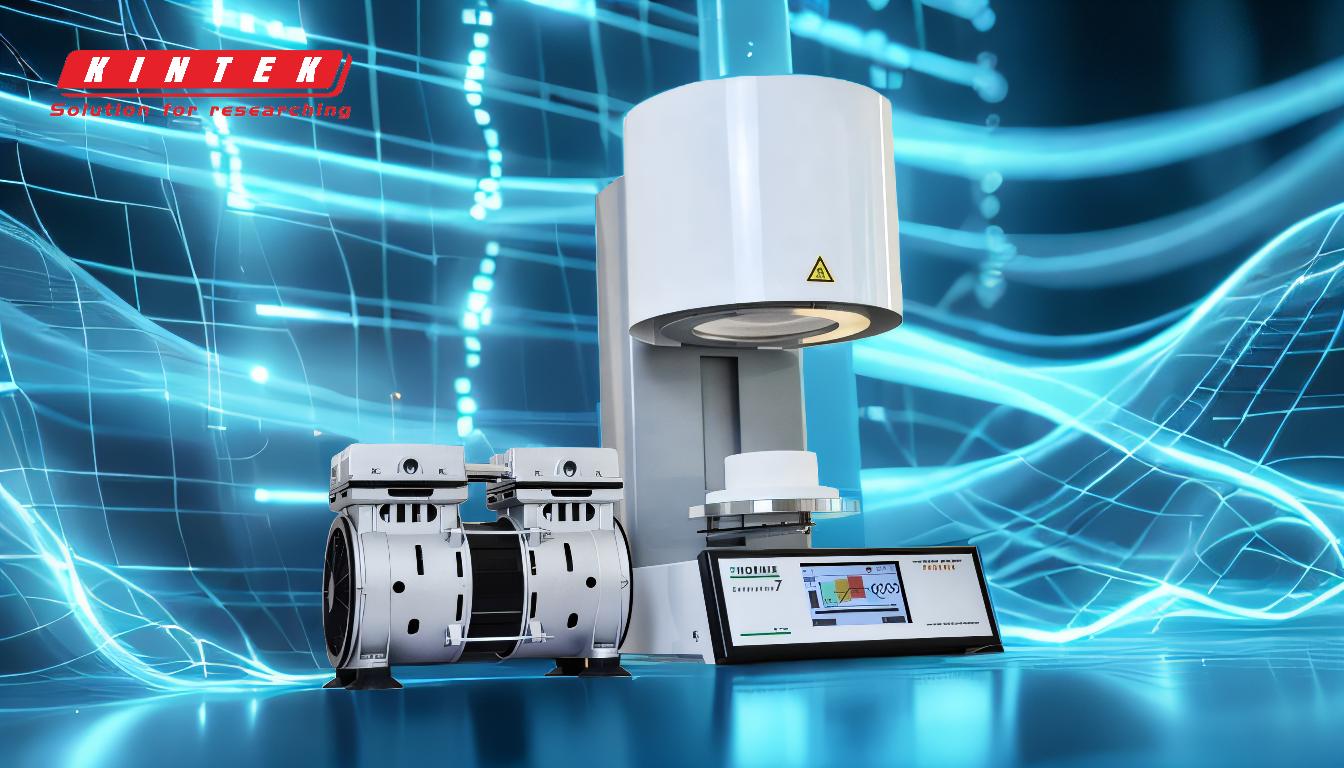
-
Optimale Sintertemperatur für Dichte und Härte:
- Das Sintern bei der richtigen Temperatur gewährleistet eine maximale Verdichtung, verringert die Porosität und erhöht die Härte.
- Bei Materialien wie Zirkoniumdioxid ist eine bestimmte Temperatur (z. B. 1500 °C) entscheidend, um die gewünschten Eigenschaften zu erzielen.Abweichungen von dieser Temperatur können zu Kornwachstum führen, wodurch sich Festigkeit und Härte verringern.
-
Auswirkung von hohen Sintertemperaturen:
- Zu hohe Sintertemperaturen können ein übermäßiges Wachstum der Körner verursachen, was zu einem gröberen Gefüge führt.
- Dieses Kornwachstum erhöht die Porosität und verringert die Gesamtdichte und -härte des Materials.
