Drucksintern ist ein spezielles Verfahren zur Herstellung dichter, hochfester Materialien durch die Kombination von Hitze und Druck. Dabei wird ein Pulverpressling vorbereitet, auf eine Temperatur unterhalb seines Schmelzpunkts erhitzt und von außen Druck ausgeübt, um die Verdichtung zu verbessern und die Porosität zu verringern. Dieses Verfahren ist besonders effektiv für Materialien wie Keramik und Metalle, bei denen es auf eine geringe Porosität und eine hohe mechanische Festigkeit ankommt. Die Schritte umfassen typischerweise die Pulvervorbereitung, das Mischen, das Formen, das Sintern unter Druck und die Nachbehandlung. Drucksintern kann in verschiedenen Umgebungen wie Vakuum oder inerten Atmosphären durchgeführt werden, um Oxidation zu verhindern und die Materialintegrität sicherzustellen.
Wichtige Punkte erklärt:
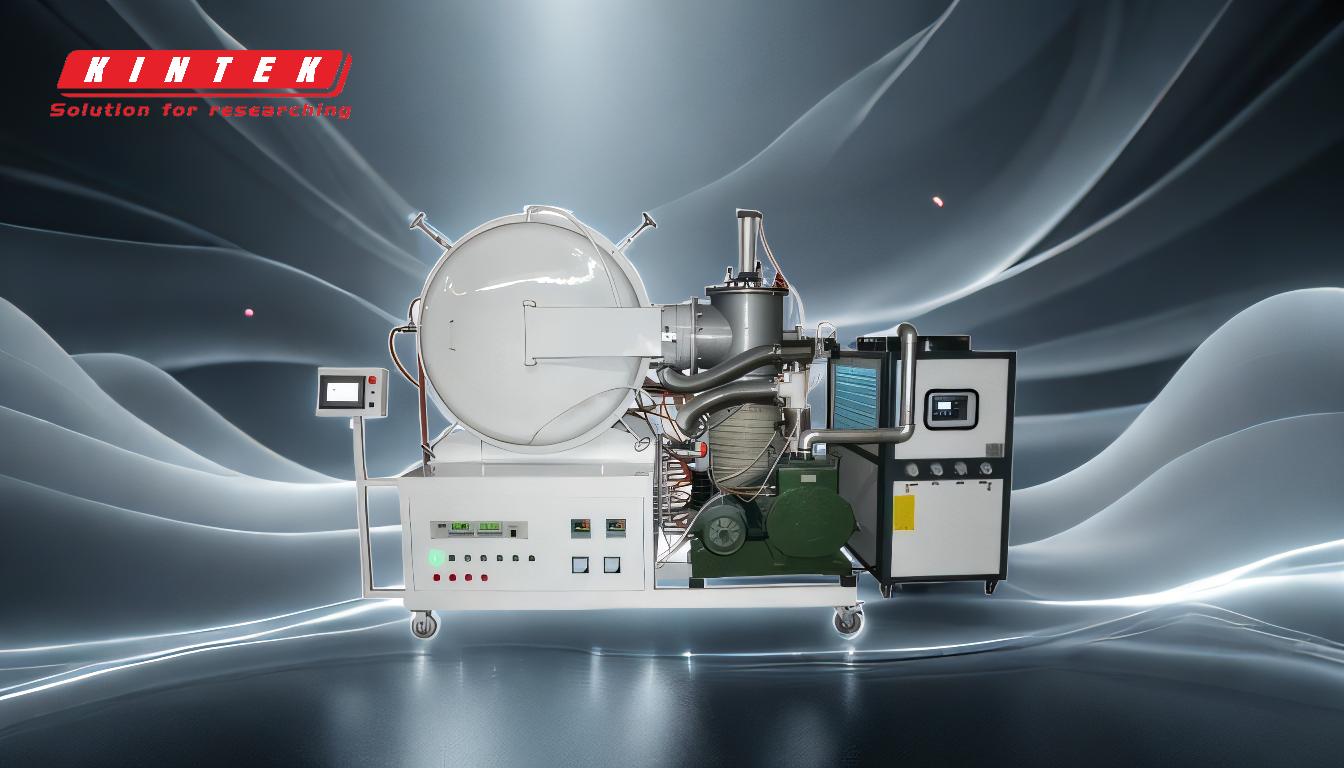
-
Herstellung von Puderkompakt:
- Der Prozess beginnt mit der Herstellung eines Pulverpresskörpers, bei dem pulverförmige Materialien mit Bindemitteln oder Haftvermittlern vermischt werden, um eine gleichmäßige Konsistenz zu gewährleisten.
- Das Pulver wird dann mithilfe von Werkzeugen wie Kaltschweißen, 3D-gedruckten Lasern oder Presswerkzeugen in einer kontrollierten Atmosphäre in die gewünschte Form gepresst.
- Dieser Schritt ist entscheidend für das Erreichen der ursprünglichen Form und Dichte des Materials vor dem Sintern.
-
Erwärmung und Konsolidierung:
- Das verdichtete Pulver wird auf eine Temperatur knapp unter seinem Schmelzpunkt erhitzt. Diese Temperatur wird sorgfältig kontrolliert, um den Sinterprozess zu aktivieren, ohne dass es zu einem vollständigen Schmelzen kommt.
- Beim Erhitzen verdampft oder verbrennt das Bindemittel (häufig ein Wachs oder Polymer), sodass die Primärpartikel an ihren Oberflächen zu verschmelzen beginnen.
