Der Plasmadruck beim Sputtern liegt in der Regel im Bereich von 5-30 mTorr (Millitorr), je nach den spezifischen Sputtering-Bedingungen und den gewünschten Resultaten.Dieser Druckbereich ist für ein effektives Sputtern von entscheidender Bedeutung, da er sicherstellt, dass die vom Target gesputterten oder reflektierten energiereichen Teilchen durch Gasphasenkollisionen \"thermisiert\" werden, bevor sie das Substrat erreichen.Dieser Thermalisierungsprozess ist für die Steuerung der Energie und der Richtung der abgeschiedenen Teilchen unerlässlich, was sich direkt auf die Qualität und Gleichmäßigkeit der Dünnschicht auswirkt.Der Druck wird in einer Vakuumkammer aufrechterhalten, in der Inertgase wie Argon ionisiert werden, um das für den Sputterprozess erforderliche Plasma zu erzeugen.
Die wichtigsten Punkte werden erklärt:
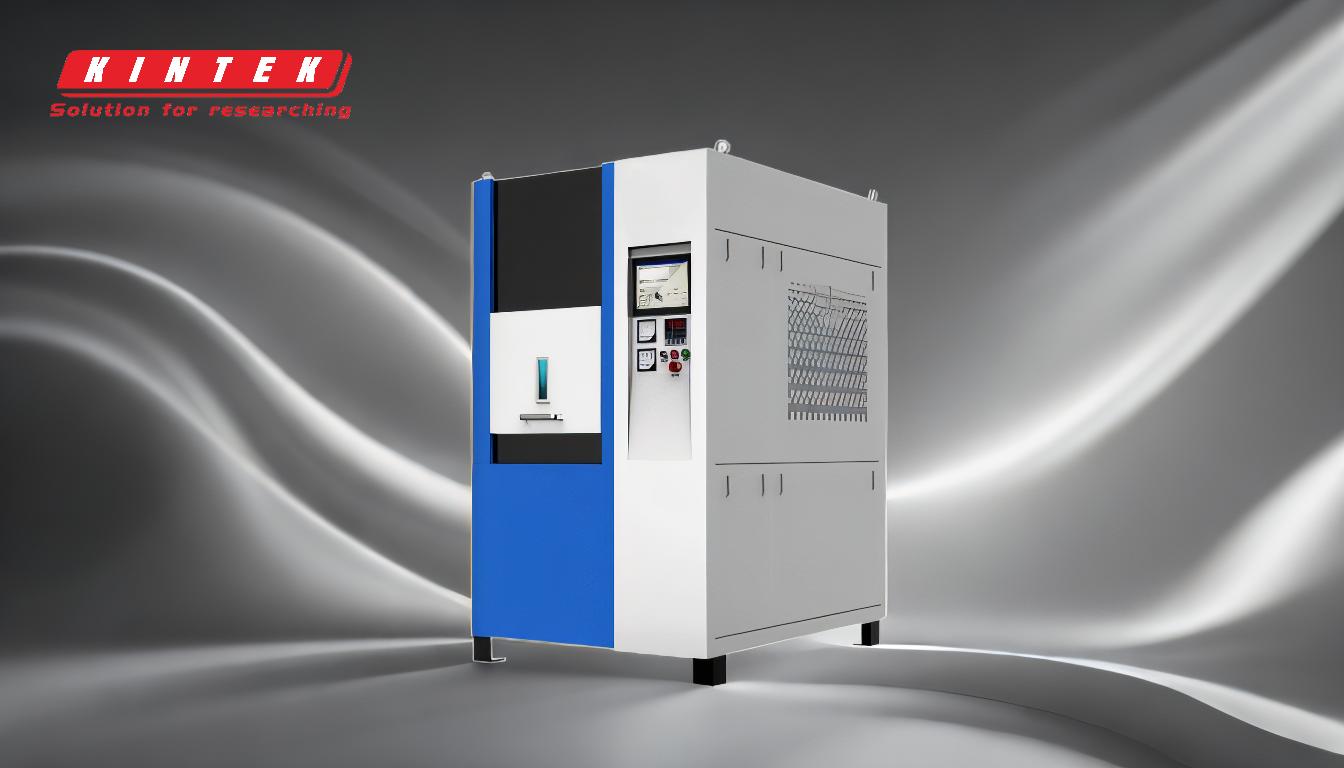
-
Plasmadruckbereich beim Sputtern:
- Der typische Plasmadruck für das Sputtern reicht von 5-30 mTorr .
- Dieser Bereich ist optimal, um zu gewährleisten, dass die gesputterten Partikel durch Zusammenstöße mit Gasatomen thermisiert werden, bevor sie das Substrat erreichen.
