Magnetronsputtern ist ein hocheffizientes Verfahren zur physikalischen Gasphasenabscheidung (PVD), mit dem dünne Schichten auf Substraten erzeugt werden.Bei diesem Verfahren wird eine Hochvakuumumgebung geschaffen, ein Inertgas (in der Regel Argon) eingeleitet und eine Hochspannung zur Erzeugung eines Plasmas angelegt.Ein Magnetfeld schließt die Elektronen in der Nähe der Oberfläche des Targets ein, wodurch die Plasmadichte und die Abscheidungsraten erhöht werden.Positiv geladene Argon-Ionen kollidieren mit dem negativ geladenen Target und stoßen Atome aus, die dann auf das Substrat wandern und dort haften bleiben und einen dünnen Film bilden.Dieses Verfahren ist in Branchen wie der Halbleiter-, Optik- und Beschichtungsindustrie weit verbreitet, da es sich durch seine Präzision und Gleichmäßigkeit auszeichnet und eine breite Palette von Materialien abscheiden kann.
Die wichtigsten Punkte werden erklärt:
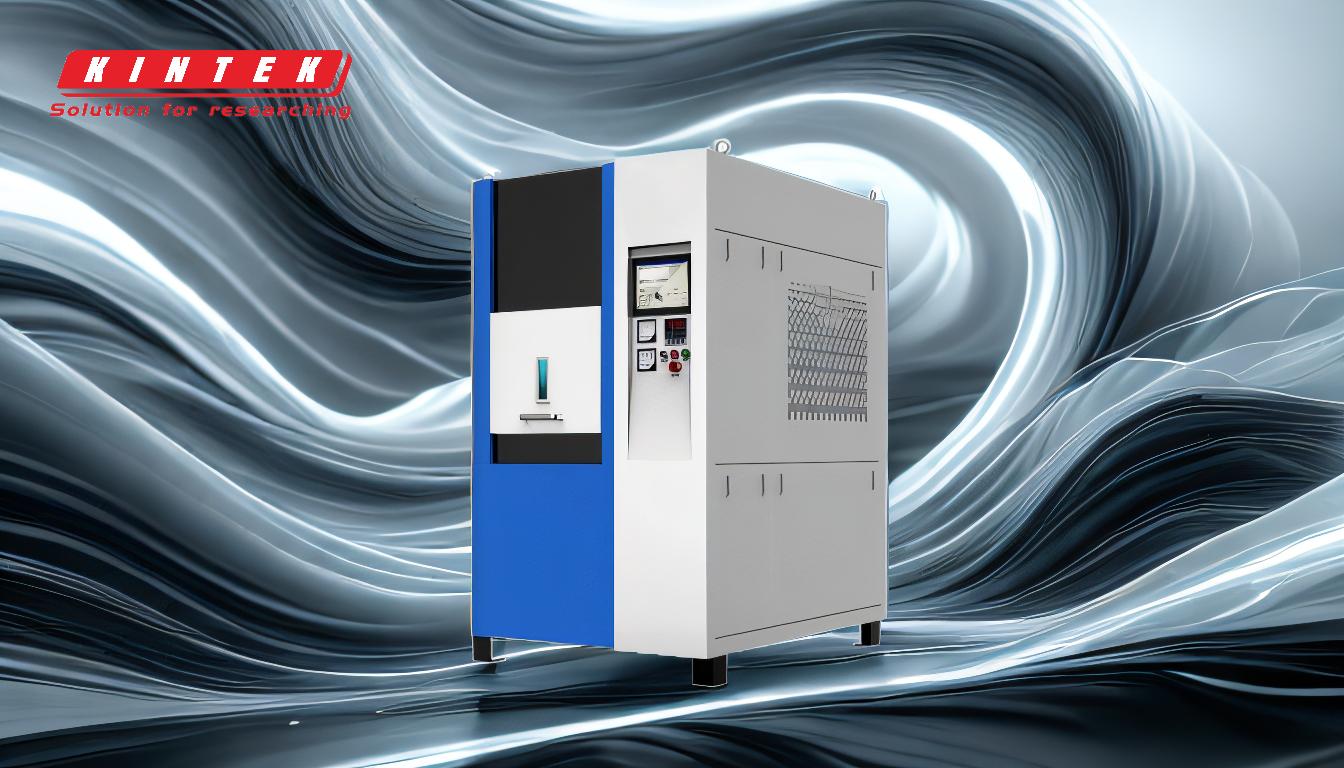
-
Vorbereitung der Vakuumkammer:
- Der Prozess beginnt mit dem Evakuieren der Kammer, um ein Hochvakuum zu erzeugen.Dieser Schritt ist entscheidend für die Minimierung von Verunreinigungen und die Gewährleistung eines sauberen Abscheidungsprozesses.
- Ein Hochvakuum reduziert das Vorhandensein unerwünschter Gase und Partikel, die die Qualität und Haftung der Dünnschicht beeinträchtigen könnten.
-
Einführung von Sputtering-Gas:
- Ein inertes Gas, in der Regel Argon, wird in die Vakuumkammer eingeleitet.Der Gasdruck wird im Milli-Torr-Bereich gehalten.
