Die höchste Sintertemperatur kann je nach dem zu verarbeitenden Material, den gewünschten Eigenschaften des Endprodukts und der Art des verwendeten Sinterofens erheblich variieren.Ausgehend von den angegebenen Referenzen können die Sintertemperaturen von 1120°C bis 1800°C reichen.Die maximale Betriebstemperatur für Standard-Sinteröfen beträgt in der Regel bis zu 1120 °C, während spezielle Sinteröfen Temperaturen von 1288 °C/2350 °F erreichen können.In Versuchen wurden Sintertemperaturen von bis zu 1800°C verwendet.Die Wahl der Temperatur wird von Faktoren wie der Materialzusammensetzung, der Partikelgröße, der erforderlichen Dichte und den gewünschten mechanischen Eigenschaften des Endprodukts beeinflusst.
Die wichtigsten Punkte werden erklärt:
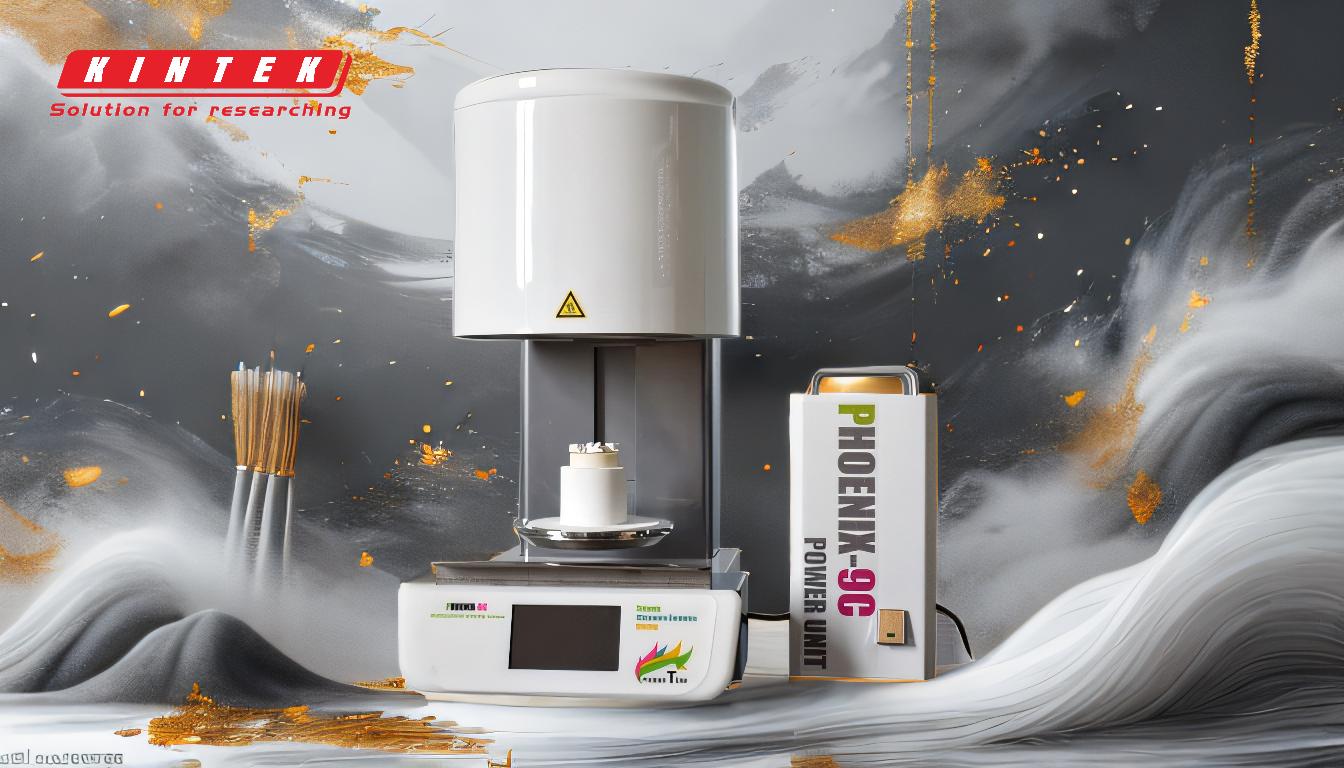
-
Bereich der Sintertemperaturen:
- Die Sintertemperaturen können je nach Material und Anwendung stark variieren.Standard-Sinteröfen arbeiten in der Regel bei bis zu 1120 °C, während spezielle Öfen 1288 °C/2350 °F erreichen können.Unter experimentellen Bedingungen wurden Temperaturen von bis zu 1800°C verwendet.
- Warum das wichtig ist:Der Temperaturbereich ist entscheidend, da er sich direkt auf die Dichte, Festigkeit und andere mechanische Eigenschaften des Sinterprodukts auswirkt.Höhere Temperaturen führen im Allgemeinen zu einer besseren Verdichtung und verbesserten mechanischen Eigenschaften, müssen aber gegen Materialbeschränkungen und Energiekosten abgewogen werden.
