Das PVD-Verfahren (Physical Vapor Deposition) ist eine vakuumbasierte Dünnfilmbeschichtungstechnologie, die in der Halbleiterherstellung weit verbreitet ist.Es umfasst die Verdampfung eines festen Materials, den Transport der verdampften Partikel auf ein Substrat und ihre anschließende Kondensation zur Bildung einer dünnen, gleichmäßigen Schicht.Das Verfahren wird unter Hochvakuumbedingungen und oft bei relativ niedrigen Temperaturen durchgeführt und eignet sich daher für empfindliche Halbleitersubstrate.PVD ist unerlässlich für die Herstellung präziser, hochwertiger Beschichtungen mit hervorragender Haftung und Gleichmäßigkeit, die für die Leistung von Halbleiterbauteilen entscheidend sind.Der Prozess umfasst in der Regel Schritte wie Dampferzeugung, Transport, Reaktion (falls zutreffend) und Abscheidung auf dem Substrat.
Die wichtigsten Punkte werden erklärt:
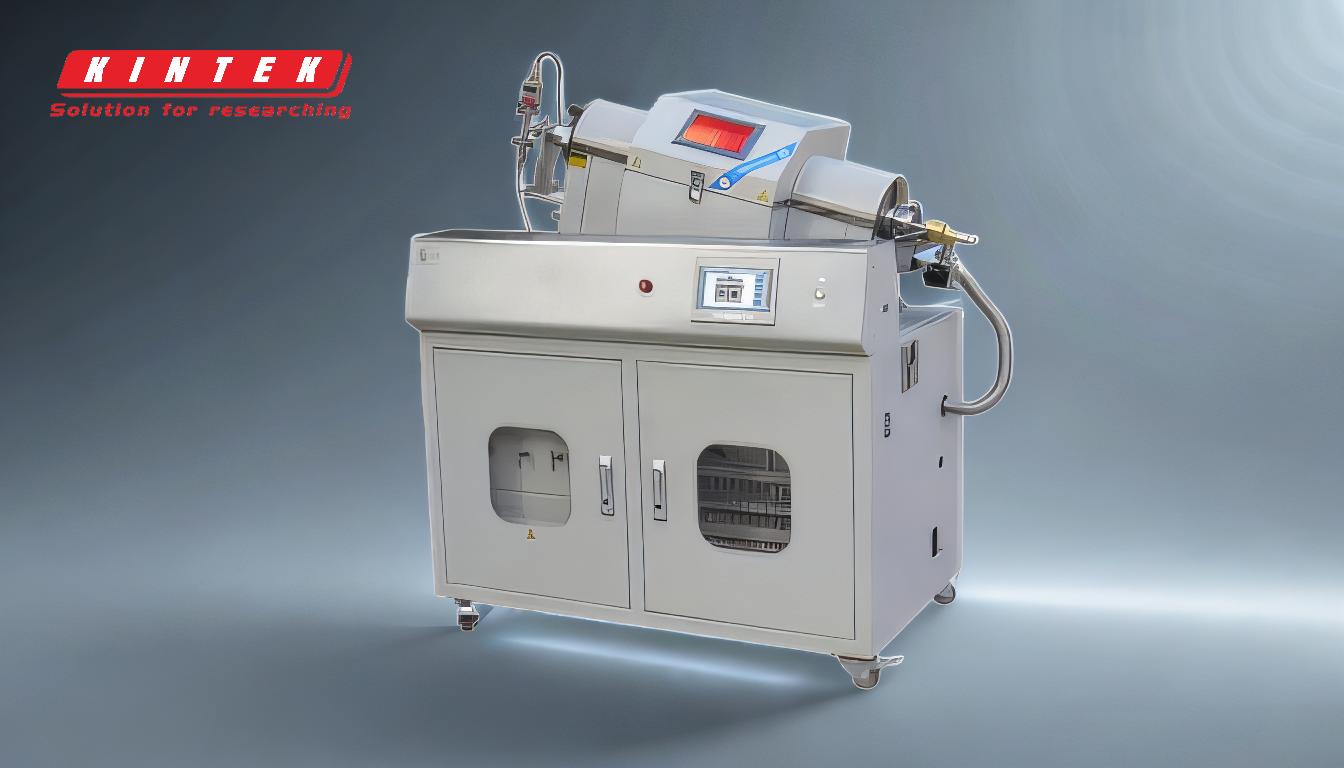
-
Verdampfung des Ausgangsmaterials:
-
Im ersten Schritt des PVD-Verfahrens wird ein festes Vorläufermaterial in einen Dampf umgewandelt.Dies geschieht durch Methoden wie:
- Verdampfung:Erhitzen des Ausgangsmaterials, bis es verdampft.
- Sputtern:Beschuss des Zielmaterials mit hochenergetischen Ionen, um Atome abzuspalten und einen Dampf zu erzeugen.
- Laserablation:Mit einem Hochleistungslaser wird das Material verdampft.
- Der Verdampfungsprozess findet in einer Hochvakuumumgebung statt, um die Kontamination zu minimieren und die Reinheit der abgeschiedenen Schicht zu gewährleisten.
