Das Sinterverfahren ist eine Technik zur Herstellung fester Materialien aus pulverförmigen Stoffen durch Anwendung von Wärme und Druck, ohne dass das Material bis zur Verflüssigung geschmolzen wird.Dieses Verfahren ist in Branchen wie der Metallurgie, der Keramik und der Glasherstellung weit verbreitet.Es umfasst mehrere wichtige Schritte: die Vorbereitung der Pulvermischung, die Verdichtung in die gewünschte Form, das Sintern bei hohen Temperaturen, um die Partikel zu verbinden, und die Behandlungen nach dem Sintern wie Bearbeitung oder Montage.Das Verfahren gewährleistet die Herstellung von Materialien mit geringer Porosität, hoher struktureller Integrität und spezifischen mechanischen Eigenschaften.Das Sintern ist für die Herstellung von Komponenten mit komplexen Formen, hoher Präzision und maßgeschneiderten Materialeigenschaften unerlässlich.
Die wichtigsten Punkte werden erklärt:
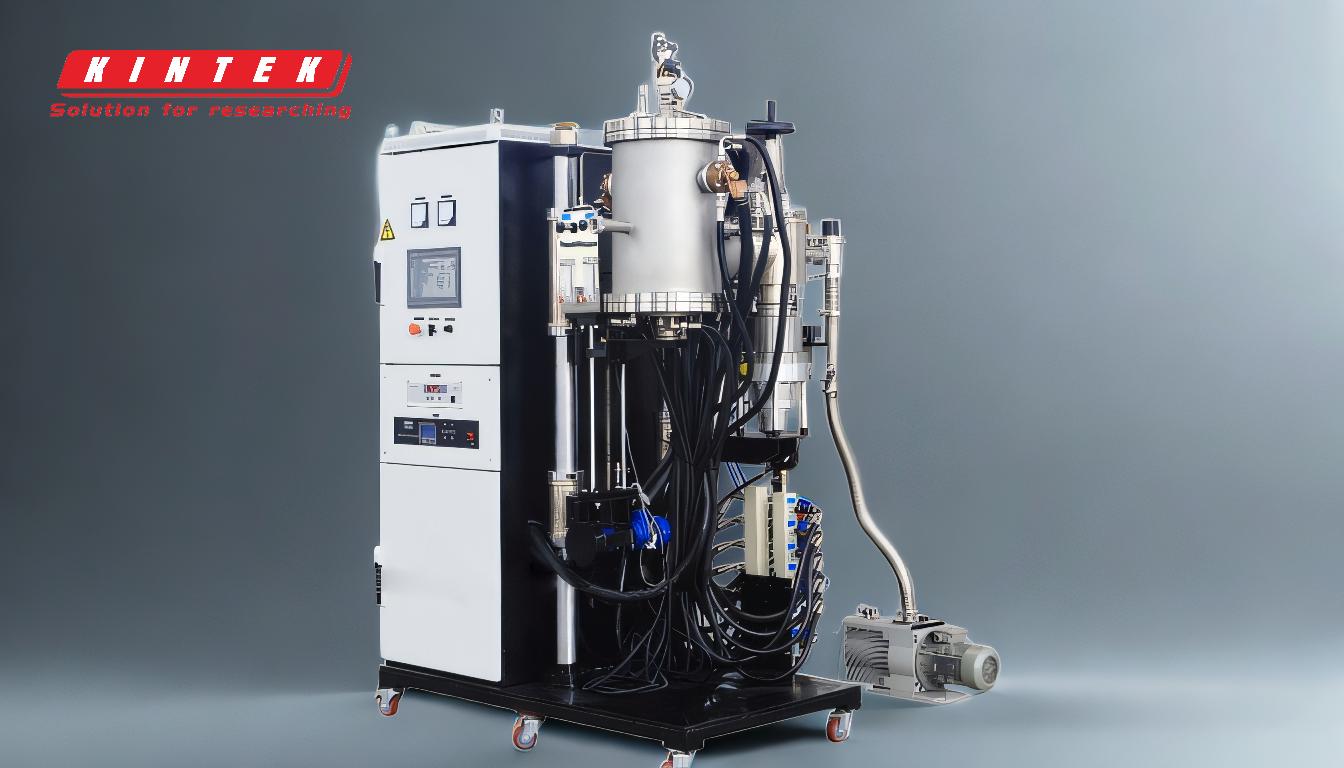
-
Herstellung einer Pulvermischung:
- Das Verfahren beginnt mit der Herstellung einer Pulvermischung, die Primärmaterialien, Haftvermittler und Zusatzstoffe wie Kupferpulver oder Hartmetalle enthalten kann.
