Die Kalzinierung ist ein thermischer Behandlungsprozess, bei dem ein Material auf hohe Temperaturen, in der Regel unterhalb seines Schmelzpunktes, erhitzt wird, um eine thermische Zersetzung, einen Phasenübergang oder die Entfernung flüchtiger Bestandteile zu bewirken.Die Temperatur spielt bei der Kalzinierung eine entscheidende Rolle, da sie die Reaktionskinetik, die Phasenumwandlungen und die endgültigen Eigenschaften des kalzinierten Materials direkt beeinflusst.Die Auswirkungen der Temperatur auf die Kalzinierung lassen sich wie folgt zusammenfassen: Höhere Temperaturen beschleunigen im Allgemeinen den Kalzinierungsprozess, fördern die Entfernung flüchtiger Bestandteile und erleichtern Phasenübergänge.Zu hohe Temperaturen können jedoch zu unerwünschten Ergebnissen wie Sinterung, Verlust der Oberfläche oder sogar Zersetzung des gewünschten Produkts führen.Die optimale Temperatur für die Kalzinierung hängt von dem jeweiligen Material und dem Verwendungszweck ab.
Die wichtigsten Punkte werden erklärt:
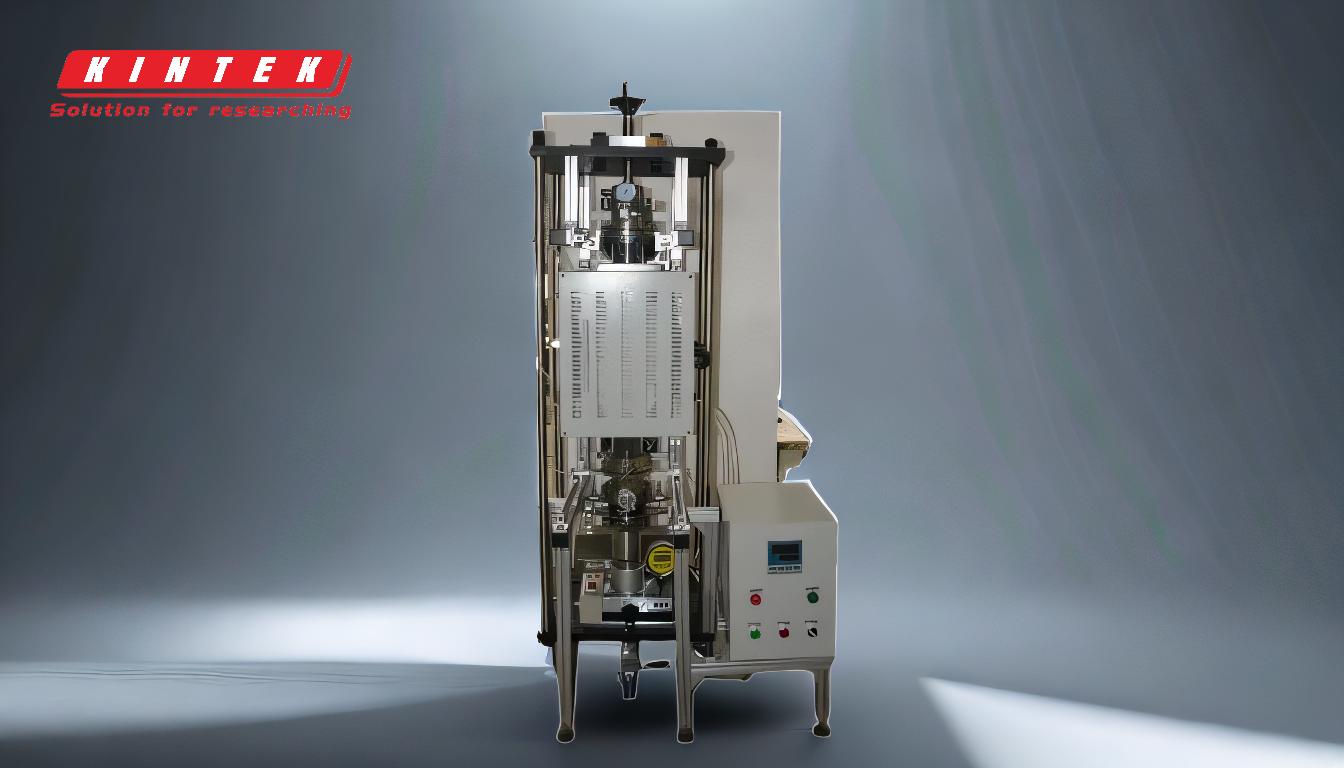
-
Beschleunigung der Reaktionskinetik:
- Die Temperatur ist ein Schlüsselfaktor bei der Bestimmung der Geschwindigkeit von Kalzinierungsreaktionen.Nach der Arrhenius-Gleichung nehmen die Reaktionsgeschwindigkeiten exponentiell mit der Temperatur zu.