-
Im ersten Schritt des PVD-Verfahrens wird ein festes Vorläufermaterial in einen Dampf umgewandelt.Dies geschieht durch Methoden wie:
-
Transport der verdampften Partikel:
-
Sobald das Ausgangsmaterial verdampft ist, werden die Atome, Moleküle oder Ionen durch die Vakuumkammer auf das Substrat transportiert.Dieser Schritt beinhaltet:
- Sicherstellung einer kontrollierten Umgebung, um unerwünschte Reaktionen oder Verunreinigungen zu vermeiden.
- Einsatz von Plasma oder reaktiven Gasen (falls erforderlich), um die Eigenschaften der verdampften Partikel zu verändern.
- Die Transportphase ist entscheidend für die Aufrechterhaltung der Integrität und Einheitlichkeit des Dampfes vor der Abscheidung.
-
Sobald das Ausgangsmaterial verdampft ist, werden die Atome, Moleküle oder Ionen durch die Vakuumkammer auf das Substrat transportiert.Dieser Schritt beinhaltet:
-
Reaktion mit reaktiven Gasen (optional):
- Bei einigen PVD-Verfahren wird den verdampften Partikeln ein reaktives Gas zugeführt, um eine Verbindung zu bilden.Dieser Schritt ist beim reaktiven PVD üblich, bei dem das Ziel darin besteht, ein Verbundmaterial (z. B. Nitride oder Oxide) und nicht ein reines Metall abzuscheiden.
- Das reaktive Gas geht mit den verdampften Partikeln eine chemische Wechselwirkung ein und bildet eine Verbindung, die dann auf dem Substrat abgeschieden wird.
-
Abscheidung auf dem Substrat:
-
Der letzte Schritt besteht in der Kondensation der verdampften Partikel auf dem Substrat, um eine dünne, gleichmäßige Schicht zu bilden.Zu den wichtigsten Aspekten dieses Schrittes gehören:
- Adhäsion:Gewährleistung einer starken Bindung zwischen der abgeschiedenen Schicht und dem Substrat.
- Gleichmäßigkeit:Erzielung einer gleichmäßigen Dicke über das gesamte Substrat.
- Kristallinität:Steuerung der Mikrostruktur der abgeschiedenen Schicht, um bestimmte Anforderungen an die Halbleiterleistung zu erfüllen.
- Das Substrat wird in der Regel auf einer niedrigeren Temperatur gehalten als das aufgedampfte Material, um die Kondensation zu erleichtern.
-
Der letzte Schritt besteht in der Kondensation der verdampften Partikel auf dem Substrat, um eine dünne, gleichmäßige Schicht zu bilden.Zu den wichtigsten Aspekten dieses Schrittes gehören:
-
Hoch-Vakuum-Umgebung:
-
Der gesamte PVD-Prozess wird unter Hochvakuumbedingungen durchgeführt, um:
- die Verunreinigung durch atmosphärische Gase zu minimieren.
- Bessere Kontrolle über den Abscheidungsprozess.
- Verbesserung der Qualität und Leistung der abgeschiedenen Dünnschicht.
-
Der gesamte PVD-Prozess wird unter Hochvakuumbedingungen durchgeführt, um:
-
Anwendungen in der Halbleiterfertigung:
-
PVD ist in der Halbleiterindustrie weit verbreitet für:
- Abscheidung leitfähiger Schichten (z. B. Aluminium, Kupfer) für Zwischenverbindungen.
- Erzeugung von Sperrschichten (z. B. Titannitrid) zur Verhinderung von Diffusion.
- Herstellung von Dünnschichten für fortschrittliche Halbleiterbauelemente wie Transistoren und Speicherzellen.
-
PVD ist in der Halbleiterindustrie weit verbreitet für:
-
Vorteile von PVD:
- Präzision:Ermöglicht die Abscheidung extrem dünner und gleichmäßiger Schichten.
- Material Vielseitigkeit:Geeignet für eine Vielzahl von Materialien, darunter Metalle, Legierungen und Verbindungen.
- Niedrige Temperatur:Verringert das Risiko, temperaturempfindliche Substrate zu beschädigen.
- Hohe Reinheit:Minimiert Verunreinigungen und gewährleistet hochwertige Beschichtungen.
Durch die Kenntnis dieser wichtigen Schritte und Überlegungen können Halbleiterhersteller die PVD-Technologie nutzen, um Hochleistungsgeräte mit präzisen und zuverlässigen Dünnschichtbeschichtungen herzustellen.
Zusammenfassende Tabelle:
Die wichtigsten Schritte im PVD-Prozess | Einzelheiten |
---|---|
Verdampfung | Umwandlung von festem Material in Dampf durch Verdampfung, Sputtern oder Ablation. |
Transport | Die verdampften Partikel wandern durch eine Hochvakuumkammer zum Substrat. |
Reaktion (optional) | Reaktive Gase können zur Bildung von Verbundwerkstoffen verwendet werden. |
Abscheidung | Der Dampf kondensiert auf dem Substrat und bildet eine dünne, gleichmäßige Schicht. |
Hoch-Vakuum-Umgebung | Sorgt für minimale Verunreinigung und präzise Kontrolle des Prozesses. |
Anwendungen | Für leitende Schichten, Sperrschichten und moderne Halbleiterbauelemente. |
Vorteile | Präzision, Materialvielfalt, niedrige Temperatur und hohe Reinheit. |
Entdecken Sie, wie PVD Ihre Halbleiterfertigung verbessern kann. Kontaktieren Sie uns noch heute für fachkundige Beratung!