- Durch die Thermalisierung wird die kinetische Energie der Teilchen verringert, was eine kontrolliertere und gleichmäßigere Abscheidung ermöglicht.
-
Die Rolle von Inertgas und Plasmabildung:
- Zur Erzeugung des Plasmas werden Inertgase wie Argon in die Vakuumkammer eingeleitet.
- Das Gas wird mit einer Hochspannung (3-5 kV) oder elektromagnetischer Anregung ionisiert, wobei Ar+-Ionen entstehen.
- Diese Ionen werden in Richtung des Targets (Kathode) beschleunigt, wo sie zusammenstoßen und Targetatome ausstoßen, wodurch der Sputterprozess eingeleitet wird.
-
Bedeutung der Vakuumbedingungen:
- Der Sputterprozess beginnt mit der Erzeugung eines Vakuums in der Kammer, typischerweise etwa 1 Pa (0,0000145 psi) , um Feuchtigkeit und Verunreinigungen zu entfernen.
- Um eine Kontamination durch Restgase zu vermeiden, werden zunächst niedrigere Drücke verwendet, bevor Argon bei höheren Drücken eingeführt wird.
-
Thermalisierung von gesputterten Partikeln:
- Bei höheren Gasdrücken (z. B. 5-30 mTorr) stoßen die gesputterten Ionen mit den Gasatomen zusammen, wodurch sie Energie verlieren und sich diffus bewegen.
- Durch diese zufällige Bewegung wird sichergestellt, dass die Partikel das Substrat mit kontrollierter Energie erreichen, wodurch sich die Qualität der Schicht und die Abdeckung verbessern.
-
Einfluss des Drucks auf die Abscheidung:
- Höhere Drücke verbessern die Abdeckung, indem sie sicherstellen, dass die Partikel gleichmäßig über das Substrat verteilt werden.
- Niedrigere Drücke ermöglichen ballistische Stöße mit hoher Energie, was für bestimmte Anwendungen, die eine hochenergetische Abscheidung erfordern, wünschenswert sein kann.
-
Faktoren, die die Sputtering-Ausbeute beeinflussen:
-
Die Sputterausbeute (Anzahl der pro einfallendem Ion ausgestoßenen Zielatome) hängt von folgenden Faktoren ab:
- Energie der einfallenden Ionen.
- Masse der Ionen und der Zielatome.
- Einfallswinkel.
- Diese Faktoren variieren je nach Targetmaterial und Sputterbedingungen.
-
Die Sputterausbeute (Anzahl der pro einfallendem Ion ausgestoßenen Zielatome) hängt von folgenden Faktoren ab:
-
Magnetfeld und Einschluss:
- Ein Magnetfeld wird häufig eingesetzt, um das Plasma um das Target herum einzuschließen, die Dichte der Ar+-Ionen zu erhöhen und die Sputtereffizienz zu verbessern.
- Dieser magnetische Einschluss ist entscheidend für die Aufrechterhaltung eines stabilen Plasmas und die Verbesserung der Abscheideraten.
-
Praktische Überlegungen zu Ausrüstung und Verbrauchsmaterial:
- Achten Sie bei der Auswahl der Geräte auf den Druckbereich und die Kompatibilität mit Inertgasen wie Argon.
- Stellen Sie sicher, dass die Vakuumpumpe die erforderlichen Drücke (1 Pa bis 30 mTorr) erreichen und aufrechterhalten kann.
- Wählen Sie eine Stromquelle (DC oder RF), die mit der gewünschten Abscheidungsrate und Materialkompatibilität übereinstimmt.
Durch die Kenntnis dieser Schlüsselpunkte können die Käufer von Geräten und Verbrauchsmaterialien fundierte Entscheidungen über den Sputterprozess treffen, die eine optimale Leistung und eine hochwertige Dünnschichtabscheidung gewährleisten.
Zusammenfassende Tabelle:
Hauptaspekt | Einzelheiten |
---|---|
Plasma Druckbereich | 5-30 mTorr |
Verwendetes Inertgas | Argon |
Vakuumkammer Druck | ~1 Pa (0,0000145 psi) |
Thermalisierungsprozess | Sorgt für kontrollierte Energie und Richtung der abgeschiedenen Partikel |
Rolle des Magnetfelds | Begrenzt das Plasma, erhöht die Ar+-Ionendichte und verbessert die Sputtereffizienz |
Überlegungen zur Ausrüstung | Vakuumpumpe, Stromquelle (DC/RF) und Kompatibilität mit Inertgasen |
Sind Sie bereit für die Optimierung Ihres Sputtering-Prozesses? Kontaktieren Sie noch heute unsere Experten für maßgeschneiderte Lösungen!