- Bei der Kalzinierung von Kalkstein (CaCO₃ → CaO + CO₂) beispielsweise verkürzen höhere Temperaturen die für die vollständige Zersetzung erforderliche Zeit erheblich.
- Diese Beschleunigung ist entscheidend für industrielle Prozesse, bei denen Effizienz und Durchsatz eine wichtige Rolle spielen.
-
Entfernung von flüchtigen Bestandteilen:
- Die Kalzinierung wird häufig eingesetzt, um flüchtige Bestandteile wie Wasser, Kohlendioxid oder organische Stoffe aus einem Material zu entfernen.
- Höhere Temperaturen verstärken die Verflüchtigung dieser Bestandteile und gewährleisten ihre vollständige Entfernung.Bei der Kalzinierung von Gips (CaSO₄-2H₂O → CaSO₄ + 2H₂O) beispielsweise werden die Wassermoleküle durch höhere Temperaturen besser ausgetrieben.
- Die Temperatur muss jedoch sorgfältig kontrolliert werden, um einen übermäßigen Energieverbrauch oder eine Beschädigung des Materials zu vermeiden.
-
Phasenübergänge und Kristallisation:
- Die Temperatur beeinflusst die Phasenübergänge und das Kristallisationsverhalten von Materialien während der Kalzinierung.
- Bei der Kalzinierung von Aluminiumoxid (Al(OH)₃ → Al₂O₃) beispielsweise sind bestimmte Temperaturbereiche erforderlich, um gewünschte kristalline Phasen wie γ-Al₂O₃ oder α-Al₂O₃ zu erreichen.
- Die Wahl der Temperatur kann die endgültigen Eigenschaften des Materials, wie Oberfläche, Porosität und mechanische Festigkeit, bestimmen.
-
Risiko der Sinterung und Agglomeration:
- Höhere Temperaturen können zwar die Kalzinierung verbessern, aber sie erhöhen auch das Risiko des Sinterns, bei dem die Partikel miteinander verschmelzen und so die Oberfläche und Porosität verringern.
- Das Sintern kann sich negativ auf die Leistung von Materialien in Anwendungen wie Katalyse oder Adsorption auswirken, wo eine große Oberfläche entscheidend ist.
- Daher muss die Temperatur optimiert werden, um die Vorteile der Kalzinierung mit den Risiken der Sinterung in Einklang zu bringen.
-
Energieeffizienz und Kostenüberlegungen:
- Höhere Temperaturen erfordern mehr Energie, was die Betriebskosten erhöhen kann.
- Energieeffiziente Kalzinierungsverfahren beinhalten häufig die Optimierung des Temperaturprofils, um den Energieverbrauch zu minimieren und gleichzeitig die gewünschten Materialeigenschaften zu erzielen.
- So kann beispielsweise das Vorheizen des Materials oder der Einsatz von Abwärmerückgewinnungssystemen die Gesamteffizienz verbessern.
-
Materialspezifische Effekte:
-
Die Auswirkung der Temperatur auf die Kalzinierung ist je nach dem zu verarbeitenden Material unterschiedlich.Zum Beispiel:
- Bei der Kalzinierung von Kaolin (Al₂Si₂O₅(OH)₄ → Al₂O₃-2SiO₂ + 2H₂O) führen höhere Temperaturen zur Bildung von Metakaolin, das in Zement und Keramiken verwendet wird.
