Die physikalische Gasphasenabscheidung (PVD) ist ein vielseitiges Dünnschichtverfahren, das zur Herstellung haltbarer, hochleistungsfähiger Beschichtungen auf verschiedenen Substraten eingesetzt wird.Bei diesem Verfahren wird ein festes Vorläufermaterial in eine Dampfphase umgewandelt, die dann auf einem Substrat kondensiert und eine dünne Schicht bildet.Dies wird durch Methoden wie thermisches Verdampfen, Sputtern oder andere physikalische Verfahren erreicht, in der Regel in einer Vakuumumgebung, um Verunreinigungen zu minimieren.PVD-Beschichtungen sind für ihre hervorragende Haftung, Kratzfestigkeit und Korrosionsbeständigkeit bekannt und eignen sich daher für Anwendungen in Branchen wie Luft- und Raumfahrt, Elektronik und medizinische Geräte.Das Verfahren ist sehr gut steuerbar und ermöglicht eine präzise Steuerung der Schichtdicke und -zusammensetzung.
Die wichtigsten Punkte werden erklärt:
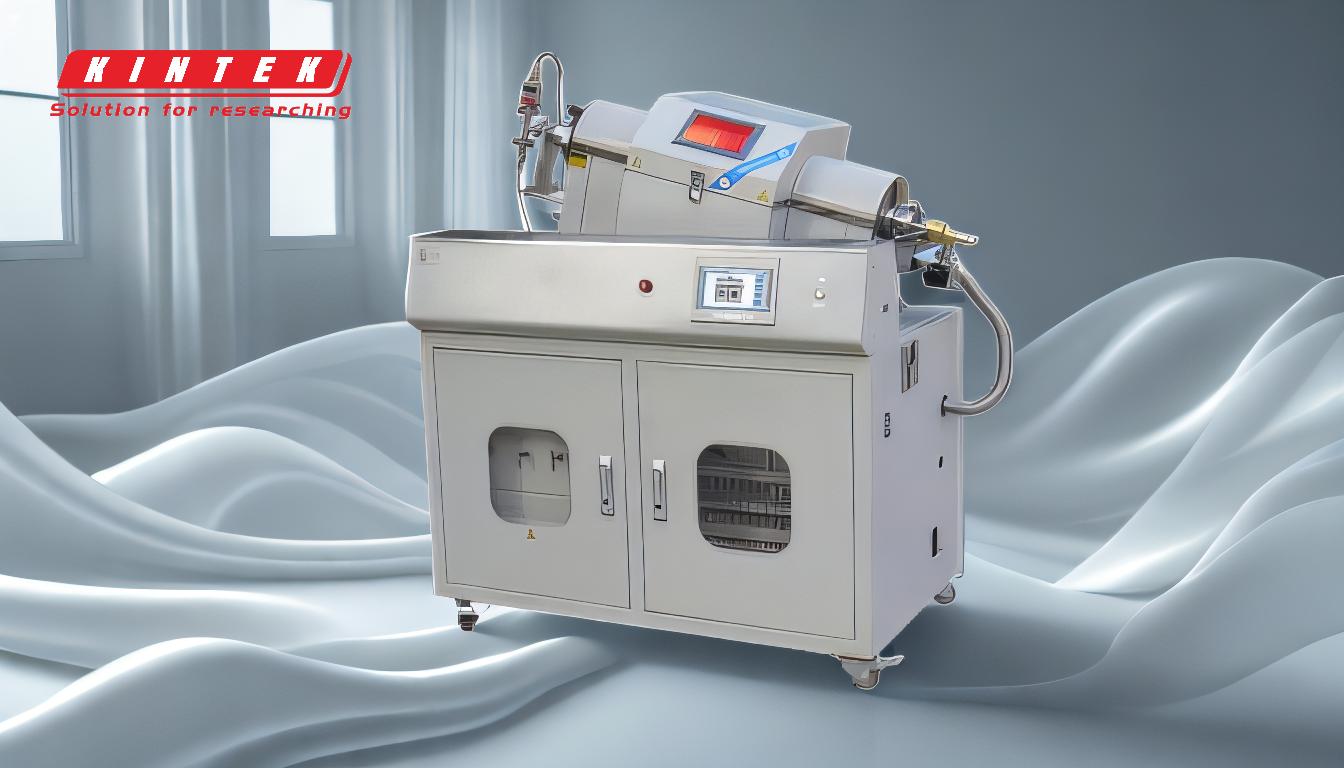
-
Grundprinzip von PVD:
- Beim PVD-Verfahren wird ein festes Material in eine Dampfphase umgewandelt, die dann als dünne Schicht auf ein Substrat aufgebracht wird.
