Der Drehrohrofen ist ein thermisches Hochtemperaturverfahren, das zur Verarbeitung von körnigen oder pulverförmigen Materialien eingesetzt wird.Dabei werden die Materialien in einer rotierenden Trommel erhitzt, um chemische Reaktionen wie Kalzinierung, Oxidation, Reduktion oder Sinterung zu ermöglichen.Elektrische Drehrohröfen sind eine besondere Art von Drehrohröfen, die elektrische Heizelemente verwenden, um die erforderlichen Temperaturen zu erreichen.Diese Öfen verfügen über mehrere Heizzonen, die jeweils unabhängig voneinander geregelt werden, und sind mit Kühlsystemen ausgestattet, um die Austrittstemperatur des Materials zu steuern.Das Verfahren ist in hohem Maße anpassbar, wobei die Größe des Ofens, die Heizelemente und die Drehgeschwindigkeit auf das jeweilige Material und die Produktionsanforderungen zugeschnitten sind.Elektrische Drehrohröfen eignen sich besonders gut für Anwendungen, die eine präzise Temperaturregelung und Gleichmäßigkeit erfordern.
Die wichtigsten Punkte erklärt:
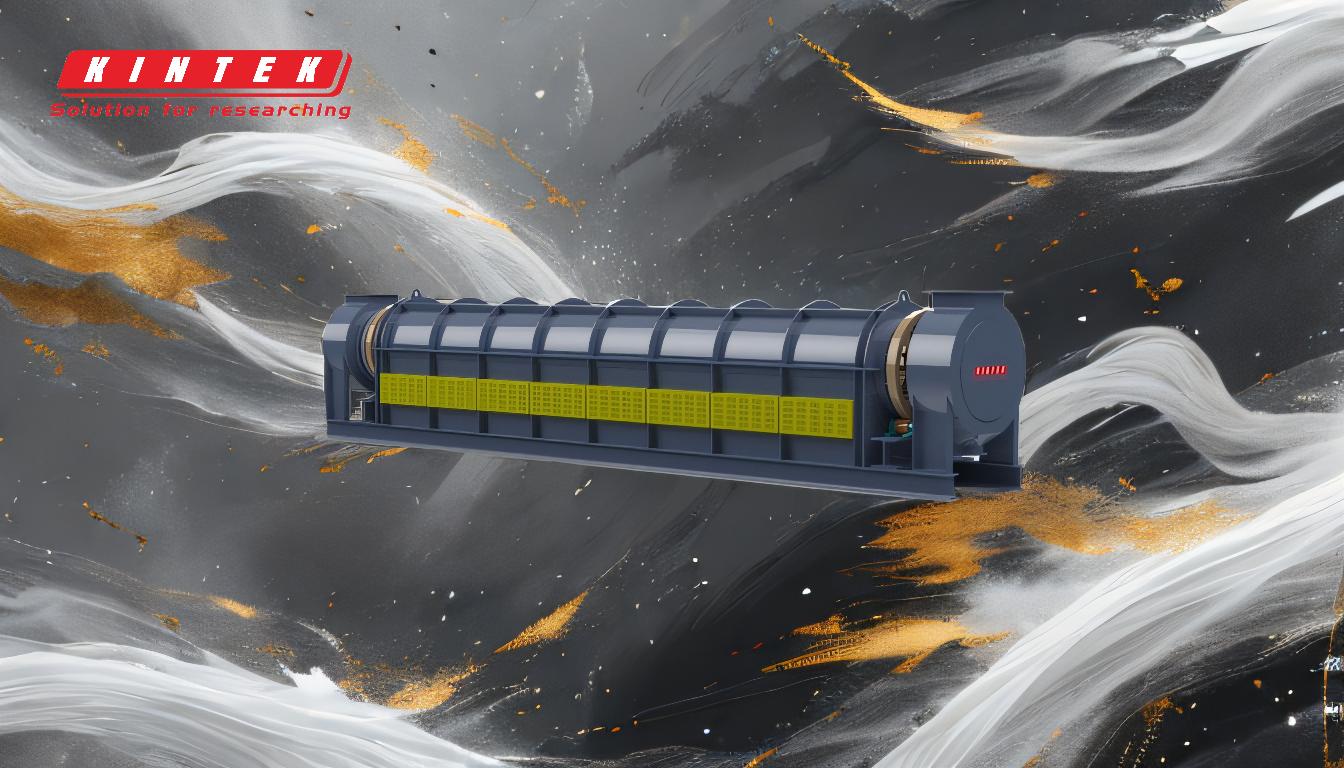
-
Typen von Drehrohröfen:
- Drehrohröfen können sein direkt befeuert oder indirekt befeuert (Kalzinatoren) .Direkt befeuerte Öfen nutzen den direkten Kontakt zwischen dem Material und dem Prozessgas, um Reaktionen einzuleiten, während indirekt befeuerte Öfen auf die Wärme des von außen beheizten Trommelmantels angewiesen sind.