- Bei hohen Temperaturen können auch Defekte wie Risse oder Hohlräume entstehen, die die Materialeigenschaften weiter verschlechtern.
-
Auswirkung von niedrigen Sintertemperaturen:
- Unzureichende Sintertemperaturen führen zu einer unvollständigen Verdichtung, wodurch das Material eine höhere Porosität aufweist.
- Niedrige Temperaturen verhindern eine ordnungsgemäße Bindung zwischen den Partikeln, was zu schwächeren mechanischen Eigenschaften und geringerer Härte führt.
- Das Material erreicht möglicherweise nicht die gewünschte Festigkeit oder Haltbarkeit und ist daher für Hochleistungsanwendungen ungeeignet.
-
Die Rolle der Sinterzeit:
- Längere Sinterzeiten bei hohen Temperaturen können das Kornwachstum und die Defektbildung verschlimmern und die Dichte und Härte verringern.
- Unzureichende Sinterzeiten ermöglichen möglicherweise keine vollständige Verdichtung, was zu suboptimalen Materialeigenschaften führt.
- Die Abstimmung von Sinterzeit und Temperatur ist entscheidend für das Erreichen des gewünschten Gefüges und der gewünschten Eigenschaften.
-
Einfluss der Sinteratmosphäre:
- Die Sinteratmosphäre (z. B. reduzierend, oxidierend oder inert) beeinflusst die endgültigen Eigenschaften des Materials.
- Eine reduzierende Atmosphäre verhindert Oxidation und ermöglicht den Abbau von Oberflächenoxiden, was die Verdichtung fördert und die Härte verbessert.
- Eine ungeeignete Atmosphäre kann zu Oxidation oder Verunreinigung führen, was sich negativ auf Dichte und Härte auswirkt.
-
Mikrostrukturelle Veränderungen während des Sinterns:
- Das Sintern wirkt sich direkt auf die Korngröße, die Porengröße und die Verteilung der Korngrenzen im Mikrogefüge des Materials aus.
- Kleinere, gleichmäßige Körner und minimale Porosität tragen zu einer höheren Dichte und Härte bei.
- Übermäßiges Kornwachstum oder eine unregelmäßige Porenverteilung schwächen das Material und verringern seine mechanischen Eigenschaften.
-
Praktische Implikationen für die Materialauswahl:
- Das Verständnis des Verhältnisses zwischen Sintertemperatur, Dichte und Härte ist für die Auswahl des richtigen Materials für bestimmte Anwendungen unerlässlich.
- Für hochfeste und langlebige Komponenten ist eine präzise Steuerung der Sinterbedingungen erforderlich, um optimale Eigenschaften zu erzielen.
- Abweichungen von den idealen Sinterparametern können zu Materialversagen oder verminderter Leistung in anspruchsvollen Umgebungen führen.
Durch die sorgfältige Kontrolle von Sintertemperatur, -zeit und -atmosphäre können Hersteller die Dichte und Härte von Sinterwerkstoffen optimieren und sicherstellen, dass sie die erforderlichen Leistungsstandards für ihre vorgesehenen Anwendungen erfüllen.
Zusammenfassende Tabelle:
Faktor | Einfluss auf Dichte und Härte |
---|---|
Optimale Temperatur | Sorgt für maximale Verdichtung, reduziert die Porosität und erhöht die Härte. |
Hohe Temperatur | Verursacht übermäßiges Kornwachstum, erhöht die Porosität und verringert Dichte und Härte. |
Niedrige Temperatur | Führt zu unvollständiger Verdichtung, höherer Porosität und schwächeren mechanischen Eigenschaften. |
Sinterzeit | Verlängerte Zeiten bei hohen Temperaturen verschlechtern das Kornwachstum; unzureichende Zeiten behindern die Verdichtung. |
Sinteratmosphäre | Reduzierende Atmosphären fördern die Verdichtung; ungeeignete Atmosphären verursachen Oxidation oder Defekte. |
Mikrostrukturelle Veränderungen | Kleinere, gleichmäßige Körner und minimale Porosität erhöhen Dichte und Härte. |
Benötigen Sie Hilfe bei der Optimierung der Sinterbedingungen für Ihre Materialien? Kontaktieren Sie noch heute unsere Experten !