- Das Pulver wird sorgfältig gemischt, um die Gleichmäßigkeit der Zusammensetzung zu gewährleisten, die für gleichbleibende Materialeigenschaften des Endprodukts entscheidend ist.
- In einigen Fällen werden Bindemittel oder Schmiermittel hinzugefügt, um die Fließfähigkeit und Verdichtung des Pulvers zu verbessern.
-
Verdichtung (Pressen):
- Das gemischte Pulver wird dann mit Hilfe von Hochdruckpresswerkzeugen oder Formen in eine bestimmte Form gepresst.Bei diesem Schritt entsteht ein "Grünkörper", der eine kohärente, aber zerbrechliche Struktur aufweist.
- Die Verdichtung kann bei Raumtemperatur oder in beheizten Formen erfolgen, je nach Material und gewünschten Eigenschaften.
- Der beim Verdichten ausgeübte Druck sorgt dafür, dass die Pulverpartikel in engem Kontakt stehen, was für die spätere effektive Sinterung unerlässlich ist.
-
Sintern (Erwärmung und Bindung):
- Der Grünling wird in einen Sinterofen gelegt und auf eine Temperatur knapp unter dem Schmelzpunkt des Ausgangsmaterials erhitzt.Diese Temperatur wird sorgfältig kontrolliert, um ein Schmelzen zu vermeiden und gleichzeitig die Partikelbindung zu ermöglichen.
- Während des Sinterns werden flüchtige Bestandteile wie Bindemittel oder Schmierstoffe entfernt, und die Partikel beginnen, sich durch Diffusion zu verbinden, wodurch eine Struktur mit geringer Porosität entsteht.
- Schlüsselparameter wie Temperatur, Luftmenge, Vakuum und Schichtdicke werden genauestens kontrolliert, um eine optimale Sinterung zu gewährleisten.
-
Partikelverschmelzung und Verdichtung:
- Mit steigender Temperatur verdichten sich die Partikel und verschmelzen, wodurch die Porosität verringert und die Festigkeit und Dichte des Materials erhöht wird.
- In einigen Fällen wird das Flüssigphasensintern (Liquid Phase Sintering, LPS) eingesetzt, bei dem sich eine flüssige Phase bildet und in die verbleibenden Poren fließt, wodurch die Verdichtung weiter verstärkt wird.
- In dieser Phase kann es zur Bildung martensitischer oder kristalliner Mikrostrukturen kommen, die zu den mechanischen Eigenschaften des Materials beitragen.
-
Abkühlung und Erstarrung:
- Nach dem Sintern wird das Material allmählich abgekühlt, damit es zu einer einheitlichen Masse erstarrt.
- Die Abkühlungsgeschwindigkeit kann das endgültige Mikrogefüge und die Eigenschaften des Materials beeinflussen und ist daher ein entscheidender Schritt im Prozess.
-
Behandlungen nach der Sinterung:
- Bearbeitungen:Gesinterte Teile können eine Bearbeitung mit Diamantwerkzeugen oder Ultraschallverfahren erfordern, um präzise Abmessungen und Oberflächengüten zu erzielen.
- Zusammenbau:In einigen Fällen werden gesinterte Keramik- oder Metallteile metallisiert und gelötet, um sie mit anderen Komponenten zu verbinden.
