Bei der Aufdampfbeschichtung handelt es sich um ein Verfahren der physikalischen Gasphasenabscheidung (PVD), mit dem dünne, gleichmäßige Materialschichten auf einem Substrat erzeugt werden. Dabei wird ein Ausgangsmaterial in einer Hochvakuumumgebung bis zu seinem Verdampfungspunkt erhitzt, wodurch es verdampft und dann auf dem Zielobjekt kondensiert. Diese Methode gewährleistet eine saubere, präzise und hochwertige Beschichtung, die häufig in Branchen wie Elektronik, Optik und Luft- und Raumfahrt eingesetzt wird. Das Verfahren beruht auf der Aufrechterhaltung eines Vakuums, um Verunreinigungen zu minimieren und eine gute Haftung des Beschichtungsmaterials auf dem Substrat zu gewährleisten.
Die wichtigsten Punkte werden erklärt:
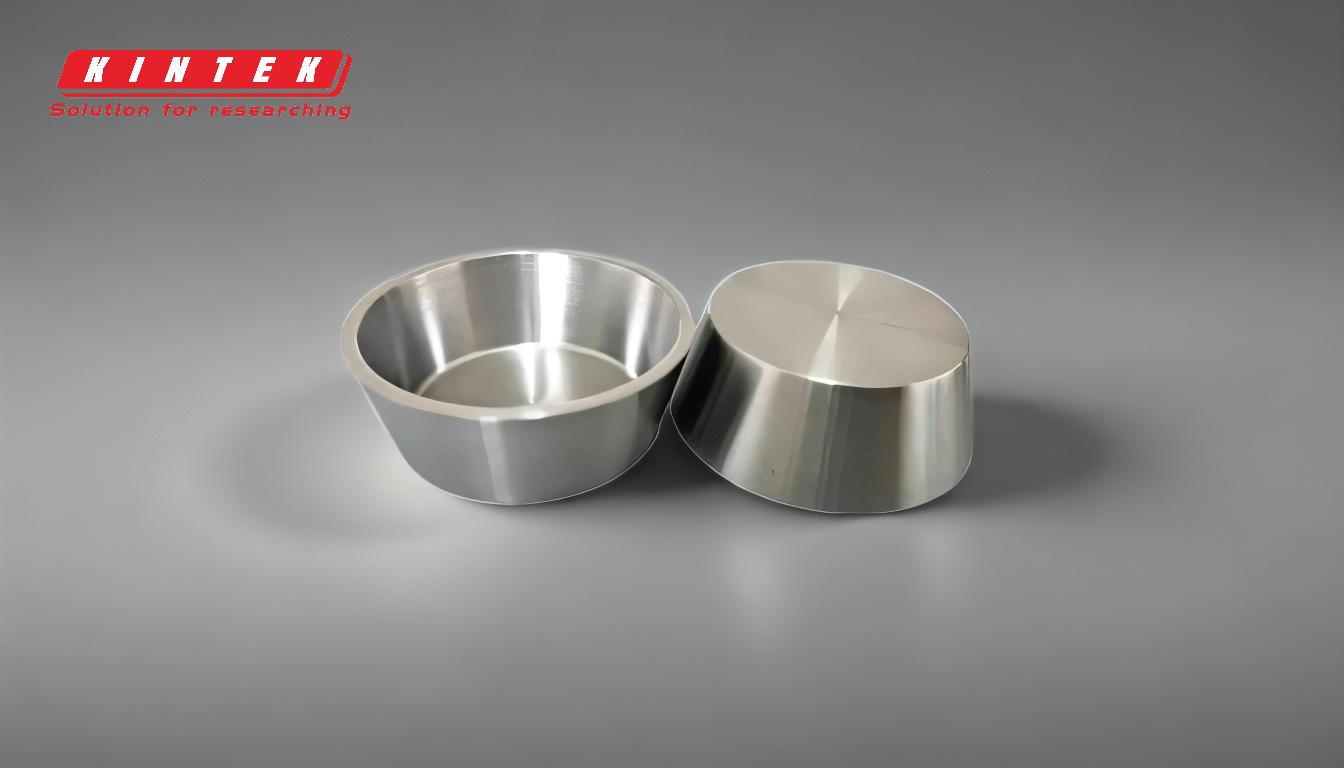
-
Vorbereitung der Vakuumkammer:
- Das Verfahren beginnt damit, dass das Substrat (Zielobjekt) und das Ausgangsmaterial in eine Hochvakuumkammer gebracht werden.
- Eine Vakuumpumpe saugt Luft und andere Gase ab, um eine Niederdruckumgebung zu schaffen, die die Wahrscheinlichkeit von Gaskollisionen und Verunreinigungen verringert.
- Dieser Schritt ist von entscheidender Bedeutung, um die Reinheit der Beschichtung zu gewährleisten und einen klaren Weg für das verdampfte Material zu schaffen.
-
Erhitzen des Ausgangsmaterials:
- Das Ausgangsmaterial (z. B. ein Metall, eine Legierung oder eine Verbindung) wird mit Methoden wie Widerstandserwärmung, Elektronenstrahlheizung oder Induktionserwärmung auf seinen Schmelz- oder Verdampfungspunkt erhitzt.
