Die physikalische Gasphasenabscheidung (PVD) ist ein vakuumbasiertes Beschichtungsverfahren, mit dem dünne Materialschichten auf ein Substrat aufgebracht werden.Das Verfahren umfasst die Verdampfung eines festen Materials in eine Dampfphase, den Transport des Dampfes zum Substrat und die Kondensation des Dampfes auf dem Substrat zur Bildung einer dünnen Schicht.PVD ist in Branchen wie der Halbleiterindustrie, der Optik und der Werkzeugbeschichtung weit verbreitet, da sich mit diesem Verfahren hochwertige, haltbare und präzise Beschichtungen herstellen lassen.Das Verfahren wird in der Regel unter Hochvakuumbedingungen durchgeführt und umfasst mehrere Schritte, darunter Gaserzeugung, Transport, Reaktion und Abscheidung.
Die wichtigsten Punkte werden erklärt:
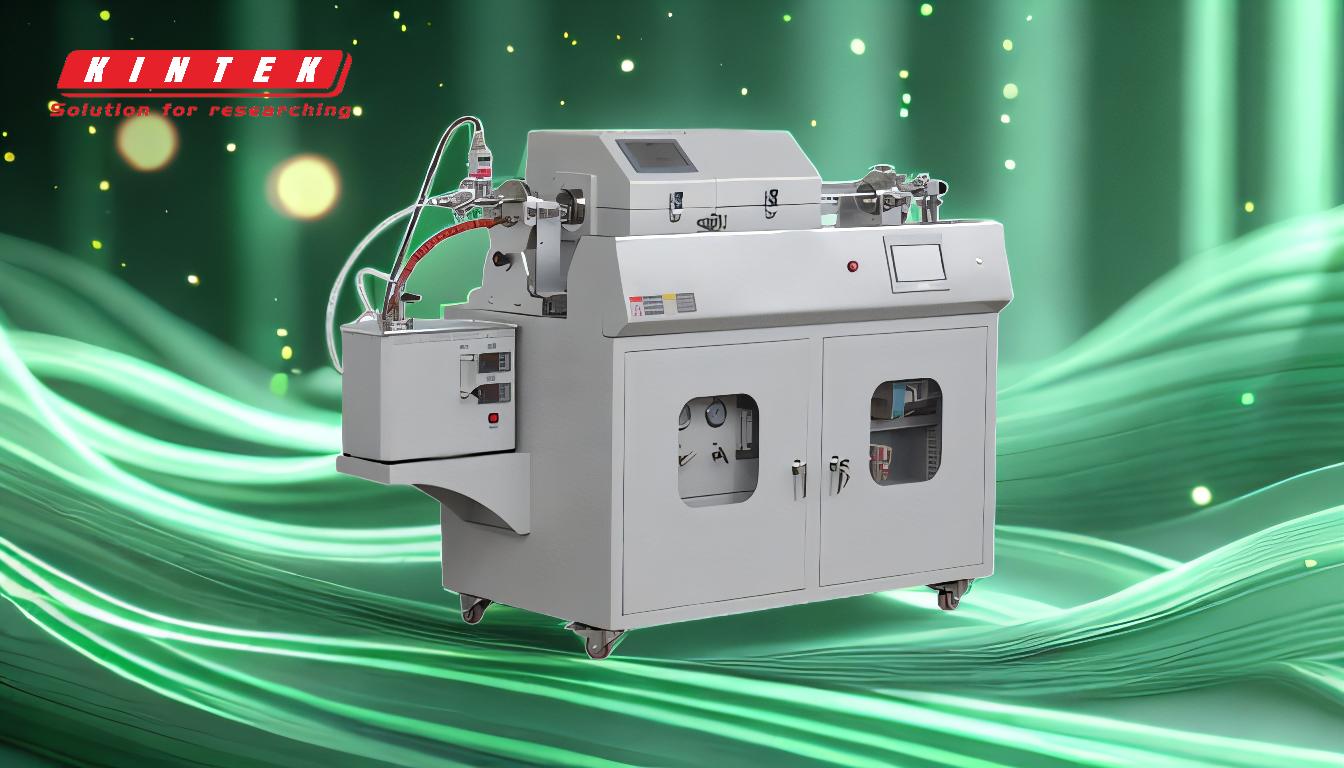
-
Verdampfung von Beschichtungsmaterial:
- Der erste Schritt im PVD-Verfahren ist die Verdampfung des Beschichtungsmaterials.Dies kann durch Methoden wie Verdampfung, Sputtern oder Laserablation erreicht werden.Beim Verdampfen wird das Material erhitzt, bis es sich in einen Dampf verwandelt.Beim Sputtern wird das Zielmaterial mit hochenergetischen Ionen beschossen, die Atome von der Oberfläche lösen und in die Dampfphase überführen.Bei der Laserablation wird ein Hochleistungslaser verwendet, um das Material zu verdampfen.
- Die Wahl der Verdampfungsmethode hängt von dem aufzubringenden Material und den gewünschten Eigenschaften der endgültigen Beschichtung ab.So wird zum Beispiel bei Metallen häufig das Sputtern verwendet, während bei Materialien mit niedrigerem Schmelzpunkt eher die Verdampfung zum Einsatz kommt.