- Argon wird gewählt, weil es chemisch inert ist und das Risiko unerwünschter chemischer Reaktionen während des Sputterprozesses verringert.
-
Erzeugung des Plasmas:
- Zwischen der Kathode (Target) und der Anode wird eine hohe negative Spannung angelegt, wodurch das Argongas ionisiert wird und ein Plasma entsteht.
- Das Plasma besteht aus positiv geladenen Argon-Ionen, freien Elektronen und neutralen Argon-Atomen.
-
Magnetischer Feldeinschluss:
- Mit Hilfe von Magnetanordnungen in der Nähe der Zieloberfläche wird ein Magnetfeld erzeugt.Dieses Feld schließt die Elektronen ein, vergrößert ihre Weglänge und erhöht die Wahrscheinlichkeit, dass Argonatome ionisiert werden.
- Die eingeschlossenen Elektronen erzeugen ein dichtes Plasma in der Nähe des Targets, was die Abscheiderate deutlich erhöht.
-
Sputtern von Targetmaterial:
- Positiv geladene Argon-Ionen aus dem Plasma werden auf das negativ geladene Target (Kathode) beschleunigt.
- Wenn diese hochenergetischen Ionen mit dem Target zusammenstoßen, stoßen sie Atome aus dem Targetmaterial aus (Sputtern).
-
Abscheidung auf dem Substrat:
- Die herausgeschleuderten Zielatome wandern durch die Vakuumkammer und lagern sich auf der Substratoberfläche ab.
- Diese Atome kondensieren und bilden einen dünnen Film, der aufgrund physikalischer und manchmal auch chemischer Bindungen auf dem Substrat haftet.
-
Kontrolle der Abscheidungsparameter:
- Die Abscheiderate, die Schichtdicke und die Gleichmäßigkeit können durch die Einstellung von Parametern wie Gasdruck, Spannung, Magnetfeldstärke und Abstand zwischen Target und Substrat gesteuert werden.
- Die präzise Steuerung dieser Parameter gewährleistet hochwertige dünne Schichten mit den gewünschten Eigenschaften.
-
Vorteile des Magnetron-Sputterns:
- Hohe Ablagerungsraten:Das Magnetfeld erhöht die Plasmadichte, was zu einer schnelleren Abscheidung führt.
- Gleichmäßige Filme:Das Verfahren ermöglicht die Abscheidung gleichmäßiger dünner Schichten auf großen Flächen.
- Vielseitigkeit:Eine breite Palette von Materialien, einschließlich Metalle, Legierungen und Keramiken, kann mit diesem Verfahren abgeschieden werden.
- Geringe Beschädigung des Substrats:Das Magnetfeld trägt dazu bei, das Substrat vor Ionenbeschuss zu schützen, wodurch Schäden verringert und die Filmqualität verbessert werden.
-
Anwendungen:
- Halbleiterindustrie:Für die Abscheidung dünner Schichten bei der Herstellung integrierter Schaltkreise und der Mikroelektronik.
- Optische Beschichtungen:Wird bei der Herstellung von Antireflexionsbeschichtungen, Spiegeln und optischen Filtern verwendet.
- Dekorative Beschichtungen:Wird zur Herstellung von haltbaren und ästhetisch ansprechenden Beschichtungen auf verschiedenen Konsumgütern verwendet.
- Schützende Beschichtungen:Zur Abscheidung von verschleißfesten und korrosionsbeständigen Beschichtungen auf Werkzeugen und Bauteilen.
-
Herausforderungen und Überlegungen:
- Ziel Erosion:Das Zielmaterial erodiert im Laufe der Zeit und muss regelmäßig ersetzt oder neu beschichtet werden.
- Wärme-Management:Das Verfahren erzeugt Wärme, die kontrolliert werden muss, um Schäden am Substrat zu vermeiden und die Qualität des Films zu erhalten.
- Kosten:Hochvakuumausrüstung und Target-Materialien können teuer sein, was das Verfahren im Vergleich zu anderen Abscheidungsmethoden teurer macht.
Zusammenfassend lässt sich sagen, dass das Magnetronsputtern ein hochentwickeltes und vielseitiges Verfahren zur Abscheidung von Dünnschichten ist, das Hochvakuum, Plasma und Magnetfelder nutzt, um präzise und hochwertige Beschichtungen zu erzielen.Die Fähigkeit, eine breite Palette von Materialien abzuscheiden und dabei die Schichteigenschaften hervorragend zu kontrollieren, macht dieses Verfahren in verschiedenen High-Tech-Industrien unverzichtbar.
Zusammenfassende Tabelle:
Hauptaspekt | Einzelheiten |
---|---|
Verfahren | Hochvakuum, Argongas, Plasmaerzeugung, Magnetfeldeinschluss. |
Vorteile | Hohe Abscheideraten, gleichmäßige Schichten, Vielseitigkeit, geringe Substratschädigung. |
Anwendungen | Halbleiter, optische Schichten, dekorative Schichten, Schutzschichten. |
Herausforderungen | Target-Erosion, Wärmemanagement, hohe Anlagenkosten. |
Entdecken Sie, wie das Magnetronsputtern Ihre Prozesse verbessern kann. Kontaktieren Sie uns noch heute !