-
Faktoren, die die Sintertemperatur beeinflussen:
- Materialzusammensetzung:Verschiedene Materialien haben unterschiedliche Schmelzpunkte und ein unterschiedliches Sinterverhalten.So benötigen beispielsweise Keramiken und Metalle unterschiedliche Temperaturbereiche für eine optimale Sinterung.
- Partikelgröße:Feinere Pulver sintern in der Regel bei niedrigeren Temperaturen, da ihre Oberfläche größer ist, was die Partikelbindung verbessert.
- Gewünschte Eigenschaften:Die erforderliche Dichte, Zugfestigkeit und andere mechanische Eigenschaften des Endprodukts beeinflussen die Wahl der Sintertemperatur.
- Atmosphäre:Die Sinteratmosphäre (z. B. Luft, Vakuum, Argon/Stickstoff) kann den Sinterprozess und die maximale Temperatur, die sicher verwendet werden kann, beeinflussen.
- Warum das wichtig ist:Die Kenntnis dieser Faktoren hilft bei der Auswahl der geeigneten Sintertemperatur, um die gewünschten Produkteigenschaften zu erreichen, ohne das Material oder den Ofen zu beschädigen.
-
Vorteile des Hochtemperatursinterns:
- Das Hochtemperatursintern kann die mechanischen Eigenschaften des Endprodukts erheblich verbessern, einschließlich der Zugfestigkeit, der Biegewechselfestigkeit und der Kerbschlagarbeit.
- Warum das wichtig ist:Für Anwendungen, die Hochleistungswerkstoffe erfordern, wie z. B. Bauteile für die Luft- und Raumfahrt oder die Automobilindustrie, ist das Hochtemperatursintern unerlässlich, um die erforderliche Festigkeit und Haltbarkeit zu erreichen.
-
Beschränkungen der Ausrüstung:
- Die maximale Betriebstemperatur von Sinteröfen und Brennöfen ist ein begrenzender Faktor.Standardöfen erreichen in der Regel eine Höchsttemperatur von 1120 °C, während spezielle Öfen bis zu 1288 °C/2350 °F erreichen können.In Versuchsaufbauten können sogar noch höhere Temperaturen erreicht werden, z. B. 1800 °C.
- Warum das wichtig ist:Die Wahl der Anlage ist entscheidend für das Erreichen der gewünschten Sintertemperatur.Der Einsatz von Geräten, die die erforderliche Temperatur nicht erreichen, kann zu suboptimalen Produkteigenschaften führen.
-
Experimentelles vs. industrielles Sintern:
- In Versuchen können die Sintertemperaturen auf extreme Werte wie 1800°C erhöht werden, um die Grenzen der Materialeigenschaften und des Sinterverhaltens zu erforschen.
- Bei industriellen Anwendungen liegt der Schwerpunkt häufig auf der Abwägung von Temperatur, Kosten, Energieeffizienz und Anlagenkapazität, was in der Regel zu niedrigeren Höchsttemperaturen führt.
- Warum das wichtig ist:Experimentelle Daten können als Grundlage für die industrielle Praxis dienen, aber praktische Zwänge begrenzen oft die in der Großproduktion verwendeten Temperaturen.
-
Optimale Parameter für die Sinterung:
- Der optimale Sinterprozess wird durch Parameter wie Temperatur, Druck, durchschnittliche Korngröße und Gasatmosphäre beeinflusst.Höhere Temperaturen und feinere Pulver können die Verdichtung erhöhen, aber die Menge der flüssigen Phase muss sorgfältig kontrolliert werden.
- Warum es wichtig ist:Das richtige Gleichgewicht zwischen diesen Parametern ist entscheidend für die Herstellung hochwertiger Sinterprodukte mit den gewünschten Eigenschaften.
Zusammenfassend lässt sich sagen, dass die höchste Sintertemperatur vom Material, den gewünschten Eigenschaften und der verwendeten Ausrüstung abhängt, wobei Standardöfen bis zu 1120°C, Spezialöfen bis zu 1288°C/2350°F und Versuchsaufbauten bis zu 1800°C erreichen können.Das Verständnis der Faktoren, die die Sintertemperatur beeinflussen, und der Grenzen der verfügbaren Anlagen ist entscheidend für die Auswahl der geeigneten Sinterbedingungen.
Zusammenfassende Tabelle:
Aspekt | Einzelheiten |
---|---|
Standard-Ofenbereich | bis zu 1120°C |
Spezialisierter Ofenbereich | Bis zu 1288°C/2350°F |
Experimenteller Bereich | Bis zu 1800°C |
Wichtige Einflussfaktoren | Materialzusammensetzung, Partikelgröße, gewünschte Eigenschaften, Sinteratmosphäre |
Vorteile von Hochtemperatur | Erhöhte Zugfestigkeit, Biegewechselfestigkeit und Kerbschlagarbeit |
Benötigen Sie Hilfe bei der Auswahl der richtigen Sintertemperatur für Ihre Anwendung? Kontaktieren Sie unsere Experten noch heute!