-
Transport des Dampfes zum Substrat:
- Sobald das Material verdampft ist, werden die Atome, Moleküle oder Ionen durch die Vakuumkammer zum Substrat transportiert.Dieser Transport findet in einer Hochvakuumumgebung statt, um Kollisionen mit anderen Teilchen zu minimieren und sicherzustellen, dass der Dampf das Substrat mit minimaler Verunreinigung erreicht.
- Während des Transports kann der Dampf mit anderen Partikeln kollidieren, was zu Reaktionen führt, die die chemische Zusammensetzung des Dampfes verändern können.Dies ist besonders wichtig bei reaktiven PVD-Verfahren, bei denen ein reaktives Gas (wie Stickstoff oder Sauerstoff) zugeführt wird, um mit dem verdampften Material Verbindungen zu bilden.
-
Kondensation und Abscheidung auf dem Substrat:
- Der letzte Schritt im PVD-Verfahren ist die Kondensation des Dampfes auf dem Substrat, wo er einen dünnen Film bildet.Das Substrat wird in der Regel auf einer niedrigeren Temperatur gehalten als der Dampf, was die Kondensation fördert.Die Atome oder Moleküle im Dampf haften an dem Substrat und bilden eine feste Schicht.
- Die Eigenschaften der abgeschiedenen Schicht, wie Dicke, Gleichmäßigkeit und Haftung, hängen von Faktoren wie der Substrattemperatur, der Abscheiderate und den Vakuumbedingungen ab.Hochwertige Beschichtungen erfordern eine genaue Kontrolle dieser Parameter.
-
Reaktives PVD und Verbundwerkstoffbildung:
- Bei einigen PVD-Verfahren wird ein reaktives Gas in die Vakuumkammer eingeleitet, um Verbindungen mit dem verdampften Material zu bilden.Bei der Abscheidung von Titannitrid (TiN) zum Beispiel wird Titan verdampft und Stickstoffgas eingeleitet.Die Titanatome reagieren mit dem Stickstoff und bilden TiN, das dann auf dem Substrat abgeschieden wird.
- Reaktives PVD ermöglicht die Abscheidung einer breiten Palette von Verbindungen, darunter Oxide, Nitride und Karbide, die die Eigenschaften der Beschichtung, wie Härte, Verschleißfestigkeit und Korrosionsbeständigkeit, verbessern können.
-
Vorteile von PVD:
- PVD-Beschichtungen sind für ihre hohe Reinheit, Dichte und Haftung bekannt, wodurch sie sich für Anwendungen eignen, die präzise und dauerhafte Beschichtungen erfordern.Mit diesem Verfahren kann eine Vielzahl von Materialien beschichtet werden, darunter Metalle, Keramiken und Verbundwerkstoffe.
- PVD ist auch ein umweltfreundliches Verfahren, da keine gefährlichen Chemikalien verwendet werden oder schädliche Nebenprodukte entstehen.Die Vakuumumgebung sorgt dafür, dass das Verfahren sauber und frei von Verunreinigungen ist.
-
Anwendungen von PVD:
- PVD ist in verschiedenen Branchen weit verbreitet, unter anderem in der Halbleiterindustrie, wo es zur Abscheidung dünner Schichten aus Materialien wie Siliziumdioxid und Aluminium verwendet wird.In der Optikindustrie wird PVD zur Herstellung von Antireflexionsschichten und Spiegeln verwendet.In der Werkzeugindustrie werden PVD-Beschichtungen auf Schneidwerkzeuge aufgebracht, um deren Verschleißfestigkeit und Lebensdauer zu erhöhen.
- Aufgrund seiner Vielseitigkeit eignet sich das PVD-Verfahren für eine breite Palette von Anwendungen, von dekorativen Beschichtungen auf Konsumgütern bis hin zu funktionalen Beschichtungen in der Luft- und Raumfahrt und in medizinischen Geräten.
Zusammenfassend lässt sich sagen, dass das PVD-Verfahren eine sehr kontrollierte und vielseitige Methode zur Abscheidung dünner Materialschichten auf einem Substrat ist.Es umfasst die Verdampfung eines festen Materials, den Transport des Dampfes zum Substrat und die Kondensation des Dampfes zur Bildung einer dünnen Schicht.Das Verfahren kann durch den Einsatz reaktiver Gase zur Bildung von Verbindungen verbessert werden und bietet zahlreiche Vorteile, darunter hochwertige Beschichtungen und Umweltfreundlichkeit.PVD wird in einer Vielzahl von Branchen eingesetzt, von Halbleitern bis zu Werkzeugbeschichtungen, und ist damit eine wichtige Technologie in der modernen Fertigung.
Zusammenfassende Tabelle:
Hauptaspekt | Einzelheiten |
---|---|
Prozess-Schritte | Verdampfung → Transport → Kondensation und Ablagerung |
Methoden der Verdampfung | Verdampfung, Sputtern, Laserablation |
Wesentliche Vorteile | Hohe Reinheit, Dichte, Haftfähigkeit; umweltfreundlich |
Anwendungen | Halbleiter, Optik, Werkzeugbeschichtungen, Luft- und Raumfahrt, medizinische Geräte |
Reaktives PVD | Formt Verbindungen (z. B. TiN) mit reaktiven Gasen wie Stickstoff oder Sauerstoff |
Entdecken Sie, wie PVD Ihren Fertigungsprozess verbessern kann. Kontaktieren Sie unsere Experten noch heute !