- Zusätzliche Behandlungen, wie Wärmebehandlung oder Oberflächenbeschichtung, können zur Verbesserung bestimmter Eigenschaften wie Härte oder Korrosionsbeständigkeit durchgeführt werden.
-
Anwendungen und Variationen:
- Das Sintern wird in verschiedenen Industriezweigen eingesetzt, z. B. bei der Herstellung von Stahl (wo Eisenerz und Koks für die Verwendung in Hochöfen gesintert werden), Keramik und modernen Werkstoffen wie Hartmetallen.
- Das Verfahren kann an verschiedene Materialien und Anwendungen angepasst werden, z. B. an 3D-gedruckte Komponenten oder komplex geformte Teile, die hohe Präzision erfordern.
-
Vorteile des Sinterns:
- Komplexe Formen:Das Sintern ermöglicht die Herstellung von Bauteilen mit komplizierten Geometrien, die mit herkömmlichen Fertigungsmethoden nur schwer zu erreichen sind.
- Materialeffizienz:Das Verfahren minimiert den Materialabfall, da überschüssiges Pulver oft wiederverwendet werden kann.
- Maßgeschneiderte Eigenschaften:Durch Anpassung der Zusammensetzung, der Verdichtung und der Sinterparameter können die Hersteller die Eigenschaften des Materials auf bestimmte Anwendungen abstimmen.
-
Herausforderungen und Überlegungen:
- Kontrolle der Parameter:Um gleichbleibende Ergebnisse zu erzielen, müssen Temperatur, Druck und andere Sinterparameter genau kontrolliert werden.
- Porosität Management:Obwohl das Sintern die Porosität reduziert, können bei einigen Anwendungen zusätzliche Schritte zur Beseitigung von Restporen erforderlich sein.
- Grenzen des Materials:Nicht alle Werkstoffe sind für das Sintern geeignet, und für einige sind spezielle Anlagen oder Techniken erforderlich.
Zusammenfassend lässt sich sagen, dass das Sinterverfahren eine vielseitige und effiziente Methode zur Herstellung von Hochleistungswerkstoffen und -komponenten ist.Durch die sorgfältige Kontrolle jedes einzelnen Schritts - von der Pulvervorbereitung bis zur Nachsinterung - können die Hersteller Produkte mit maßgeschneiderten Eigenschaften und komplexen Geometrien herstellen, was das Sintern zu einem Eckpfeiler der modernen industriellen Fertigung macht.
Zusammenfassende Tabelle:
Schritt | Beschreibung |
---|---|
Vorbereitung des Pulvers | Mischen von Grundstoffen, Zusatzstoffen und Bindemitteln, um Gleichmäßigkeit und Fließfähigkeit zu gewährleisten. |
Verdichtung (Pressen) | Hochdruckverformung des Pulvers zu einem zerbrechlichen "Grünling". |
Sintern (Erhitzen) | Erhitzen unter den Schmelzpunkt, um Partikel zu verbinden, die Porosität zu verringern und die Festigkeit zu erhöhen. |
Abkühlung und Erstarrung | Allmähliche Abkühlung zur Verfestigung des Materials und zur Beeinflussung des Gefüges. |
Behandlungen nach dem Sintern | Bearbeitungen, Montage oder zusätzliche Behandlungen zur Erzielung von Präzision und Verbesserung der Eigenschaften. |
Anwendungen | Einsatz in der Stahlproduktion, in der Keramik und bei hochentwickelten Materialien wie Hartmetallen. |
Vorteile | Produziert komplexe Formen, minimiert den Abfall und ermöglicht maßgeschneiderte Materialeigenschaften. |
Herausforderungen | Erfordert eine präzise Steuerung der Parameter und hat möglicherweise Materialbeschränkungen. |
Entdecken Sie, wie das Sintern Ihren Fertigungsprozess verändern kann. Kontaktieren Sie unsere Experten noch heute !