- Elektrische Drehrohröfen Es handelt sich um eine spezielle Art von Öfen, die mit elektrischen Heizelementen arbeiten, um hohe Temperaturen zu erreichen, was sie ideal für eine präzise thermische Verarbeitung macht.
-
Anwendungen von elektrischen Drehrohröfen:
- Elektrische Drehrohröfen werden eingesetzt für Kalzinieren von körnigen oder pulverförmigen Materialien und zur Erleichterung von Hochtemperaturreaktionen wie Oxidation und Reduzierung .
- Sie werden auch eingesetzt bei Sintern Ein Verfahren, bei dem Materialien bis knapp unter ihren Schmelzpunkt erhitzt werden, um ihre Festigkeit zu erhöhen. Es wird häufig bei der Pelletierung von Eisenerz und der Herstellung von Stützmitteln eingesetzt.
-
Heizsystem:
- Die Heizelemente in einem elektrischen Drehrohrofen werden typischerweise hergestellt aus Nickel-Chrom-Legierungen (z. B. 1Cr18Ni9Ti, Cr25Ni20Si2) oder Eisen-Chrom-Aluminium-Legierungen (z. B. 0Cr13A14, 0Cr25A15).
- Diese spiralförmigen Elemente sind an den Seiten und am Boden des Ofens angebracht und unterteilen sich in vier Heizzonen jede mit unabhängiger Temperaturregelung.
-
Prozess der Kühlung:
- Die Kühlung erfolgt über einen Trommelkühler Hier wird Wasser auf die Außenseite der Trommel gesprüht, um das Material beim Durchlaufen der Trommel indirekt zu kühlen.
- Dadurch wird sichergestellt, dass das Material die erforderliche Auslauftemperatur erreicht.
-
Mechanismus der Rotation:
- Der Ofen wird durch ein Zahnkranz verbunden mit einem Elektromotor mit variabler Drehzahl .Ein 6 x 60 m großer Ofen benötigt zum Beispiel rund 800 kW bei einer Drehung von 3 Umdrehungen pro Minute .
- A Antrieb mit variabler Geschwindigkeit regelt den Materialdurchsatz, und ein Hilfsantrieb (z. B. kleiner Elektromotor oder Dieselmotor) wird bei Stromausfällen eingesetzt, um Schäden zu vermeiden.
-
Konstruktion des Ofens:
- Das Drehrohr wird hergestellt aus Nickel-Basis-Legierungen mit einer Temperaturbeständigkeit von bis zu 1100℃ .
- Die Trommeldurchmesser und -länge können auf der Grundlage der Materialverarbeitungskapazität angepasst werden, und es können mehrere unabhängige Heizzonen eingerichtet werden, um die Produktionsanforderungen zu erfüllen.
-
Dimensionierung und Design:
- Die Dimensionierung eines Drehrohrofens umfasst technische Grundsätze , thermische und chemische Analysen und Erfahrung um die Verarbeitungsziele zu erreichen.
- Zu den wichtigsten Faktoren gehören Kapazität , Wärmeerzeugung , maximale Vorschubgeschwindigkeit , Verweilzeit und Bettprofil die den Durchmesser und die Länge des Ofens bestimmen.
-
Anpassungsfähigkeit und Flexibilität:
- Elektrische Drehrohröfen bieten eine hohe Flexibilität, mit anpassbaren Heizzonen , Drehzahlen und Kühlsysteme die auf spezifische Materialien und Produktionsanforderungen zugeschnitten sind.
- Dadurch eignen sie sich für ein breites Spektrum industrieller Anwendungen, vom Kalzinieren bis zum Sintern.
Durch die Kombination von präziser Temperaturregelung, effizienter Kühlung und anpassbarem Design bieten elektrische Drehrohröfen eine zuverlässige und vielseitige Lösung für die Verarbeitung von Materialien bei hohen Temperaturen.
Zusammenfassende Tabelle:
Aspekt | Einzelheiten |
---|---|
Arten von Drehrohröfen | Direkt befeuerte, indirekt befeuerte (Kalzinatoren) und elektrische Drehrohröfen. |
Anwendungen | Kalzinierung, Oxidation, Reduktion und Sinterung. |
Heizsystem | Heizelemente aus einer Nickel-Chrom- oder Eisen-Chrom-Aluminium-Legierung. |
Kühlung | Trommelkühler mit Wassersprühung zur indirekten Kühlung. |
Rotations-Mechanismus | Zahnkranzgetriebe und Elektromotor mit variabler Geschwindigkeit für präzise Steuerung. |
Konstruktion des Ofens | Rohre aus Nickelbasislegierung, Durchmesser und Länge individuell anpassbar. |
Anpassung | Einstellbare Heizzonen, Drehgeschwindigkeiten und Kühlsysteme. |
Entdecken Sie, wie elektrische Drehrohröfen Ihre Materialverarbeitung optimieren können. Kontaktieren Sie uns noch heute für eine fachkundige Beratung!