- Bei der Kalzinierung von Metalloxiden ist die Temperaturkontrolle von entscheidender Bedeutung, um eine übermäßige Reduktion oder Oxidation zu vermeiden, die die Eigenschaften des Materials verändern kann.
- Die Kenntnis des spezifischen thermischen Verhaltens des Materials ist für die Optimierung des Kalzinierungsprozesses unerlässlich.
-
Die Auswirkung der Temperatur auf die Kalzinierung ist je nach dem zu verarbeitenden Material unterschiedlich.Zum Beispiel:
-
Auswirkungen auf die Eigenschaften des Endprodukts:
- Die Temperatur während der Kalzinierung wirkt sich direkt auf die endgültigen Eigenschaften des Produkts aus, z. B. auf die Partikelgröße, die Morphologie und die chemische Zusammensetzung.
- Bei der Herstellung von Katalysatoren zum Beispiel bestimmt die Kalzinierungstemperatur die aktive Oberfläche und die Stabilität des Katalysators.
- Bei der Herstellung von Keramik beeinflusst die Temperatur die Dichte, die Härte und die thermische Stabilität des Endprodukts.
-
Thermische Zersetzung und Stabilität:
- Einige Materialien können sich bei hohen Temperaturen thermisch zersetzen, was zur Bildung unerwünschter Nebenprodukte oder zum Verlust der gewünschten Eigenschaften führt.
- Bei der Kalzinierung von Karbonaten zum Beispiel können zu hohe Temperaturen zur Bildung von Sekundäroxiden oder Verunreinigungen führen.
- Eine sorgfältige Temperaturkontrolle ist notwendig, um die Stabilität und Reinheit des Endprodukts zu gewährleisten.
Zusammenfassend lässt sich sagen, dass die Temperatur ein entscheidender Parameter bei der Kalzinierung ist, der die Reaktionsgeschwindigkeit, die Phasenübergänge und die endgültigen Materialeigenschaften beeinflusst.Höhere Temperaturen können zwar die Effizienz und Effektivität der Kalzinierung verbessern, müssen aber sorgfältig kontrolliert werden, um nachteilige Auswirkungen wie Versinterung, Energieineffizienz oder Materialzersetzung zu vermeiden.Die optimale Temperatur für die Kalzinierung hängt von dem jeweiligen Material und der beabsichtigten Anwendung ab und erfordert ein gründliches Verständnis des thermischen Verhaltens des Materials und der Prozessanforderungen.
Zusammenfassende Tabelle:
Schlüsselfaktor | Einfluss der Temperatur |
---|---|
Reaktionskinetik | Höhere Temperaturen beschleunigen die Reaktionen und verkürzen die Zersetzungszeit. |
Beseitigung flüchtiger Bestandteile | Erhöhte Temperaturen verbessern die Verflüchtigung zur vollständigen Entfernung von Wasser, CO₂ usw. |
Phasenübergänge | Zum Erreichen der gewünschten kristallinen Phasen (z. B. γ-Al₂O₃) sind bestimmte Temperaturen erforderlich. |
Risiken bei der Sinterung | Übermäßige Hitze kann zum Schmelzen der Partikel führen, wodurch sich Oberfläche und Porosität verringern. |
Energie-Effizienz | Höhere Temperaturen erhöhen die Energiekosten; Optimierung ist der Schlüssel zur Kosteneffizienz. |
Materialspezifische Auswirkungen | Die Temperaturauswirkungen variieren je nach Material (z. B. Kaolin, Metalloxide). |
Eigenschaften des Endprodukts | Die Temperatur bestimmt die Partikelgröße, Morphologie und chemische Zusammensetzung. |
Thermische Zersetzung | Eine Überhitzung kann zu unerwünschten Nebenprodukten oder zum Verlust der gewünschten Eigenschaften führen. |
Benötigen Sie Hilfe bei der Optimierung Ihres Kalzinierungsprozesses? Kontaktieren Sie noch heute unsere Experten für maßgeschneiderte Lösungen!