- Wenn das Material erhitzt wird, geht es vom festen in den dampfförmigen Zustand über und gibt Atome oder Moleküle in die Kammer ab.
- Die Temperatur muss sorgfältig kontrolliert werden, um eine gleichmäßige Verdampfung zu erreichen und eine Überhitzung zu vermeiden, die das Material oder die Kammer beschädigen könnte.
-
Verdampfung und Ablagerung:
- Sobald das Material verdampft ist, bildet es einen Dampfstrom, der durch die Vakuumkammer strömt.
- Die verdampften Atome oder Moleküle kondensieren auf dem Substrat und bilden eine dünne, gleichmäßige Schicht.
- Die Beschichtung haftet aufgrund des hochenergetischen Zustands der Dampfteilchen und der kontrollierten Substrattemperatur auf dem Substrat, was eine starke Bindung fördert.
-
Die Rolle des Substrats Temperatur:
- Das Substrat wird häufig erhitzt, um die Haftung und Gleichmäßigkeit der Beschichtung zu optimieren.
- Die richtige Temperatur des Substrats sorgt dafür, dass sich das verdampfte Material gleichmäßig verteilt und effektiv mit der Oberfläche verbindet.
- Ist der Untergrund zu kalt, kann die Beschichtung nicht richtig haften; ist er zu heiß, kann es zu Fehlern oder Unebenheiten kommen.
-
Vorteile von Hochvakuumbedingungen:
- Die Hochvakuumumgebung minimiert das Vorhandensein von Verunreinigungen, wie Sauerstoff oder Feuchtigkeit, die mit dem verdampften Material reagieren könnten.
- Außerdem wird die Wärmeübertragung reduziert, was eine präzise Steuerung des Abscheidungsprozesses ermöglicht.
- Das Vakuum sorgt dafür, dass sich das verdampfte Material in einer geraden Linie bewegt und nur die Oberflächen in Sichtweite beschichtet.
-
Anwendungen der Verdunstungsbeschichtung:
-
Dieses Verfahren wird häufig in Branchen eingesetzt, die hochpräzise Beschichtungen benötigen, wie z. B:
- Elektronik: Zur Herstellung dünner Schichten auf Halbleitern und Leiterplatten.
- Optik: Zum Aufbringen von Antireflexions- oder Reflexionsschichten auf Linsen und Spiegeln.
- Luft- und Raumfahrt: Für Schutzschichten auf kritischen Komponenten.
- Die Fähigkeit, mikrodünne, gleichmäßige Beschichtungen zu erzeugen, macht es ideal für hochtechnologische Anwendungen.
-
Dieses Verfahren wird häufig in Branchen eingesetzt, die hochpräzise Beschichtungen benötigen, wie z. B:
-
Arten von Verdampfungstechniken:
- Thermische Verdampfung: Verdampfen des Ausgangsmaterials durch Widerstandsheizung.
- Elektronenstrahlverdampfung: Erhitzt und verdampft das Material mit Hilfe eines fokussierten Elektronenstrahls, geeignet für hochschmelzende Materialien.
- Induktionserwärmung: Nutzt die elektromagnetische Induktion zur Erwärmung des Materials und wird häufig für großflächige Anwendungen eingesetzt.
-
Herausforderungen und Überlegungen:
- Das Verfahren erfordert eine präzise Steuerung von Temperatur, Vakuumdruck und Abscheidungsrate.
- Die Abscheidung in der Sichtlinie bedeutet, dass komplexe Geometrien zusätzliche Techniken erfordern können, z. B. das Drehen des Substrats oder die Verwendung mehrerer Verdampfungsquellen.
- Die Kosten für die Aufrechterhaltung von Hochvakuumbedingungen und Spezialausrüstungen können für einige Anwendungen ein limitierender Faktor sein.
Wenn diese Schritte und Überlegungen befolgt werden, bietet die Aufdampfbeschichtung eine zuverlässige und effiziente Methode zur Herstellung hochwertiger Dünnfilmbeschichtungen auf einer Vielzahl von Substraten.
Zusammenfassende Tabelle:
Hauptaspekt | Einzelheiten |
---|---|
Prozess | Physikalische Gasphasenabscheidung (PVD) für die Dünnfilmbeschichtung. |
Umwelt | Hochvakuumkammer zur Minimierung der Kontamination. |
Heizmethoden | Widerstandsheizung, Elektronenstrahl- oder Induktionserwärmung zur Materialverdampfung. |
Anwendungen | Elektronik, Optik, Luft- und Raumfahrt für hochpräzise Beschichtungen. |
Vorteile | Saubere, präzise, gleichmäßige Beschichtungen mit starker Haftung. |
Herausforderungen | Erfordert eine präzise Temperaturkontrolle und Hochvakuum-Wartung. |
Entdecken Sie, wie die Aufdampfbeschichtung Ihre Projekte verbessern kann kontaktieren Sie unsere Experten noch heute !