- In einigen Fällen schmilzt ein Zwischenbindemittel wie Bronze und verbindet sich zwischen den Partikeln, wodurch das Primärkomponentenpulver unverändert bleibt.
-
Anwendung von äußerem Druck:
- Im Gegensatz zum herkömmlichen Sintern erfolgt beim Drucksintern die Anwendung von Außendruck während des Erhitzungsprozesses. Dieser Druck trägt dazu bei, die Porosität zu verringern und die Verdichtung des Materials zu beschleunigen.
- Der Druck kann je nach den spezifischen Anforderungen des zu sinternden Materials auf verschiedene Arten ausgeübt werden, beispielsweise durch mechanische Pressen oder hydraulische Systeme.
- Die Kombination aus Hitze und Druck sorgt dafür, dass die Partikel effektiver verschmelzen, was zu einem dichteren und gleichmäßigeren Endprodukt führt.
-
Partikelverschmelzung und -verdichtung:
- Mit steigender Temperatur beginnen die Partikel an ihren Oberflächen zu verschmelzen, ein Vorgang, der als Festphasensintern bezeichnet wird. Dies kann durch das Vorhandensein einer flüssigen Phase, das so genannte Liquid-Phase-Sintering (LPS), noch beschleunigt werden.
- Bei LPS bildet sich zwischen den Partikeln eine flüssige Phase, die die Sintergeschwindigkeit erhöht und die Bruchmodi des Materials verändert. Dies führt zu verbesserten Materialeigenschaften wie erhöhter Zähigkeit und verringerter Porosität.
- Die Anwendung von Druck in dieser Phase sorgt dafür, dass die Partikel näher zusammengedrückt werden, wodurch Hohlräume weiter reduziert und die Dichte des Materials erhöht werden.
-
Abkühlung und Erstarrung:
- Nach Abschluss des Sintervorgangs wird das Material allmählich auf Raumtemperatur abgekühlt. Diese Abkühlphase ist entscheidend, um sicherzustellen, dass das Material zu einer einheitlichen Masse erstarrt, ohne dass innere Spannungen oder Risse entstehen.
- Die Abkühlgeschwindigkeit wird sorgfältig kontrolliert, um einen Thermoschock zu verhindern, der andernfalls zu Materialversagen führen könnte.
- Nach dem Abkühlen durchläuft das Material Nachbehandlungsprozesse wie maschinelle Bearbeitung oder Oberflächenveredelung, um die endgültigen gewünschten Eigenschaften und Abmessungen zu erreichen.
-
Umweltaspekte:
- Drucksintern wird oft in einem Vakuum oder einer inerten Atmosphäre durchgeführt, um Oxidation und Kontamination des Materials zu verhindern. Dies ist besonders wichtig für Materialien wie Siliziumkarbid, die eine hohe Reinheit und Stabilität erfordern.
- Durch die Verwendung einer kontrollierten Umgebung wird sichergestellt, dass das Material seine gewünschten Eigenschaften behält und sich während des Sinterprozesses nicht verschlechtert.
-
Vorteile des Drucksinterns:
- Reduzierte Porosität: Durch die Anwendung von Druck wird die Porosität des gesinterten Materials erheblich verringert, was zu einem dichteren und festeren Endprodukt führt.
- Verbesserte mechanische Eigenschaften: Durch die Kombination von Hitze und Druck werden die mechanischen Eigenschaften des Materials wie Härte, Festigkeit und Verschleißfestigkeit verbessert.
- Niedrigere Sintertemperaturen: In einigen Fällen ermöglicht das Drucksintern im Vergleich zu herkömmlichen Methoden niedrigere Sintertemperaturen, was für Materialien, die empfindlich auf hohe Temperaturen reagieren, von Vorteil sein kann.
- Schnellere Sinterzeiten: Die Anwendung von Druck kann die gesamte Sinterzeit verkürzen und so den Prozess effizienter und kostengünstiger machen.
Zusammenfassend lässt sich sagen, dass Drucksintern eine äußerst effektive Methode zur Herstellung dichter Hochleistungsmaterialien ist. Durch die Kombination von Wärme und Druck verbessert dieser Prozess die Verdichtung und die mechanischen Eigenschaften des Materials und macht es für eine Vielzahl industrieller Anwendungen geeignet. Die sorgfältige Kontrolle jedes Schritts, von der Pulvervorbereitung bis zur Kühlung, stellt sicher, dass das Endprodukt die erforderlichen Spezifikationen und Leistungskriterien erfüllt.
Übersichtstabelle:
Wichtige Schritte beim Drucksintern | Einzelheiten |
---|---|
Pulverzubereitung | Mischen und Verdichten von pulverförmigen Materialien mit Bindemitteln. |
Erwärmung und Konsolidierung | Erhitzen unter den Schmelzpunkt, um das Sintern zu aktivieren. |
Anwendung von äußerem Druck | Druck ausüben, um die Porosität zu verringern und die Verdichtung zu verbessern. |
Partikelverschmelzung | Festphasen- oder Flüssigphasensintern für verbesserte Materialeigenschaften. |
Abkühlung und Erstarrung | Kontrollierte Kühlung zur Vermeidung von Rissen und zur Gewährleistung der Materialintegrität. |
Umweltaspekte | Wird im Vakuum oder in einer inerten Atmosphäre durchgeführt, um Oxidation zu verhindern. |
Vorteile | Reduzierte Porosität, verbesserte mechanische Eigenschaften, niedrigere Sintertemperaturen und schnellere Sinterzeiten. |
Entdecken Sie, wie Drucksintern Ihre Materialproduktion optimieren kann – Kontaktieren Sie noch heute unsere Experten !