- Das Verfahren findet in einer Vakuum- oder Niederdruckumgebung statt, um Störungen durch Hintergrundgase zu verringern und qualitativ hochwertige Beschichtungen zu gewährleisten.
-
Schritte im PVD-Prozess:
- Verdampfung:Das feste Vorläufermaterial wird durch Verfahren wie thermisches Verdampfen, Sputtern oder Laserablation vergast.
- Transport:Die verdampften Atome oder Moleküle wandern durch die Reaktionskammer.
- Abscheidung:Der Dampf kondensiert auf dem Substrat und bildet eine dünne Schicht mit starker Haftung und gleichmäßiger Dicke.
-
Methoden der PVD:
- Thermische Verdampfung:Das Targetmaterial wird bis zu seinem Verdampfungspunkt erhitzt, und der Dampf wird auf dem Substrat abgeschieden.
- Sputtern:Hochenergetische Ionen beschießen das Zielmaterial und lösen Atome heraus, die sich dann auf dem Substrat ablagern.
- Andere Techniken:Dazu gehören die Lichtbogenbedampfung und die gepulste Laserbedampfung, die jeweils für bestimmte Anwendungen geeignet sind.
-
Vorteile von PVD:
- Dauerhaftigkeit:PVD-Beschichtungen sind äußerst verschleiß-, kratz- und korrosionsbeständig.
- Vielseitigkeit:Kann eine breite Palette von Materialien abscheiden, auch solche mit hohem Schmelzpunkt.
- Präzision:Ermöglicht eine präzise Kontrolle der Schichtdicke und -zusammensetzung, die häufig mit Hilfe von Geräten wie Quarzkristall-Monitoren überwacht wird.
-
Anwendungen von PVD:
- Industrielle Beschichtungen:Wird für Werkzeuge, Formen und Maschinen verwendet, um Haltbarkeit und Leistung zu verbessern.
- Elektronik:Abscheidung von Dünnschichten für Halbleiter, Sensoren und optische Geräte.
- Medizinische Geräte:Bietet biokompatible und verschleißfeste Beschichtungen für Implantate und chirurgische Instrumente.
-
Wichtige Überlegungen für PVD:
- Vakuum Umwelt:Unerlässlich für die Minimierung von Verunreinigungen und die Gewährleistung hochwertiger Beschichtungen.
- Material-Kompatibilität:Die Wahl des Zielmaterials und des Trägermaterials muss auf die beabsichtigte Anwendung abgestimmt sein.
- Prozesskontrolle:Parameter wie Temperatur, Druck und Abscheidungsrate müssen sorgfältig gesteuert werden, um die gewünschten Schichteigenschaften zu erzielen.
Durch die Kenntnis dieser wichtigen Punkte können Käufer von Anlagen und Verbrauchsmaterialien fundierte Entscheidungen über die Auswahl von PVD-Systemen und -Materialien für ihre spezifischen Anforderungen treffen.
Zusammenfassende Tabelle:
Aspekt | Einzelheiten |
---|---|
Grundprinzip | Umwandlung von festem Material in Dampf, der zu einem dünnen Film auf einem Substrat kondensiert. |
Schritte im PVD-Prozess | Verdampfung → Transport → Abscheidung |
Methoden | Thermisches Verdampfen, Sputtern, Arc Vapor Deposition, Pulsed Laser Deposition |
Vorteile | Langlebigkeit, Vielseitigkeit, Präzision |
Anwendungen | Industrielle Beschichtungen, Elektronik, medizinische Geräte |
Wichtige Überlegungen | Vakuumumgebung, Materialkompatibilität, Prozesskontrolle |
Entdecken Sie, wie PVD Ihre Anwendungen verbessern kann. Kontaktieren Sie unsere Experten noch heute !